Composites
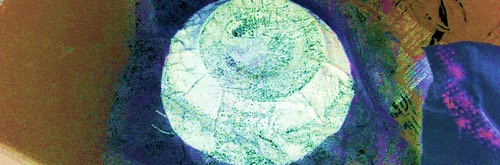
This week was an interesting week as like week 12 of molding and casting I'm not used to get my hands "dirty" with chemical products. Is clearly that composites has lot of applications in different fields, and this assignment also help me to get more confident in several machines as I used CNC, and laser cutting machine again.
Lesson
Academany Fab-2016.05.04D Lesson 14: Composites from Fab Academy on Vimeo.
Review
Academany Fab-2016.05.11B Review 14: Composites from Fab Academy on Vimeo.
Making the model for milling
I wanted to make a base for the icosahedron of the laser cut week, that maybe help me with the final project as surface for video mapping.
I used Autodesk Fusion 360 that this week has a little update to make a contour for making an 3d object by revolution method. As was a simple way to get a easy object for milling.
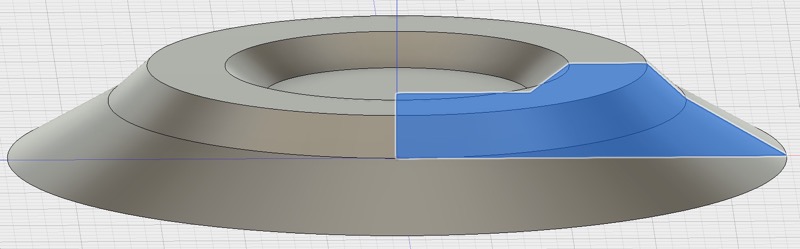
Here you can see and download the stl object of the base
Toroide Composite by bjlanza on Sketchfab
In Fablab León as many other Fablabs we use Aspire Vectrix 3D in this case version 5 for make the gcode files for the cnc machine, in this case in .tap format
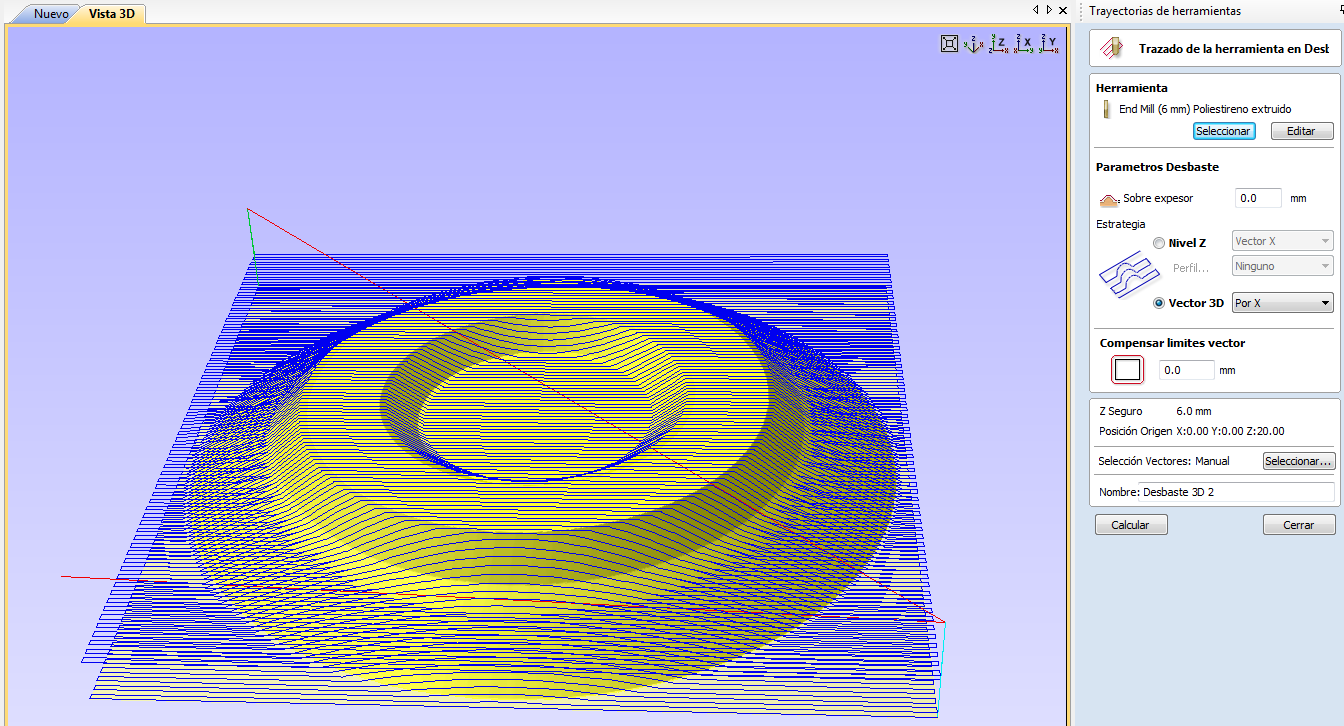
In previous weeks I just make the 2D cut strategies and never imported a stl object and use the 3D strategies, I notice that it use the same principle of grayscale heat maps of depth that the Fabmodules use for making the molds in the Modela MX-20.
