Composites
For composites assignment I decided to make a folded form. I wasn´t sure in the beginning which resin I will use: polyester resin or epoxyd resing. But I was pretty sure about the reinforcement comination of jute, 'papyrus' and that the resin I was going to use has to be completely clear. It is going to be a combination of composite and conservation of these beautiful sheets.
Papyrus
You can get papyrus in art material suppliers like Boesner in Germany. The cost for a papyrus sheet in 30 x 40 cm is about 2,80 Euro.
The sheets are made from pith of the stipe of a papyrus plant in the same way like antique Egyptians did and takes few weeks to produce it. First of all the stipes have to be soaked over 2-3 weeks to get rid of sugar. After cutting the pith in stripes and arranging them side by side, they have to be 'beaten' and pressed until a starchy soak is coming out and glue them together to a strong but flexible material.
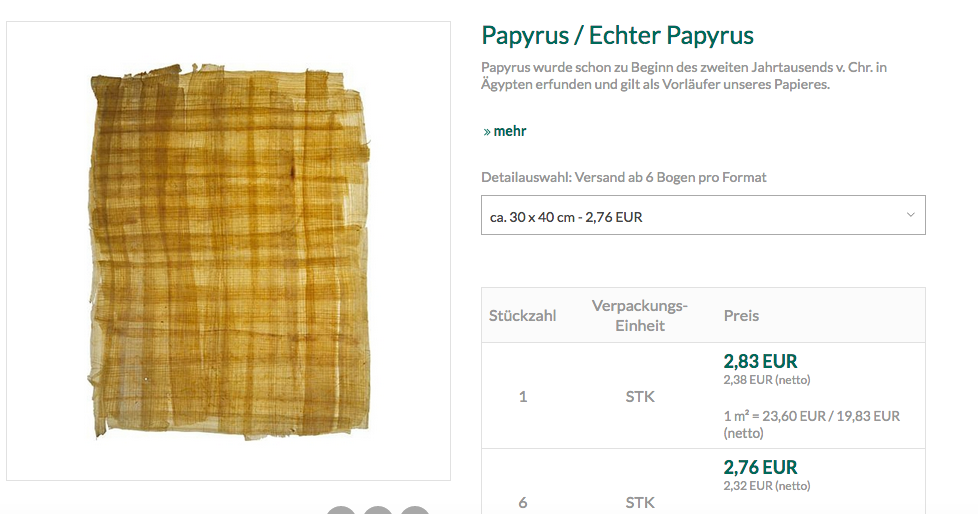
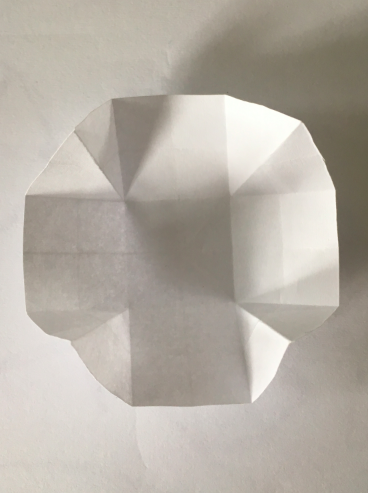
About the material I've used for composite assignment.
In general: Take care to use a chemical resistant bin for mixing and fresh air, because of acrid fumes. Wear gloves and a work coat, the resin is acid.
I have used polyester resin for composites like in molding and casting. Referred to the datasheet it is also very much suitable for composites in combination with glasfiber. But I didn't want to use glasfiber mats, I wanted to combine natural materials and embed them in clear acrylic material. Below you can see some product informations. The resin is like other resins poisonous and acid if you use it wrong. You need a good aircondition, but best it do it outside. Don' touch it without gloves, it' acid to your skin and lungs. If you are exposed to long to the vapour it can cause sterility. That is quiete frequently mentioned and should be taken serious.
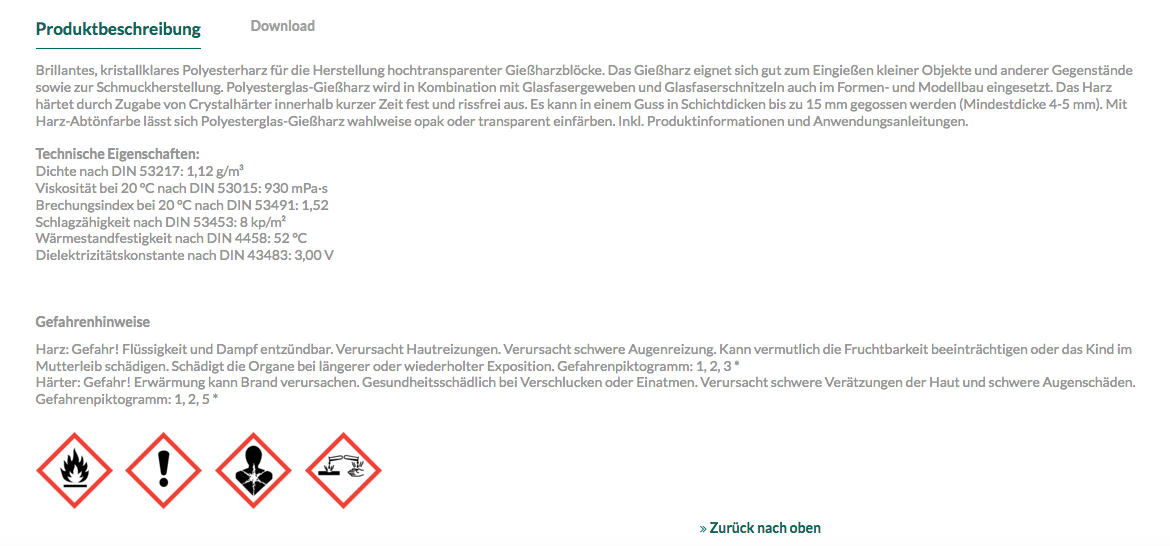
I did the whole proceeding outdoors!!
