assignment 7
computer-controlled machining
7th week
In this week we were aimed to build something BIG.
Because I have a very big Maine Coon cat, I decided to build a big chair/bed/thing for him.
Designing the piece
I chose to use my dear openScad for modelling the 3D model for simulating the piece.
It´s an Internet knowledge, cats loves circles. A circle in 3d? Lets build a sphere. If I want space for him inside it, It needs to be void.
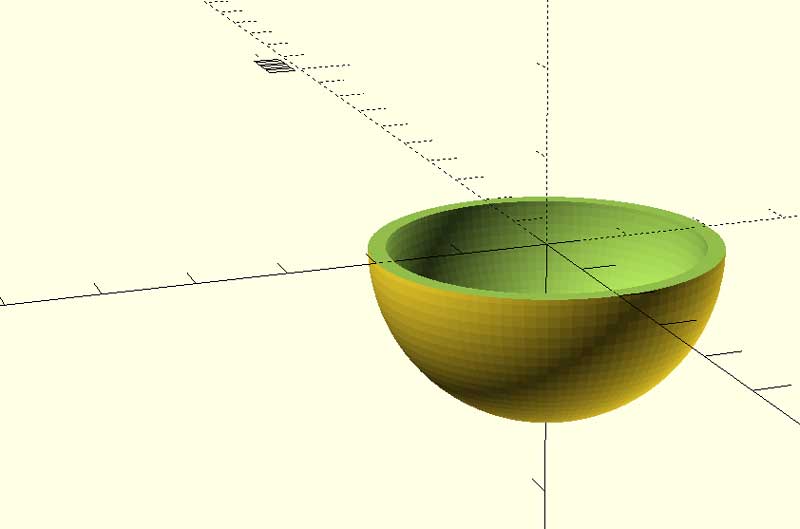
I added some "design cool" features, a flat bottom and cut the sphere with a 40 degrees cut instead the classical and boring semisphere.
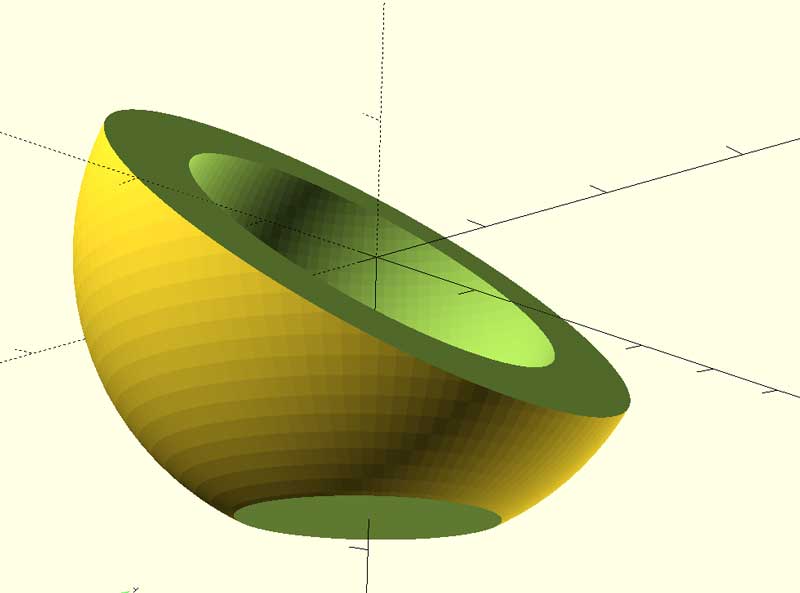
That flat corners wasn´t pretty, lets add bevel to that surface with a big torus of the same size:
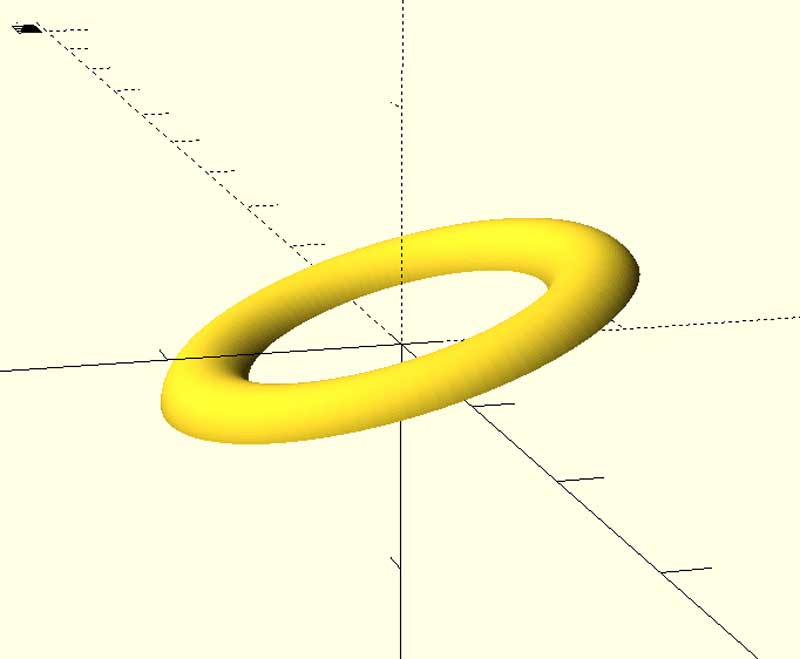
Magic¡ It´s a cool couch!
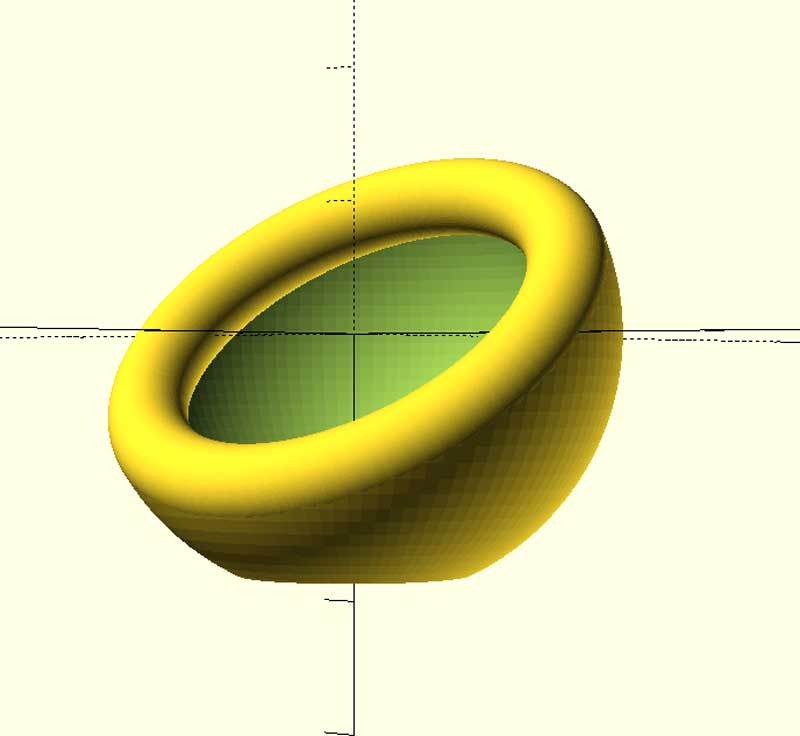
Slicing
Since the laser-cutting asingment, I was thinking about make something with stacked slices. I like how they look.
