Assignment:
A_Make a machine, including the end effector.
B_Build the passive parts and operate it manually.
C_Document the group project and your individual contribution.
B_Build the passive parts and operate it manually.
C_Document the group project and your individual contribution.
B_Design and build a Machine.
I proposed to form a group to make a solar tracker project. Last year my greenfablab's mates initiated a project that never got completed and we can benefit from their know-how and experience. They had brought it to a point but it needs further improvement before it can be fully functional.
See the projecthere.
Grégoire Durrens, one of the member of the group, is the former GreenFablab manager and will be leaving soon. The machine will than sit around unless we have him share his knowledge and bring it to a next level. I find it would be good to give the project a continuity and at the same time pay a tribute to his work benefiting from the knowledge he leaves at the Lab. Taking it one step further.
I am interested in this project mostly because it goes in the same direction as what I want to explore for my final project: self-powered artifact.
The team was quickly formed team (Jean Christophe, Trinidad, Dom and I). We met with Grégoire to get advice, share his experience and get a better understanding regarding the design and strategy he used. He had developped a light sensor system for 2 axis (calculation made by barrycenter) that is very interesting. It requires complex programming in C code and that may be too complex for the skill level of our team.
Gregoire recommended we start with a simpler version with only one axis at first (horizontal) and add the vertical axis as we go along.
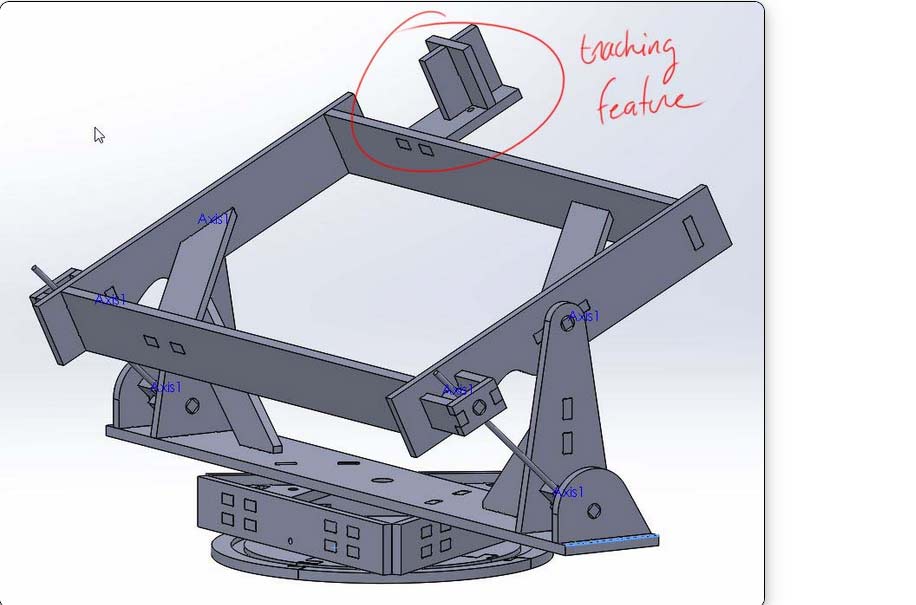
After meeting and brainstorming with the team members we decided to create our own original design avoiding to have the whole tracker move when the panel rotate. We had doubt whether to focus on only one axis (tilt up and down) or go for 2 axis integrating horizontal movement as well.
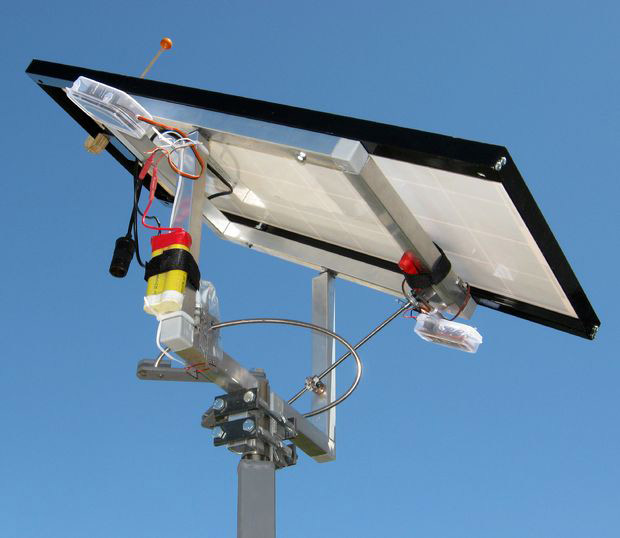
At first the dynamic of the group was a bit difficult We had difficulty and that translated in delay in taking decision about which design we will make. In the meantime I started developping few concepts and presented 1 options that I laser cut.