First step was painting my form with releasing agent. Then I prepared the mresin mixture.I have checked out reactions between body filler and polyester resin, papyrus and resin, wood and polyester resin, wood release agent and resin, stretch film and resin and aluminum foil and resin. The third picture shows that the resin isn't able to soak the layers a papyus is made with. That means I had to perforate them.
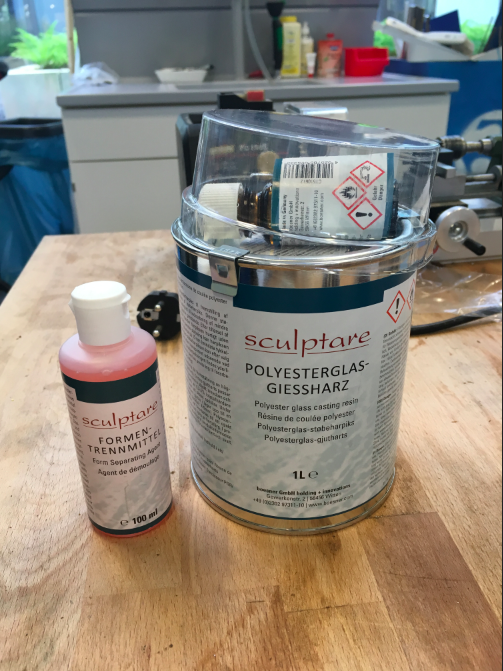
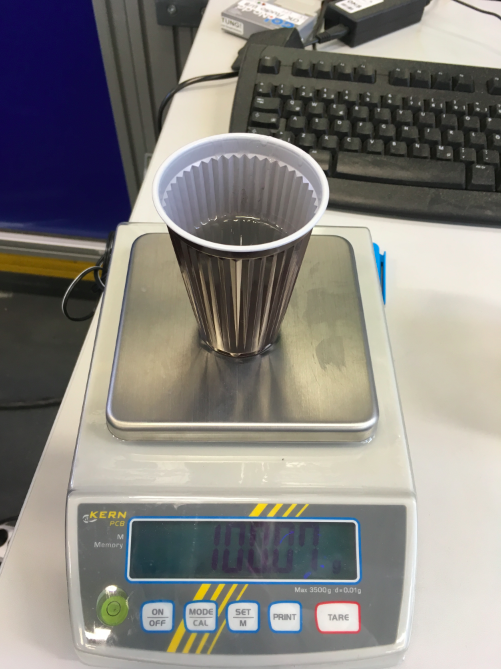
I used a fluid resin from 'sculptare' also bought at Boesner. After pouring and measuring the resin,