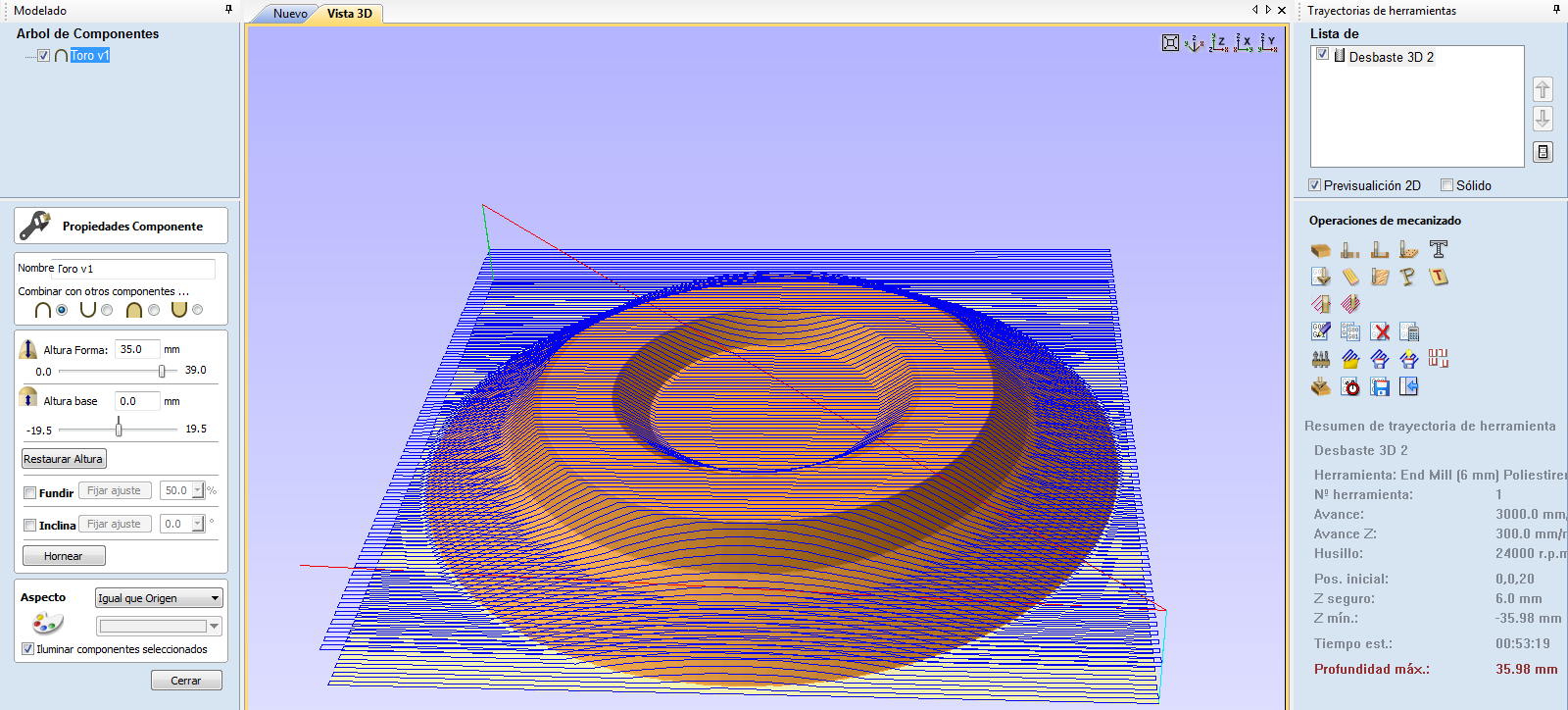
For milling the foam, a 6 mm diameter end mill bit is used, that is special for foam. As is not a hard material you can make deeper pass, but you always used the maximum rpm speed like other bits.
