Until 10 May 2017
Digital Bodies, Composite Mannequin
Contents
- Digital Bodies
- Milling Mold using CNC
- Composite Process: Vaccum Bag Mold
- Finished Composite Mannequin
Digital Bodies
Most commercial mannequins comes with standard size. I remembered the lecture from Textile bootcamp and decided to make a digital body. For this composite week, I tried to mold myself using 3D scanner, CNC, and vaccum bag mold. Through this process, I had a better understand of composite process, my posture and my figure.
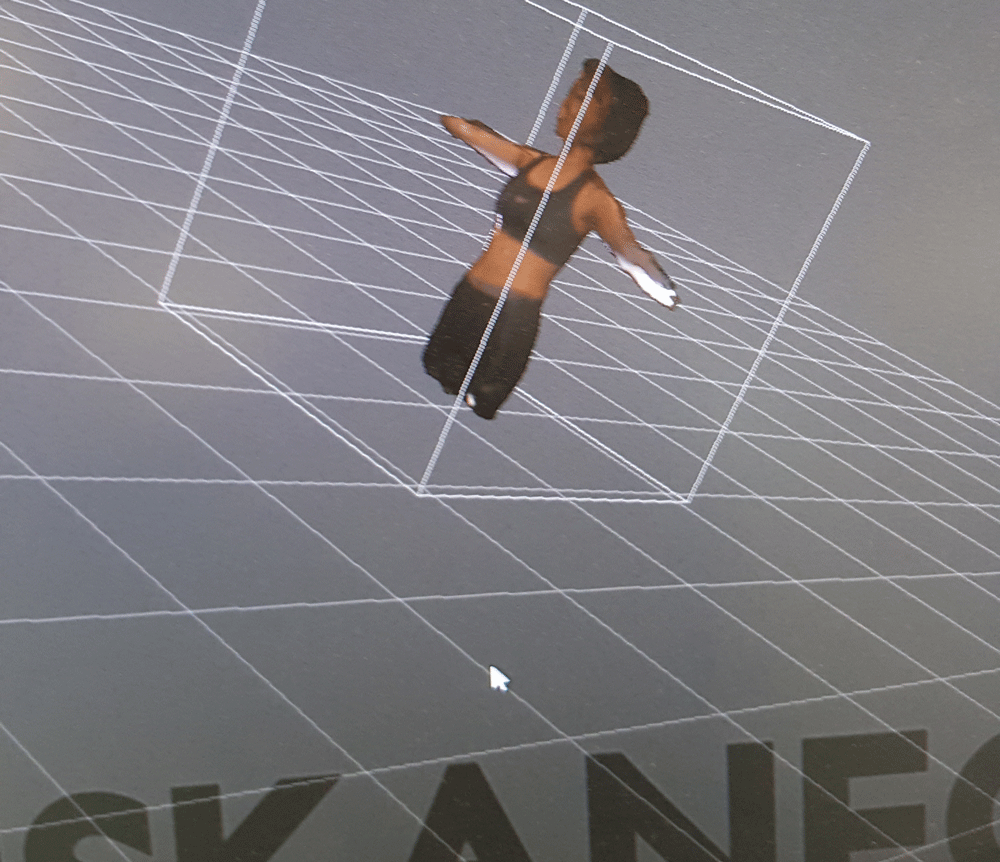
I used both XYZprinting 3D scanner(on top), and Kinect(at the bottom). For this purpose. I had better result with Kinect.
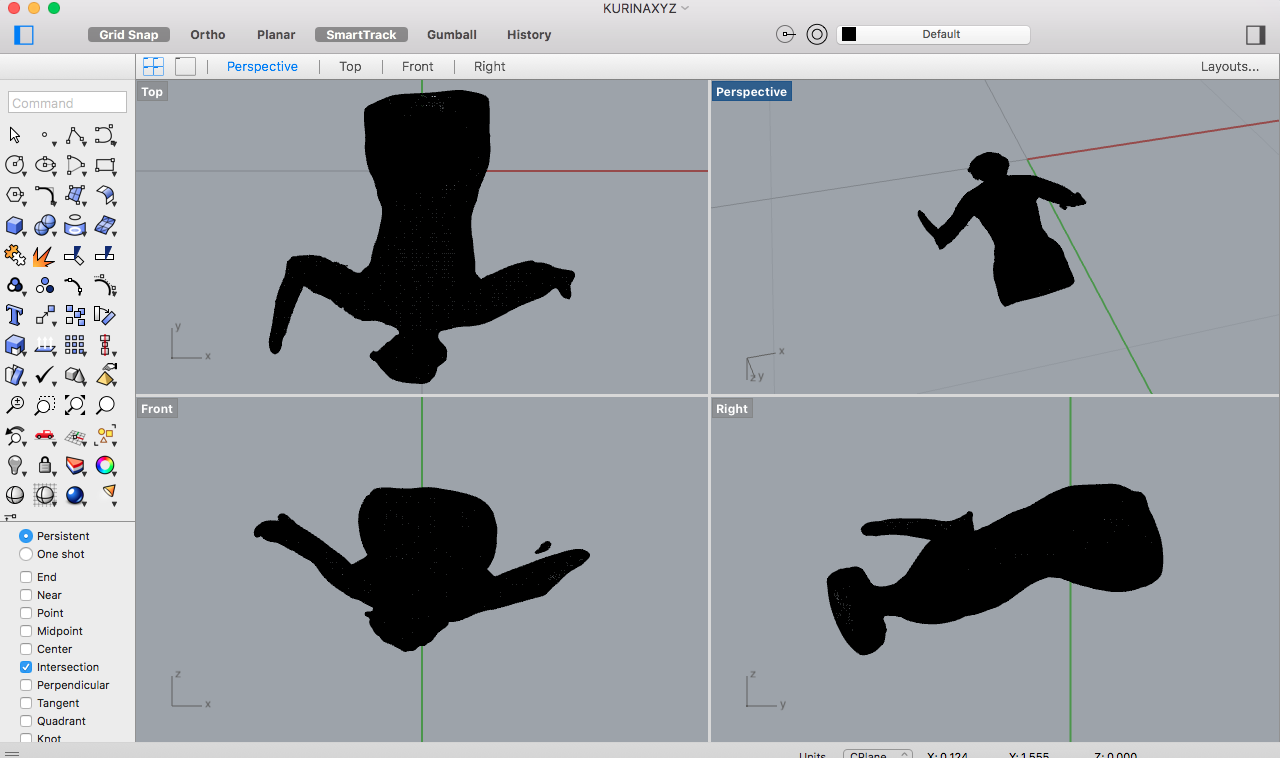
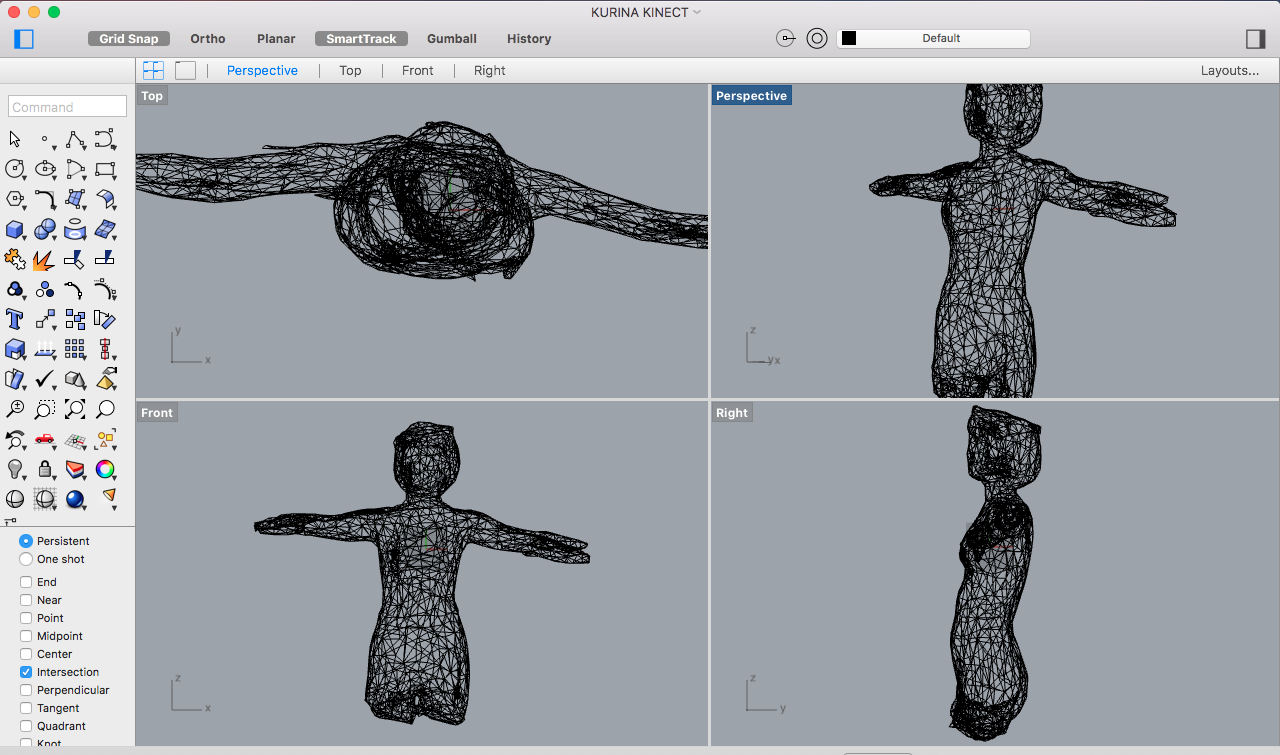
In Rhino, I modified my figure: cut off my arms, bottom, split front and back.
