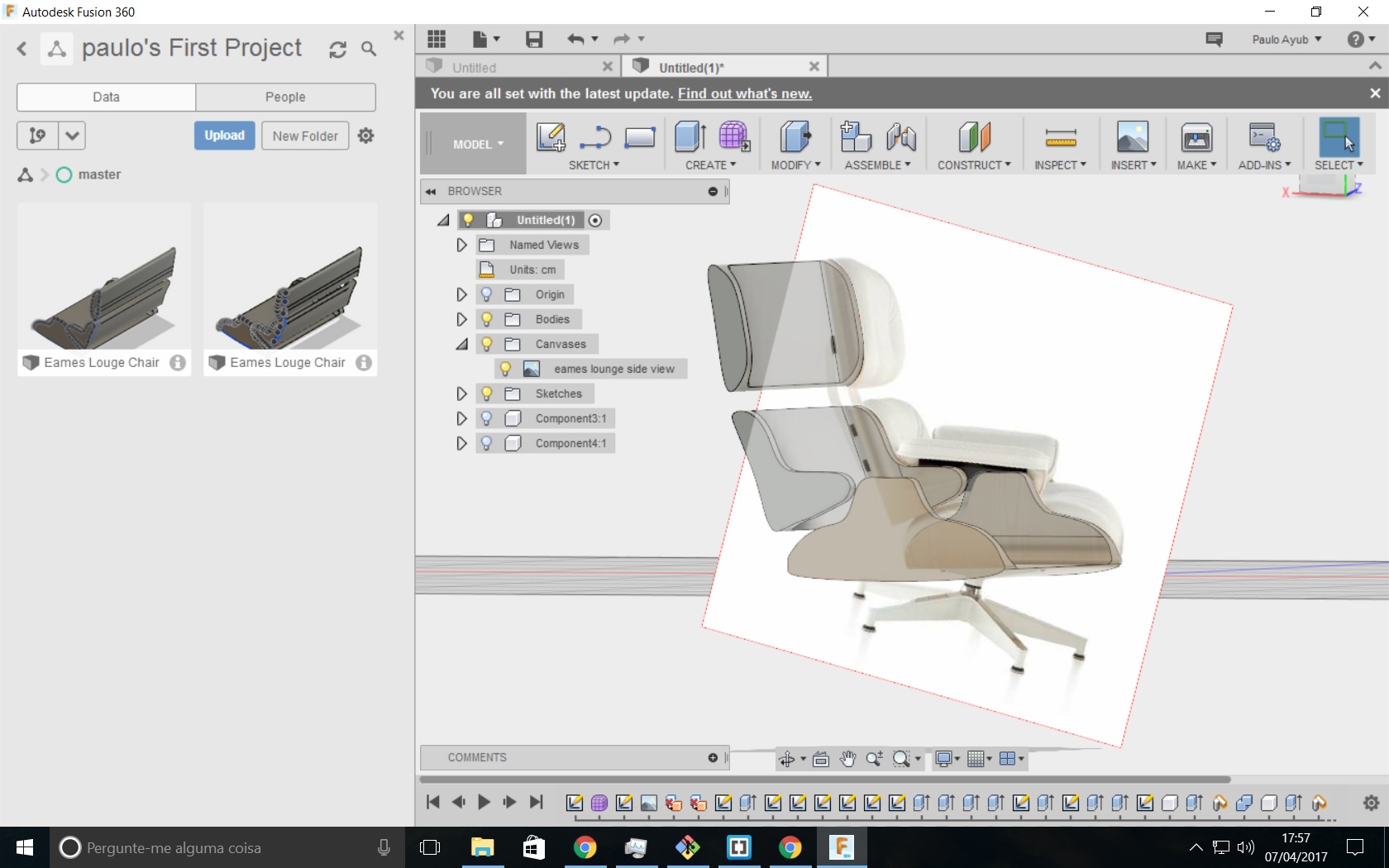
Computer-Controled Machining
In this assignment I've tried to make something for me, so I decided that I wanted a chair, but no ordinary one, a really comfortable and great looking chair.
Other day I was in a furniture store and I saw the most great looking chair my eyes ever saw, a big and large chair that was comfortable and had a really great design.
I went home and make a bunch os google searches on ergonomic designs and famous chairs and stumble upon the chair I saw in the store, the "Eames Lounge Chair".
After I saved the picture I used as a reference on Fusion 360 to make my on design. My chair it's not as round as the eames is but is larger and taller to fit my needs. To reduce weight i've removed some material and have used some spacers on my final desing. My desing dosen't have any joints, the way I assembled was using threaded rods and nuts.To draw this chair i used the "Spline" tool to make the outline and the "Extrude" tool to give my draw the size i wanted, after that i made another drawing, using spline tool again, extruding again, but this time towads the first component and using the "Cut" tool to make the actual seat.
Since the chair is compoused of tree vary similar shapes its just matter of repeting the process with the other two componets.
