Week 10 : Mechanical Design
Assignment :
Make a machine, including the end effector, build the passive parts and operate it manually.
This being a group project and since our lab have 14 fab academy students, there where two groups formed for the group assignments
Our Group Members:
- Muhammed Jaseel P.
- Nisha Elsa Johnson
- Paul Anand
- Rashid Thattayil
- Sibu Saman
- Vinod Kumar B. G.
- Yogi Kulkarni
A few ideas were discussed which includes:
- Plotter
- Foam Cutter
- Mini CNC Lathe
- CNC Plotter
After the group meeting held on 2nd of April noon, we decided to go forward with Mini CNC Lathe. Since the entire machine need not be made from scratch, it was decided to build up on the machine from the present designs available. Sibu and a few otheres made a trip to the junkyard to bring in a few components needed. At the end, we pooled a few resources. There are a few parts must for a lathe, including the Headstock with a chunk to hold the tool, a motor to power up the spindle, a tool post that can move both X and Y directions and optionally a tail-stock to support the workpiece.
Lathe
A lathe is a machine tool that rotates the workpiece on its axis to perform various operations such as cutting, sanding, knurling, drilling, or deformation, facing, turning, with tools that are applied to the workpiece to create an object with symmetry about an axis of rotation.
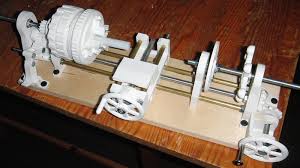
Parts...
chuck will hold the workpiece and will be attached to a Drill or some other motor or Dremel tool. But Dremel may not have the sufficient Torque for the purpose, it definitely has the speed.
Me and Jaseel 3D printed the chunk parts using the the two 3D printers here. The three drive gears were printed using Dimensions. We decided this so that the drive gears would be more stronger compared to printing using PLA plastic in Ultimaker (we did not have abs plastic spools for Ultimaker 2 in our inventory). The files for the chuck was taken from thingiverse.
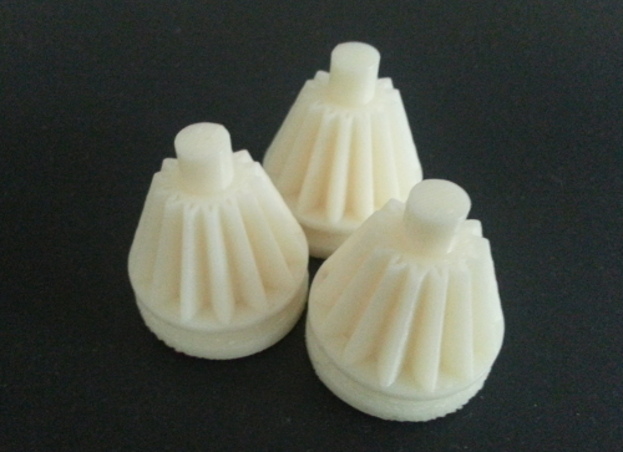

There is a front housing component also of the chuck to be printed.
We are planning to laser cut the base and the staging box, sibu is preparing the CAD files for it.
Week 11 : Machine Design
Assignment :
This week's assignment is to automate the machine built, and document the whole process in group and individual pages.
Since, our building machine was lagging the first intent was to complete it.
We had to laser cut the box for the two stages intented for X and Y movements. Modular stages allows users to explore different kinematic models easily. Different heads can be mounted to them. So, we decided to focus first on building the two axis machine that can hold a tool and could be automated.
Once the stages were build, we decided to implement the catchup plan first which was to make the plotter. Later, the same 2-axis machine could be used with a different tool to create different machines and the plotter pen could be replaced with the Lathe tool.
This week we are supposed to focus on the automation part of the machine. We did not have Gestalt boards or the MTM stages in the lab. A gestalt board is a single stepper driver that is used to control a stepper motor by the PC. Since fabrication was taking time, it was decided to use RAMPS. RepRap Arduino Mega Pololu Shield, or RAMPS for short is designed to fit the entire electronics needed for a RepRap in one small package for low cost.
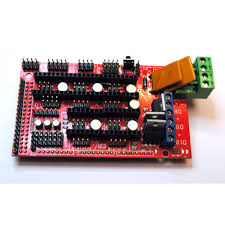
The first step was to check if RAMPS was working fine and could move a single stepper motor. At first we connected the board and motar and used RAMPS test code to test it.
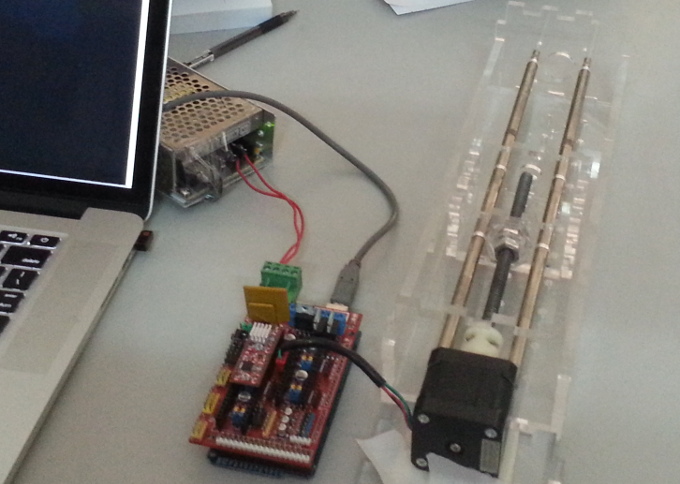
The modified version of the code was used. With the modified code working good to achieve the stepper movements, next step was to control the machine with instruction sets provided so that the motors could move the plotter head as per the instructions given. It was decided to implement a simple G-code interpreter, which would run on RAMPS and communicate with a host using a serial interface.
Video of the machine running
My contributions...
- Took files from thingiverse and 3D printed the lathe chuck parts
- Helped in documenting the group page and overall works
- Helped in taking test cut outs and acrylic machine stages cut outs.
Final assembly of machine
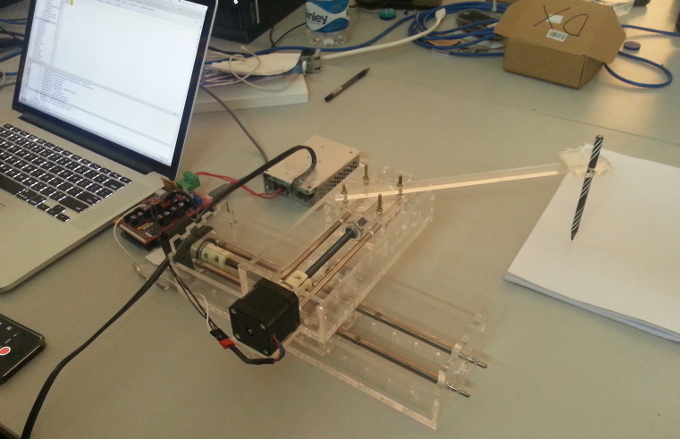