Design and make a 3D mold, and produce a fiber composite part in it
This week’s assignment was to design and make a 3D mold, and produce a fiber composite part in it. I have never done anything like this before so it will be completely new to me. Beforehand i think won’t be able to use any fibre composites in the lightsaber, so i think i’ll just make a small boat and maybe after this week’s experience i will have found some use for fibre in may final project.
The 3D Mold
To make the mold for the boat i used Tinkercad which i find very convenient for making mold for objects. I did the same thing i did in the molding and casting week but inverted the object instead of being everted.
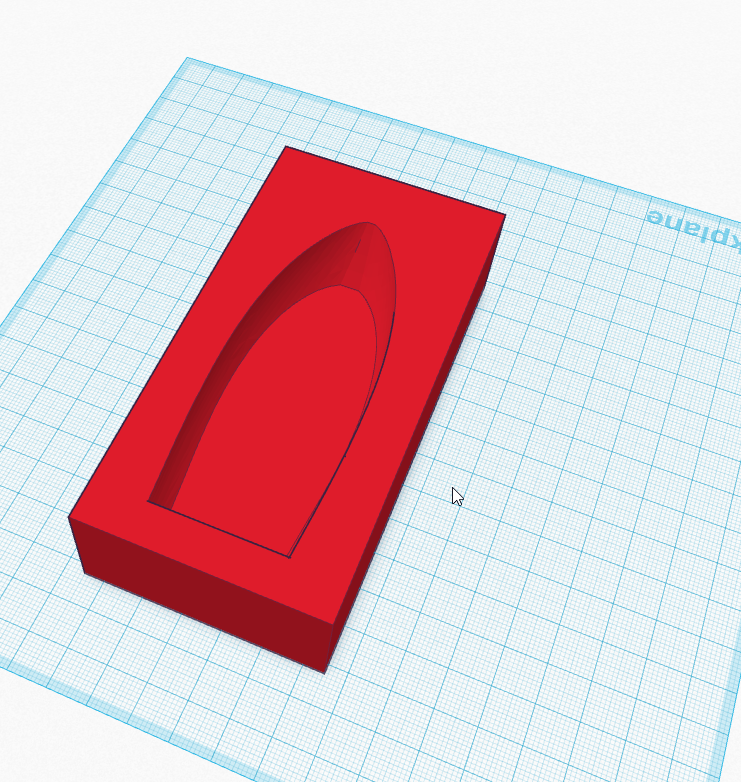
So when the 3d model was ready i imported it to Vcarve pro to get it ready for the shopbot. I was going to use foam to make my mold so i measured the foam i was going to use and entered the size in Vcarve. Then i made two toolpaths, one for the roughing part and the other for the finishing touches and next i saved these toolpaths as shopbot files.
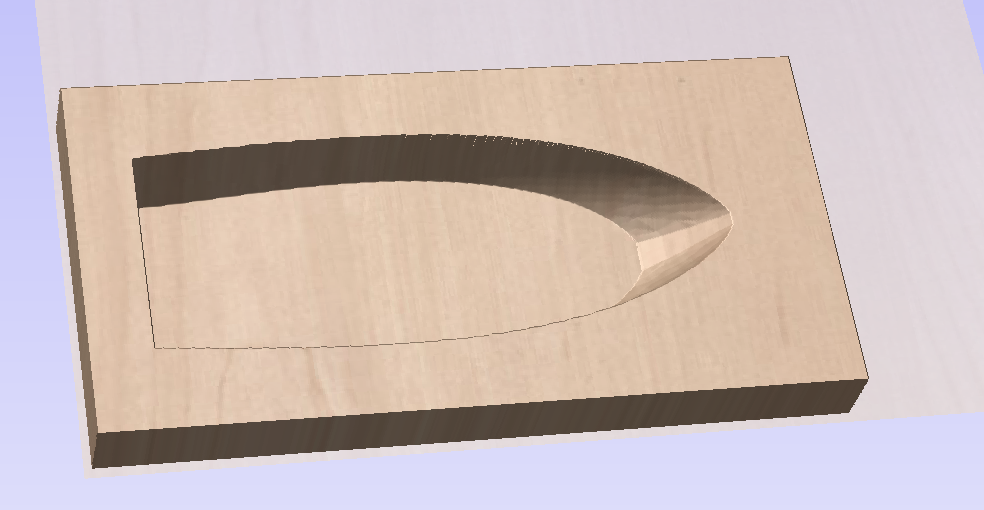
Now i placed the foam on the shopbot and fastened it by drilling it to the plate and then i started the cutting. I decided to make another mold because i found the first one to be a little bit too small. Then when the molds were ready i blew on them with a hot-air gun and painted them with Gesso to make them more compact.
