_Week05_3D SCANNING AND PRINTING
_Introduction
During this week we enjoy to work with tools for 3D scanning and printing, we start to scan in order to create a mesh that later we 3D print and also finally work with the 3D printers learning how to use it, testint design rules and differents materials that we can use to get our 3D model physical. I think that these kind of tools are nowdays so useful and powerful for prototyping, the way that we can get physical test of project in short time.
_Background
3D printing, also known as additive manufacturing (AM), refers to processes used to create a three-dimensional object in which layers of material are formed under computer control to create an object. Objects can be of almost any shape or geometry and are produced using digital model data from a 3D model or another electronic data source such as an Additive Manufacturing File (AMF) file.
A 3D scanner is a device that analyses a real-world object or environment to collect data on its shape and possibly its appearance (e.g. colour). The collected data can then be used to construct digital three-dimensional models.
_Week Assignments
Group assignment:
Individual assignment:
_Workflow /Step by Step
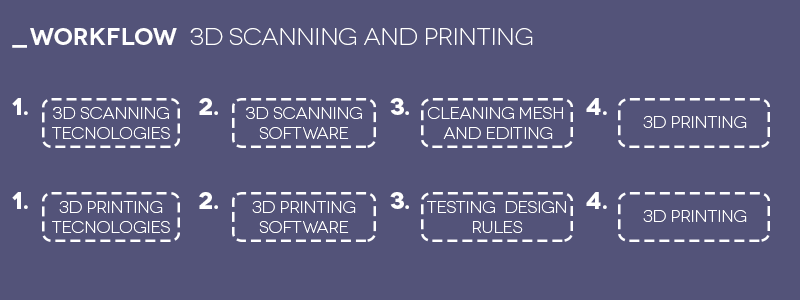
_Group assignment: Testing the design rules for your printer.
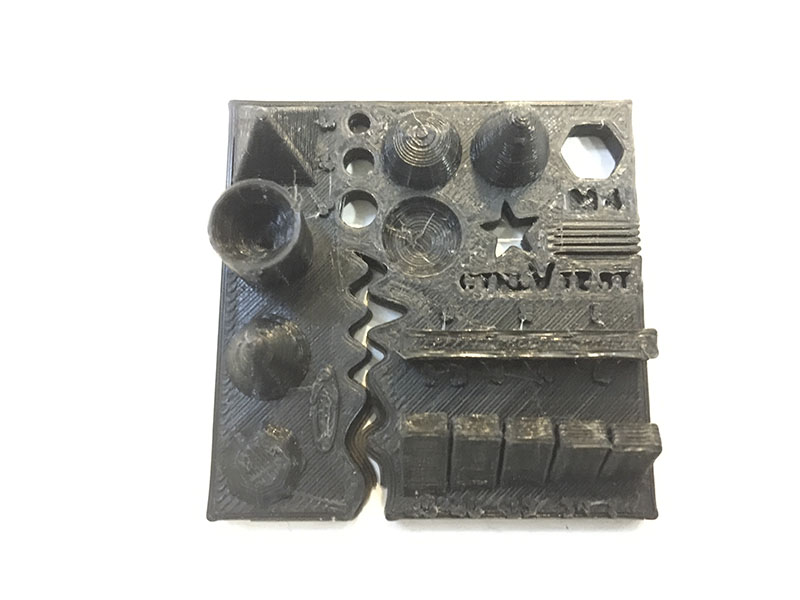
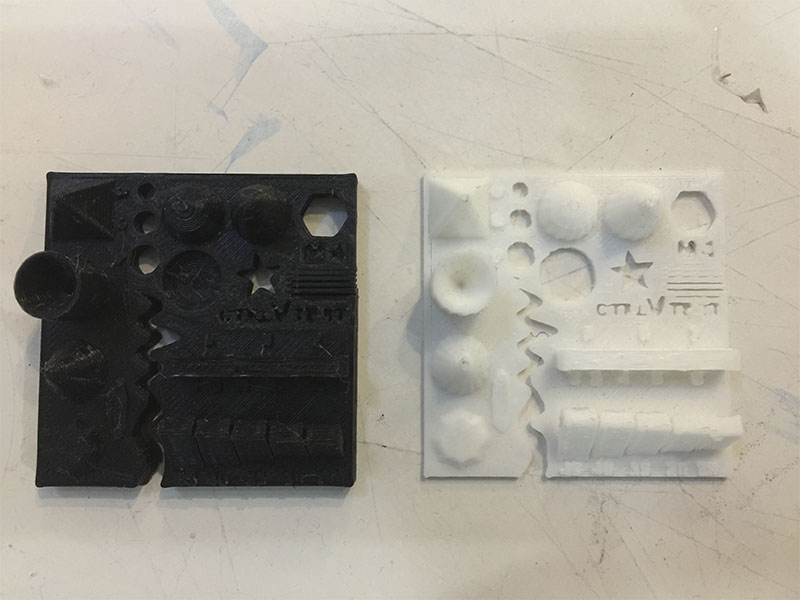