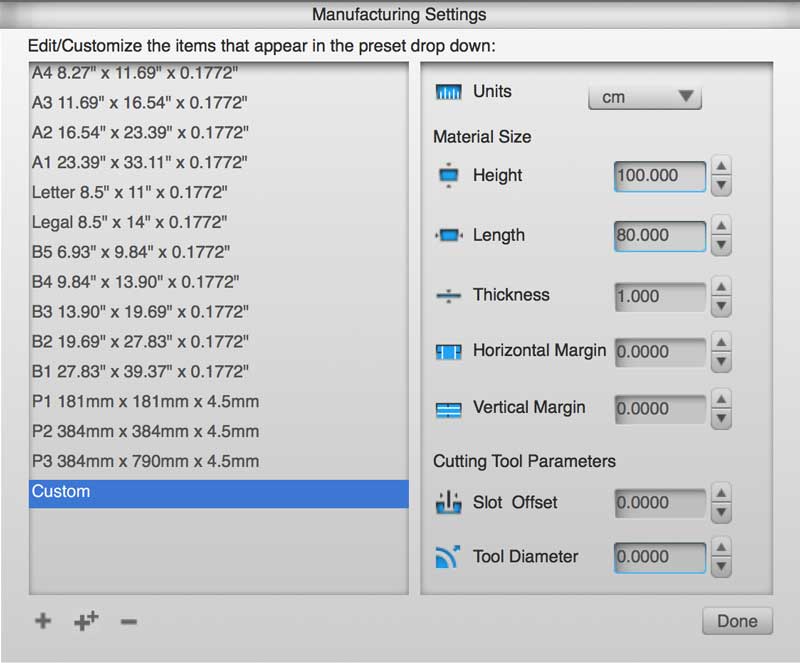
With 123D Make is super easy to slice an imported 3D Model. And even add the specs of the material, for calculating how many I will need.
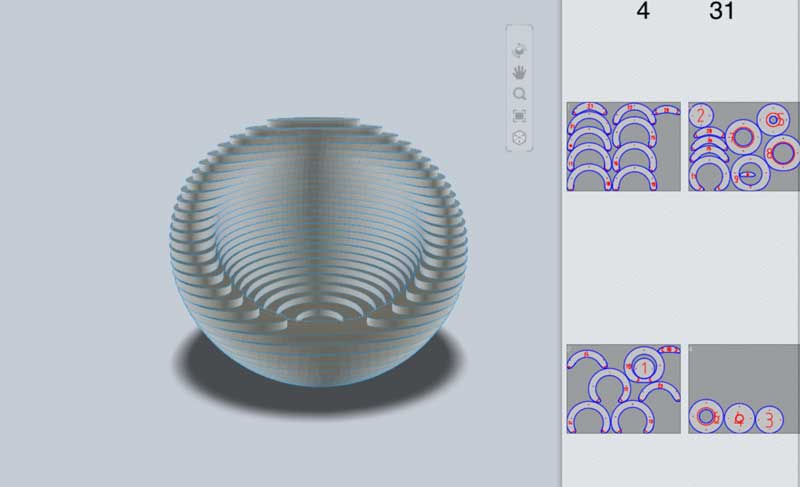
The nesting is not the best. 4 Sheets of material?. I dare you, I only have 3 pieces. The software exports an .eps file by sheet. With numbering too, its nice and quick.
I re-designed the nesting by hand in Illustrator.
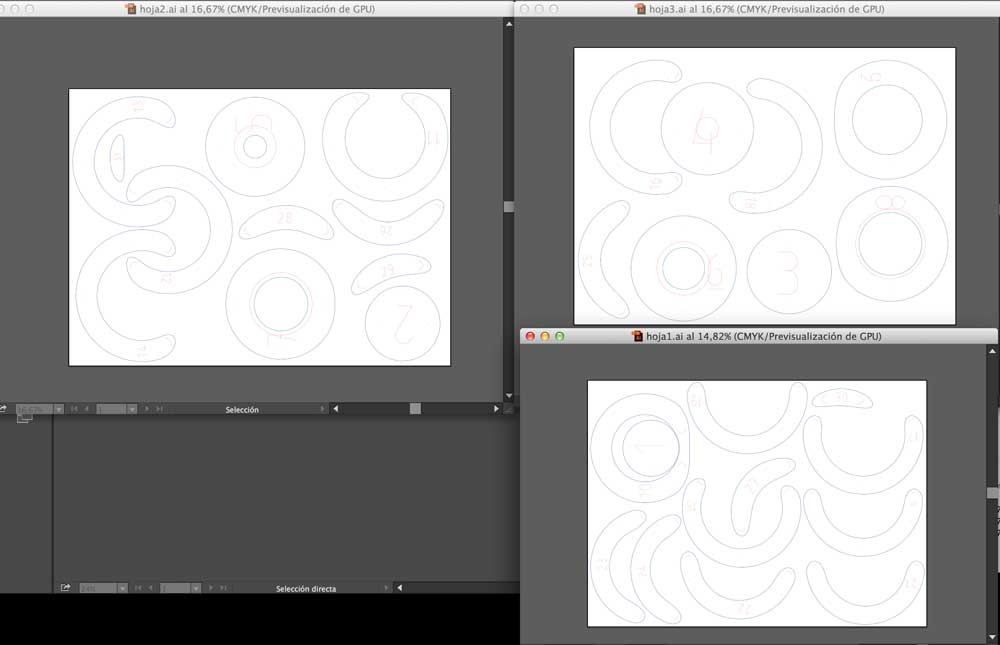
I won the battle, and nested the 31 pieces in 3 sheets of material. :)
Cutting
In our lab, we have the Mini TEC-CAM Milling machine.
We used a 5.7mm milling head for cutting.