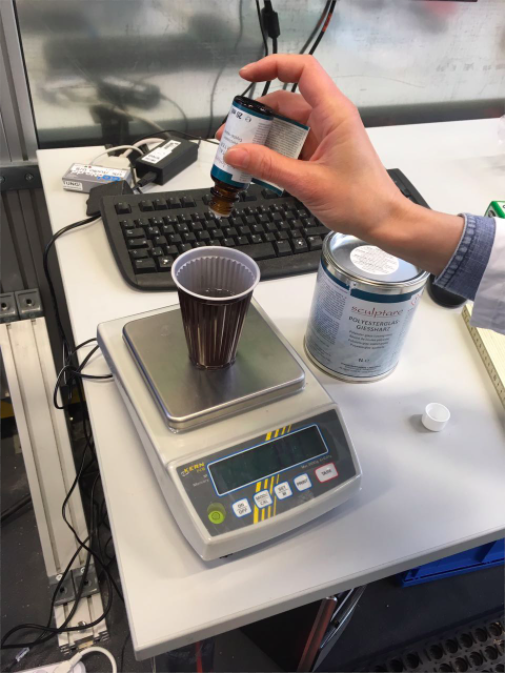
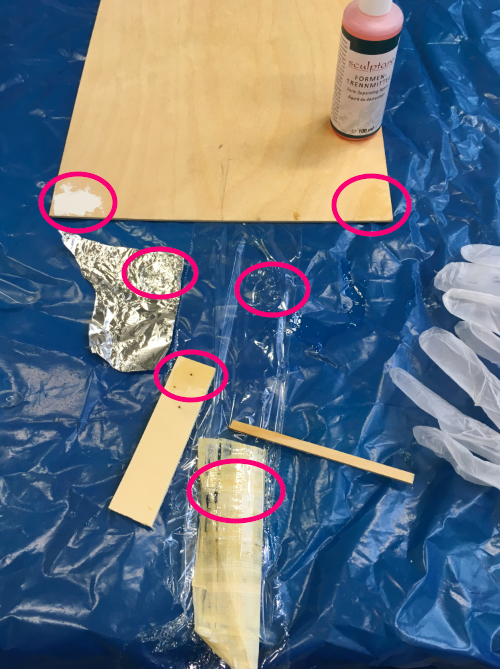

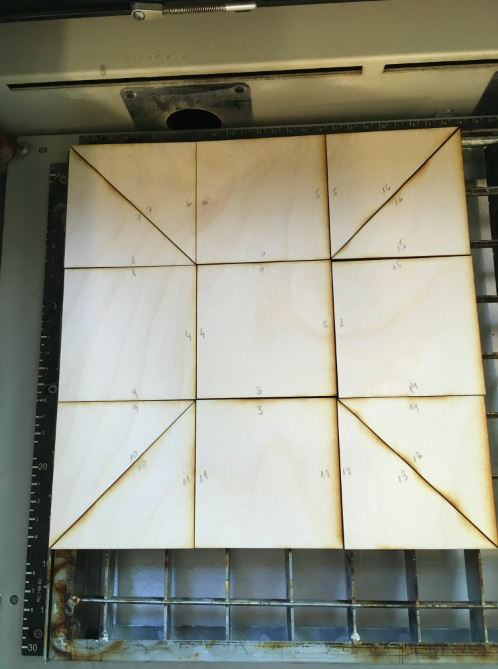
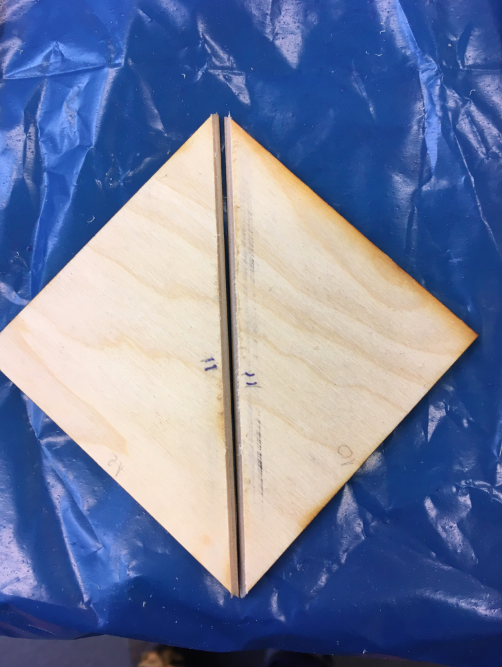
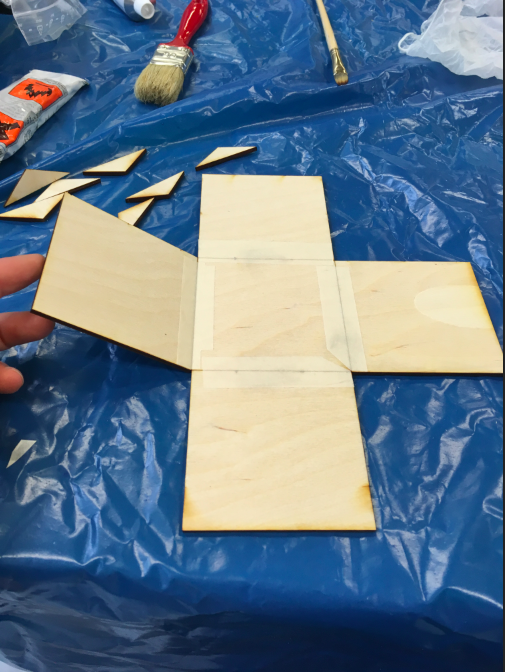
Then I lasercut the wooden plate for the folding shape, burnished some angles for the corners sticking out and started to build up the body.
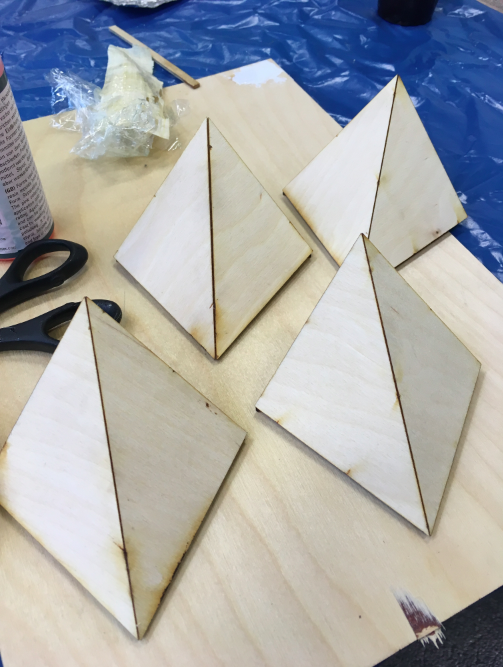
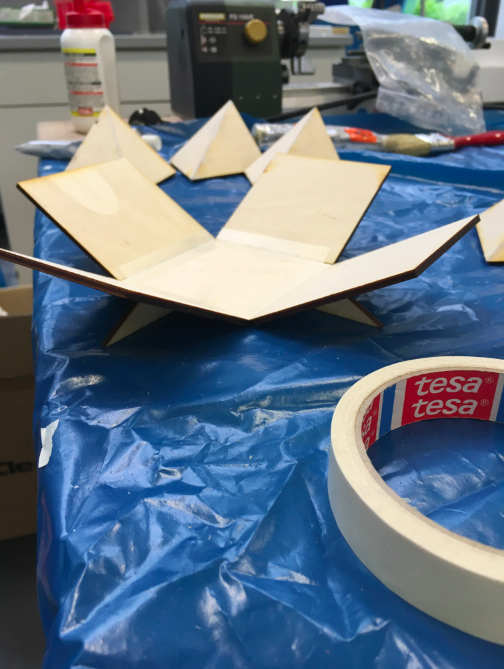
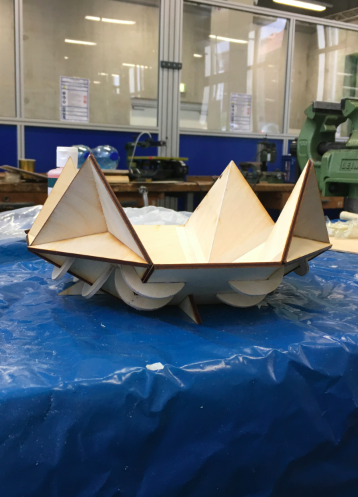
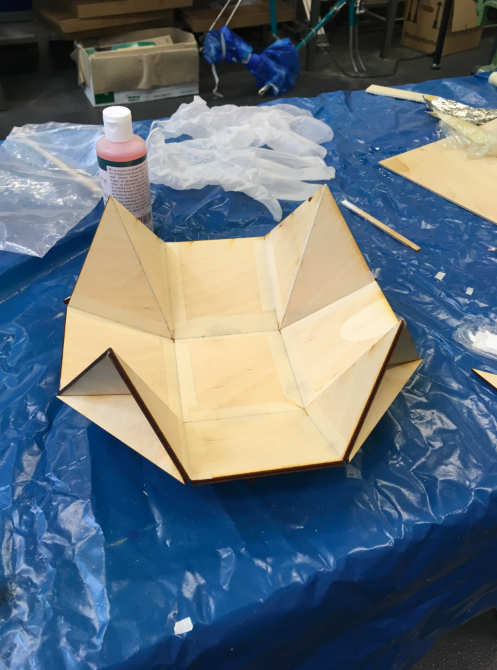
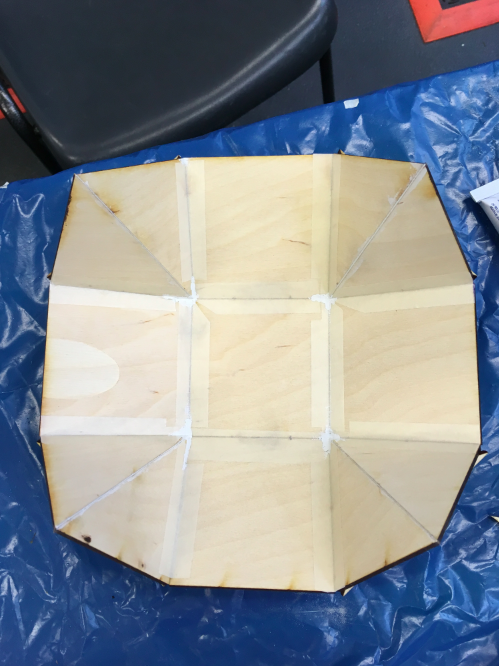
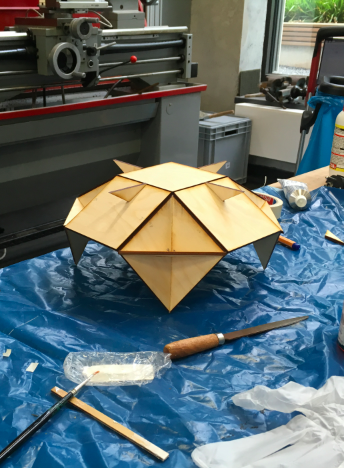