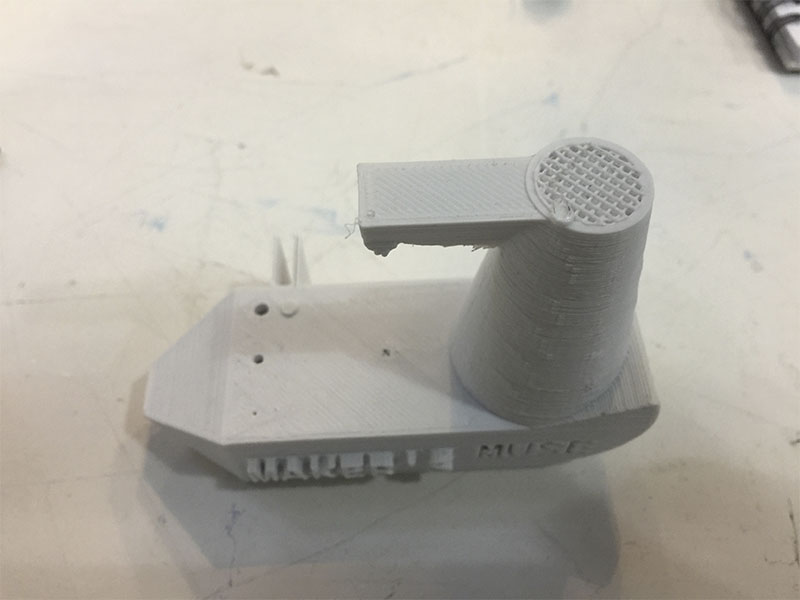
After doing the group assigment testing the rules of the 3D printers, I took 2 main decisions for my 3D print assigment: 1- No need supports because of the angle and the shape of the 3D print piece the extrusor could do the layers without problem correctly. 2- Because it was the first test of the 3Dform for seeing the dimensions in real scale and choose 20% of infill was enough for now because the ideal piece is going to be empty inside and I only have to keep 3mm of wall thickness (after in molding and casting making the two sides mold).
Check our group assignment here were we test the 3D printers of the fablab.
_Design and 3D print an object.
I try the models of the my final project that I already done in week 3, so I exported it as STL file from Rhinoceros in order to put it in the Cura software for printing in the PRUSA i3. This is one of the four pieces that I want to 3D print in order to check the dimensions, joints and the texture.
In this case, the advantages of the 3D printing as additive technique is useful because of making the texture of the module properly and for having the male/female joints to snap each module of my final project
Parameters used in this assignment:
In Cura we can set the parameters that we want and also give us a preview of the layers and which path will follow the noozle.