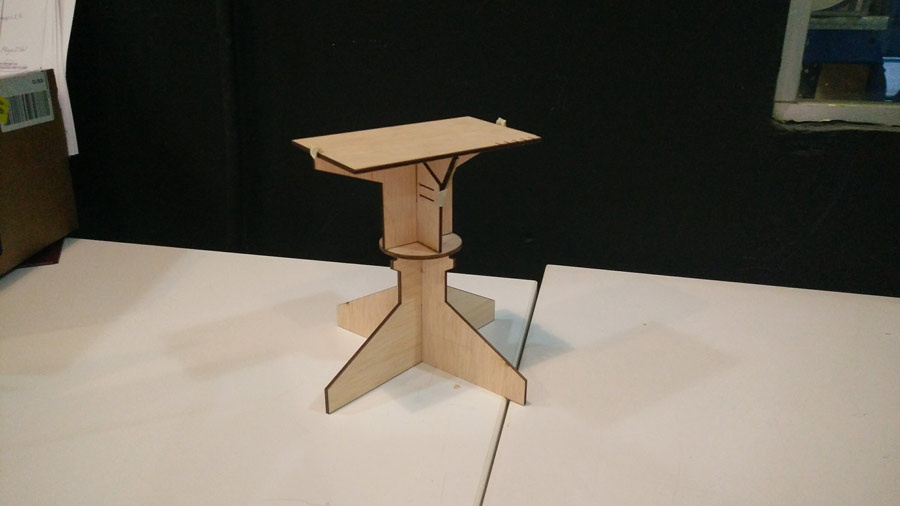
Discussing with the group we decided it would better to work a bit further on the design and find a solution so the panel is not held from each side but from a central support that distributed the strenght. I came up with this idea and started developping it.
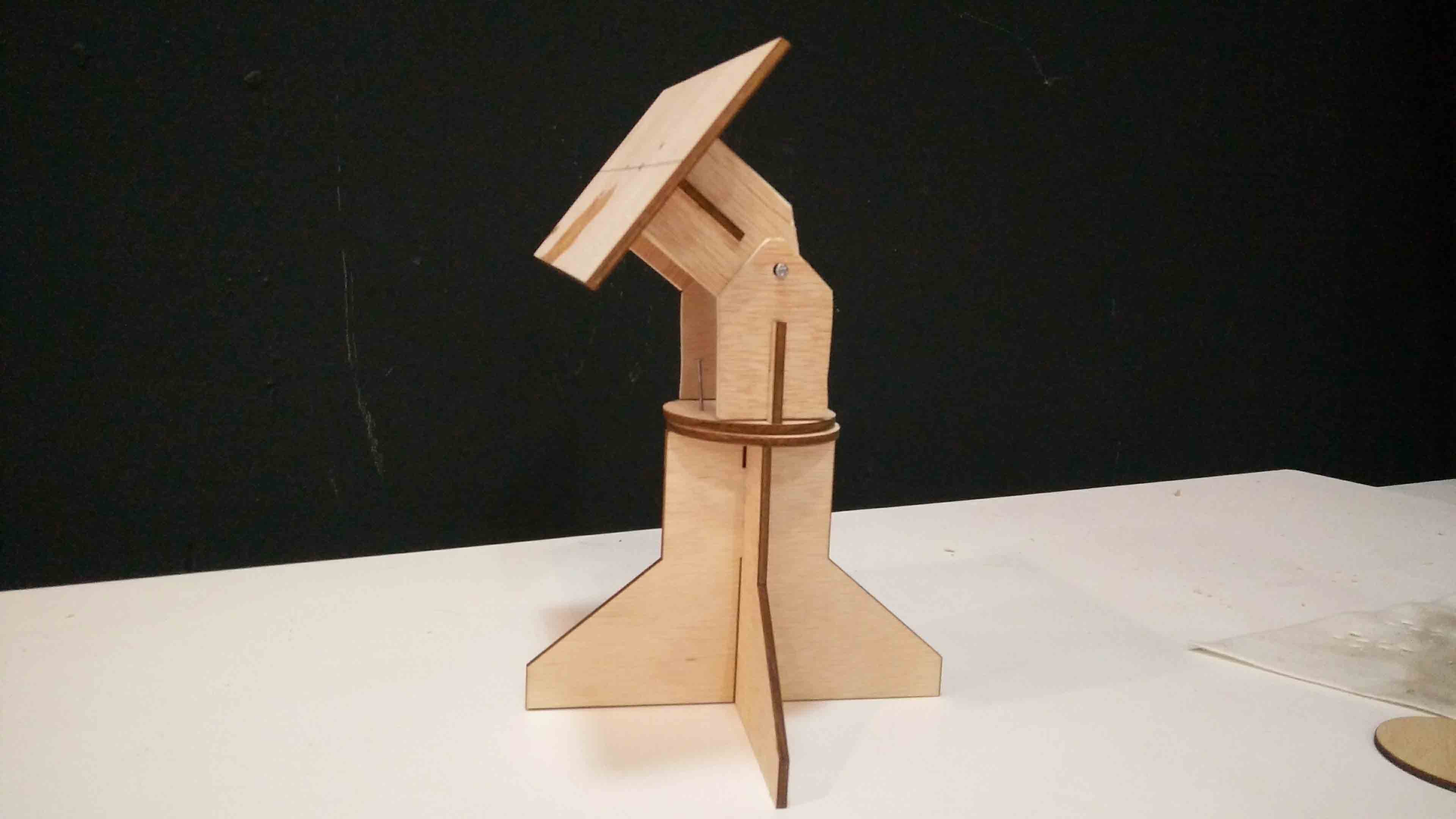
I did other iteration in which I went a bit futher to find a better balance and taking in consideration the components that will need to be integrated for the movements.