Above, you can see the build up prozess and the finished form from different perspectives.
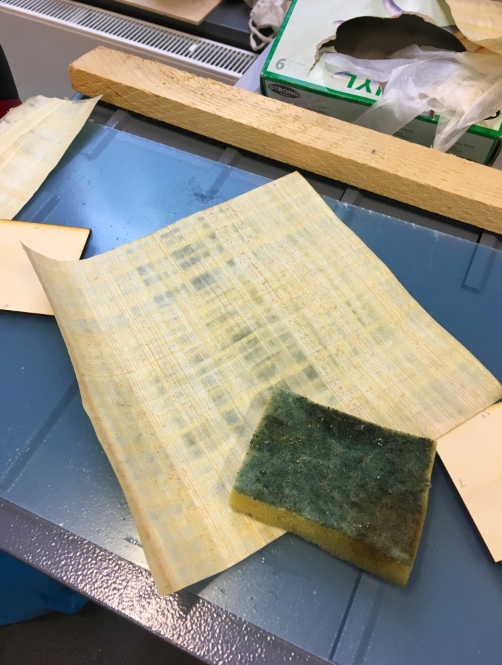
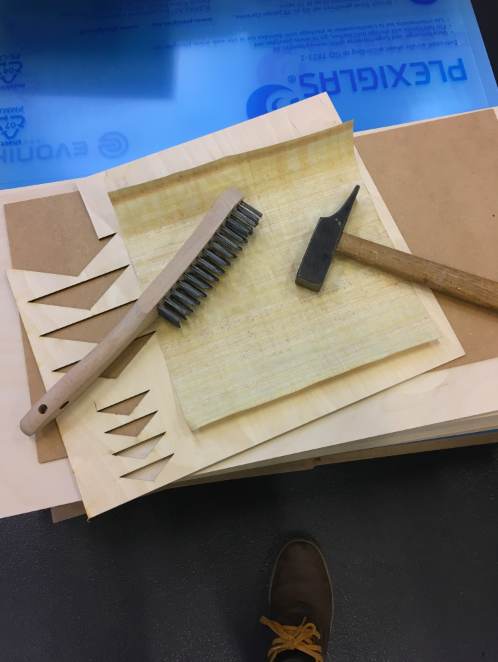
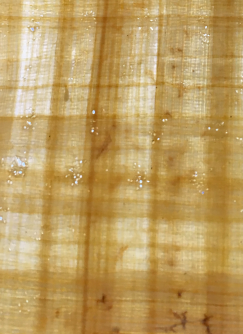
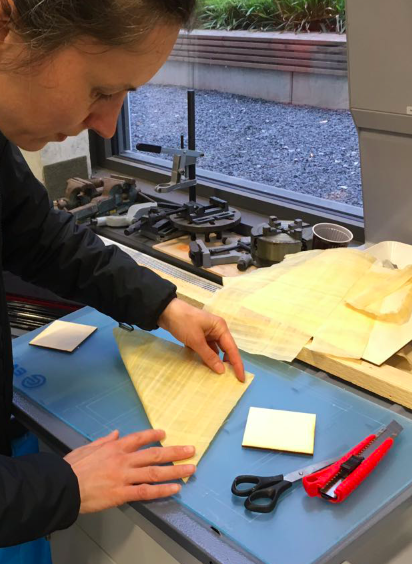
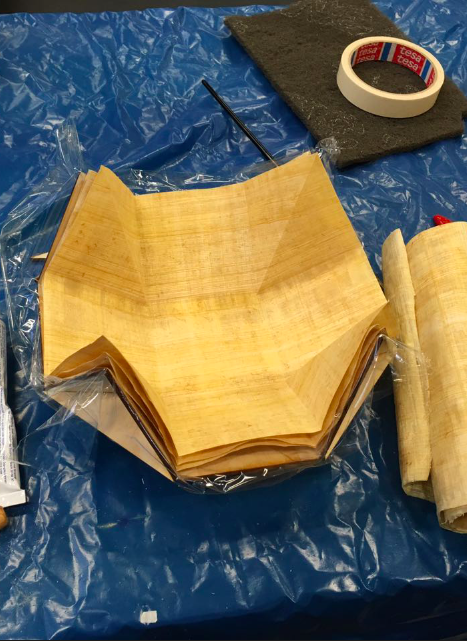
Now, it was time to prepare the papyrus leaves. The leaves are quite brash for folding or squeezing into a 3d shape. Also, papyrus is made in layers and, exept of water, the resin isn´t able to soak the leave layers. So, I wet them first, cut them into a right shape. I couldn´t lasercut them as my papyrus leaves tended to bend always. I cut out a