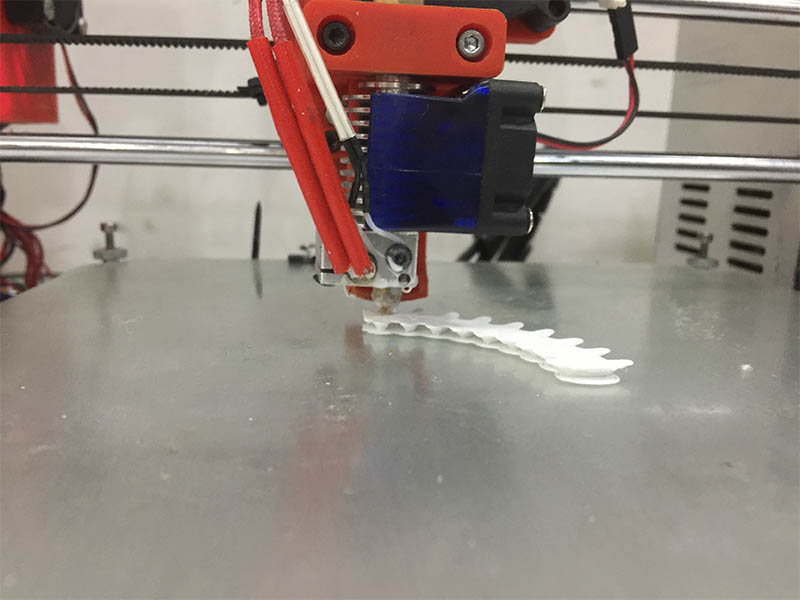
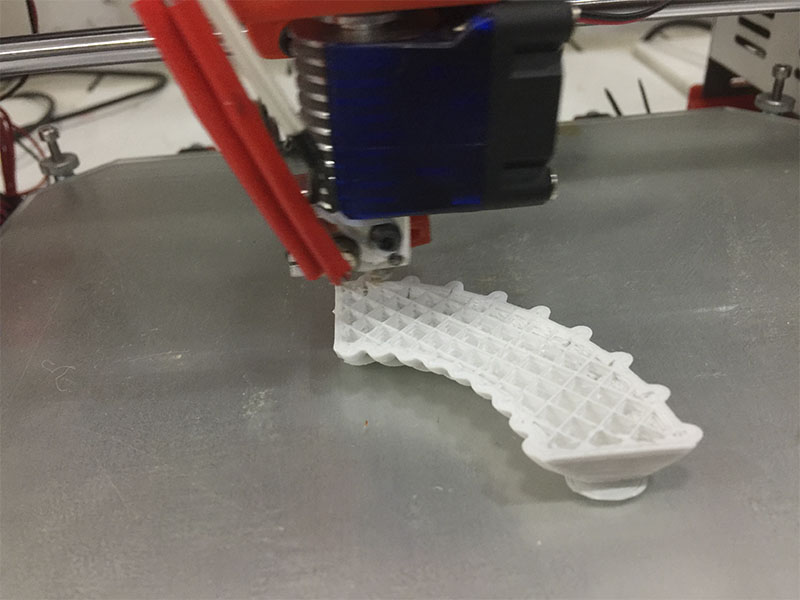
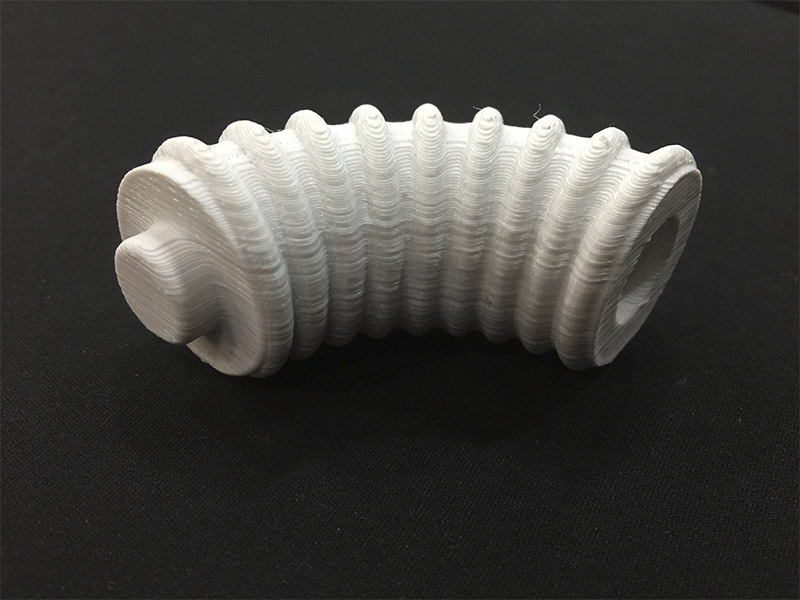
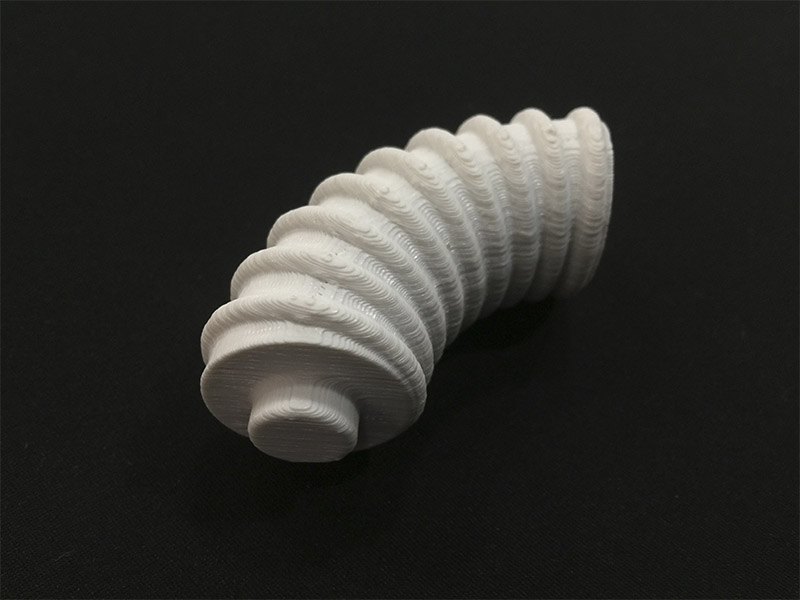
NOTE: It's important to check the correct scale at the moment of export the model.
_3D scan an object (and optionally print it).
_3D scanning.
We started creating a 3D model from an image in Rhinoceros, you can import the image and use the command HEIGHTFIELD in order to create the 3D model