To configure the G-Code files I used ArtCAM. It is a very coplete software and for each parameter it explain what it means. The cut parameters that i used was:
In my case I was using 20mm plywood, starting cut depth was 0 and final cut depth was 20,5 mm with a 0.02mm tolerance
I used the 6mm straight end bit with 2.7mm on the lateral step and 5mm on the vertical step.
I used the "ramp" option and used 10 degree as max angle and 10mm as max ramp size
"The Machine I used was the "Raptor 1313" from DS4. DS4 is a brazilian manufacture of industrial CNC router machines Link to website here
It is controlled using the Mach3 CNC Controller Software. This software reads the .gcode files and control the machine
As my project is built by stacked slices, it doesn't need kerf parameters. I just position it side by side, and made some guide holes to all the pieces stay aligned.
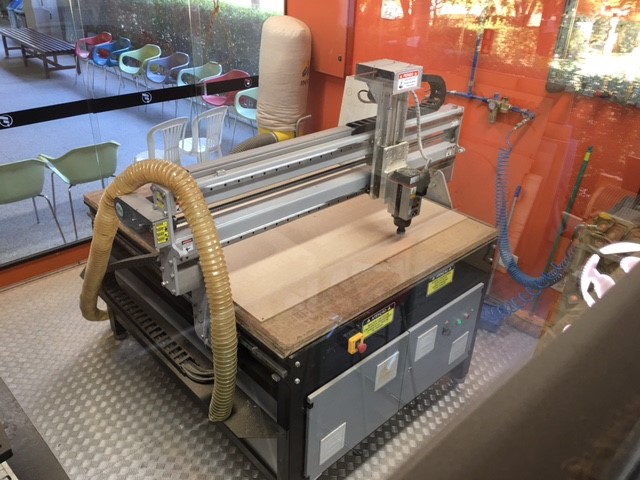
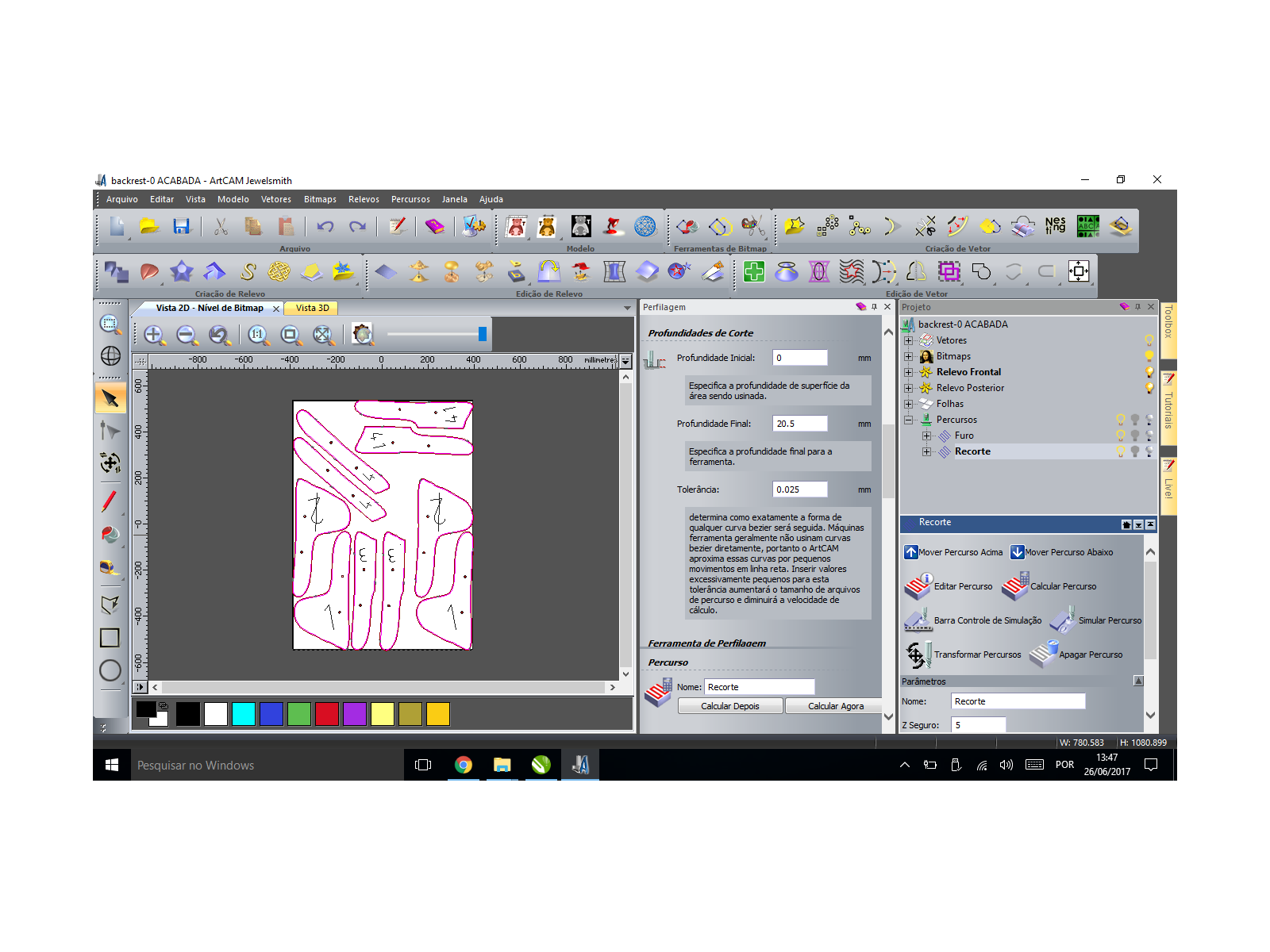
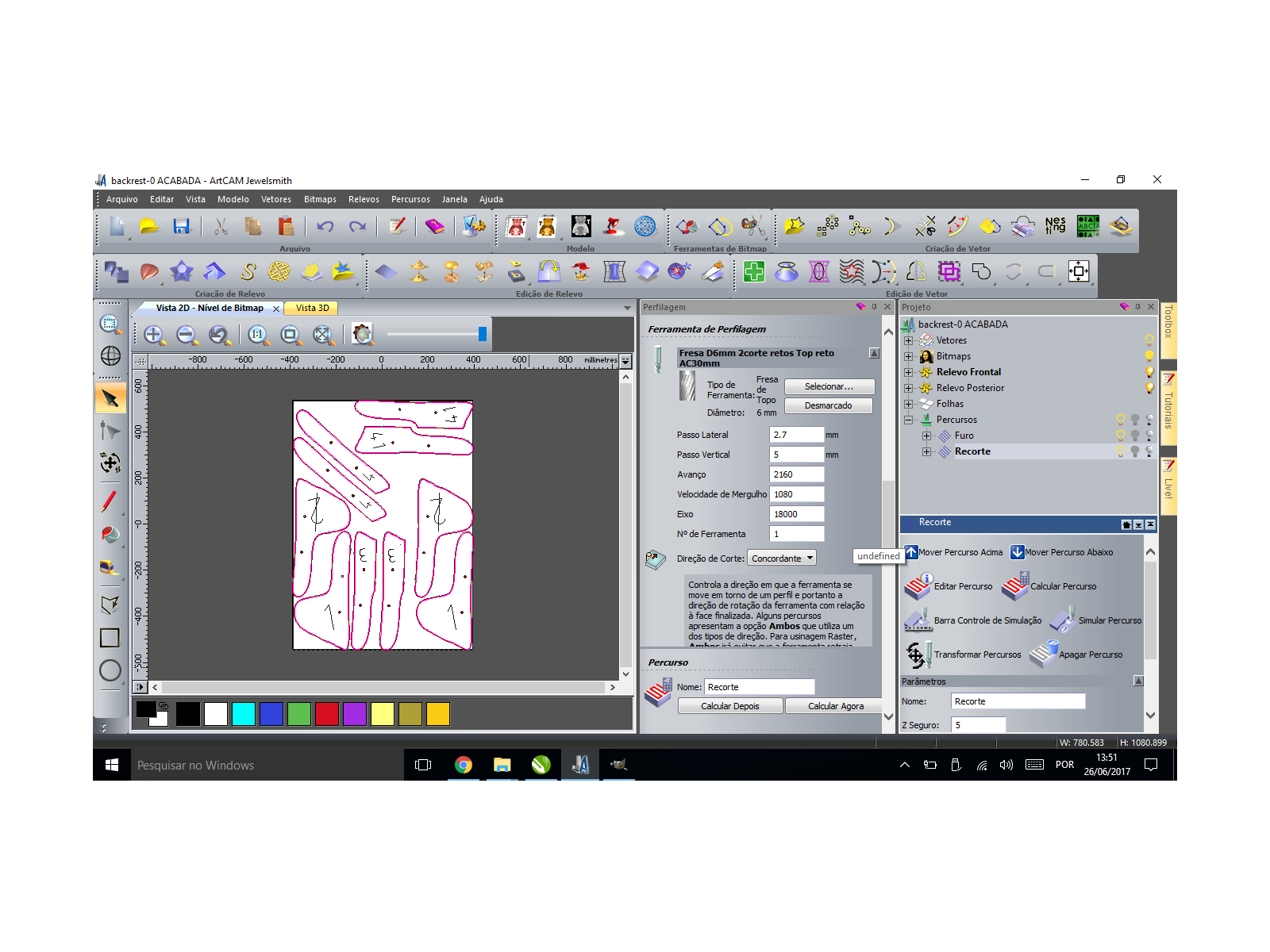