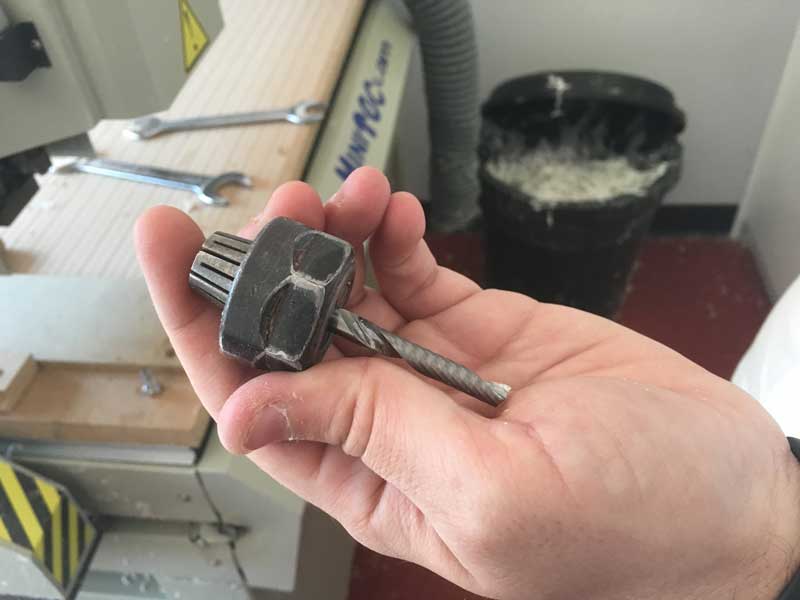
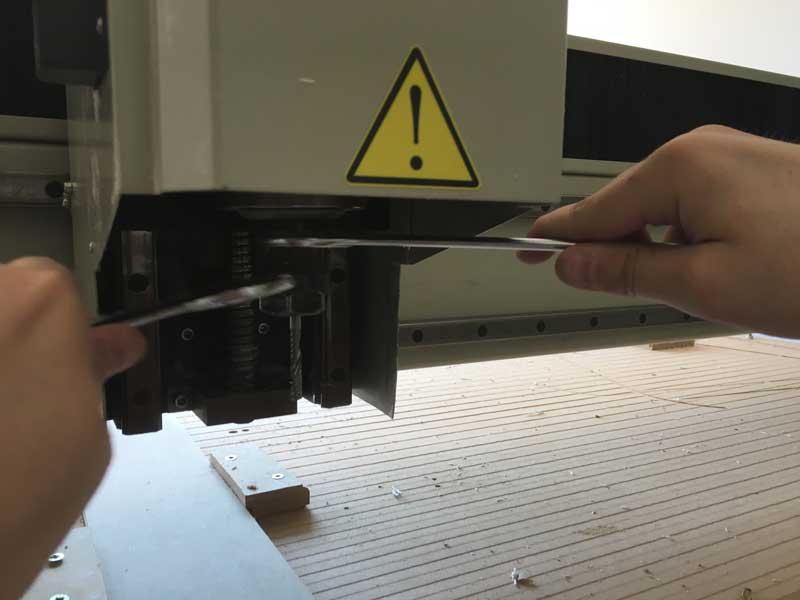
Measuring the Z axis with the sensor:
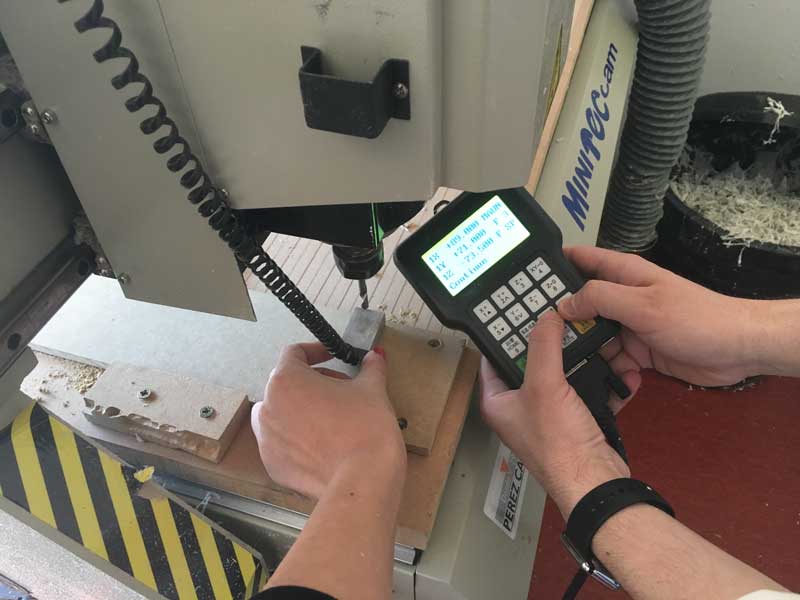
We lived the spectacular moment: the vacuum system bag belt jumped out and filled the room with sawdust.
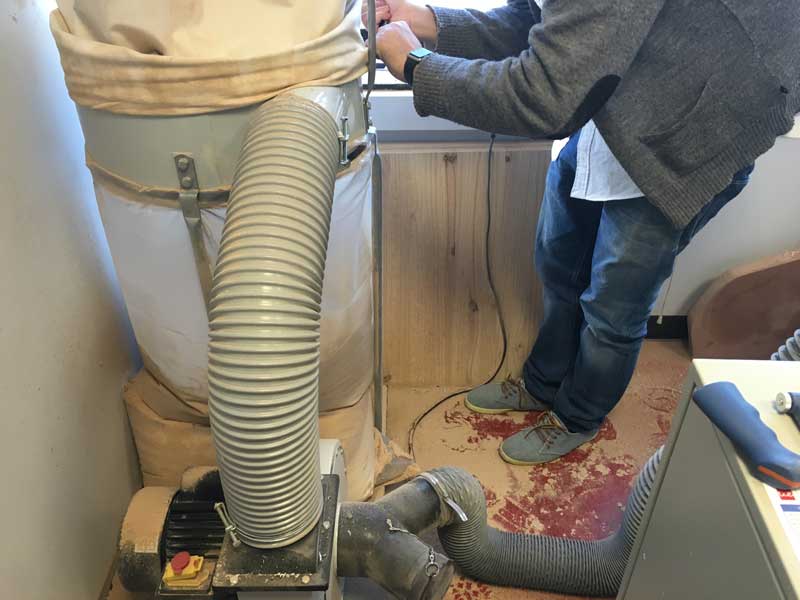
The machine works with RhinoCam. I imported a *.dxf file from my Illustrator nesting, positioned It on the based layer, with the proper measures and changed the properties for the cutting routine (amount of cutting, milling head sizes and types....) Jose helped me, I´m a little clumsy with Rhinoceros.