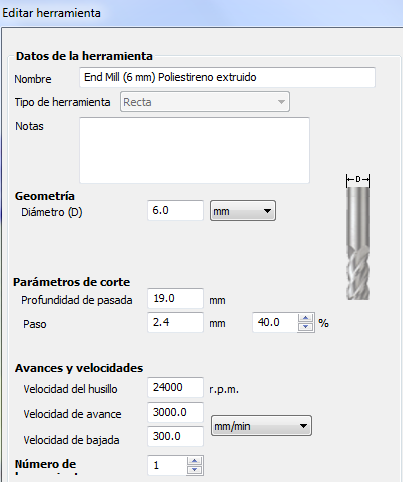
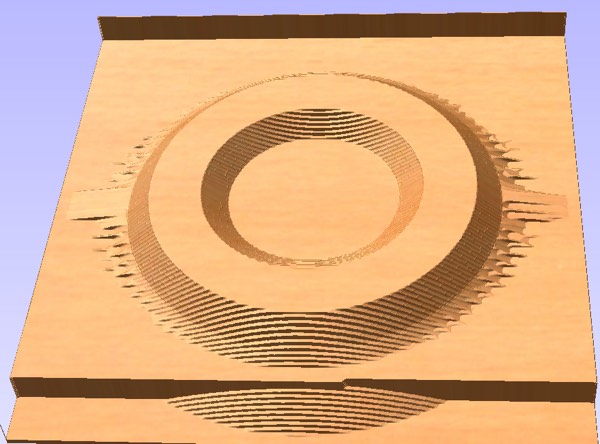
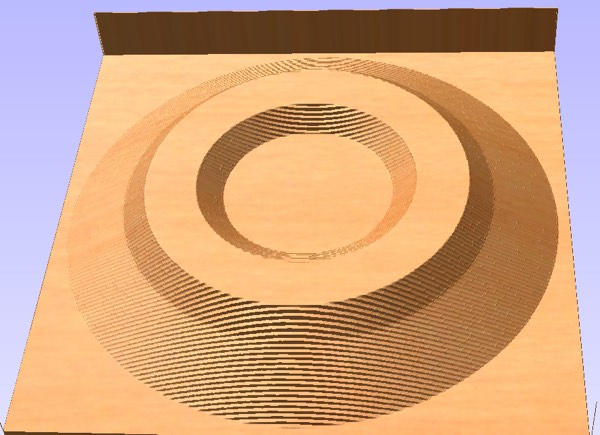
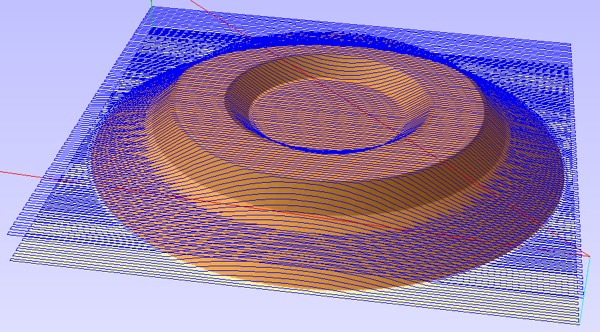
The thickness of the foam was around 39 mm without being vacuumed, remember that this type of material can change its thickness so you have to measure with precision if you plan to mill to the end of material.
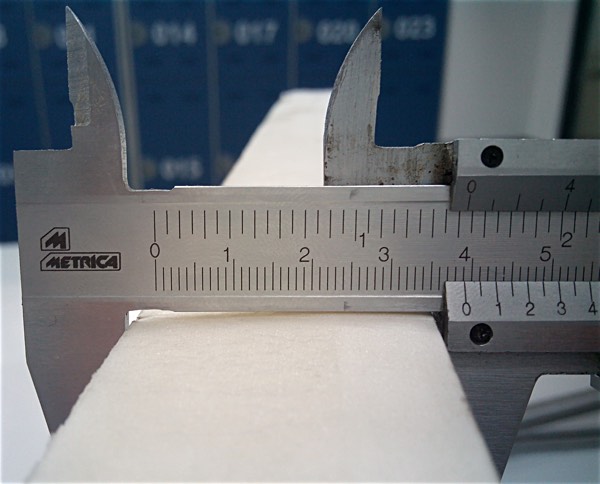
Security is the most important thing when you are working in a Fablab, so our instructor Nuria Robles, never get tired of said how to operate the machines and the security guidelines.
With a CNC you have to be very careful to don't wear any clothes, clothing accessories or long hair that can be wrapped and pulled by the machine. Also avoid the milling bit and always be aware were is the machine milling and not get hit by their axis.