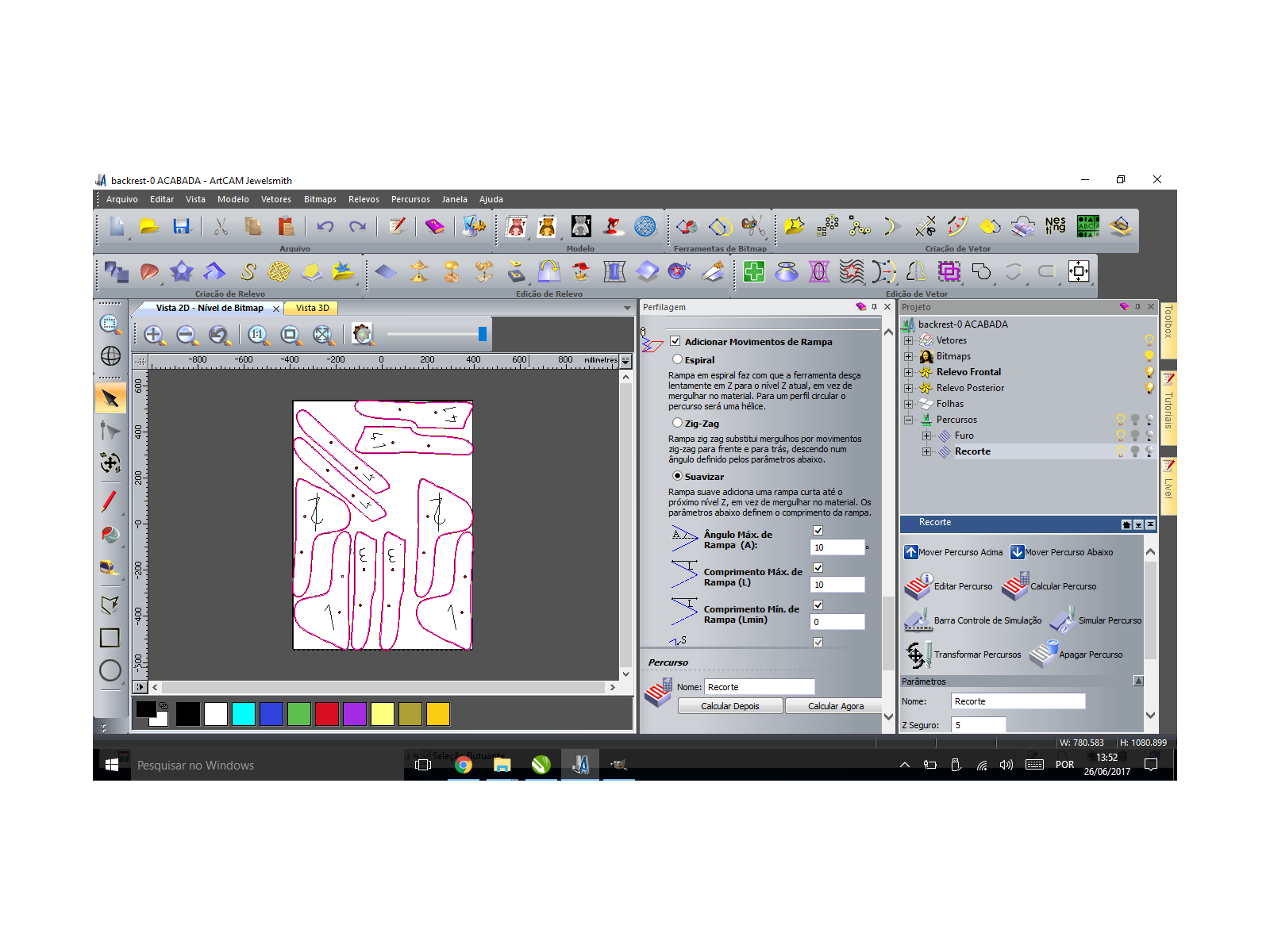
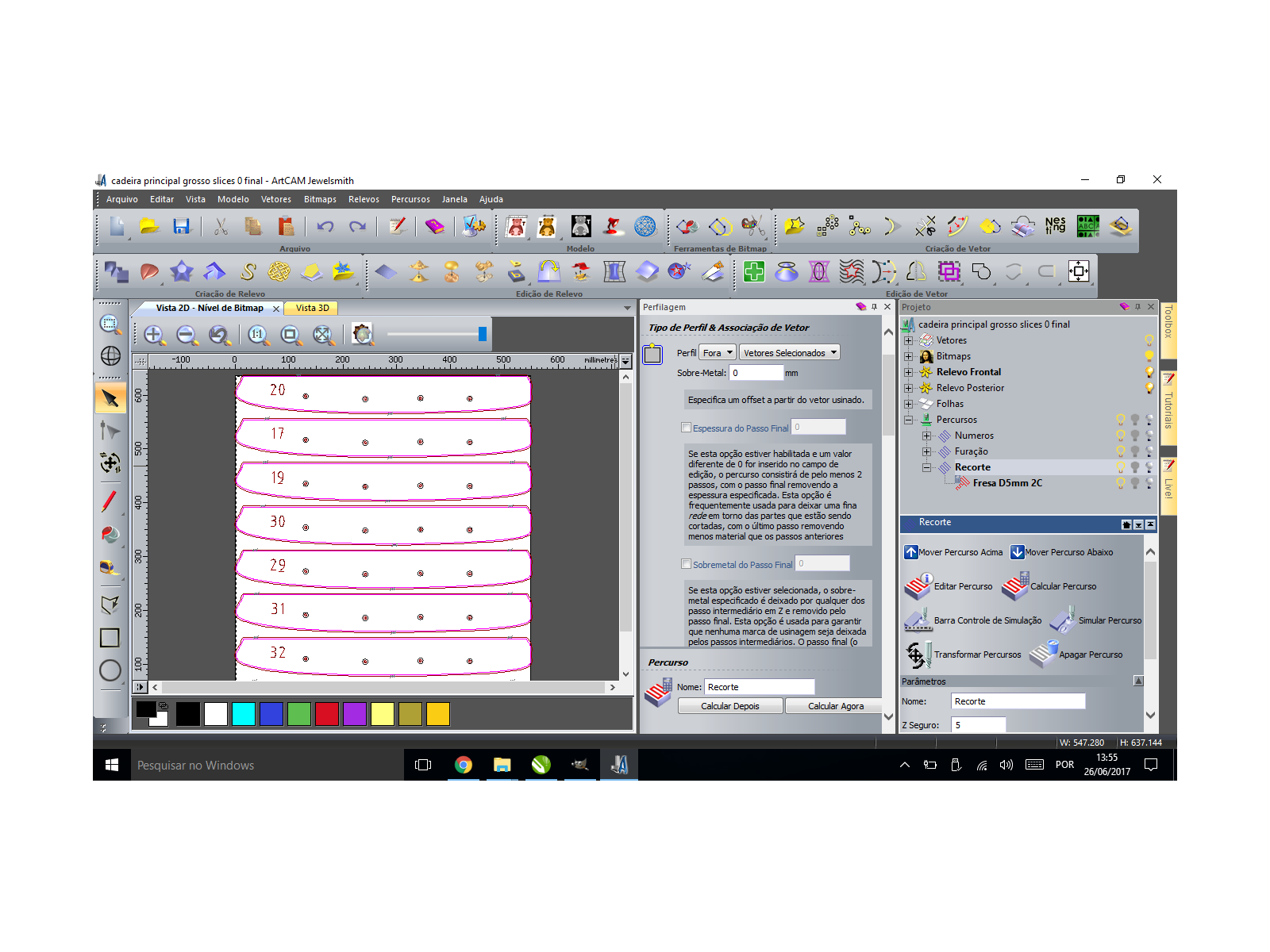
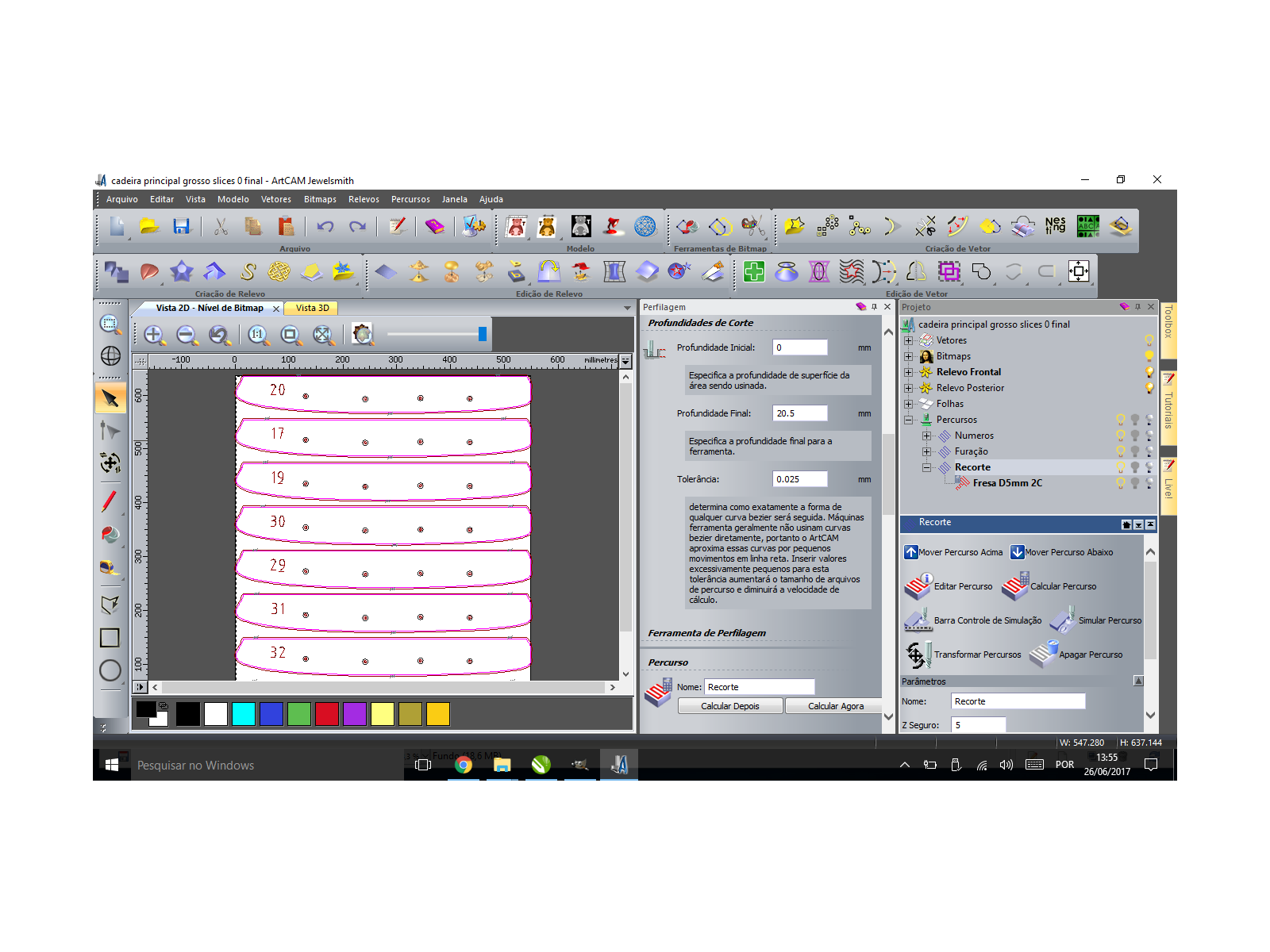
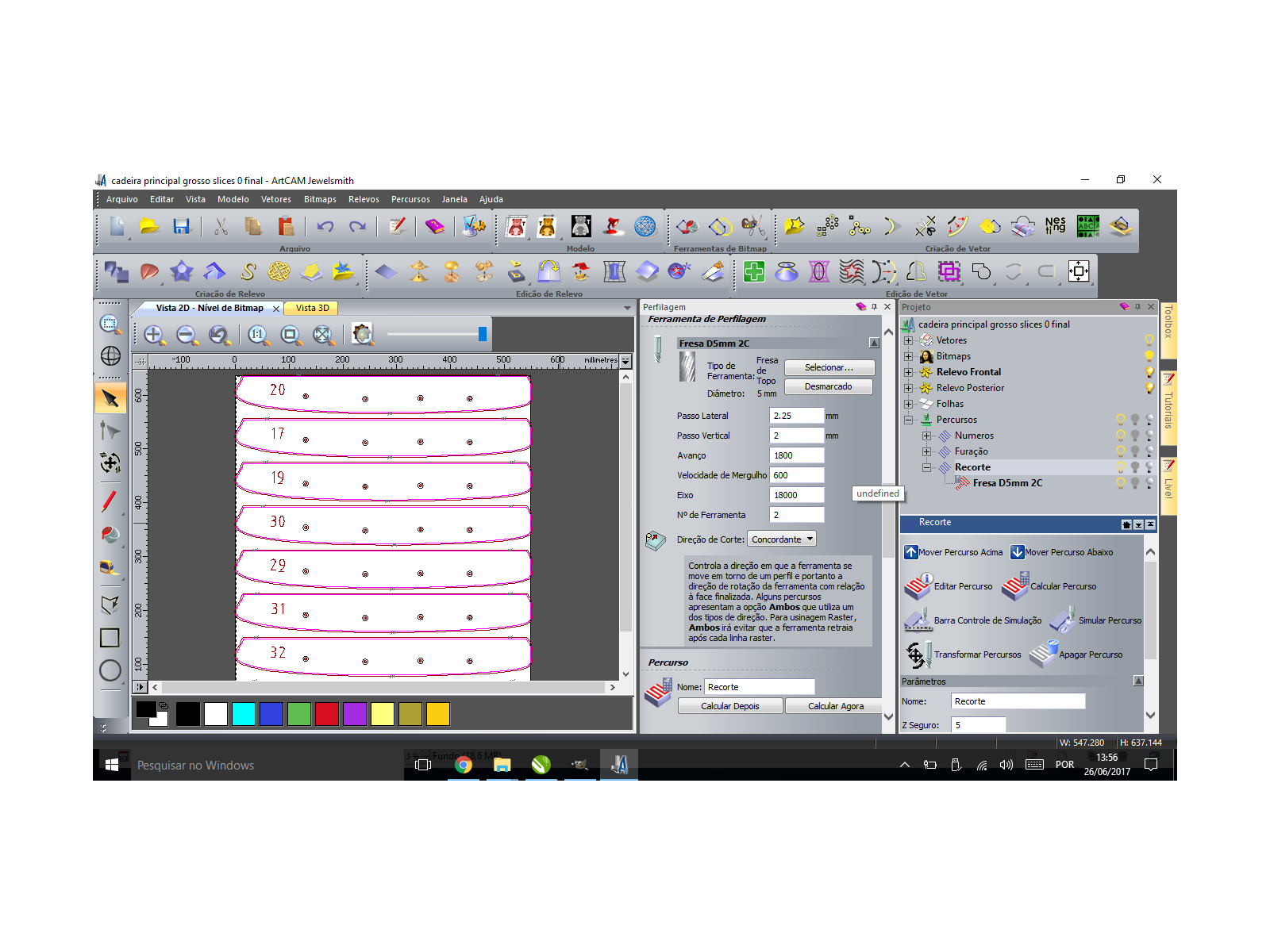
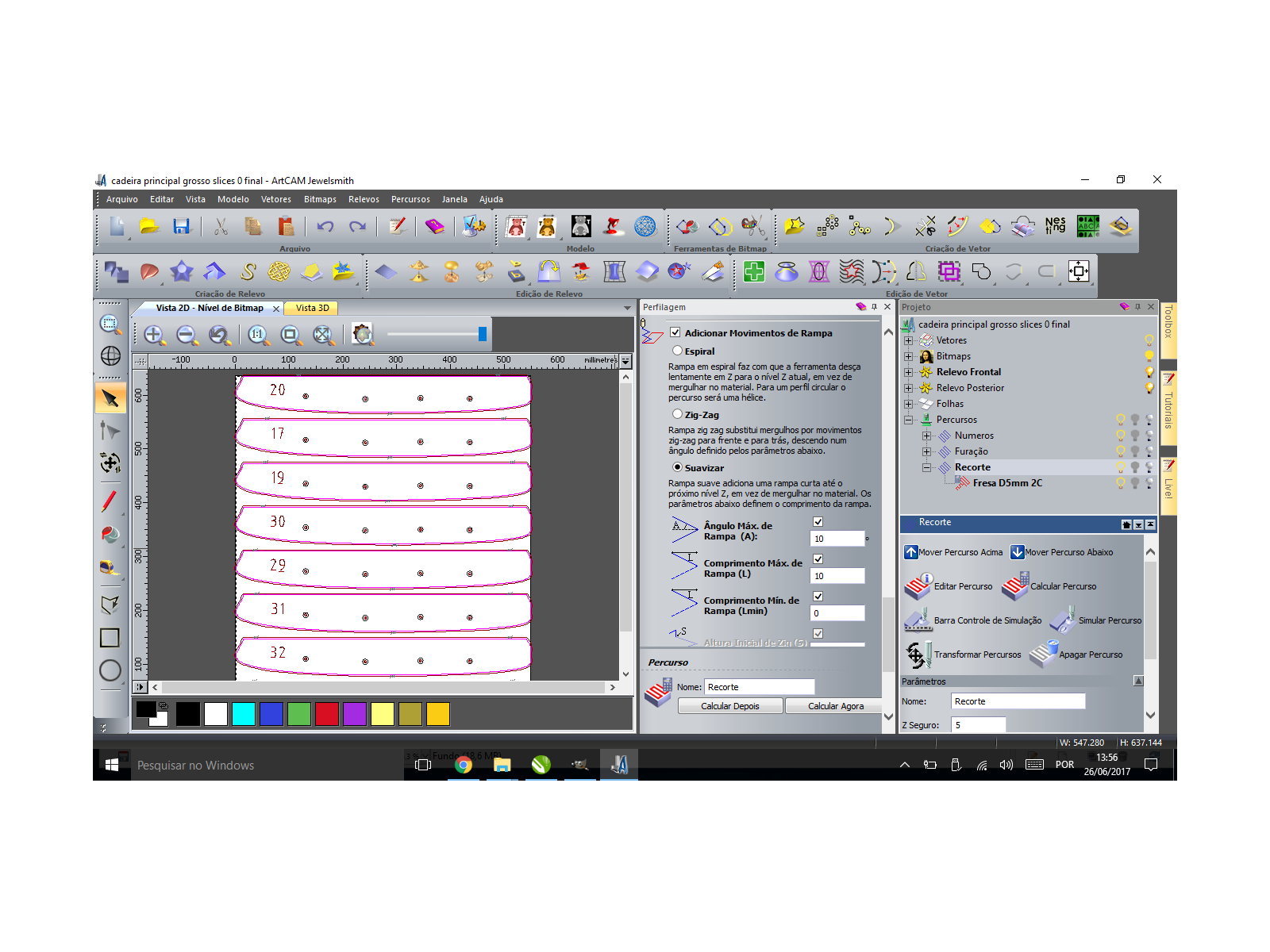
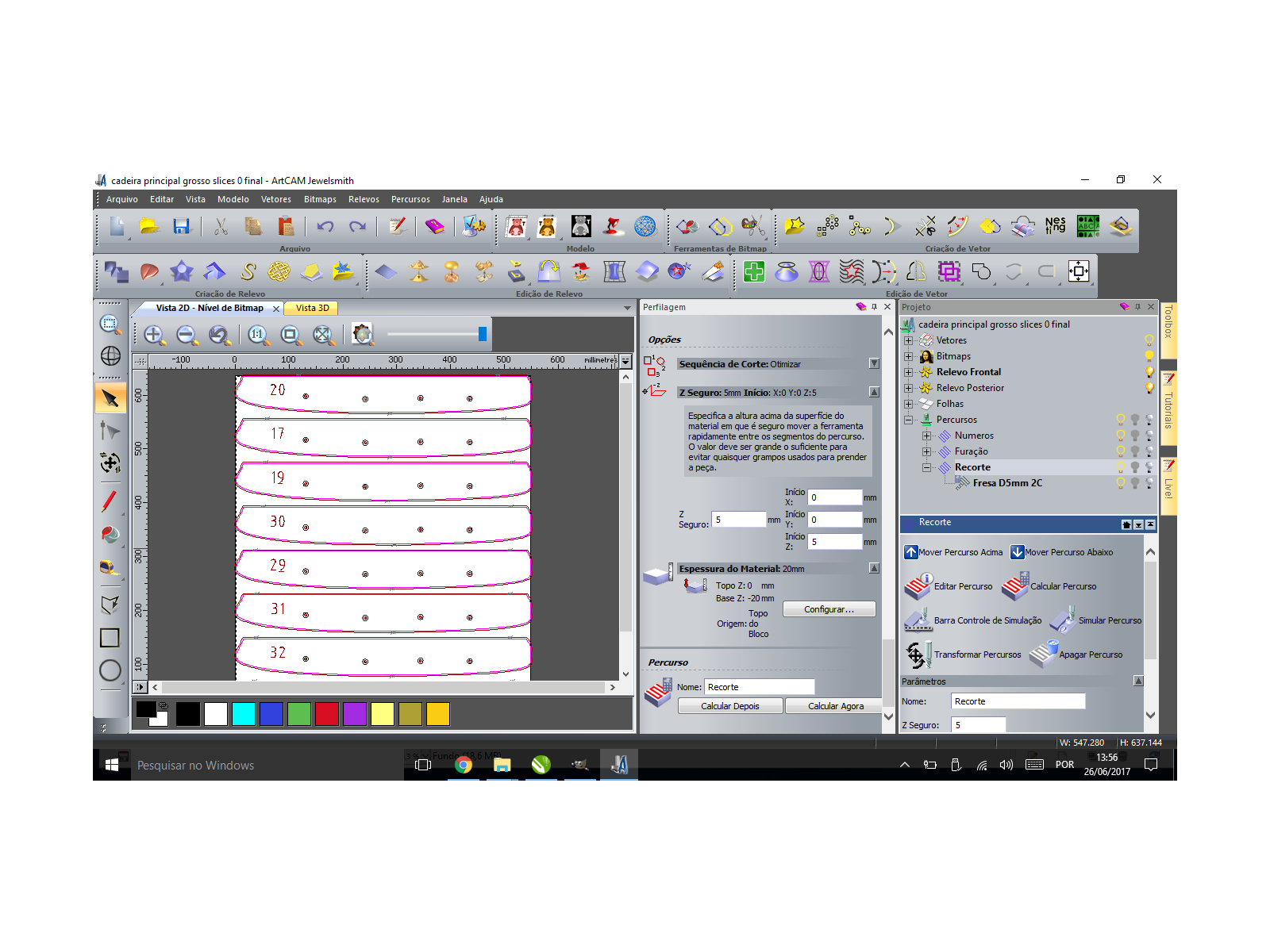