piece of wood and used it as a template. In this wet condition I perforated the leaves with an hammer and a steel brush. I got a very natural perforation structure. Then I prefolded them and let them dry in the wooden form.
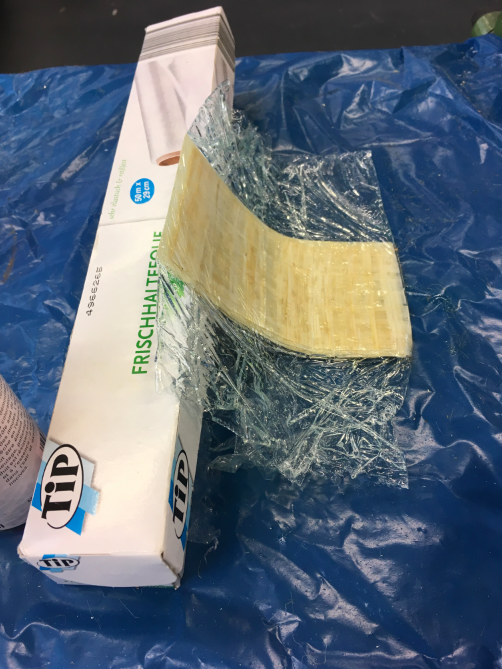
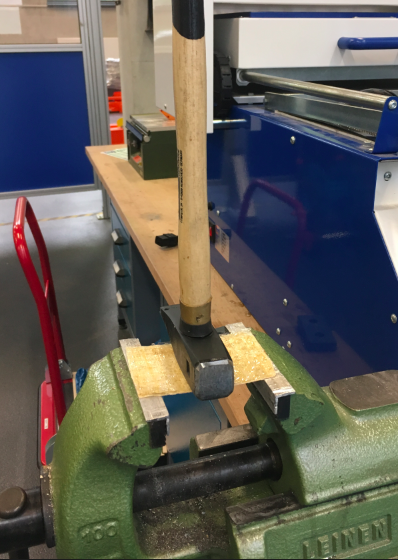
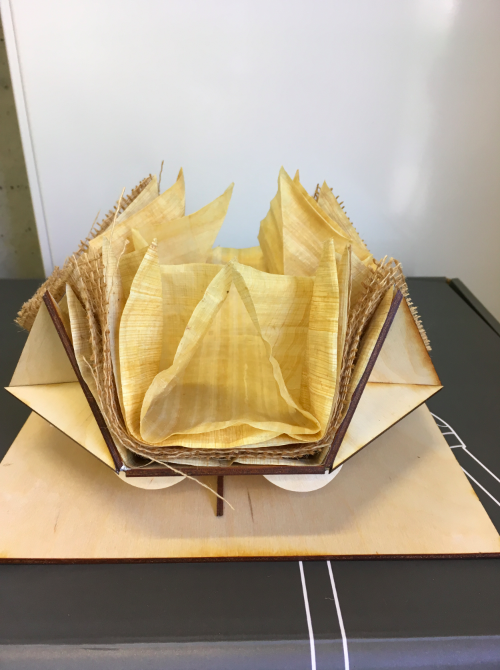
Above you can see the first failed test. The plate just didn´t get stiff, may be because the papyrus was still wet. Second test worked out but it is a very thin plate, so I decided to add some layers of jute. Left picture shows all folded papyrus layers and jute.