Also protect your eyes against parts that can be flying when milling and ear protection as is a very noisy machine. You should be near the machine and watching what is doing for cancelling as soon as possible if is any problem and your notice any strange sound or behavior.
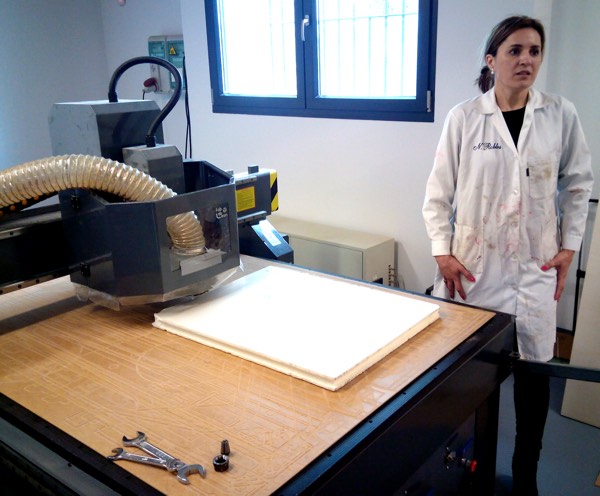
The physical bit for milling foam.º

As I was going to mill a depth of 35 mm against 39 thickness material even with vacuum, I just set Z above the material.