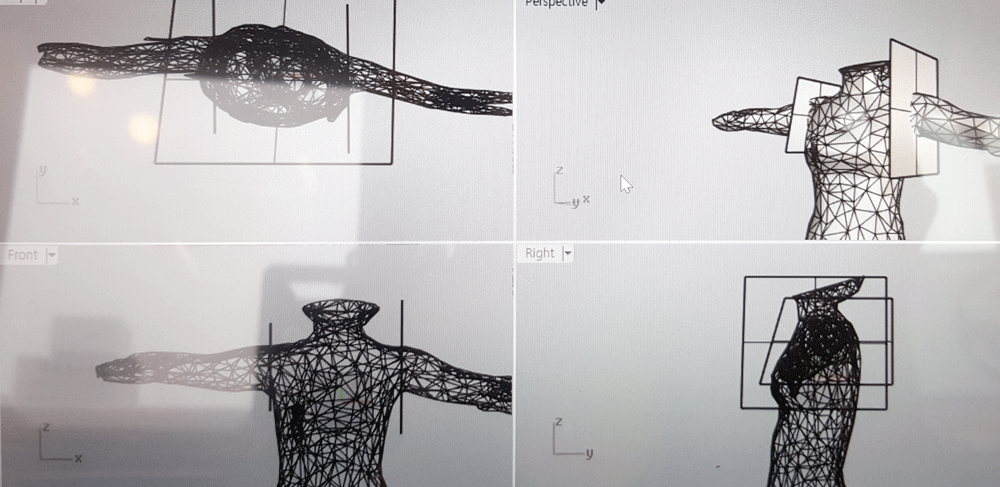
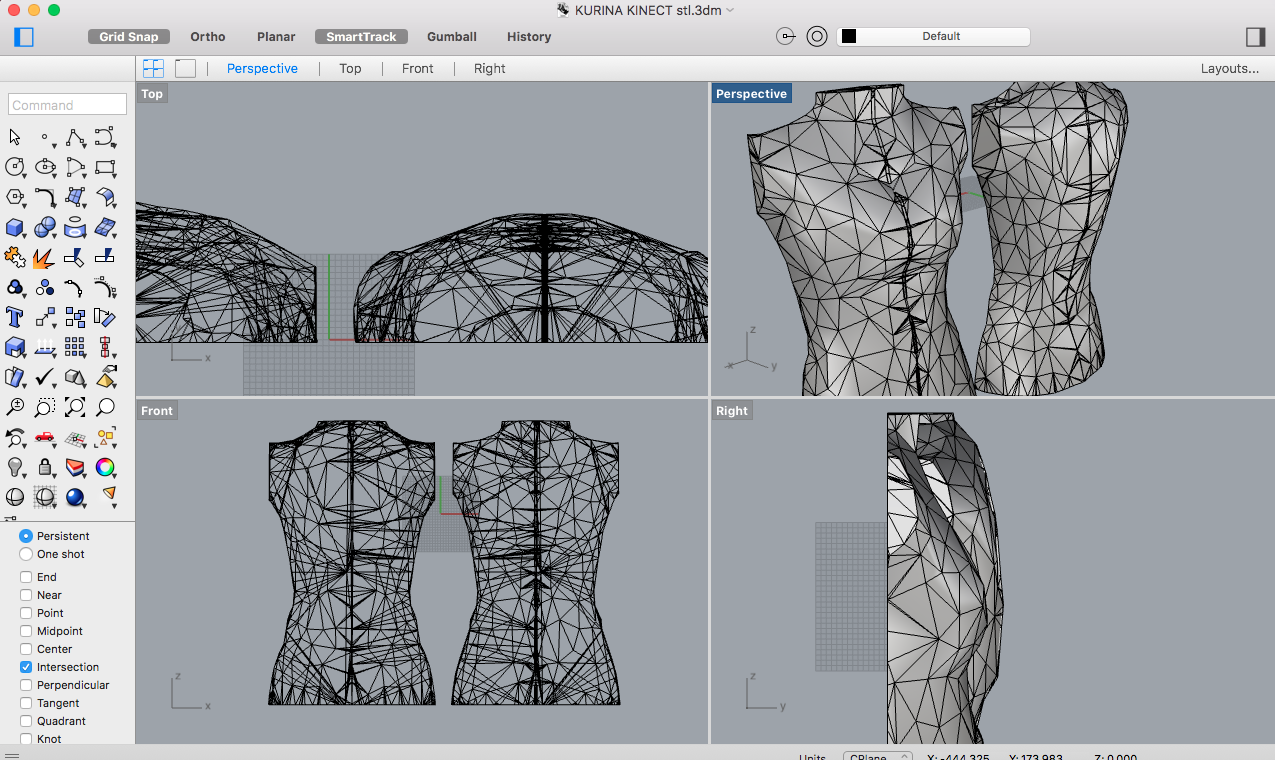
Aspire
I used aspire instead of Fabmodule, because of errors and time. I used 10mm end mill and 10mm ball nose.