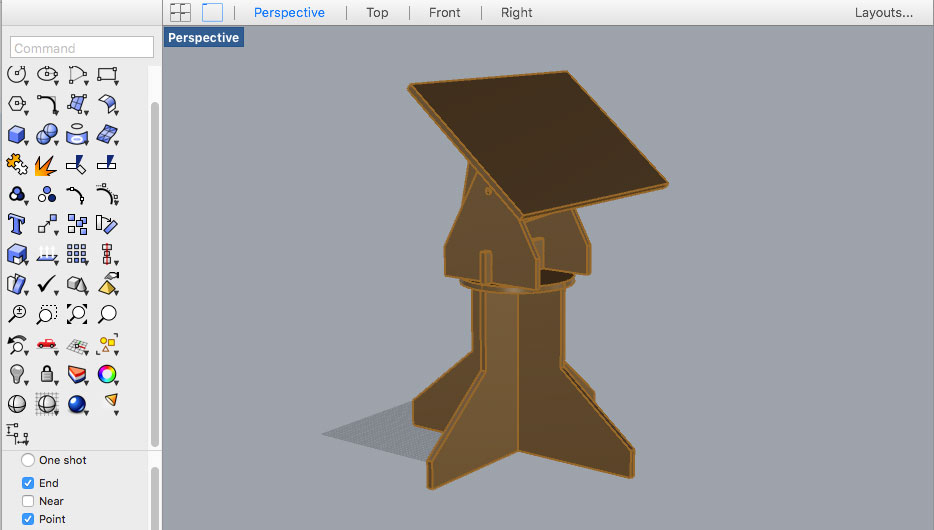
I cut a model with laser to test the sizes and proportions.
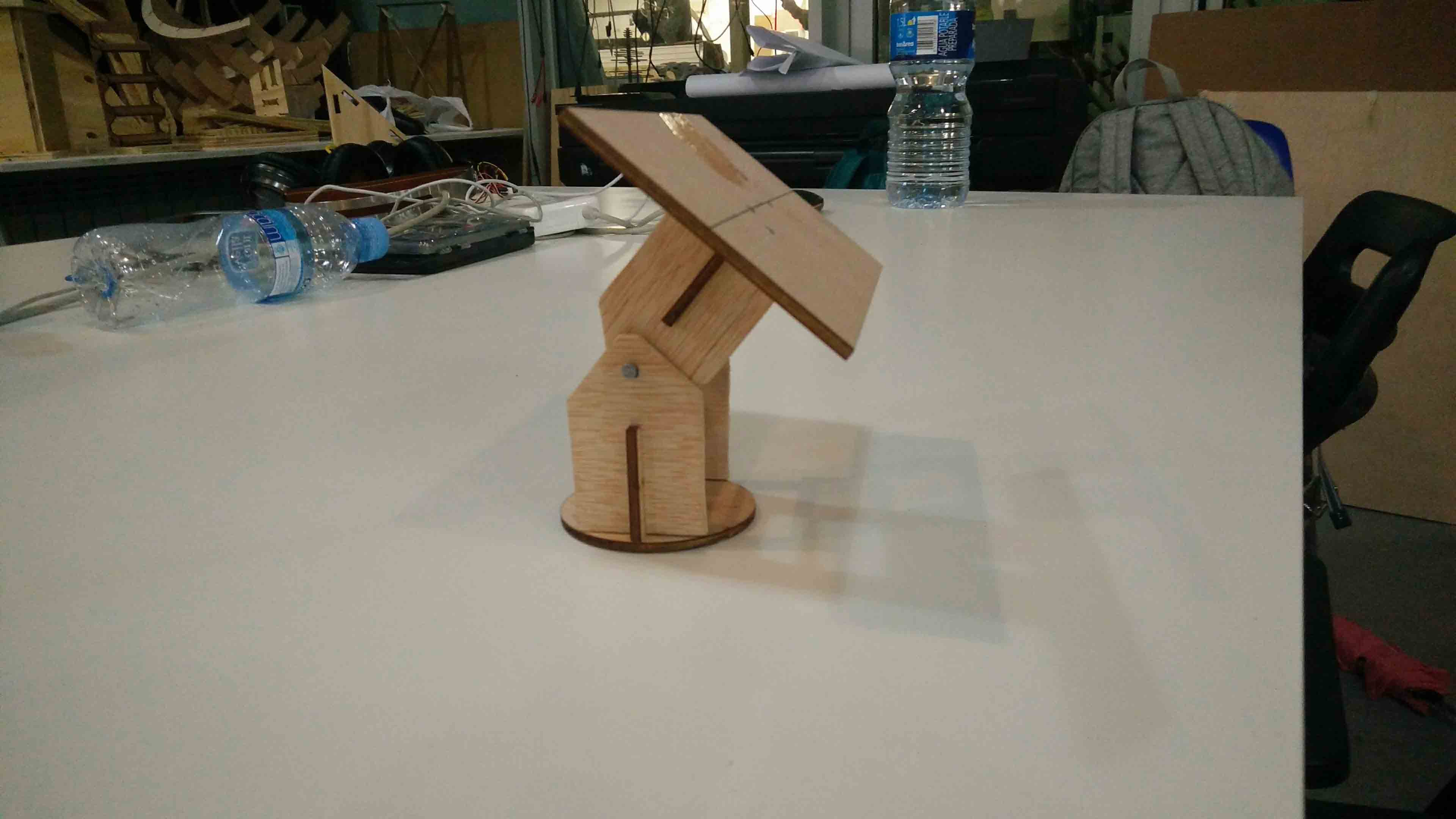
My focus was to design a tracker that can be made using as much as possible technology and materials that are available in the Fablab ecosystem. For that reason I chose design for flat material (plywood or such). I struggled with deciding how to make the panel swivel - either with a gear or a linear system option. In these model none of those issue are solved. It just shows a very summary representation of which directions we were going. Balance and proportions need lots of adjustment and thre rotation system, gears need to be designed.
On friday afternoon, after presenting the different options to Martin Seymour and our instructors the group agreed to take a new direction and we delegated to one of the member to develop it over the week-end and bring a design for Monday so we can start working on the actual making of the machine.
On monday morning the new design was not resolved and so after debating we agreed to go back to the swivel idea and agreed I would further develop my original proposal. We also decided to split the work in sub-teams. Trinidad and JC will focus on programming while Dom and I will take care of the design and mechanical part of the machine.
I made iterations of the model adjusting the proportion, reducing the weight and better compensate the counter-balance of the tilting part.