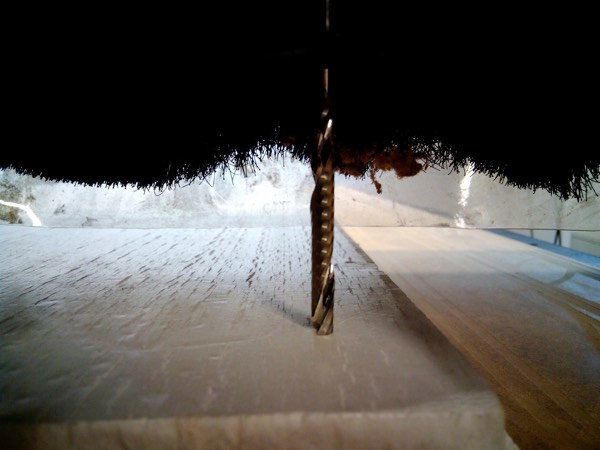
Video showing milling of the foam
Here you can see a short video CNC milling the disc.
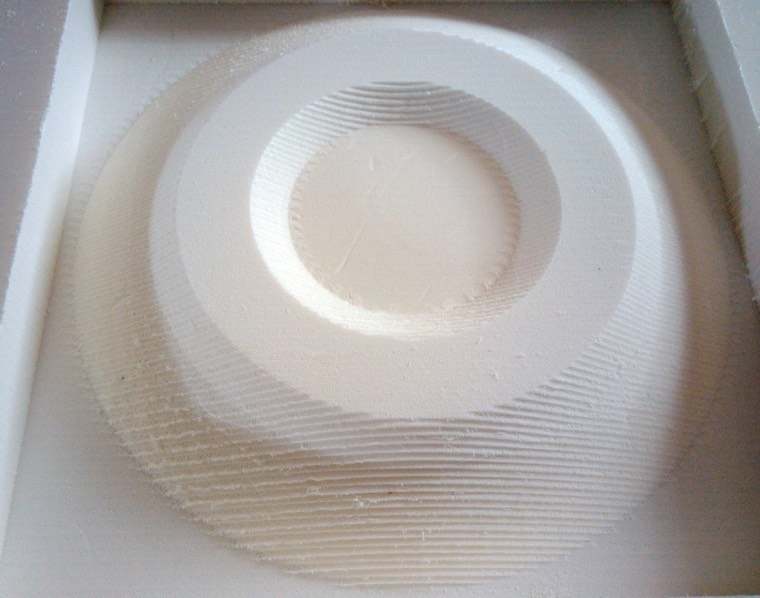
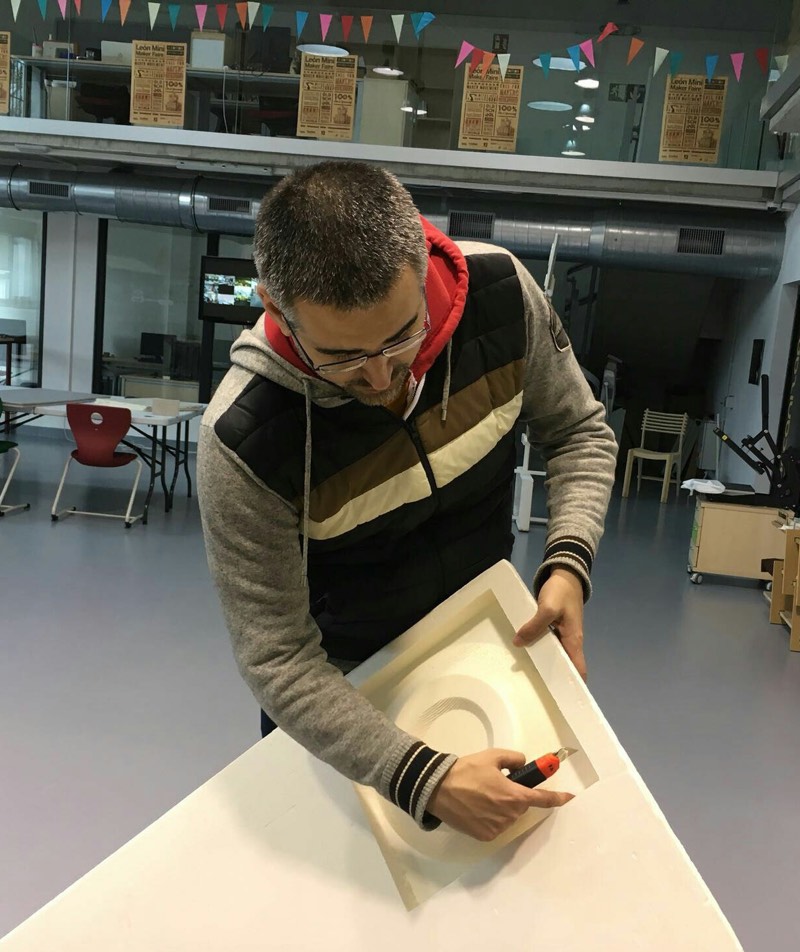
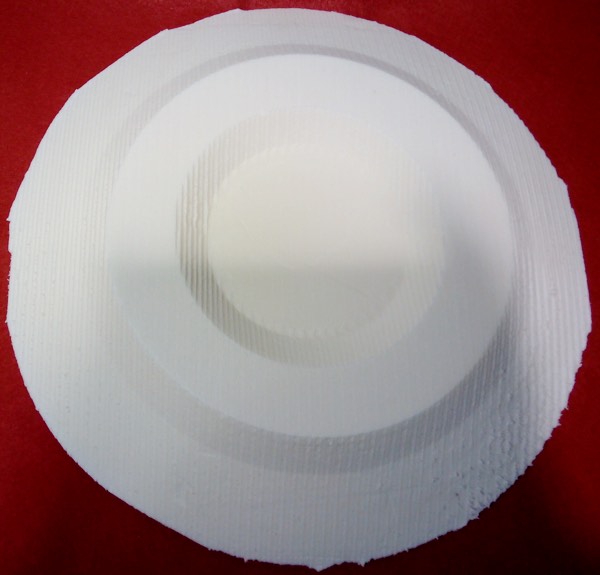
Unfolding the structure of the 3d object
Finally I just cut 2 circles of 30 cm of diameter in black burlap with the laser cut with this parameters in the epilog, The laser tube is brand new, so maybe you need to increase the power with time.