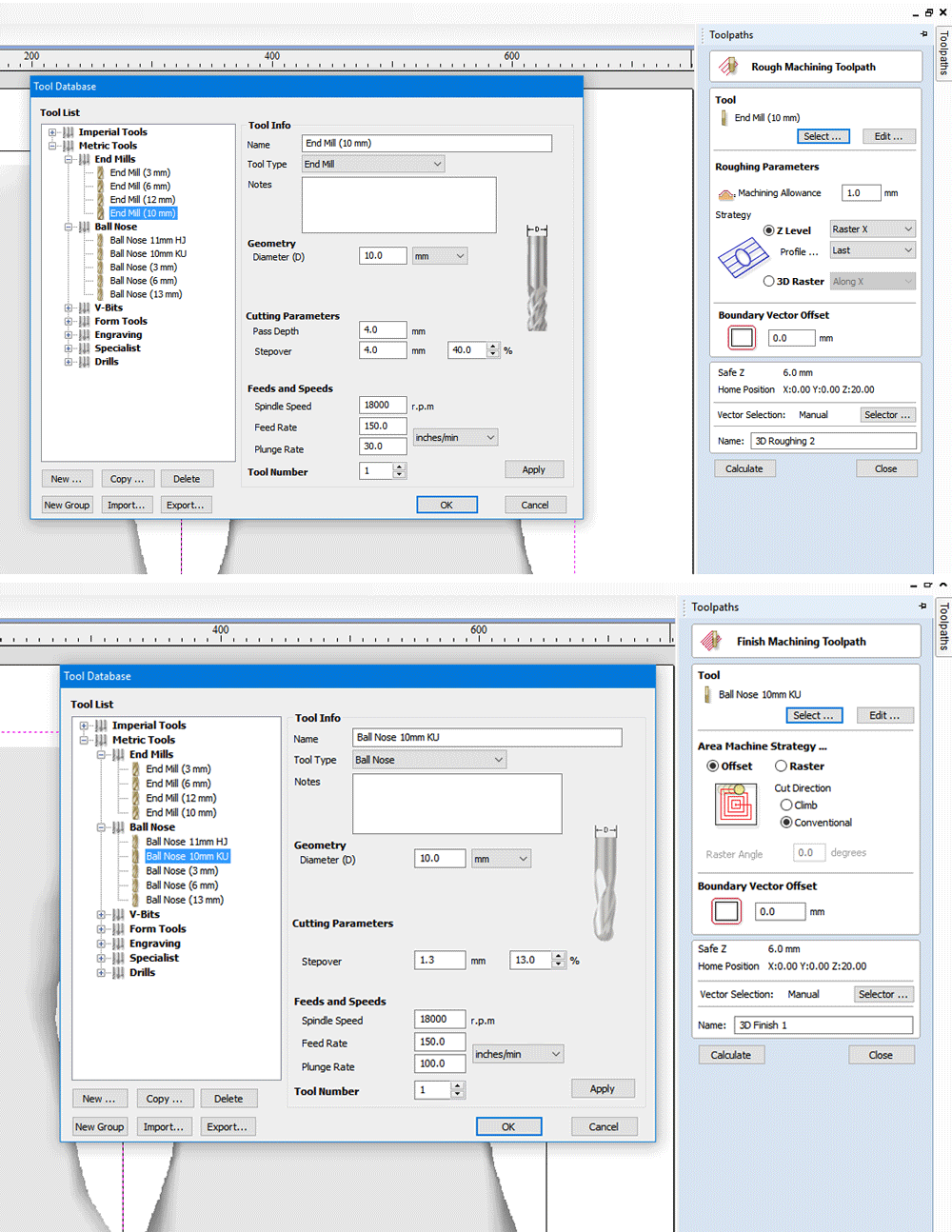
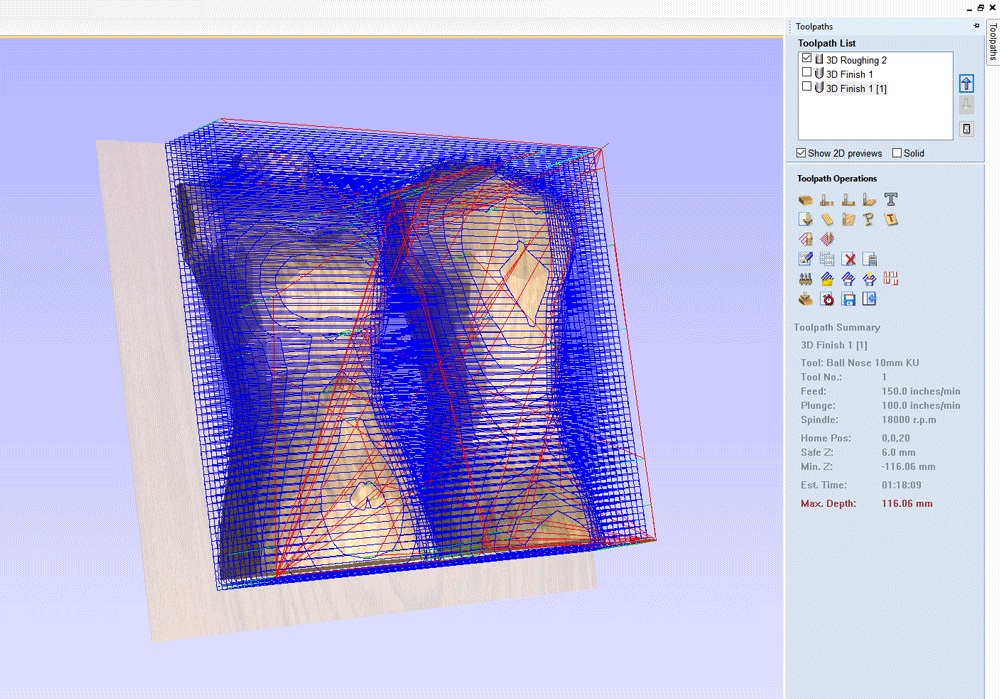
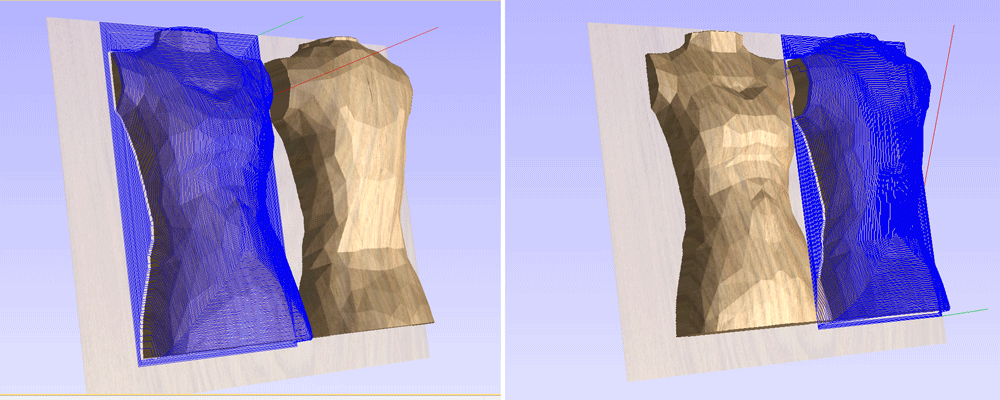
Milling Mold using CNC
For mold, I used extruded polyestirene. I've glued 4 layers to accommodate my figure.
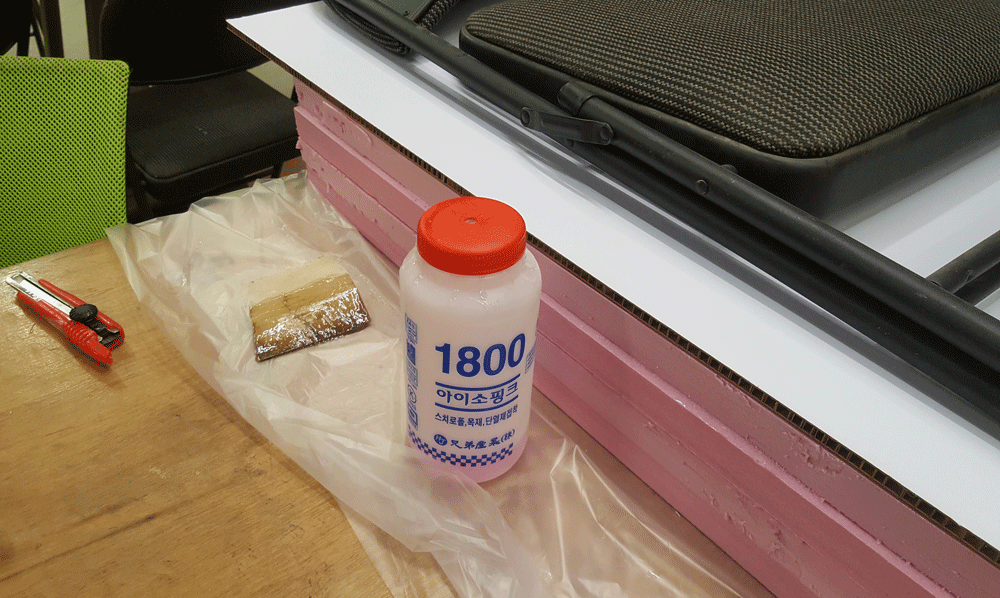
I had problem with shopbot.