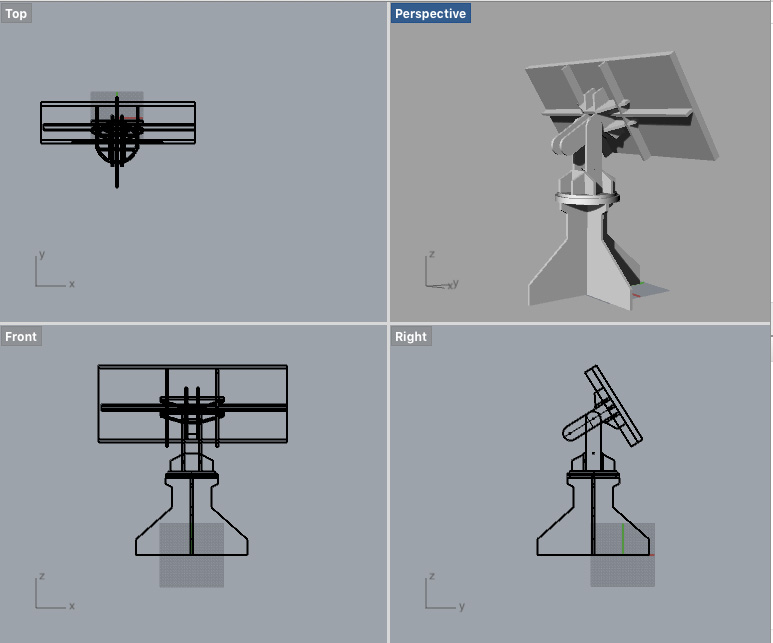
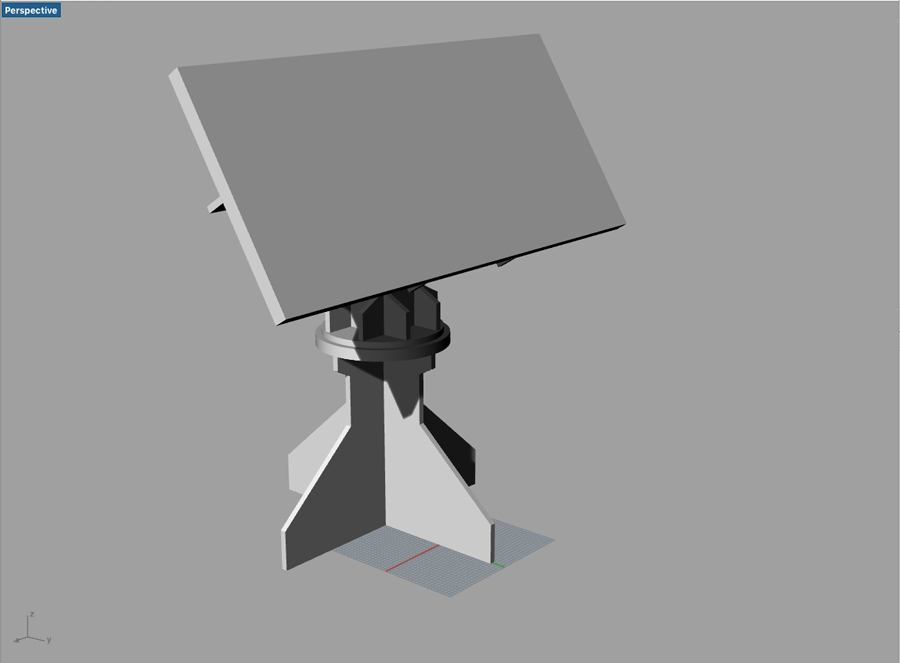
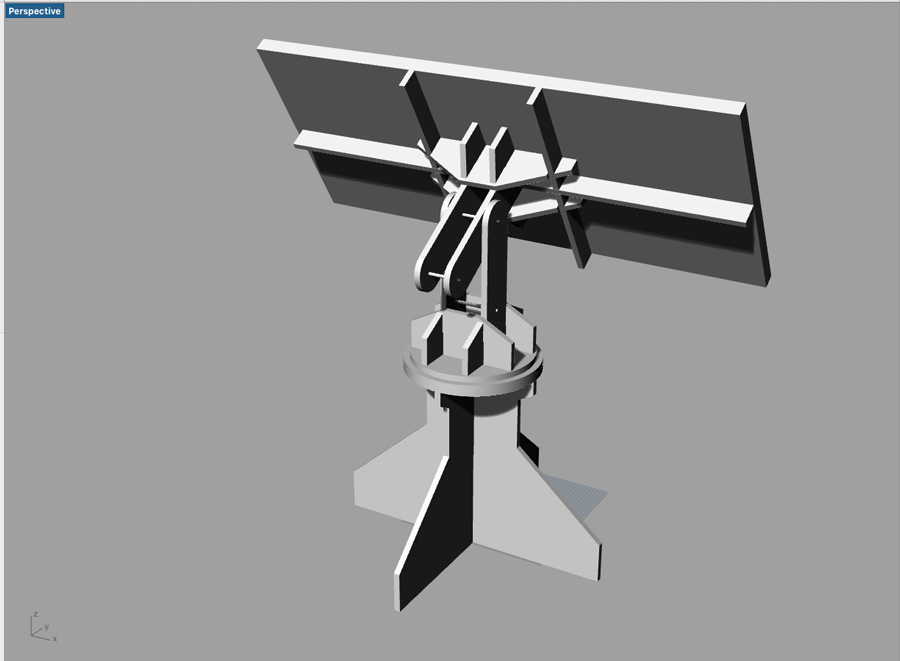
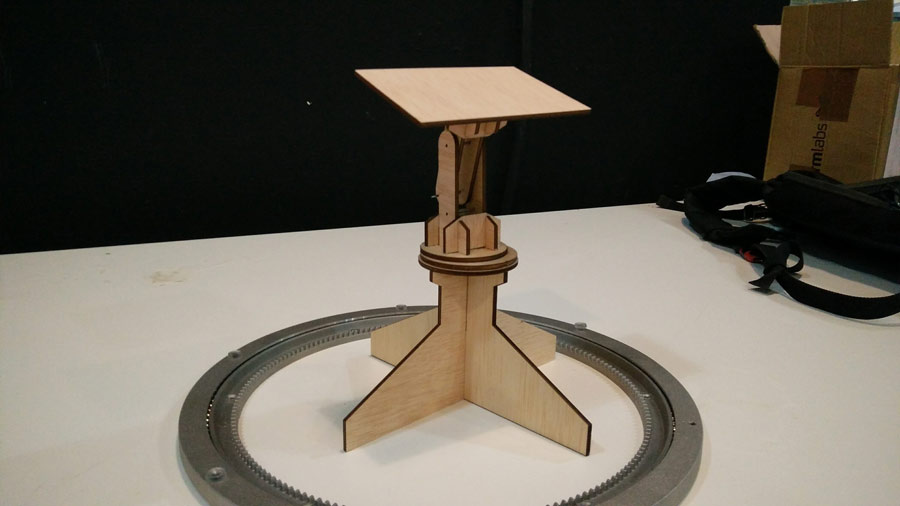
I also did some reasearch on the mechanical components and got some skate board bearing for the