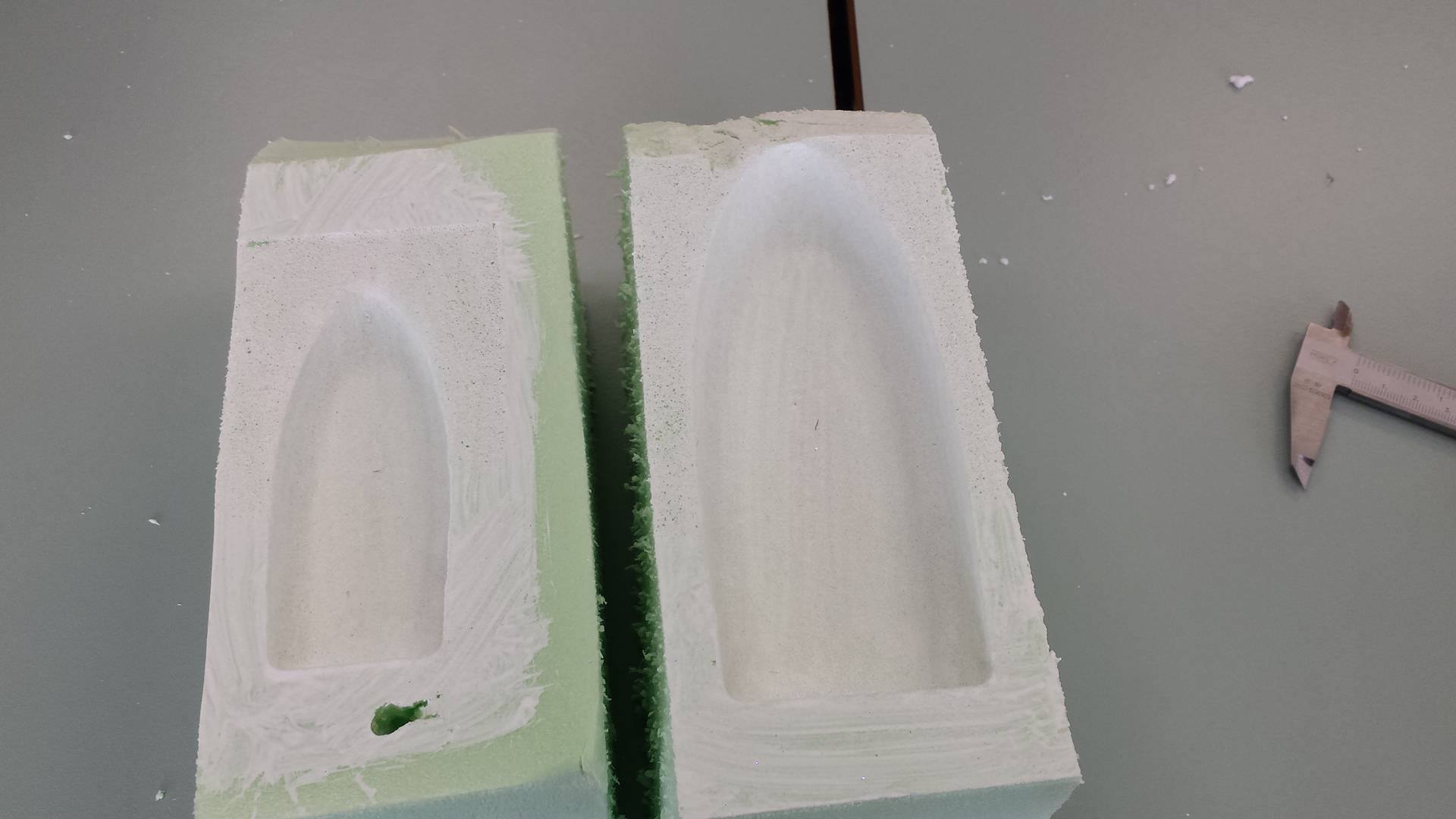
Making The Composite
Here in fab lab Vestmannaeyjar we started this week off by visiting a local glass fibre company which specializes in fixing boats among other things, using glass fibre. The owner of the company talked to us about the glass fibre and showed us