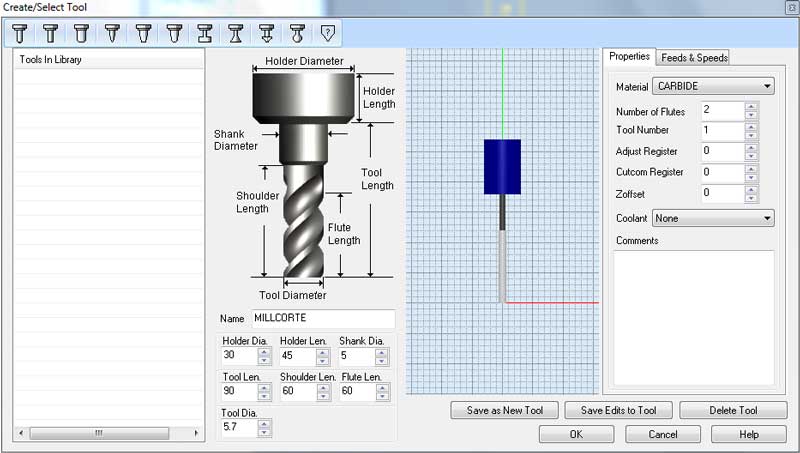
The milling head only gets up 10 from the layer when it moves.
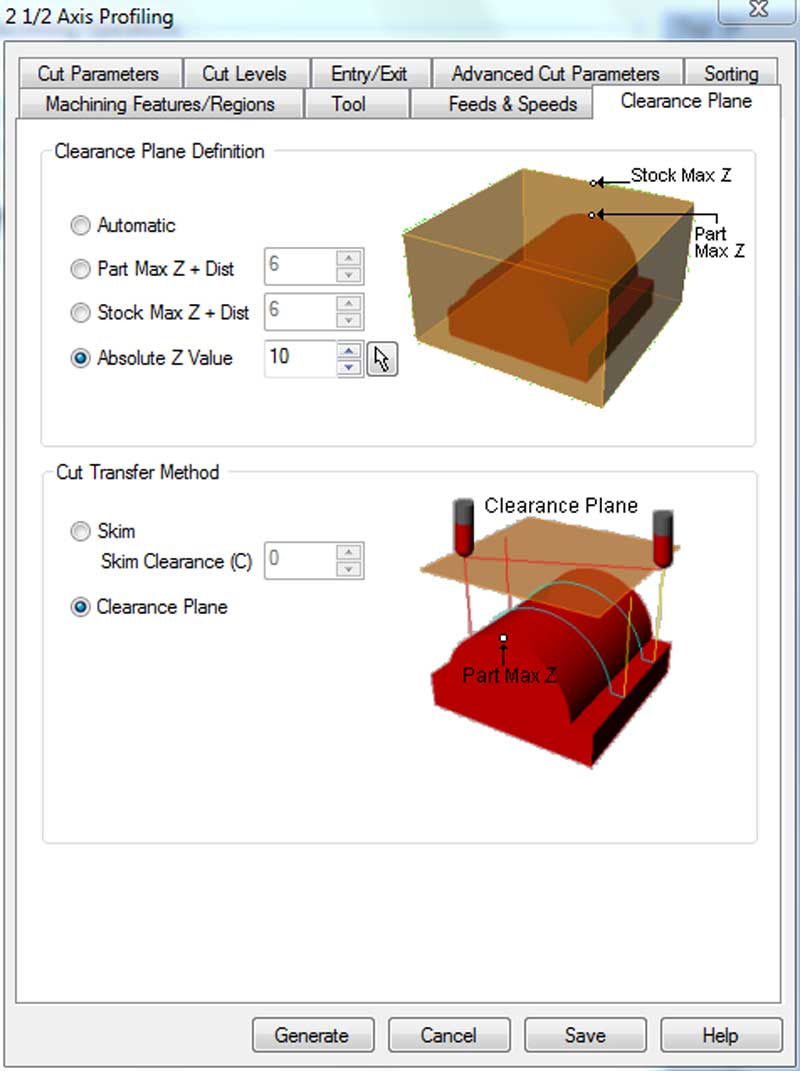
We wanted it to cut outside of the curves:
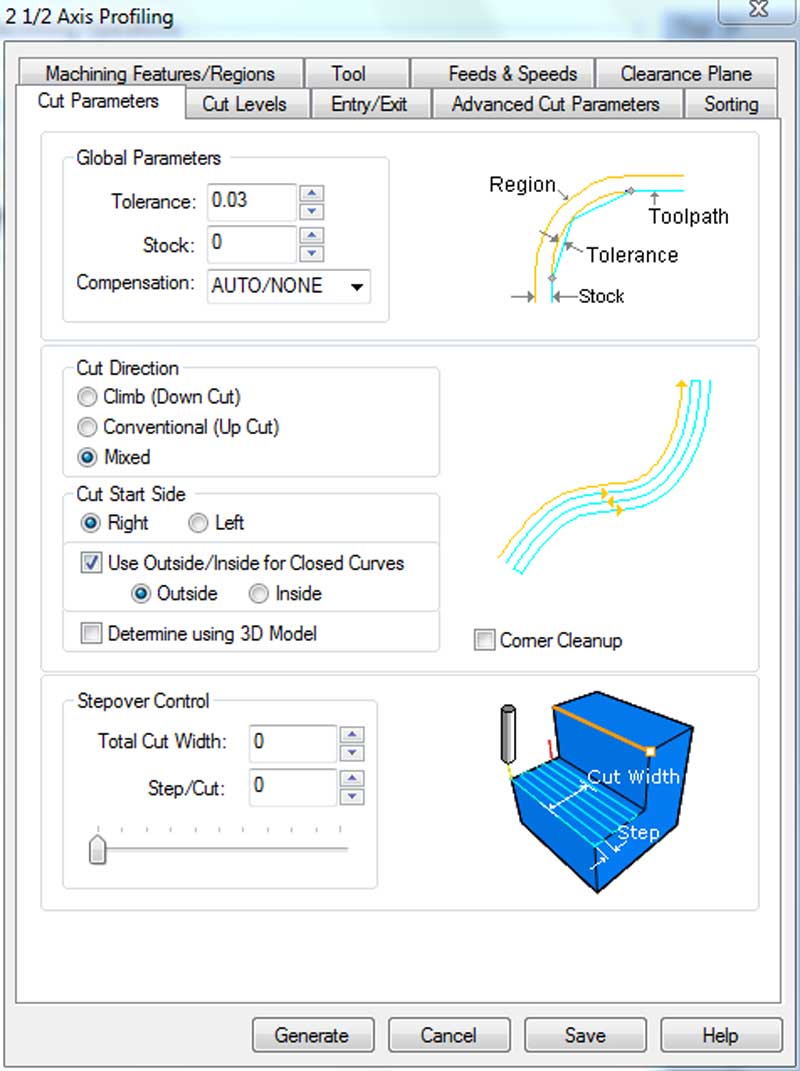
Very important tab, amount fo cuttind depth and in how many times will cut the machine. In this example, it cutted 10.5 mm in 6mm shots.