tilt movement and a "lazy susan" for the swivel. I found one at the hardware store with an integrated gear on the inside part. We are in the process of designing the gear to be 3D printed and fit to the motor shaft.
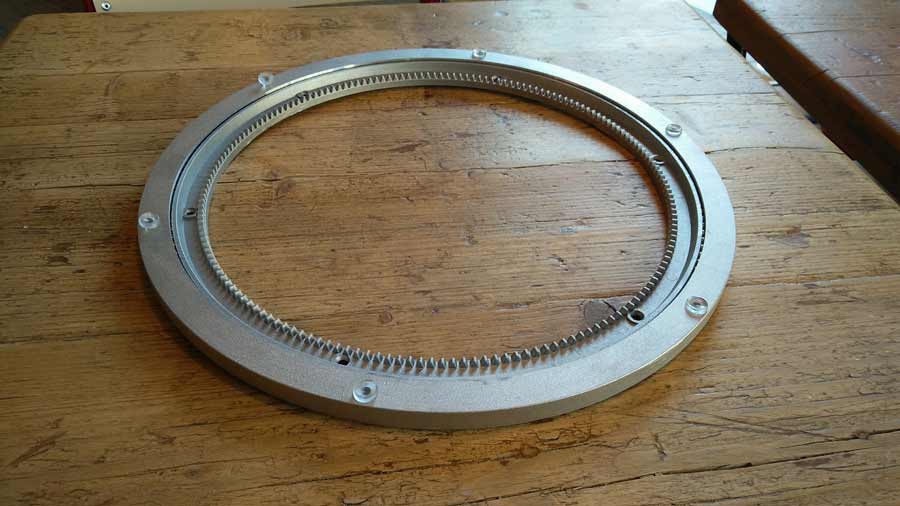