how to mix the resin and the methods for layering the resin and the glass fibre. We got some glass fibre and 2l of resin from him that we were going to use. So we mixed the resin outside because it smelled really bad and it was a lovely day outside for mixing resin.
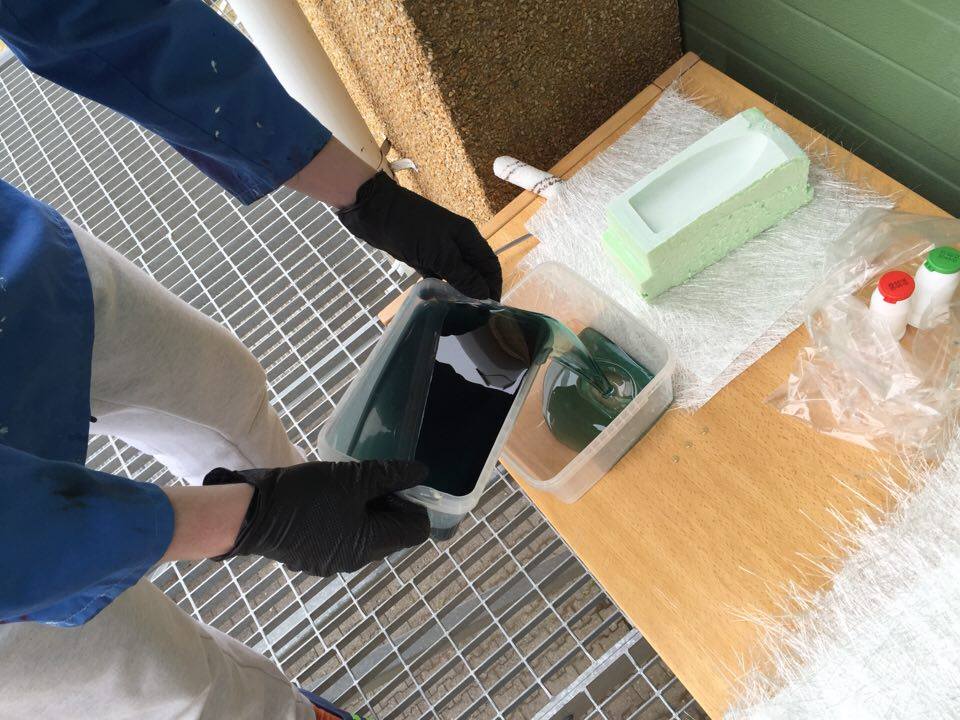