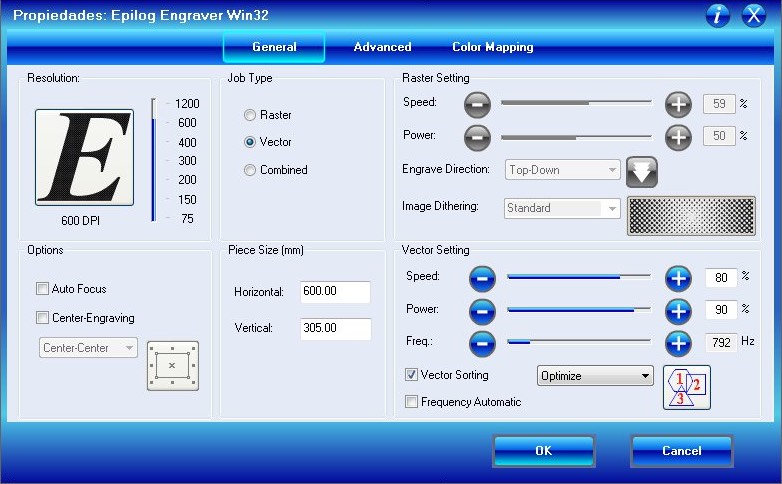
Applying the epoxy resin and vacuuming the shape
We Use Sap resin products that are environment bio friendly, so we don't need special protection for eyes, just be covered and use gloves that not contain latex
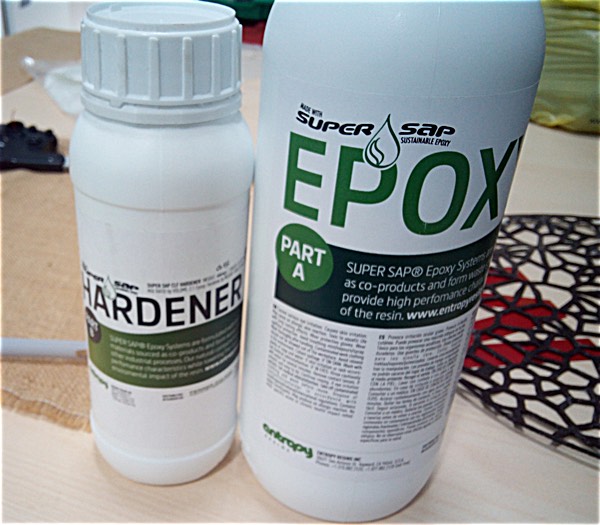
The epoxy resin was the Fast version, that has a pot life of 25 minutes, and a hardener time of 4 hours plus a curate time of a week. The proportion between resin and hardener was 47 grams of hardener per 100 grams of product A. You have the specifications here.
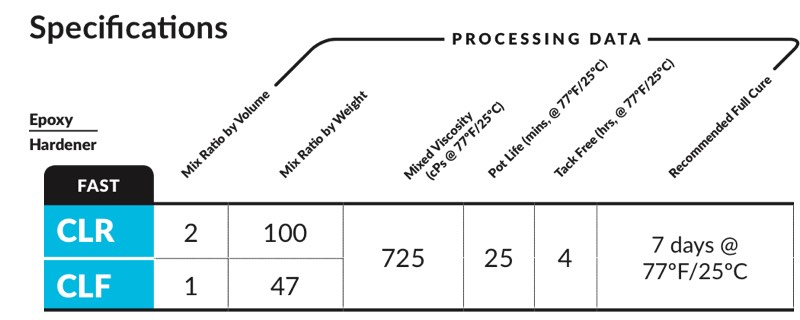