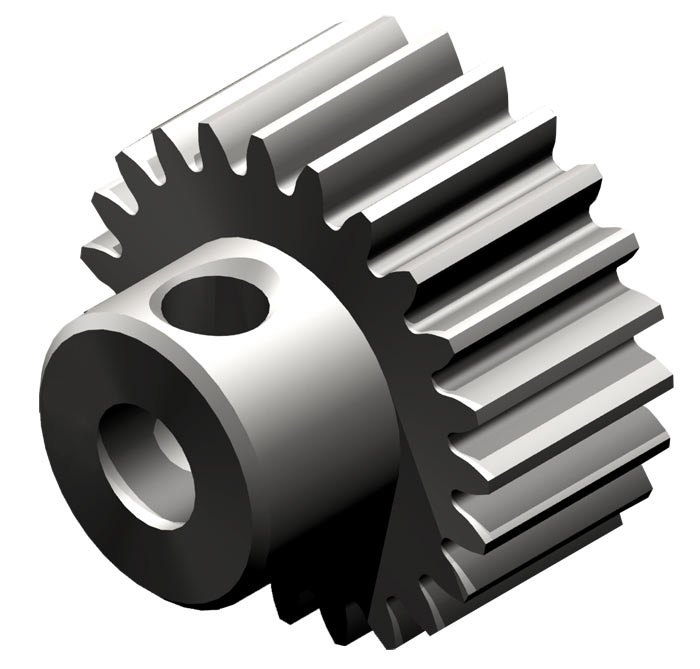
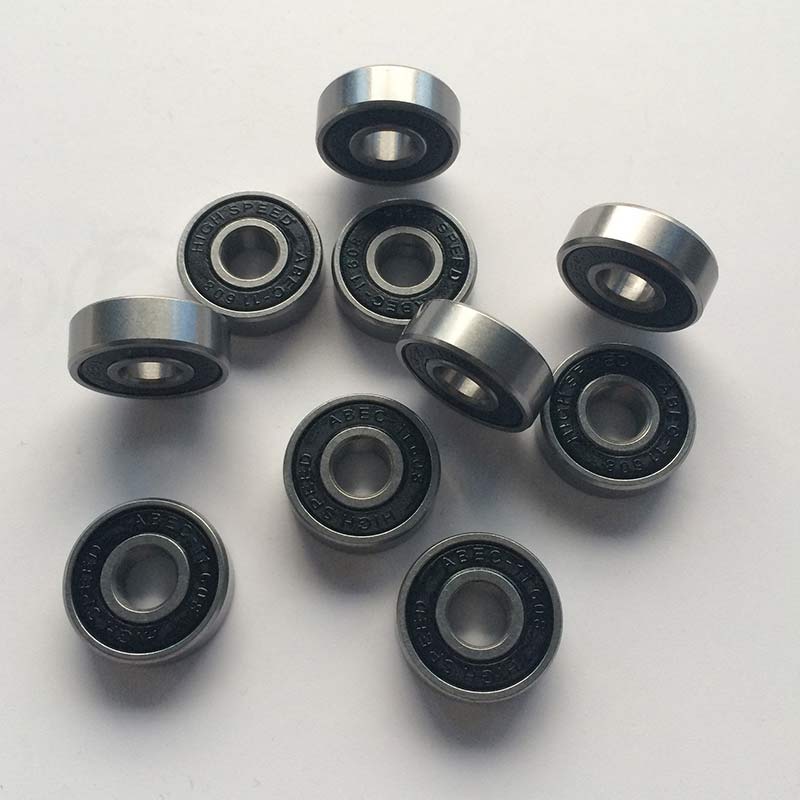
Next step is to do milling test with 15mm plywood to make shure the tolerance are right and adapt the Rhino file to the material, make the cam file, the Gcode and mill.