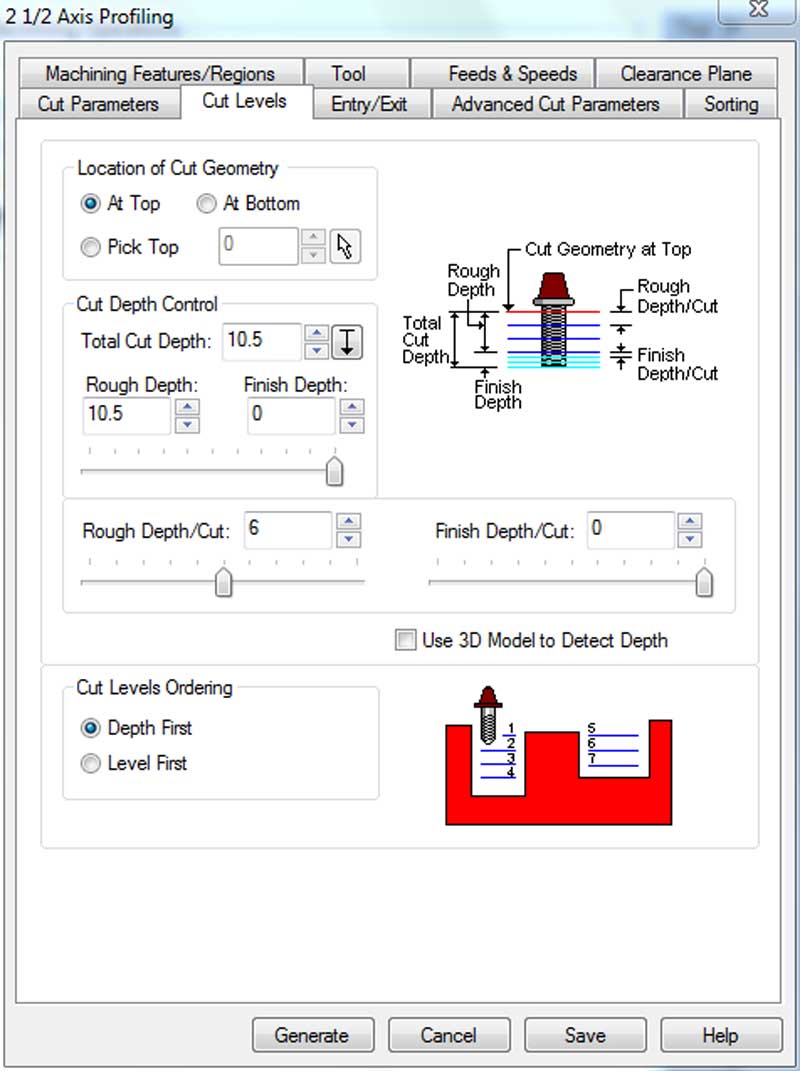

And generates the proper routine for cutting, ready to load into the usb port of the cutting remote control:
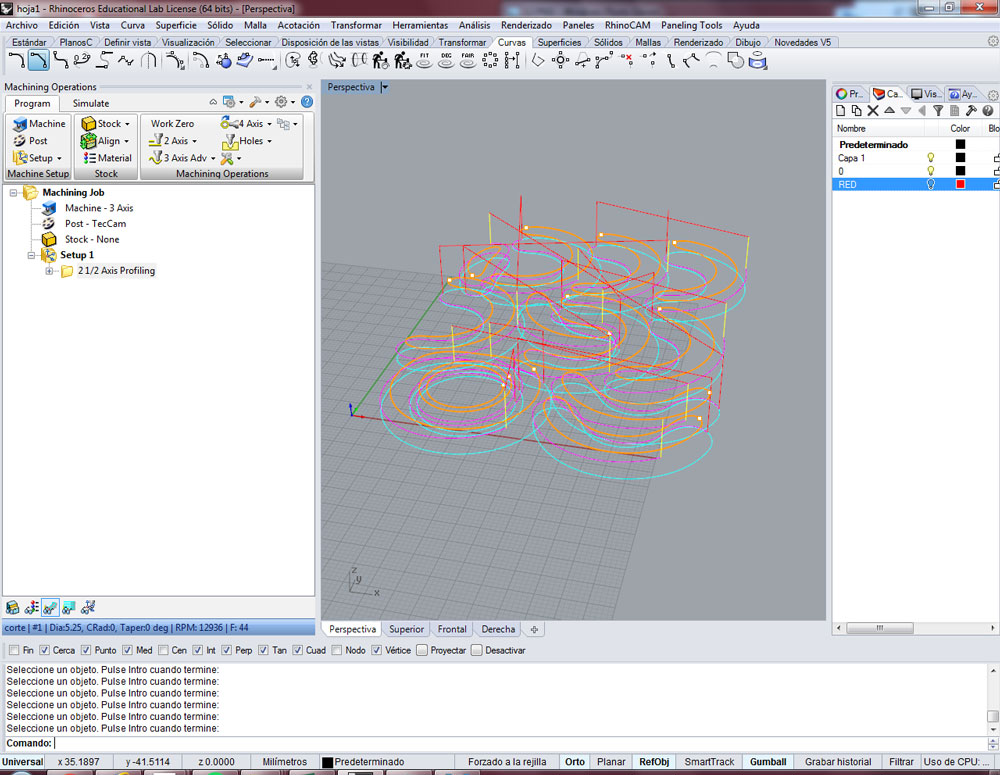
Because the material was 10mm plywood, the speed and settings were:
We noticed that when we were cutting test pieces, that when a piece is all cutted; it starts spinning and partially ruins the cut.