and giving the size that you want and the complexity of the mesh (I put 100x100).
_Commands used:
Heightfield >> put size >> put complexity of the mesh
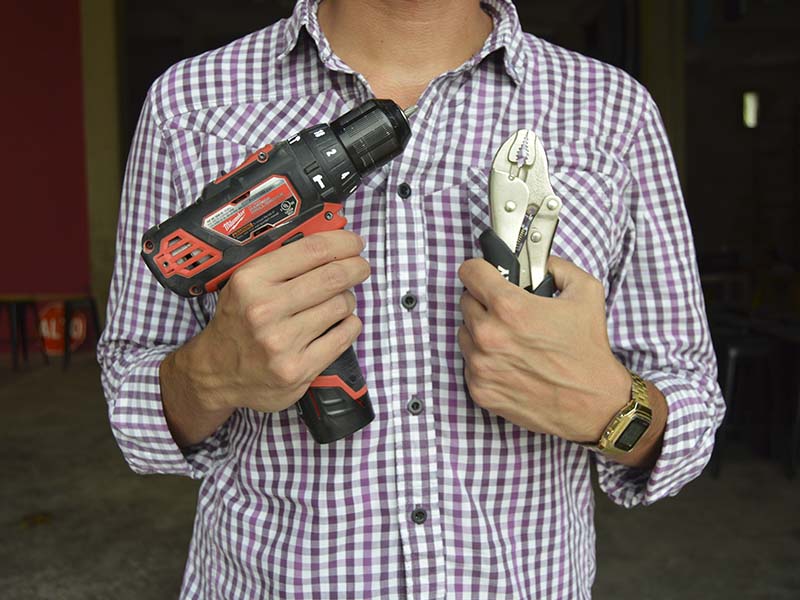
Later we 3D scanned with the Modela MDX-20 which can integrate a tool that helps create the mesh passing through the object in the bed but depends of the factor of quality we put its gonna bed better define the mesh; you can also export it as STL or DXF file.