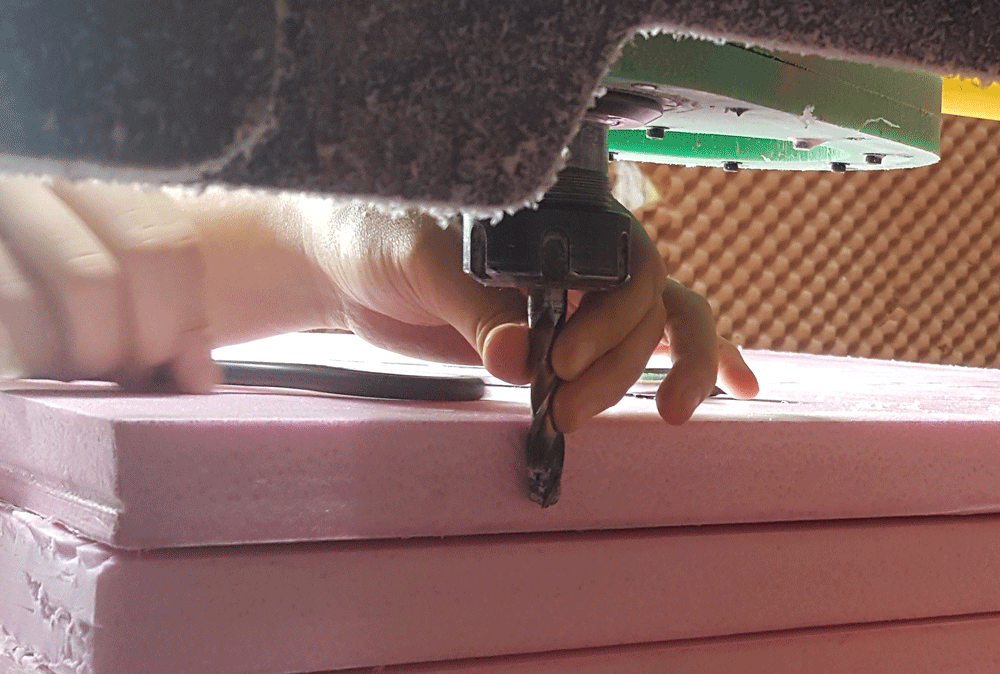
Because we didn't have enough space in the shopbot. Maximum height of Z was used. I reduced the cutter value of Safe-Z & A Pull-up() to 0, so I don't hit the soft limit.
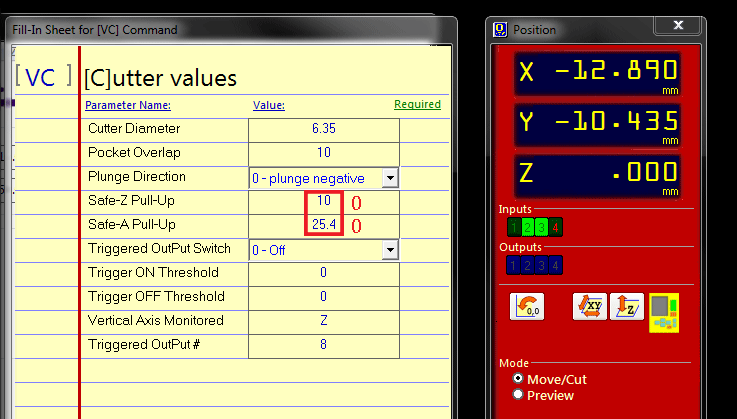
Rough Cut
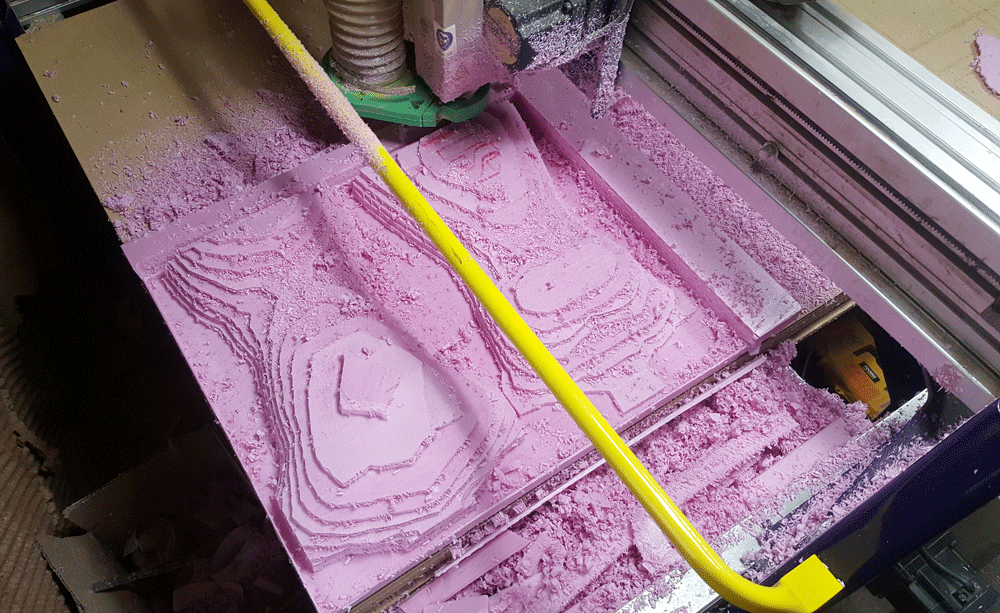
Problems: The glue didn't glue. I left the glued foam over night to dry, but it didn't completely dry. It removed part of the foam and glue got all over the end mill. Every layer of glue, I had to remove the glue.
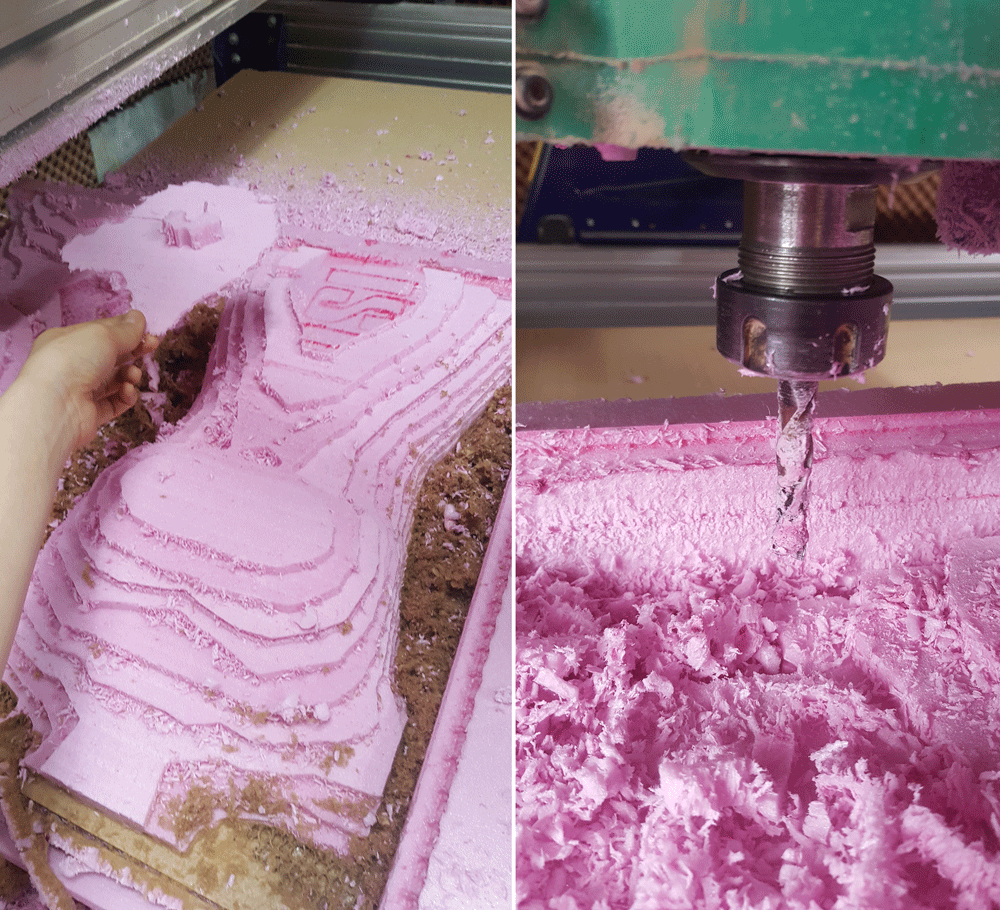
Fine Cut
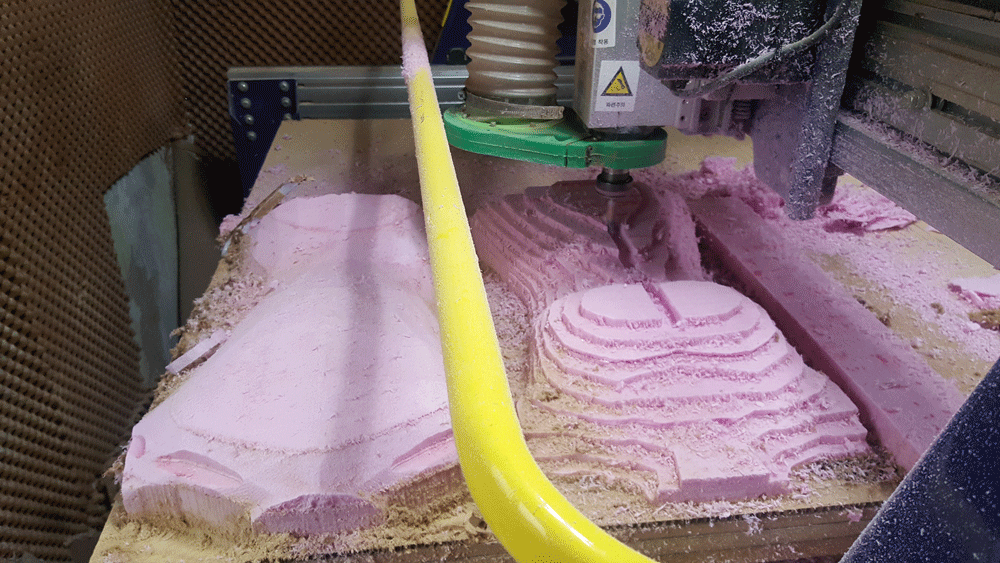
Problem: We lost Z. We ended up cutting too deep. Front cut 1cm more and back cut 5mm more.