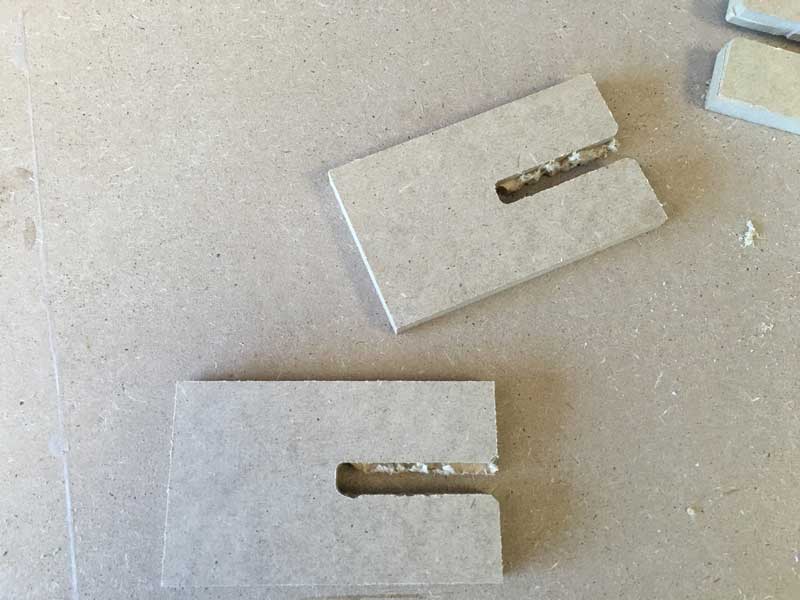
So, insted of cutting in one shot, I cutted first 0.5mm (the sheet is 1 cm height), and then fix the pieces with screws to the base layer. The final piece is going to be glued, so I didn´t care about the holes. I dont want to put my hand to hold the pieces with the machine plugged on.
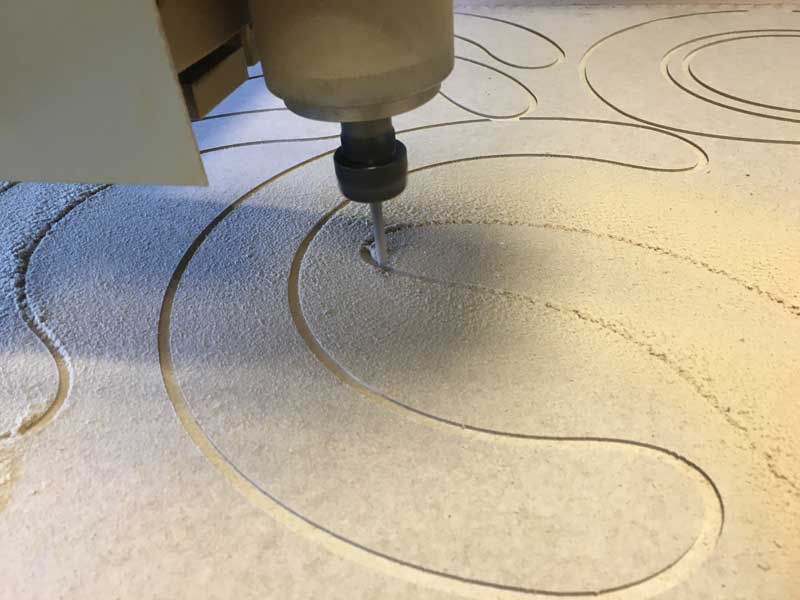
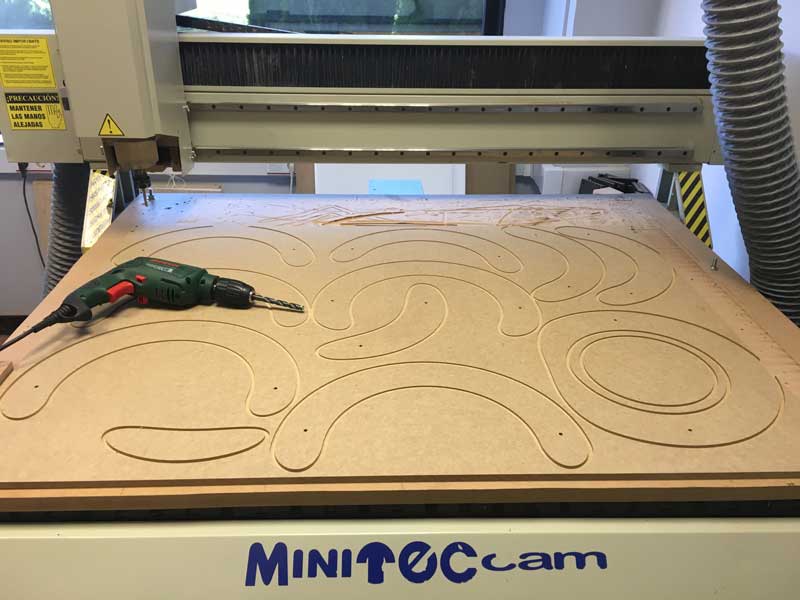
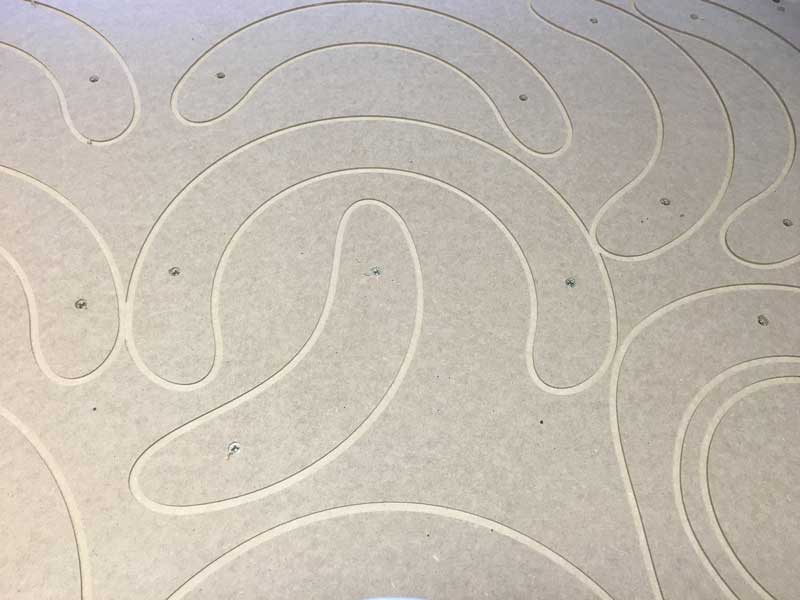
They are super-fixed now, and then I can cut them.