Then I worked with the Xbox Kinect for scanning myself, it have 3 cameras that combine the information in order to create a mesh of the object in the software Skanect that connect with the Kinect to create, clean and export the mesh as STL file.
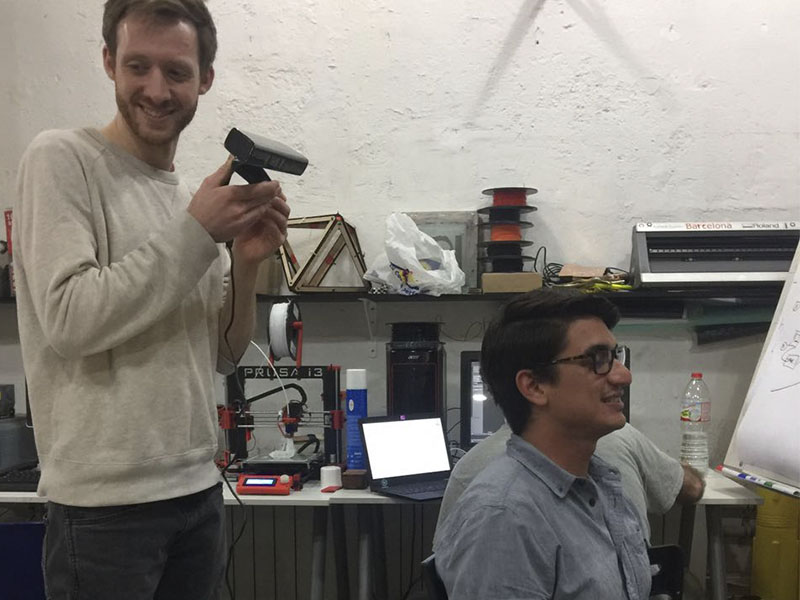
To make the mesh ready to 3D print we have to work with the 3D tools; I tried differents software seeing tutorials for how to fill holes, remove 3D parts lost in the space and double vertex and faces; you can do this direct in the Skanect software but always it's better to enhance the mesh in other 3D tool because in the free version of Skanect you can only export 5000 polygons.
_Cleaning the mesh.
_Meshlab
Meshlab its an open source system for processing and editing 3D triangular meshes,I get some information from a past FabAcademy student page. I imported de model as STL and then follow the next steps for removing isoleted parts and cleaning (menu/filters/cleaning and repairing/remove isolated pieces); but did not founded the Fill command and have some trouble with the amount of faces and crashes down the programm so i prefer to switch first to Blender make some changes.
_Commands used:
Menu >> Filters >> Remeshing, simplification and Reconstruction >> Quadric Edge Collapse Decimation (for reduction of faces).
Menu >> Filters >> Cleaning and repairing>>Remove isolated pieces (remove floating useless parts).
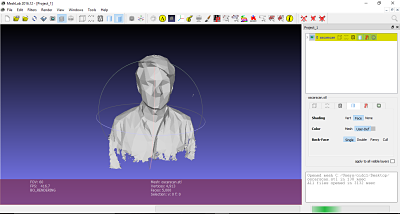
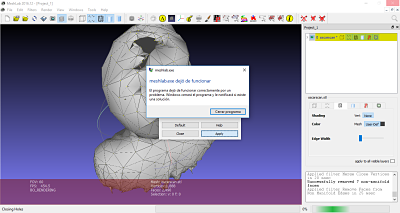
_Blender
Blender is the free and open source 3D creation suite, I used this software to enhance the quality of the mesh. Then I exported the mesh as STL to Meshmixer.