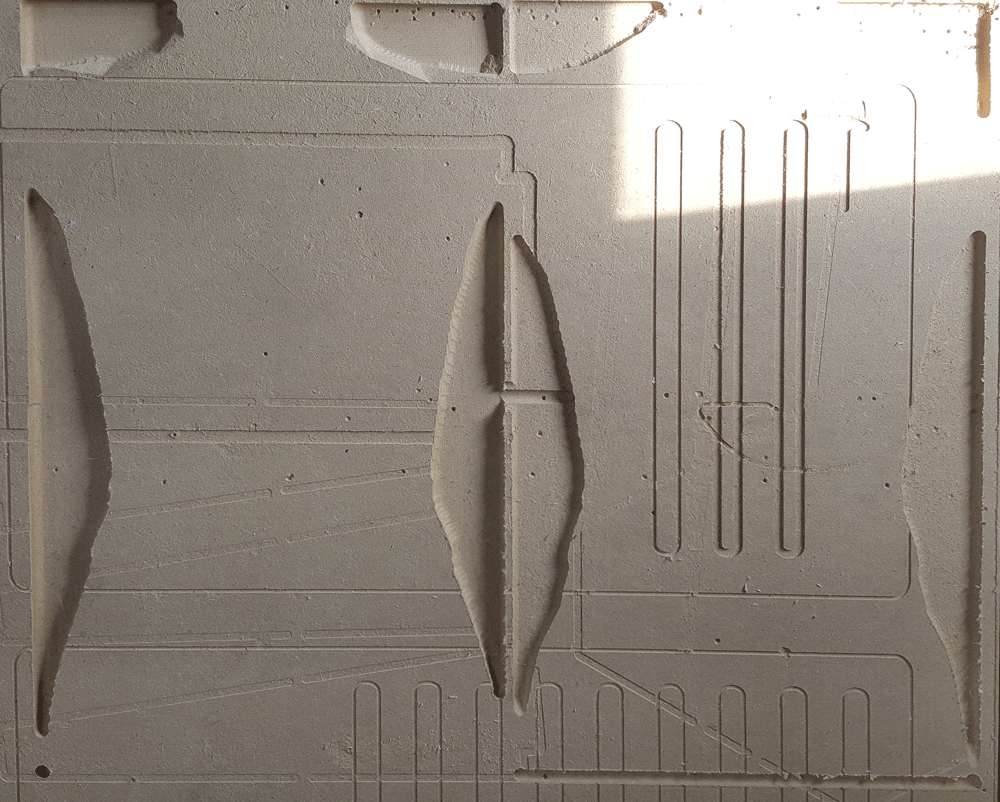
Straight from CNC
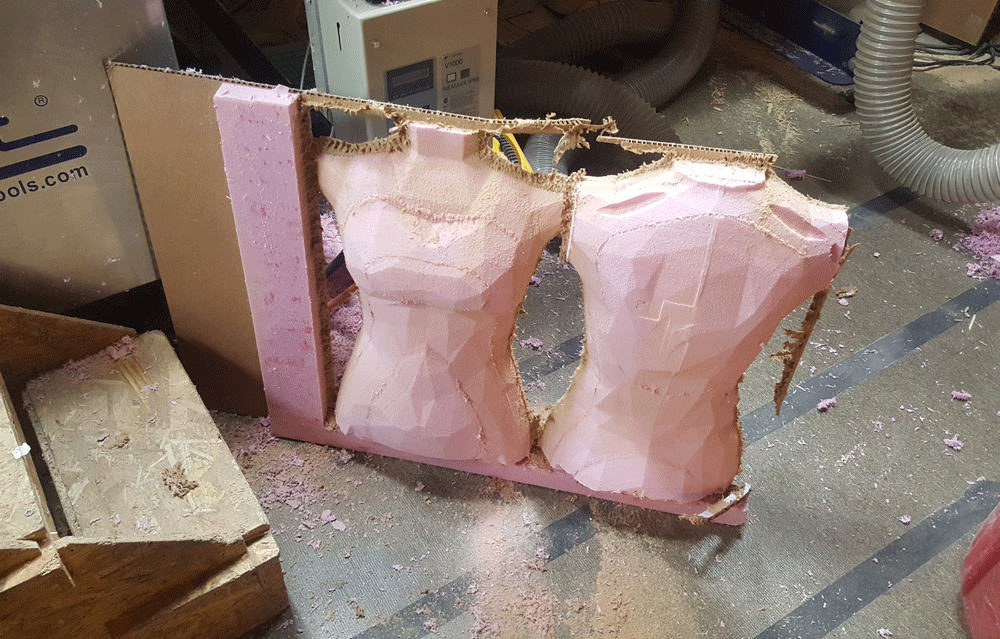
The fact that I've cut too much, the front and the back didn't match, so carve with old-fashion box cutter.
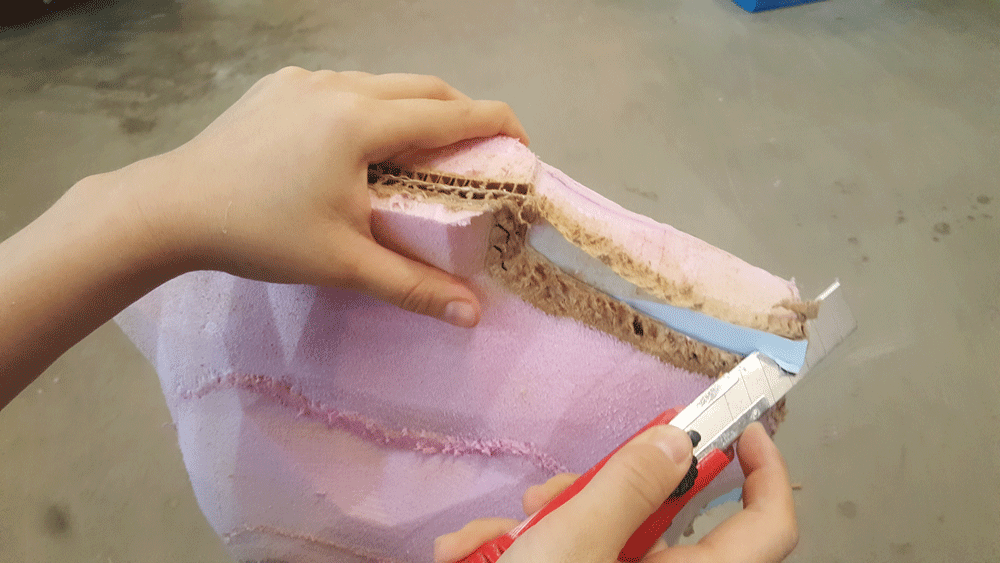
Composite
I've used drape technique from garment construction. First, I would lay down fabric on top of the mold and draw the outline with darts.