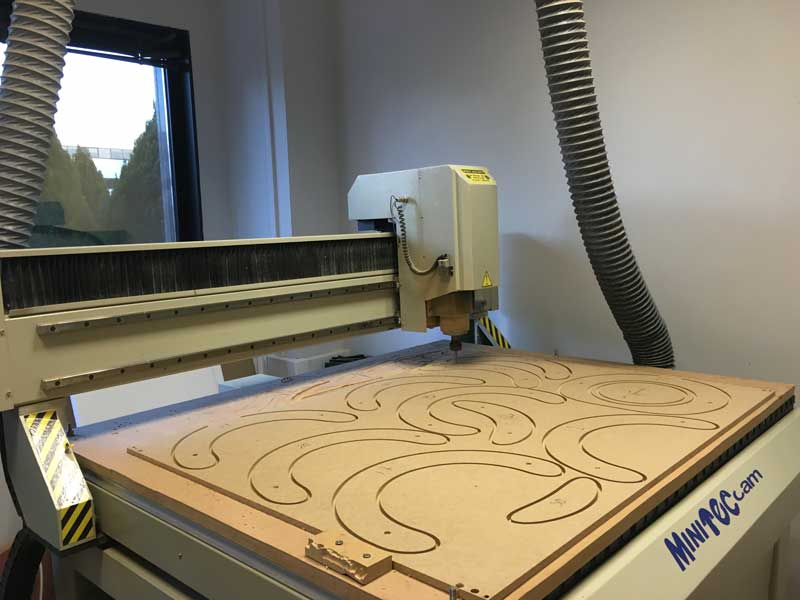
Even having the pieces screwed to the sacrificial layer, the wood was a little bended and in some areas It doesn´t cut until the end, but only for 1mm or 2.
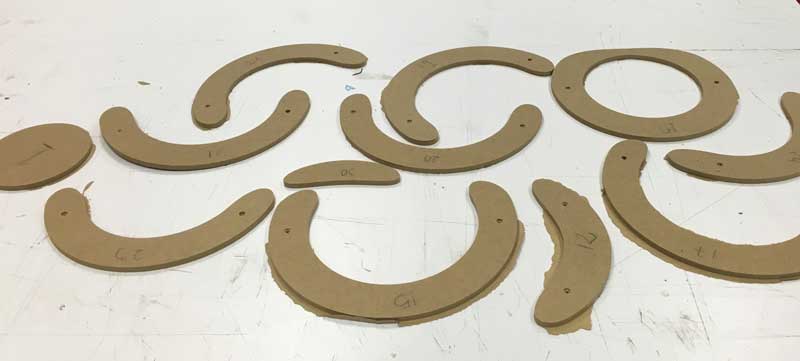
This extra of material is easy to remove by hand, is like a sheet of paper.
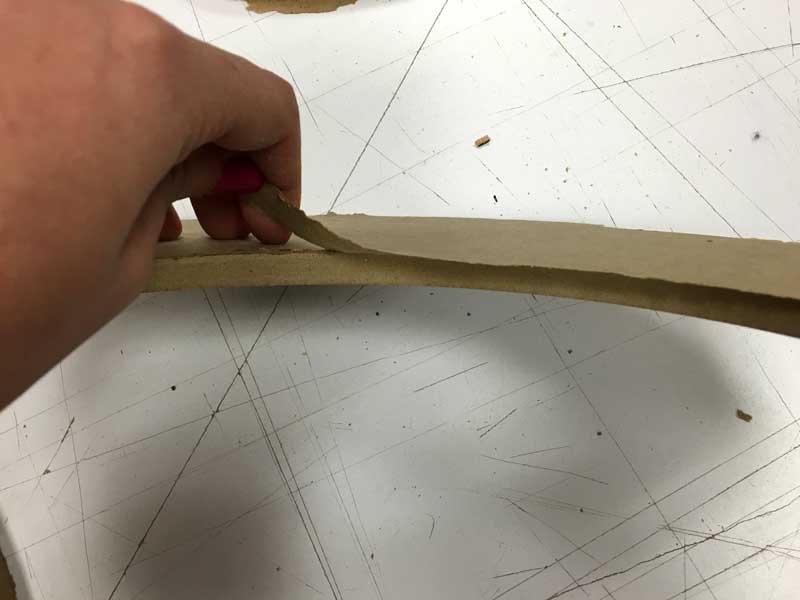

For the other two sheets of wood, I made the same routine at first: cutting 0.5 mm at slow speed to check that everything is ok; but then I made the cutting routines faster and a little bit speeder, in two layers; and the pieces didn´t move from its place.
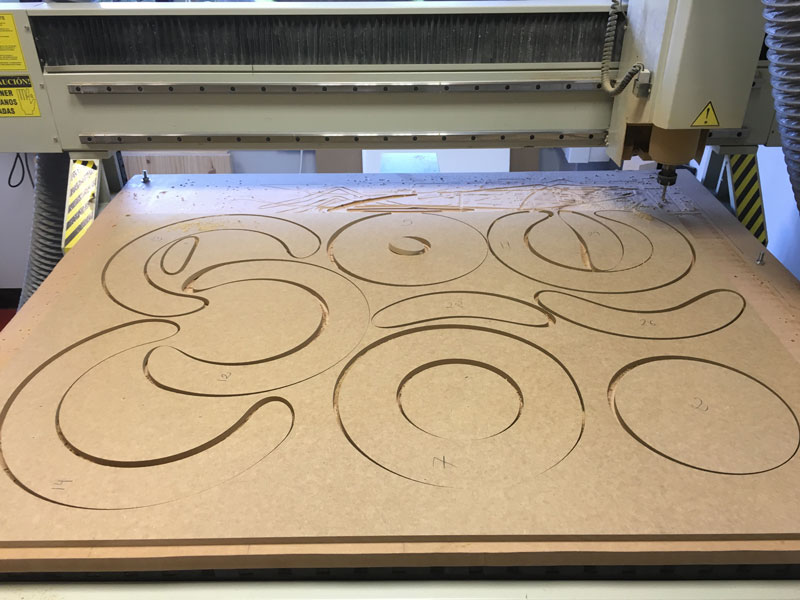
I made a mistake on the last one, I forgot to order the software to cut inner pieces before the outside ones, so two of them moved and cutted wrong the circles. I fixed them a little sanding them before.