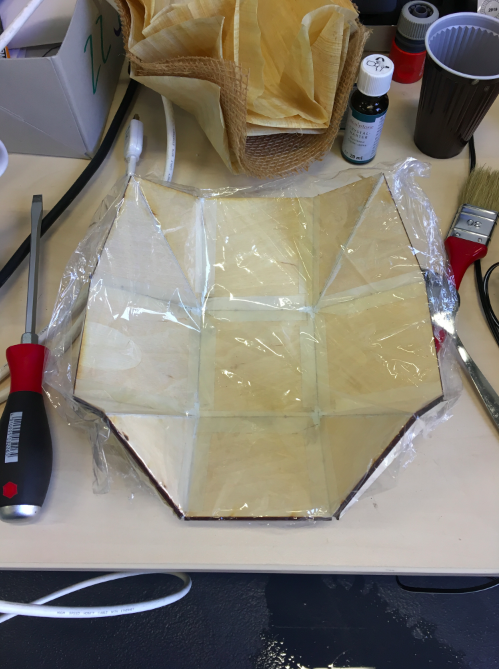
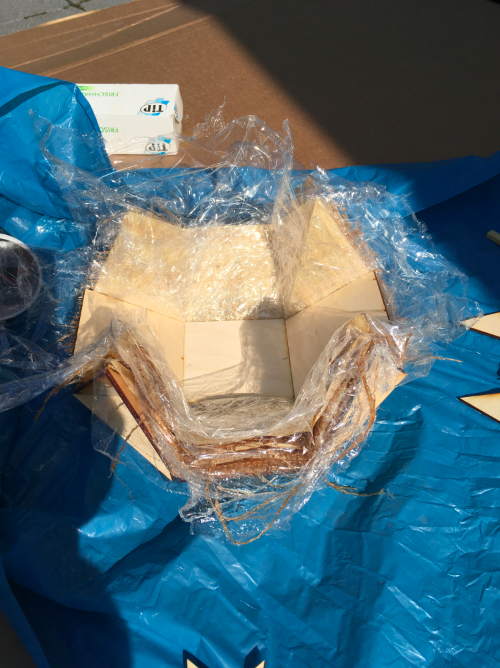
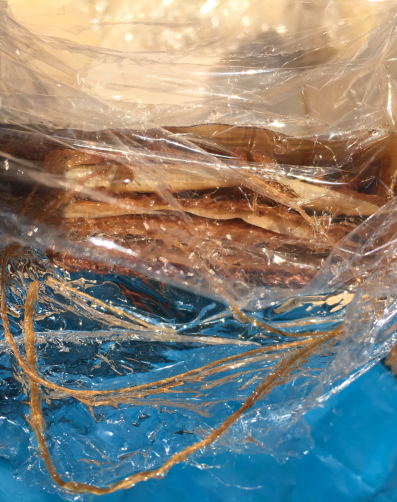
Now, I prepared the wood with releasing agent and put some stretch foil on top to get sure. Then I soaked the layers with the resin and put the layers alternating. It looks wild and I hoped it would be good, finally.
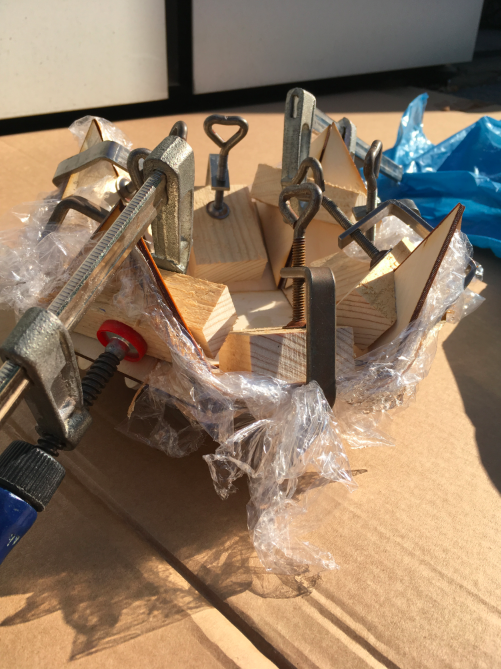
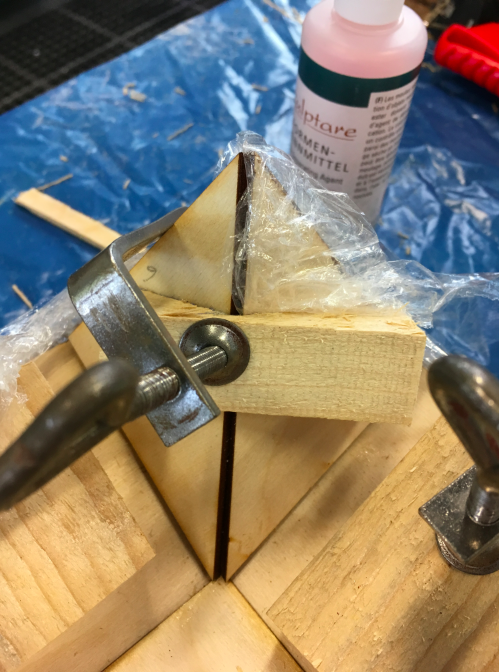
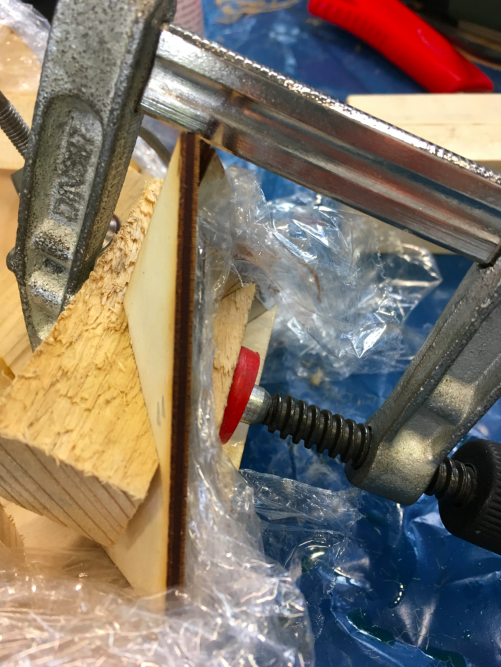
Then I had to press it. The shape was not usefull for vacuuming because of the sharp edges and somehow I thought it is better to do a concave form the convex. I cut out the same pieces and used them for squeezing with clamps.