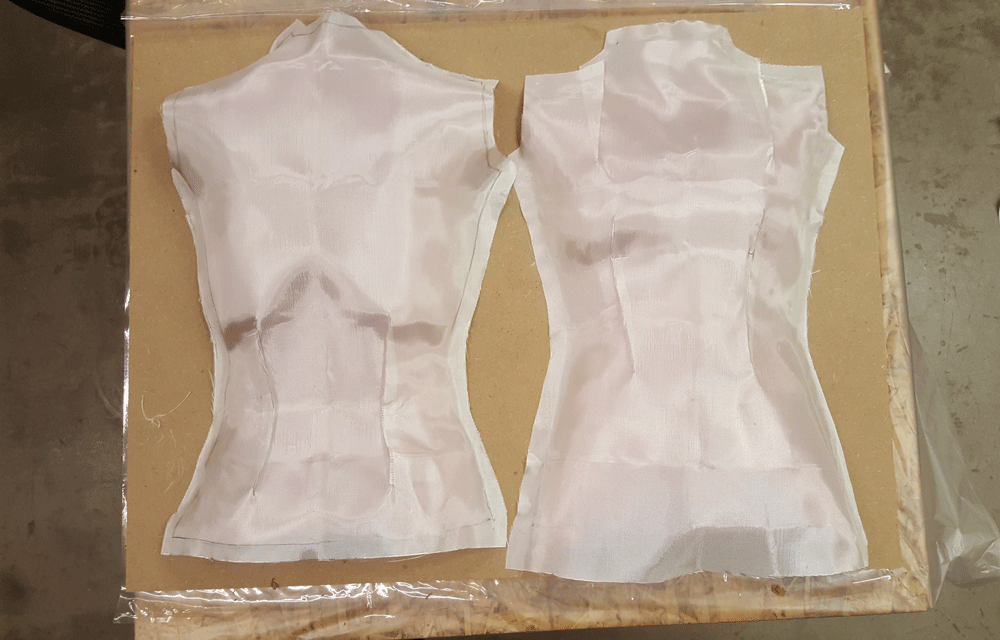
Second, drew lines with rulers and darts.
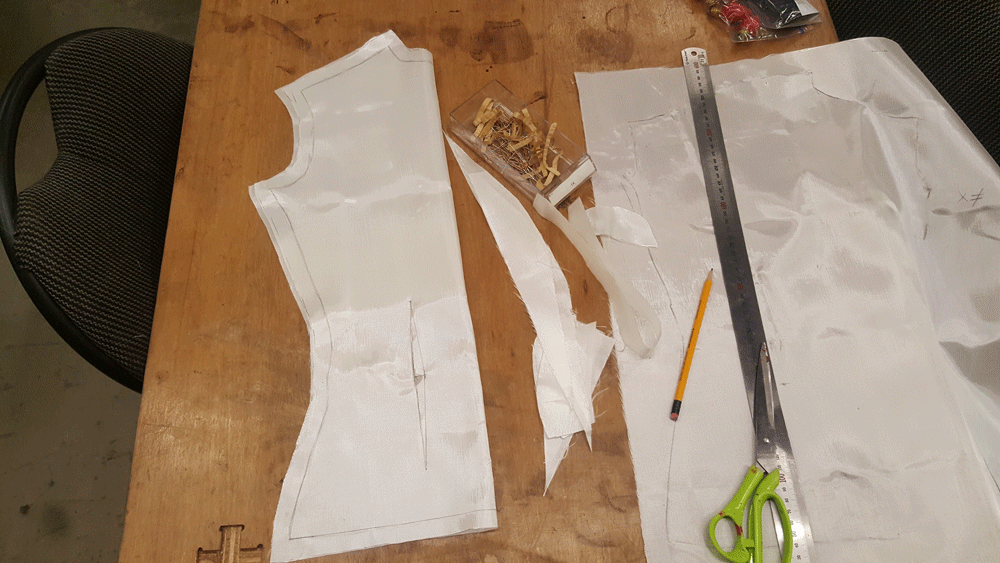
I couldn't find pins around the lab, so I used 10k resister.
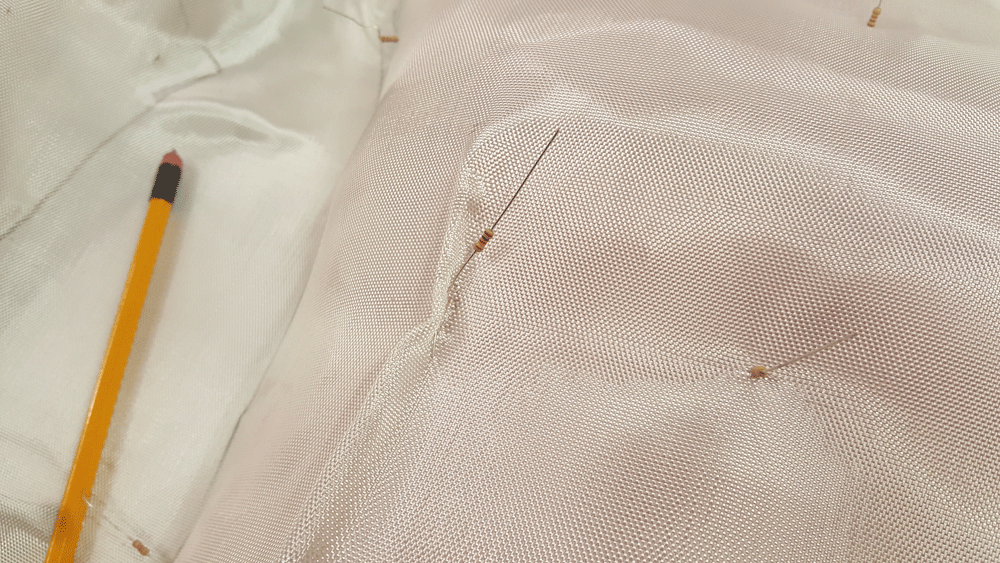
All set!
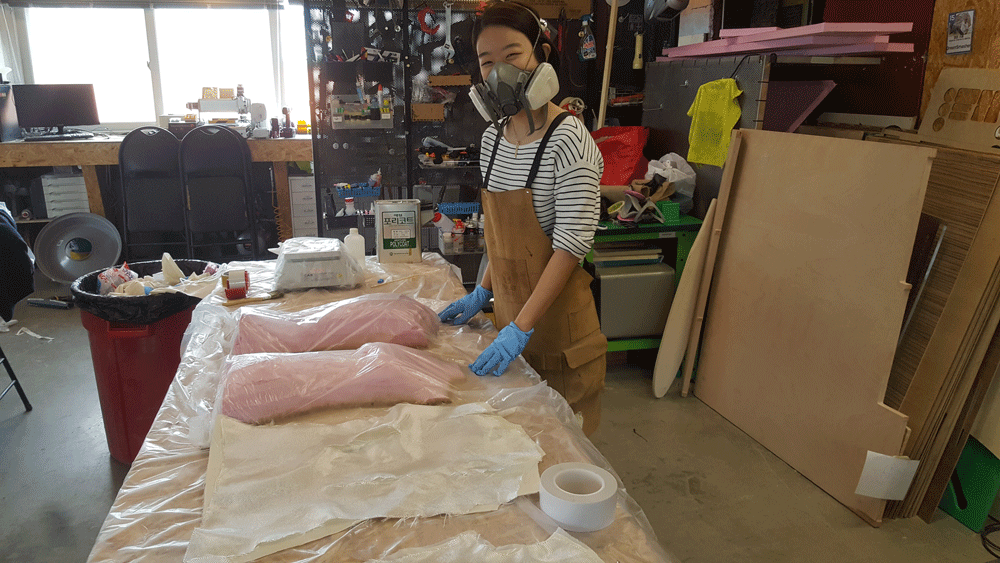
500 grams of polycoat and 15 grams of hardener. Polycoat MSDS PDF
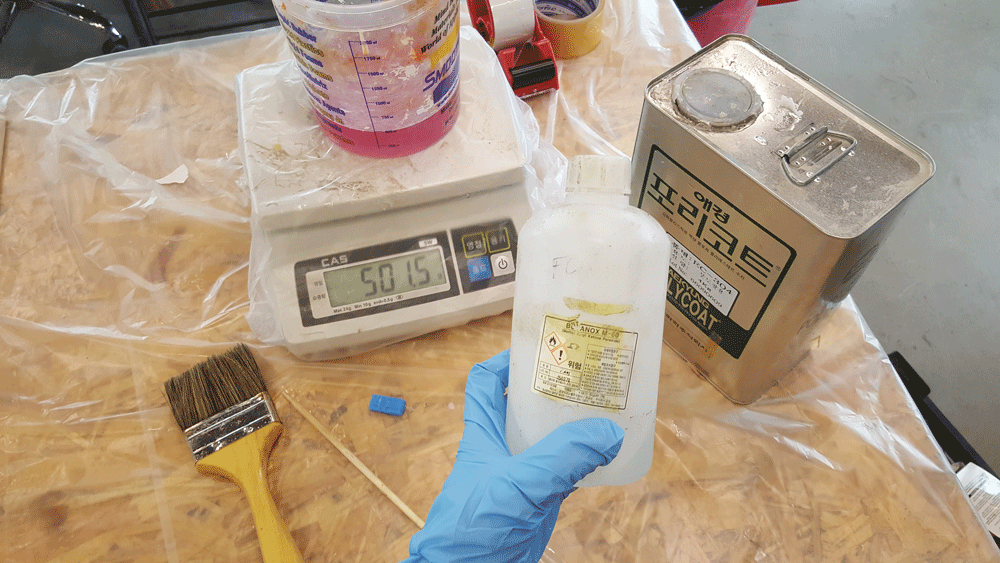
z
I had around 5~10 minutes to coat my mold.