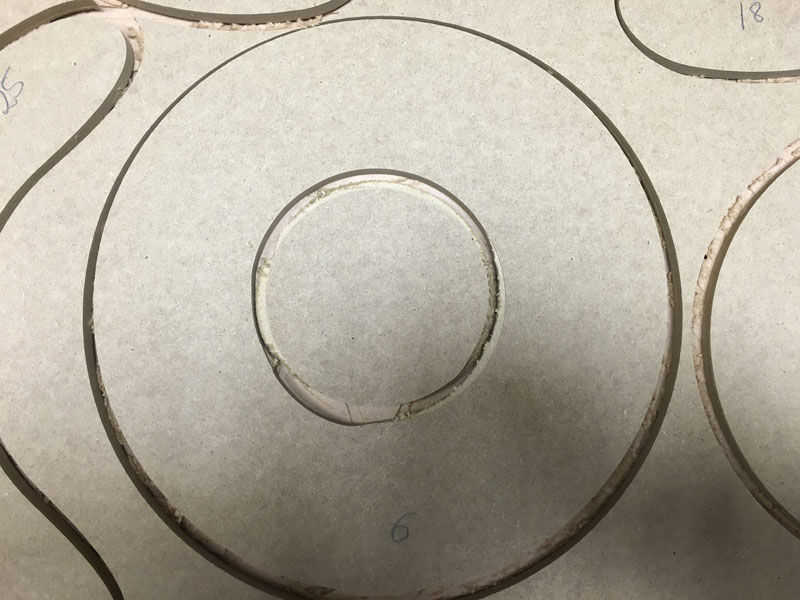
Gluing the pieces was quite easy, but then I realized what where the little points on the design output from 123D Make, patterns for placing them properly....
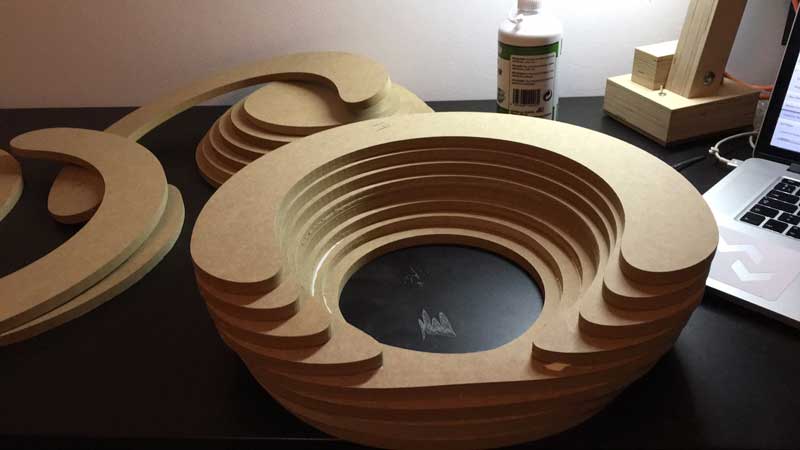
I made a super mistake taking measures. Its quite small for my cat. I should made it double of the actual size. And it doesn´t look comfortable at all. But I think this is going to be a cool plantpot.
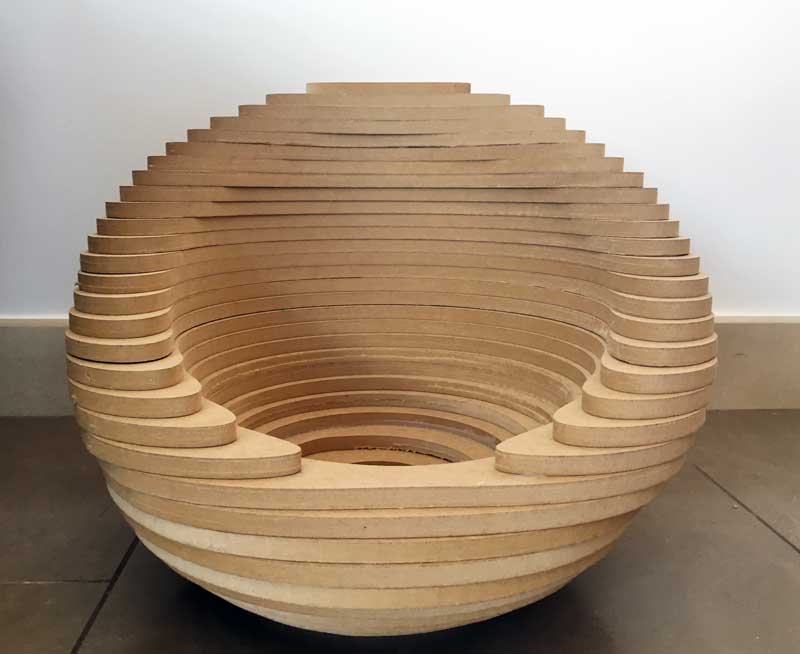
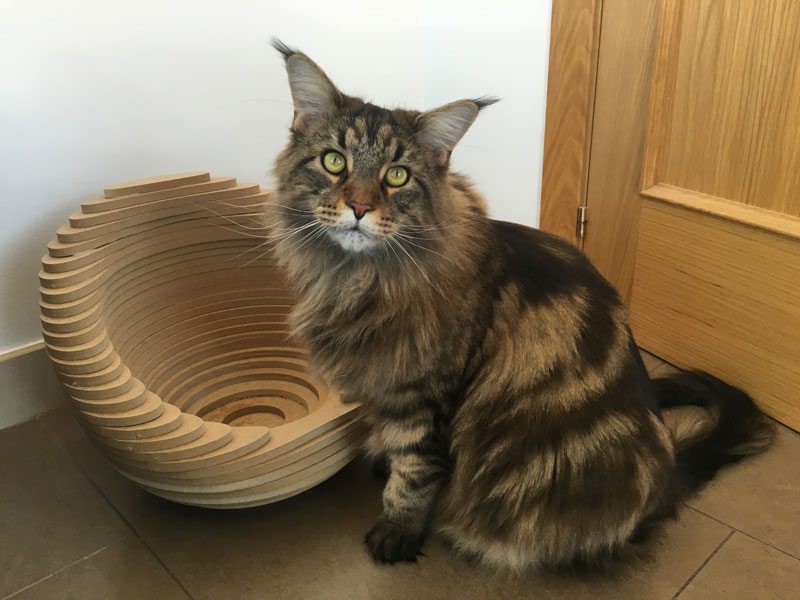
I want to make a second one, with other construction mode, im not happy with this assignment results, altought I learnt a lot about computer controlled machining.
COMPUTER-CONTROLLED MACHINING |
|
Explained how you made your files for machining |
X |
Shown how you made something BIG (setting up the machine, testing joints etc) |
X |
Described problems and how you fixed them |
X |
Included your design files and ‘hero shot’ photos of final object |
X |