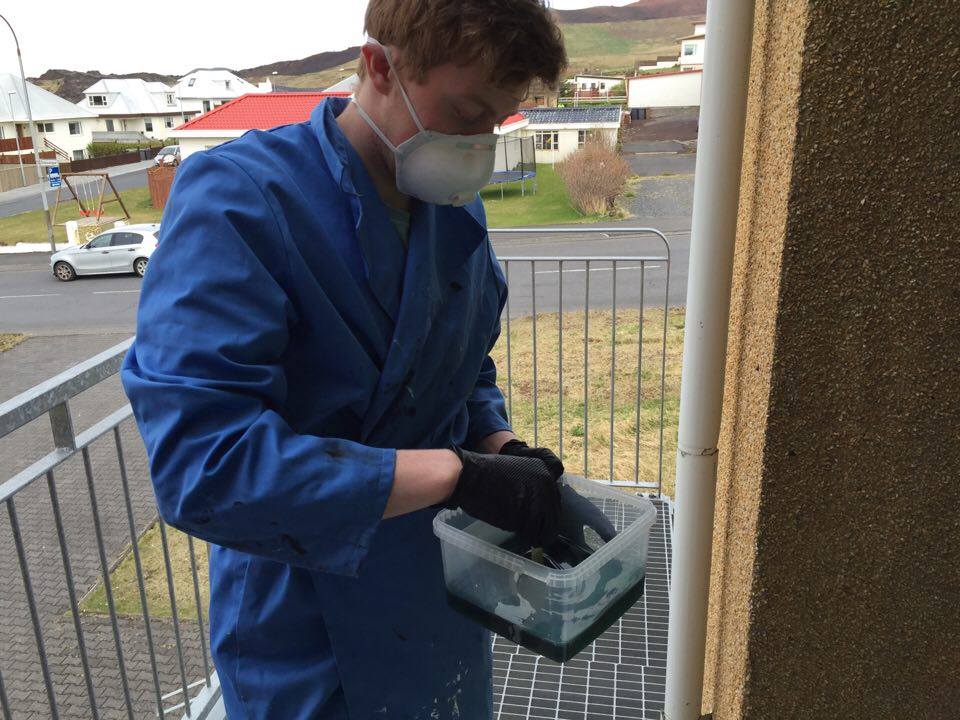
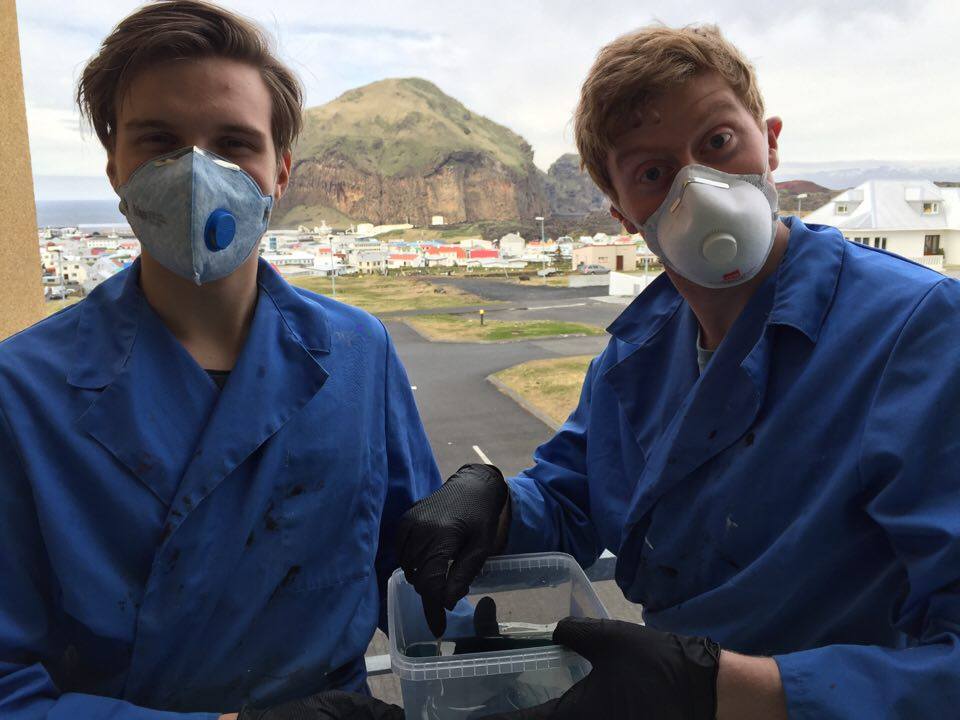
The mixing went well and then it was time to layer the resin and the glass fibre. I found that part pretty difficult, i put 3 layers of glass fibre and after that was complete it was time to wait for it to hardened.