Have a clean workspace with anything at hand is a must, also is a "dirty" assignment that can leave traces in the floor or work tables so better if your cover it with plastic and papers
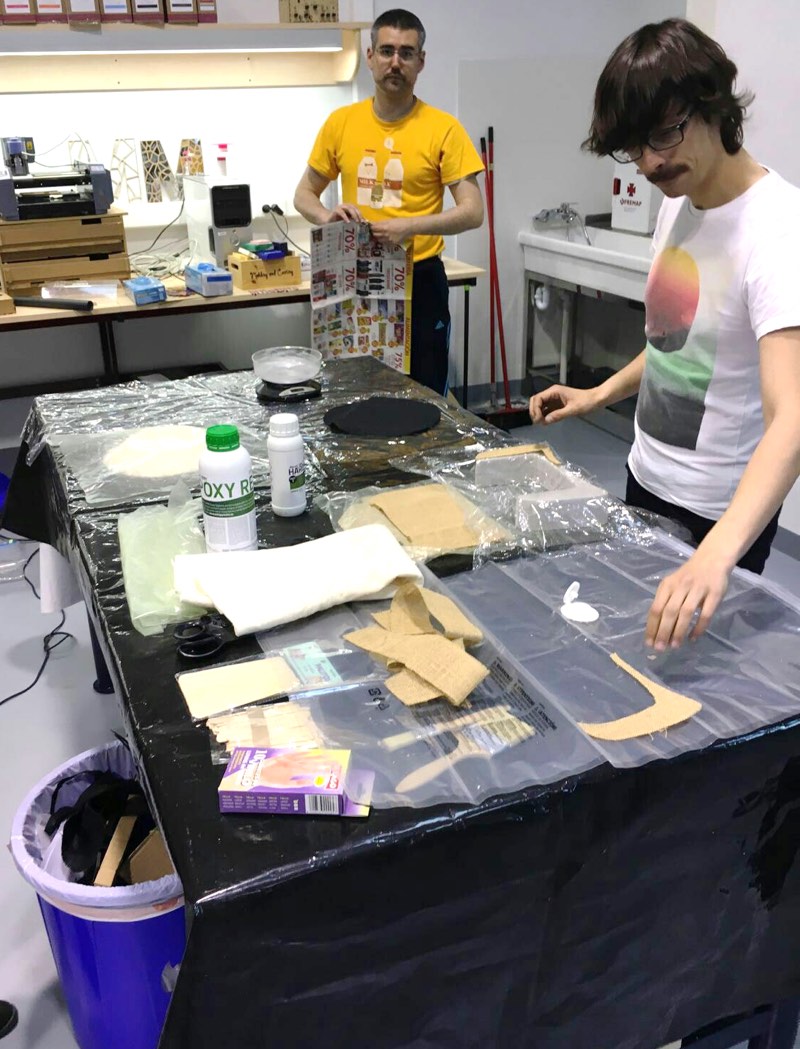
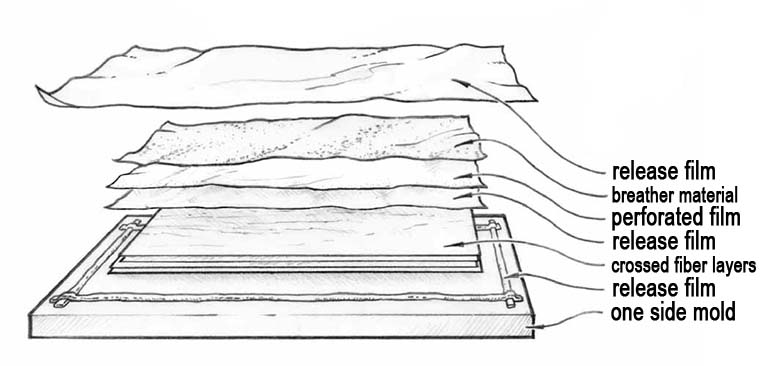
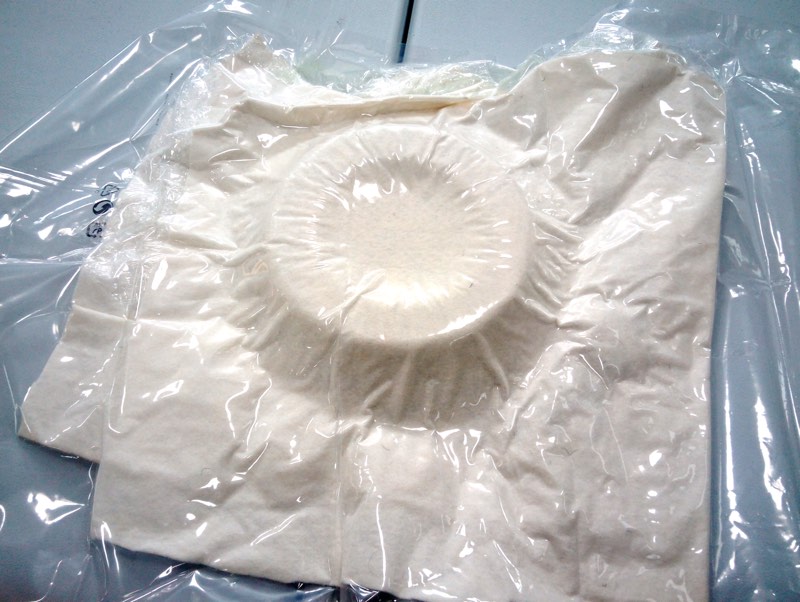
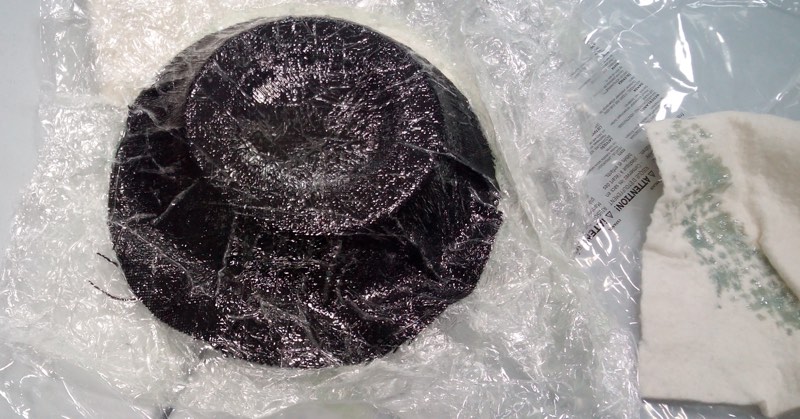
The final result was not perfect as during manipulation one layer move and make a hat instead a base, but the procedure was affordable and I will repeat again as also my classmate Luis Diaz will make some improvements in his model, so we will have another dirty day in Fablab. Also I can get some ideas of the worldwide review.