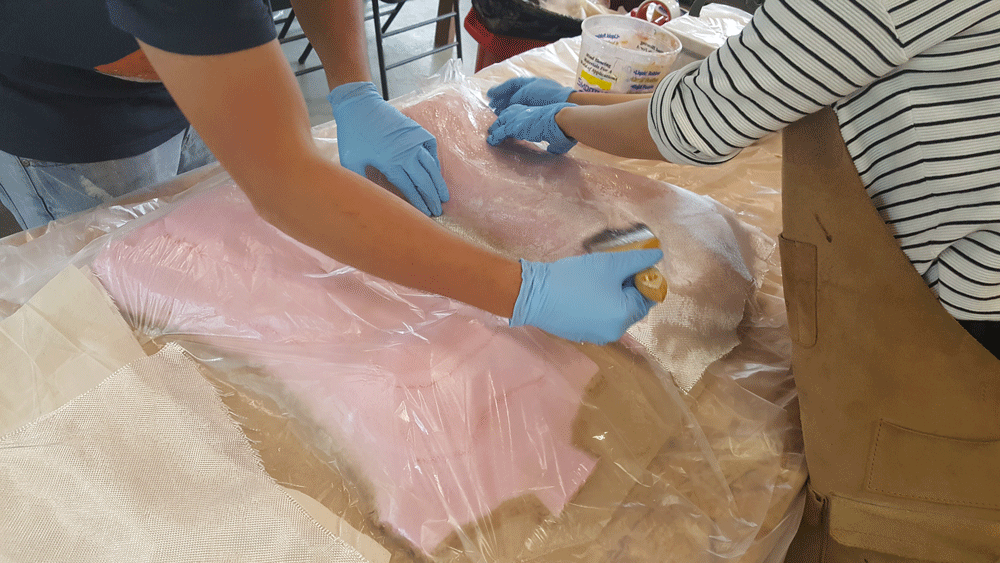
Here is diagram of what I did
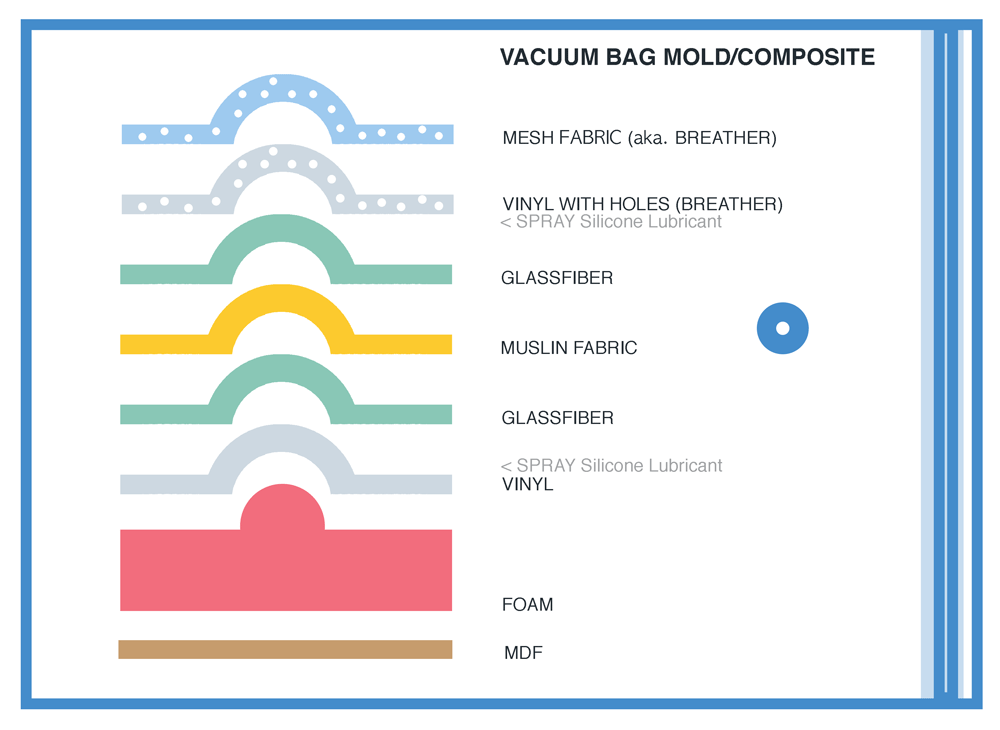
Double seal the vaccum bag with taping the open edge.
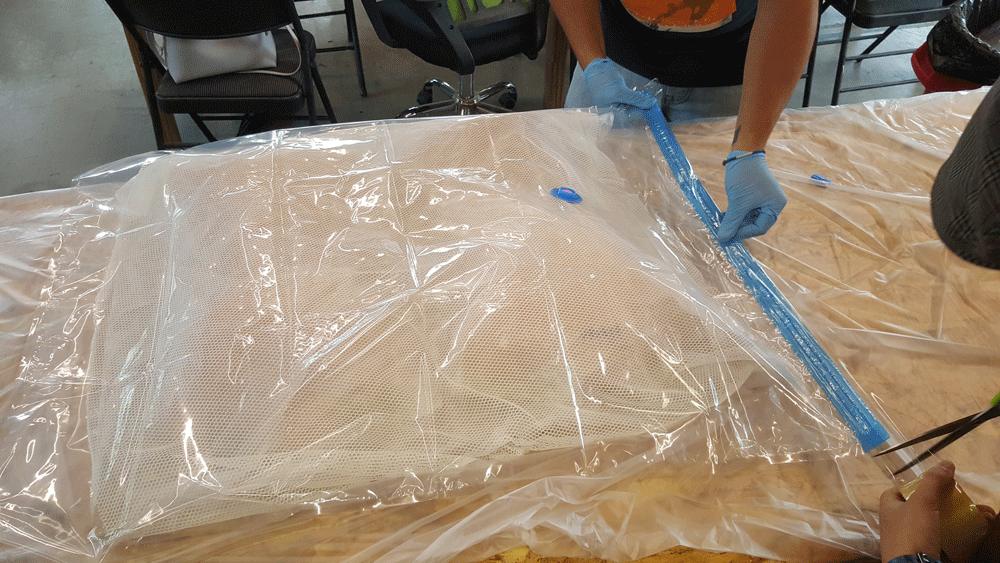
Left the mold by the window. It's the warmest place in the lab.