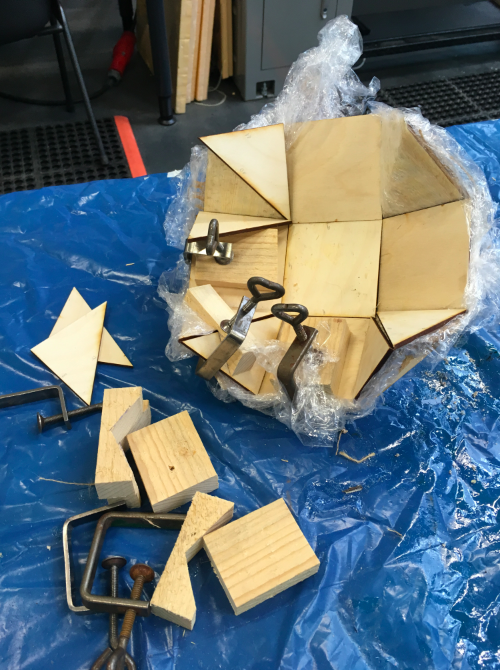
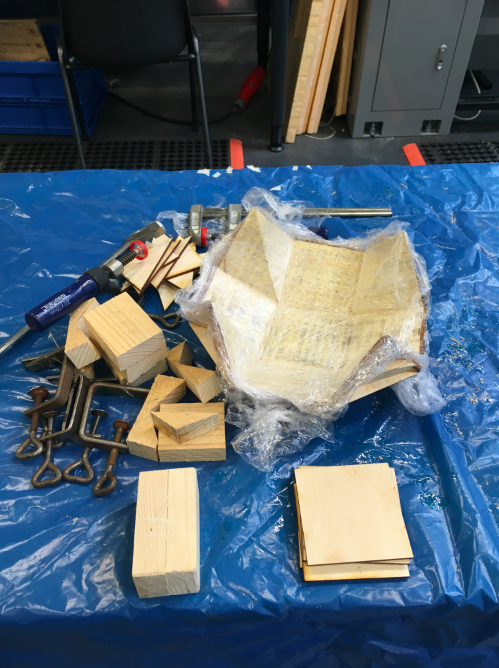
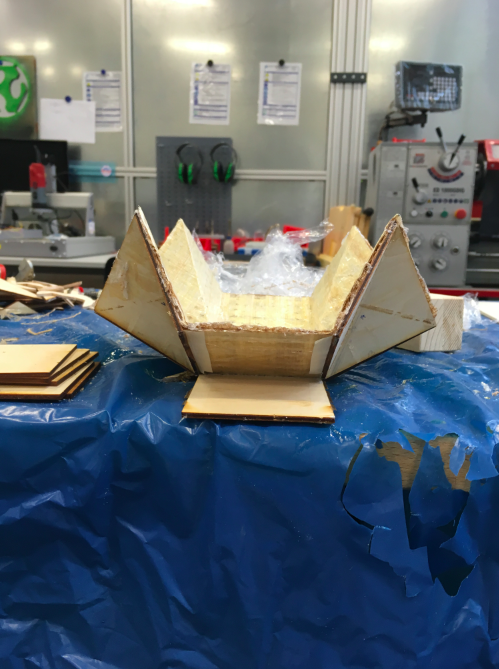
After 2 days I dismantled the shape. It was still sticky but very strong. Dismantling prozess was no problem because I´ve used stretch foil and releasing agent to be sure.