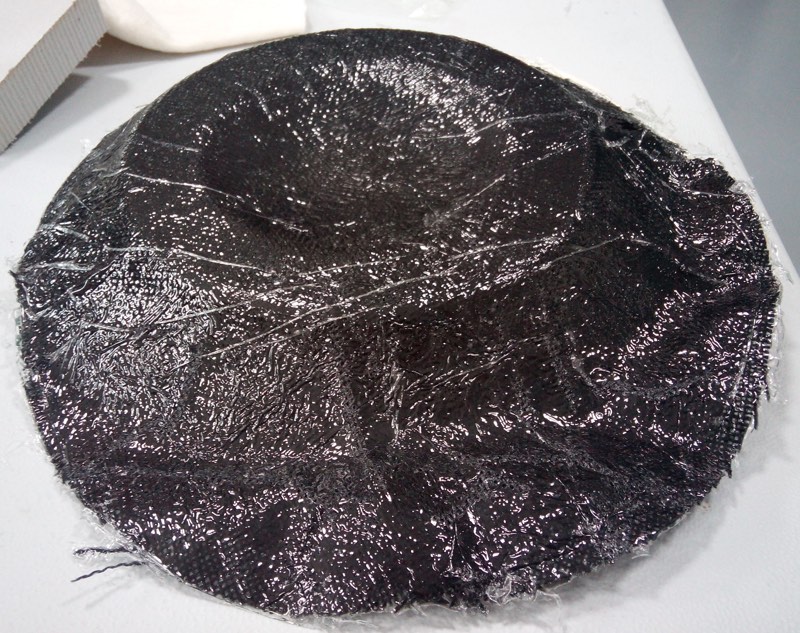
I made a second try fixating the mold with pins to avoid the movement, not perfect but much better
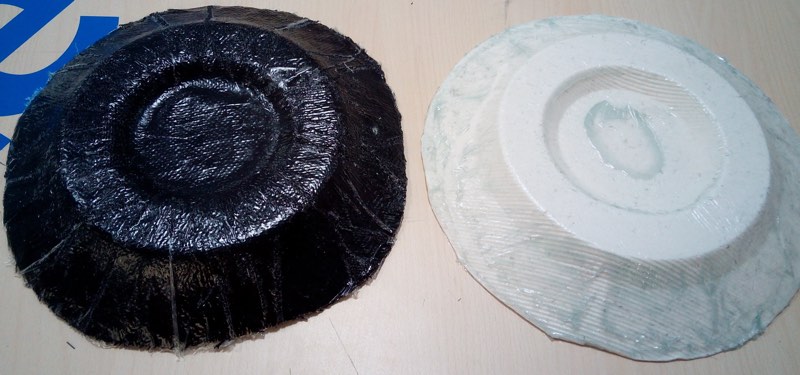
Final result of second try that I use as base for the icosahedron of week 2.
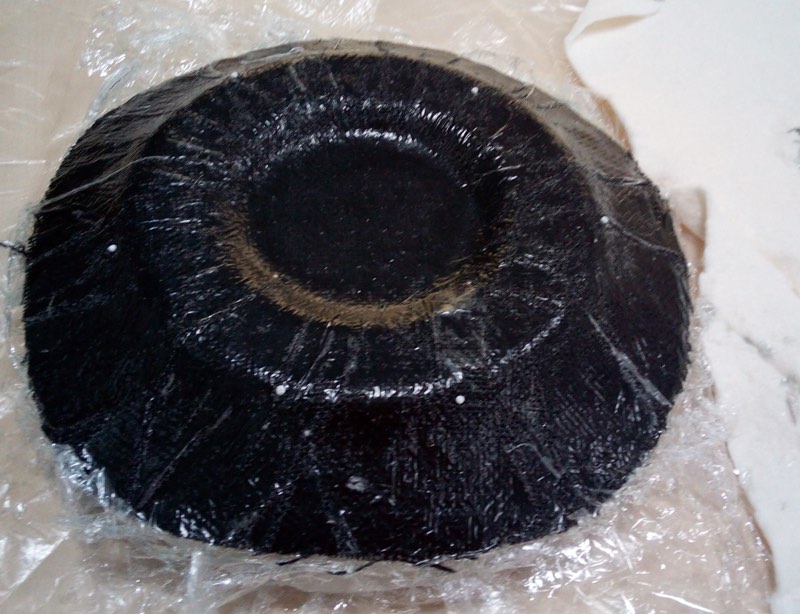