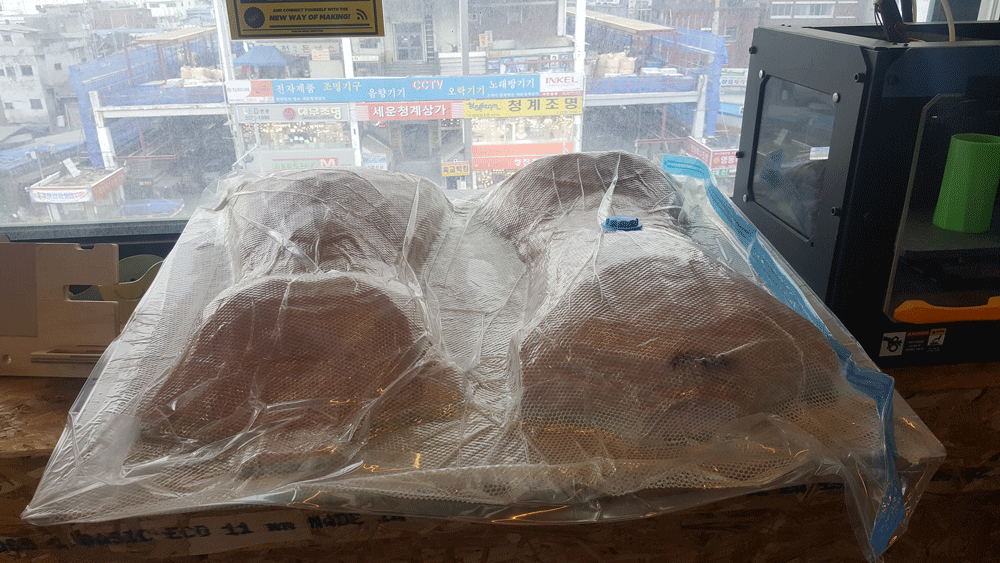
After the mold is completely dry. I've used box cutter and scissors to cut off the unnecessary parts.
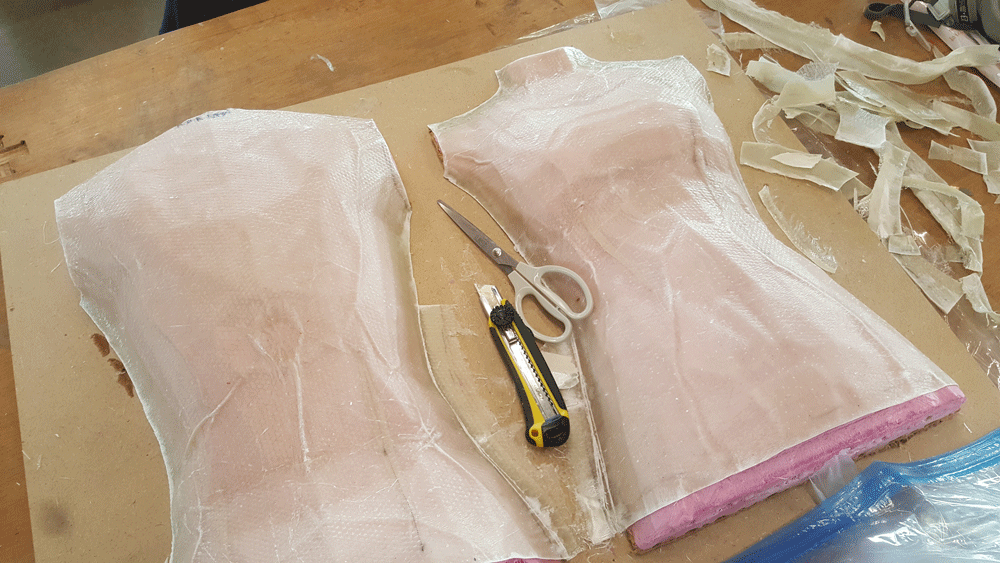
Composite Mannequin
Done!
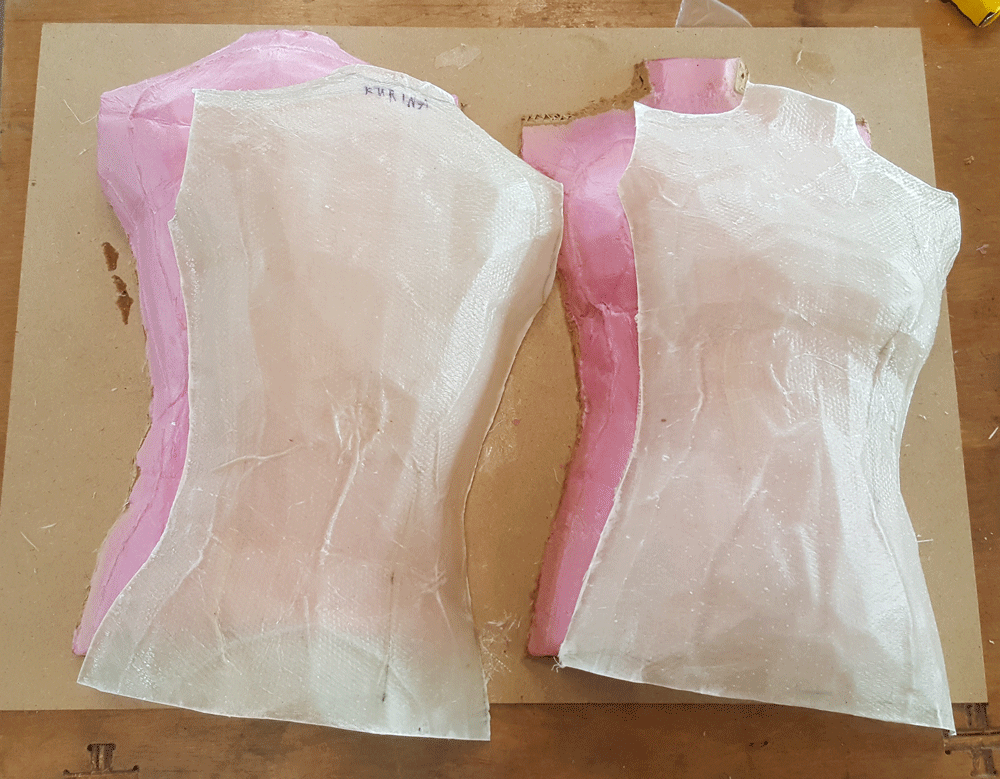
Overall, it was successful and fun process. Here is the STL file for CNC
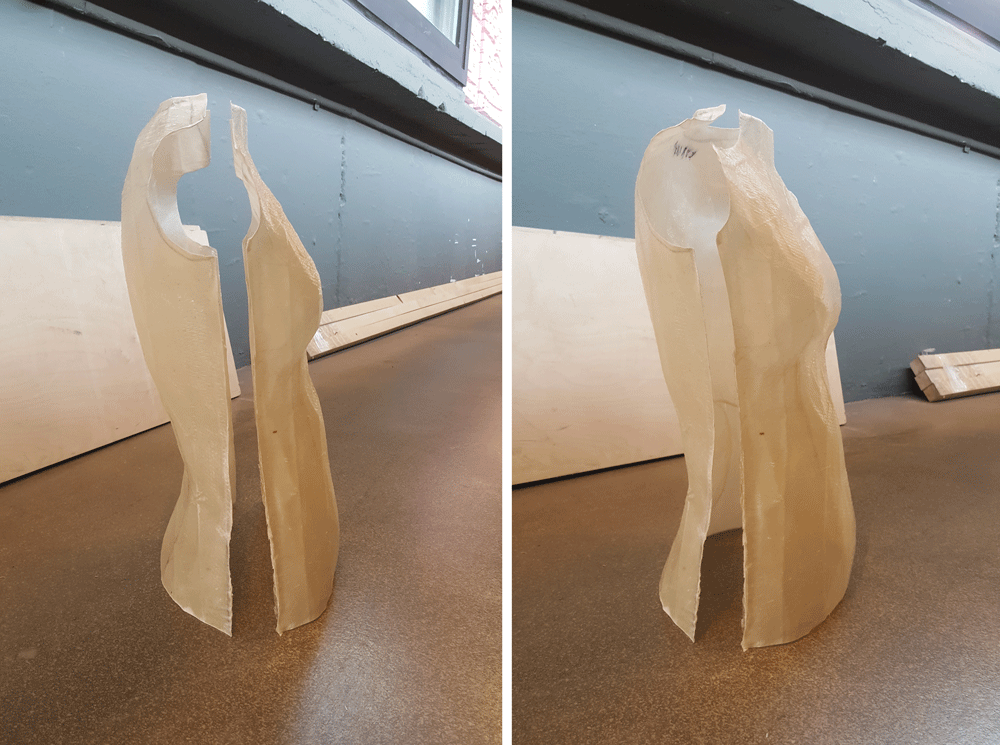
14th Meeting:
composite 3 May, 2017 10pm~1am(Seoul)
Homework
o - have you made a big 3d mould?
o - have you used fiber composite on it?
o - select and apply suitable materials and processes to create a composite part
o - does it look awesome?
o - Described your problems and how you fixed
o - Include your design files and photos