_Commands used:
Object Mode / Object Modifiers >> Subdivision Surface Modifier >> View amount 3 Render amount 2 (used to split the faces of a mesh into smaller faces giving a smooth appearance).
Object Mode / Object Modifiers >> Shrinkwrap Modifier (allows an object to “shrink” to the surface of another object).
Sculpt Mode / Crease F brush (used to alter the shape of a model).
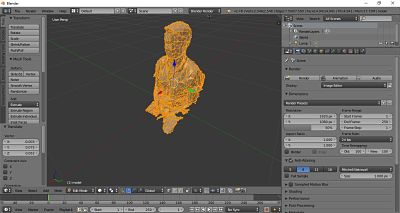
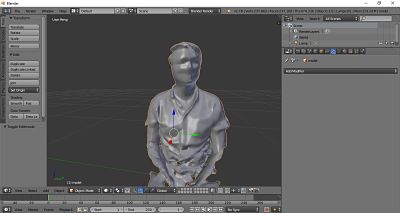
_Autodesk MeshMixer
Meshmixer is state-of-the-art software for working with triangle meshes. I saw this Clean up meshes tutorial that helped me to clean very easy the mesh, going through 2 options to do it.
Option 1 is to fill the holes manually one by one checking the amount of each fill.
_Commands used:
Press F button and select the contour of the hole to fill >> Press S button and then ENTER to confirm the fill. (used to fill holes manual).
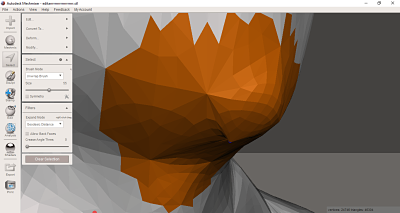
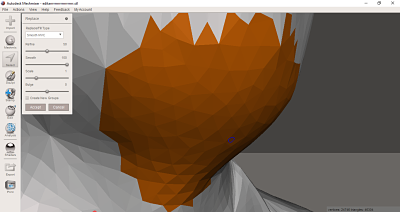
Option 2 is using tools that automatically solve the problem and cut the model.