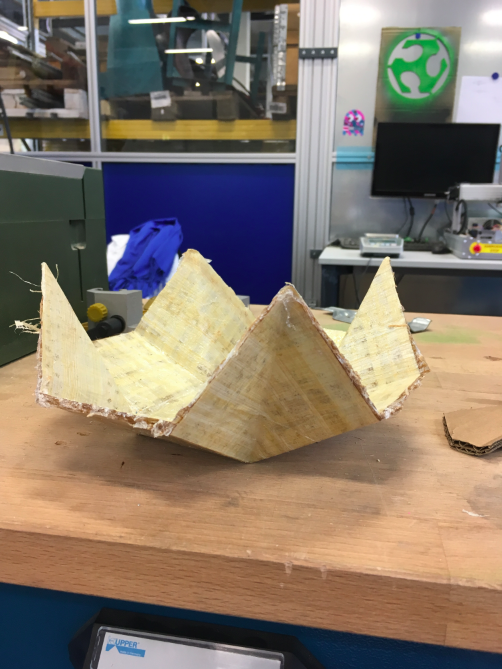
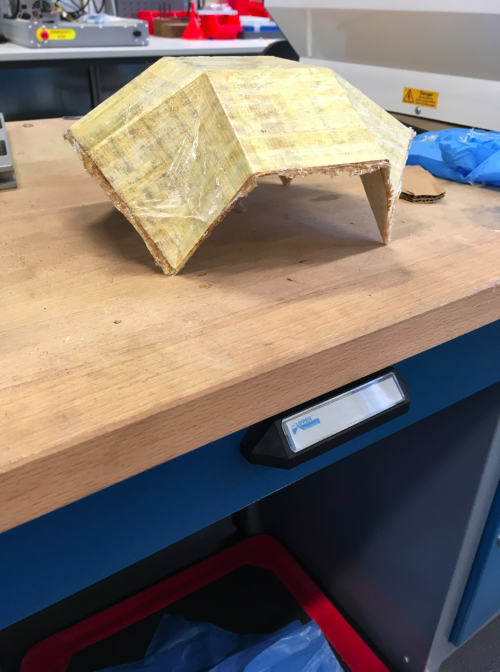
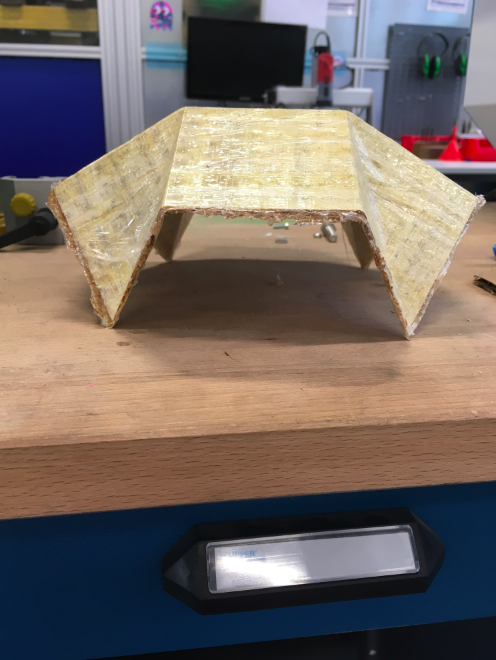
The bowl is filled with earplugs:
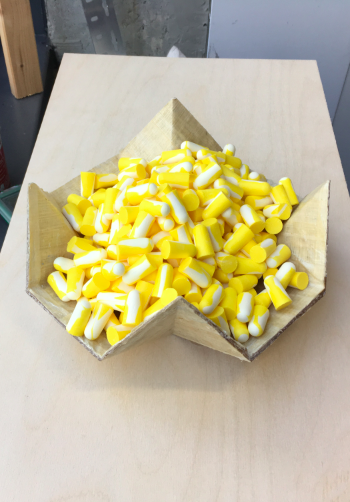
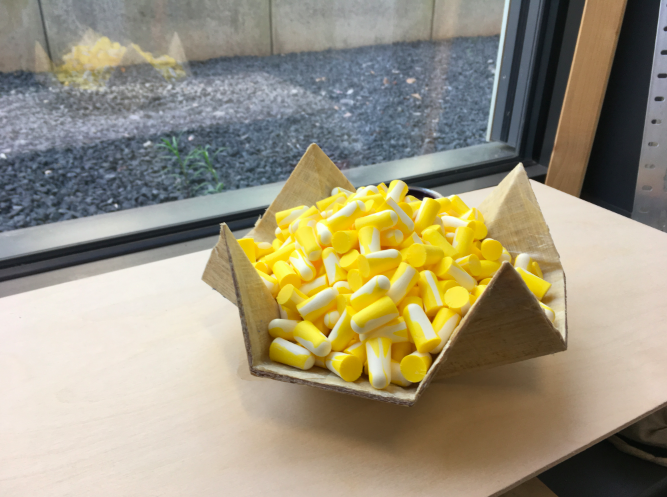
Below you can see some tests: left 56kg right 25kg
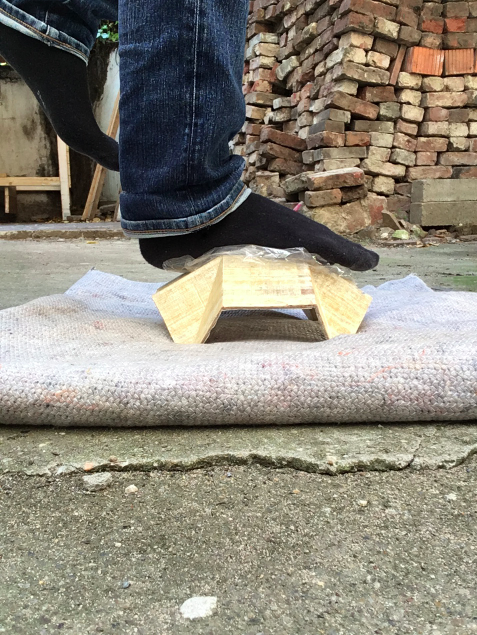
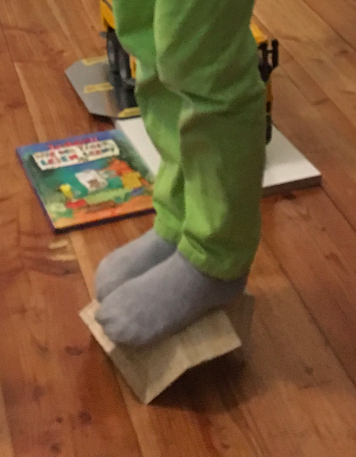
Tapping with hammer:
Download Lasercutfiles. If you want to press the form, you should cut out twice.
Folding in dwg
Folding in dxf
supporting triangles dxf