After the cutting process we elaborate a panel with the information about some cutting materials and what parameters to use on the machine
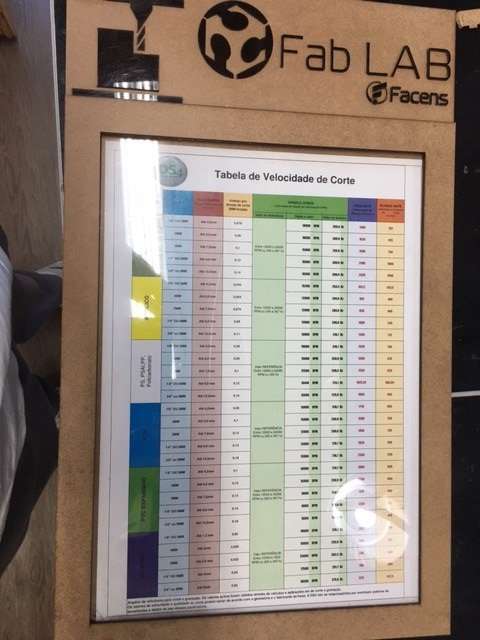
I just draw the wood part of the chair, i will cut the aluminium afterwards and that will allow me to make the fine ajustments by feelling the chair on my back.
I will use car foam and lether to finish this project and make the chair even more confortable.
Fusion360 File Avaliable Here DXF Files Avaliable Here