_Commands used:
Edit Menu >> Make Solid (used to automatically fill all the holes detected).
Edit Menu >> Plane cut (used to cut the mesh to create a plane for easy 3D print).
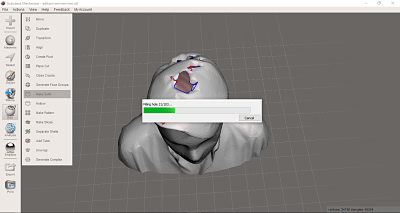
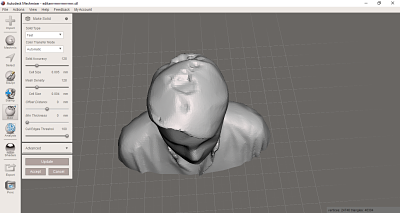
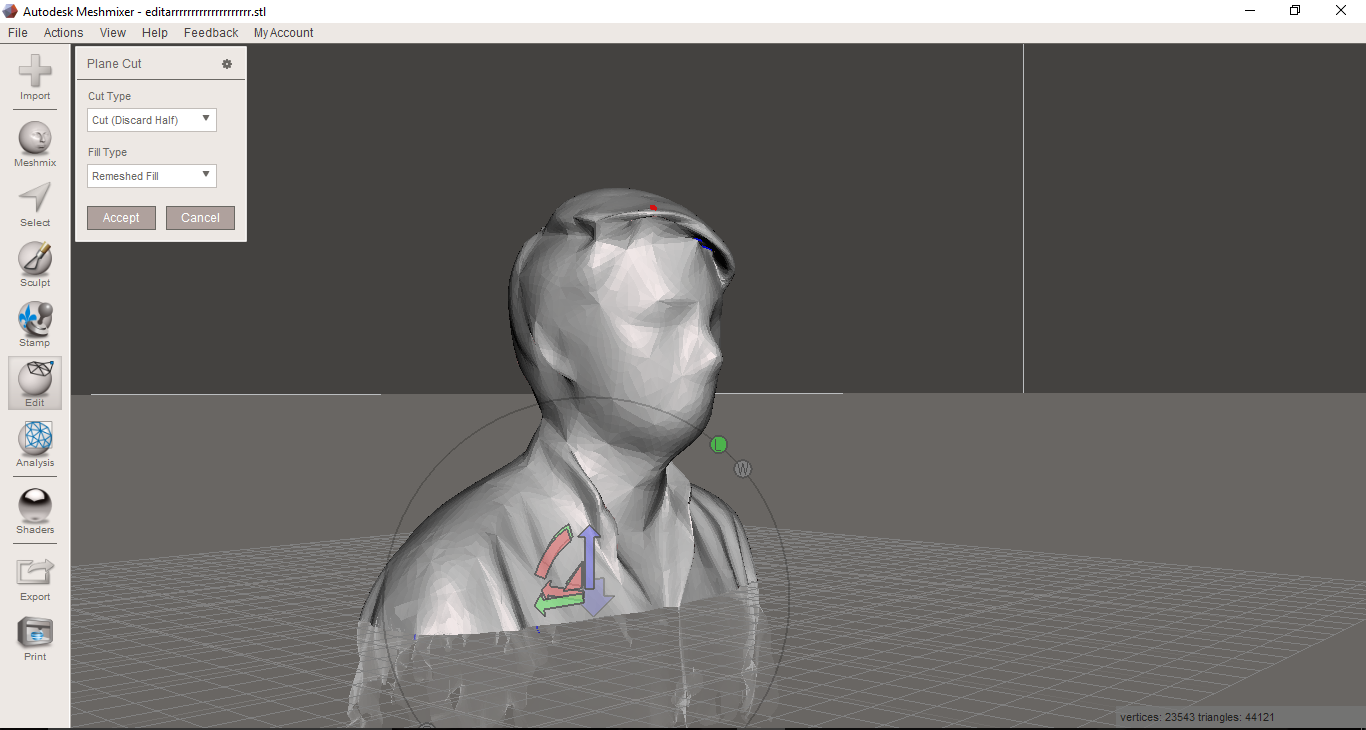
_3D printing.
So in order to 3D print the 3D scan, I exported as STL from Meshmixer to imported in Cura software to create the gcode for the 3D printer. In the Cura software I used the following parameters:
- 10% Infill density
- 60 mm/s Print speed
- Without supports
- Without supports
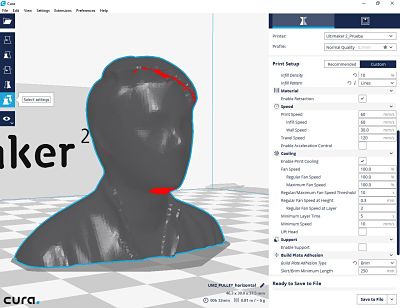
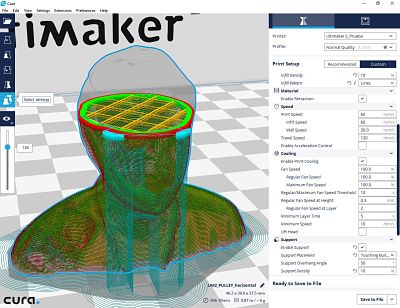
NOTE: For upload this final photo of the print the Brackets flip 180° automatically I dont know why, so i found this forum that say the image was taken upside down so some software dont flip it (like the photos in Iphone or photos in the computer). Finally I've take a screenshot and put the image correct to solve the problem.
_FILES
All the files for this assignment are available to download here