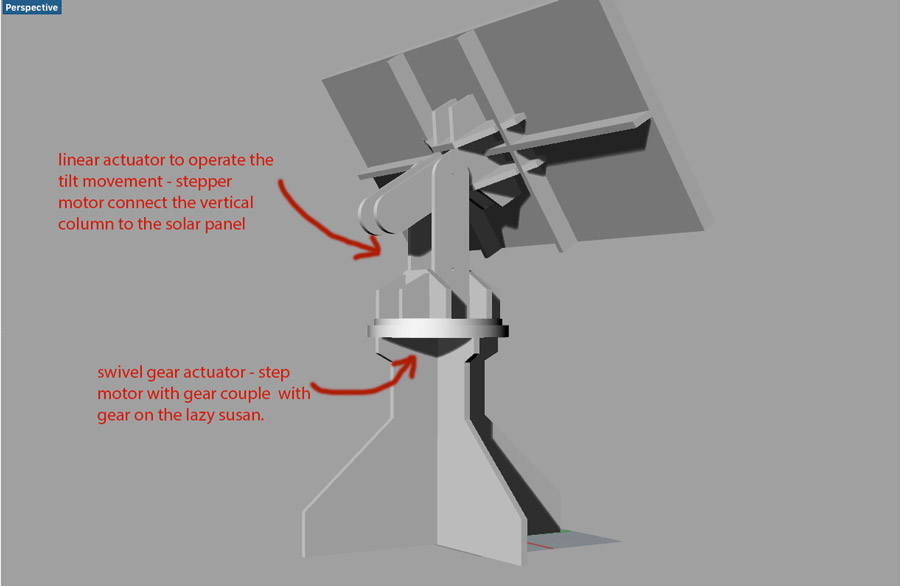
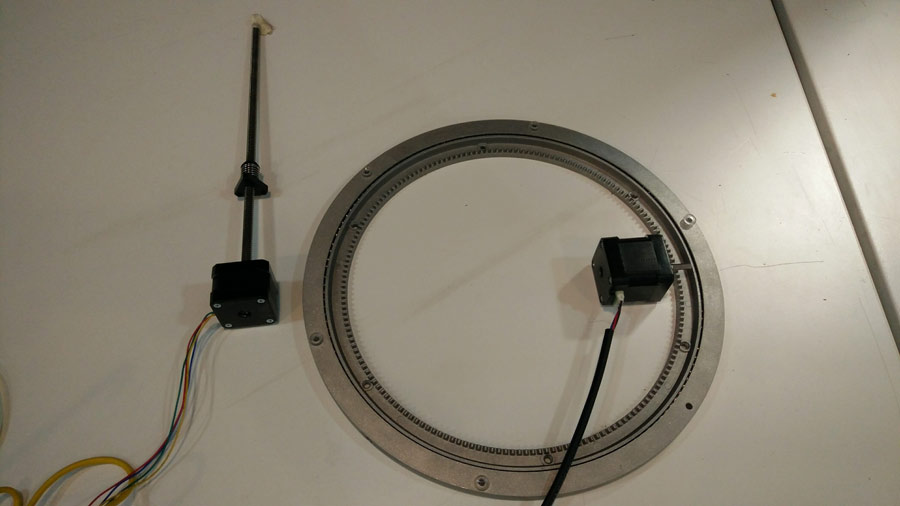

Working on making the right gear I did a putty casting of the gear of the lazy susan with the the intention to 3D scan is with the Modela.(the actual lazy susan do not fit on the Modela bed.
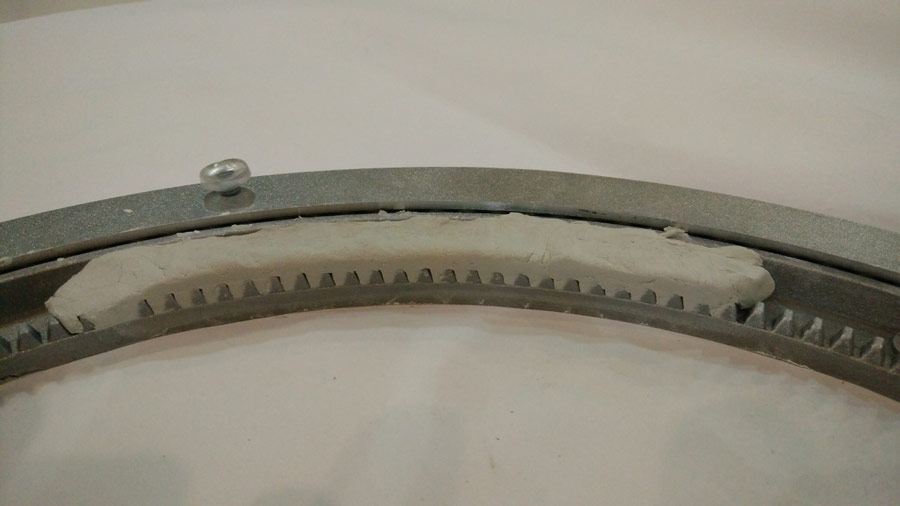
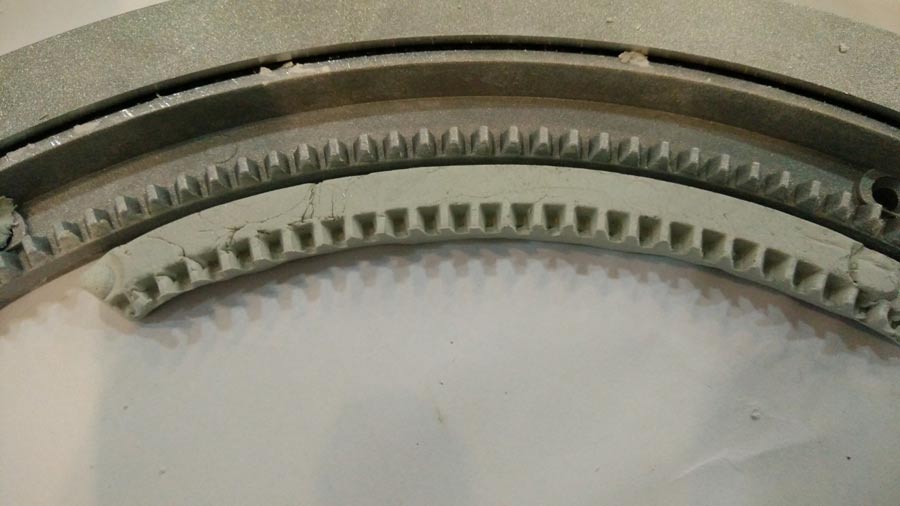
Here the link to the group project.
Here some solar tracker references I had researched.
DIY solar tracker
DIY simple idea
schematic diy solar panel
Sunfolding system
I have learned a lot about Rhino, most particalurly working with the 4 view front and developping a dynamic workflow.