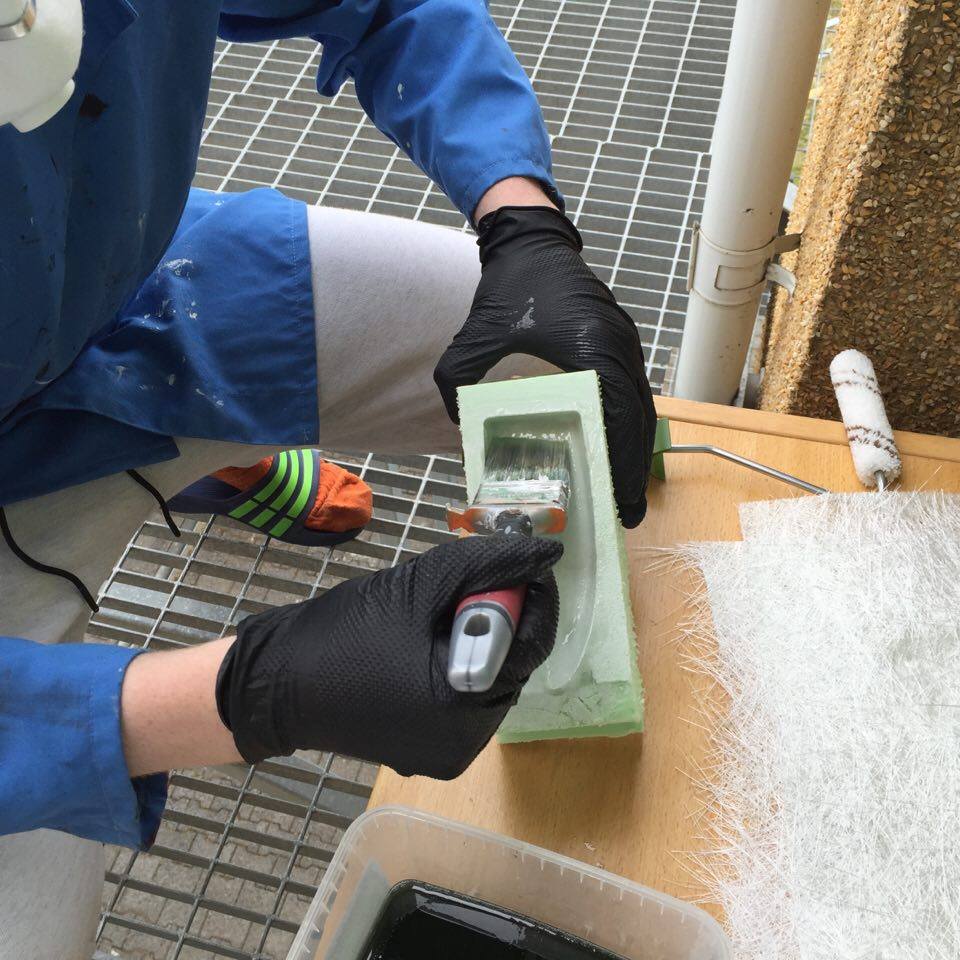
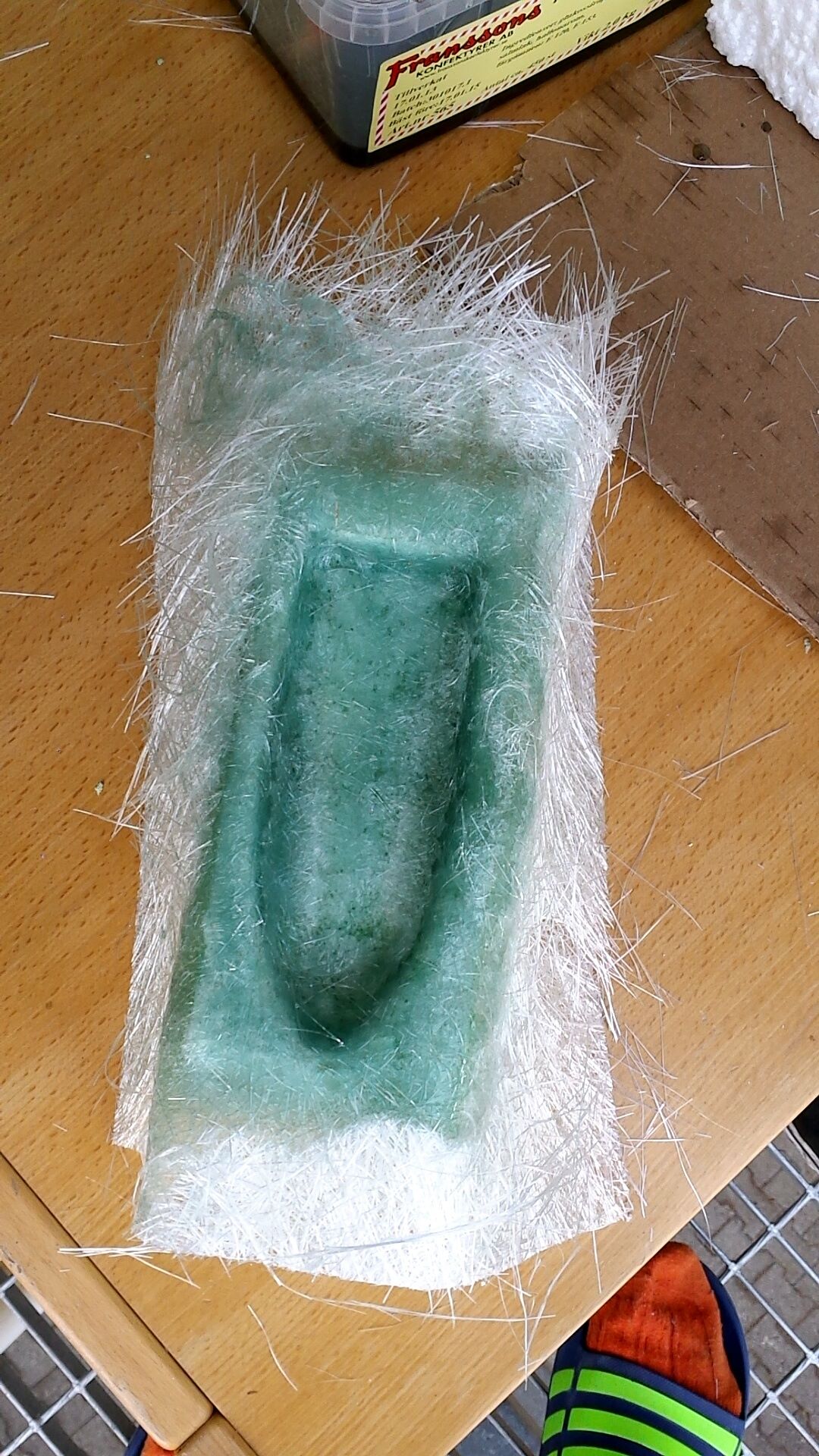
About 24 hours later the boat was ready if we can called that a boat. I can’t say that it looked good, i had forgotten to put plastic at the bottom of the mold so the resin had melted a little bit of the foam, so i’ll have to remember that if i’ll do this again.
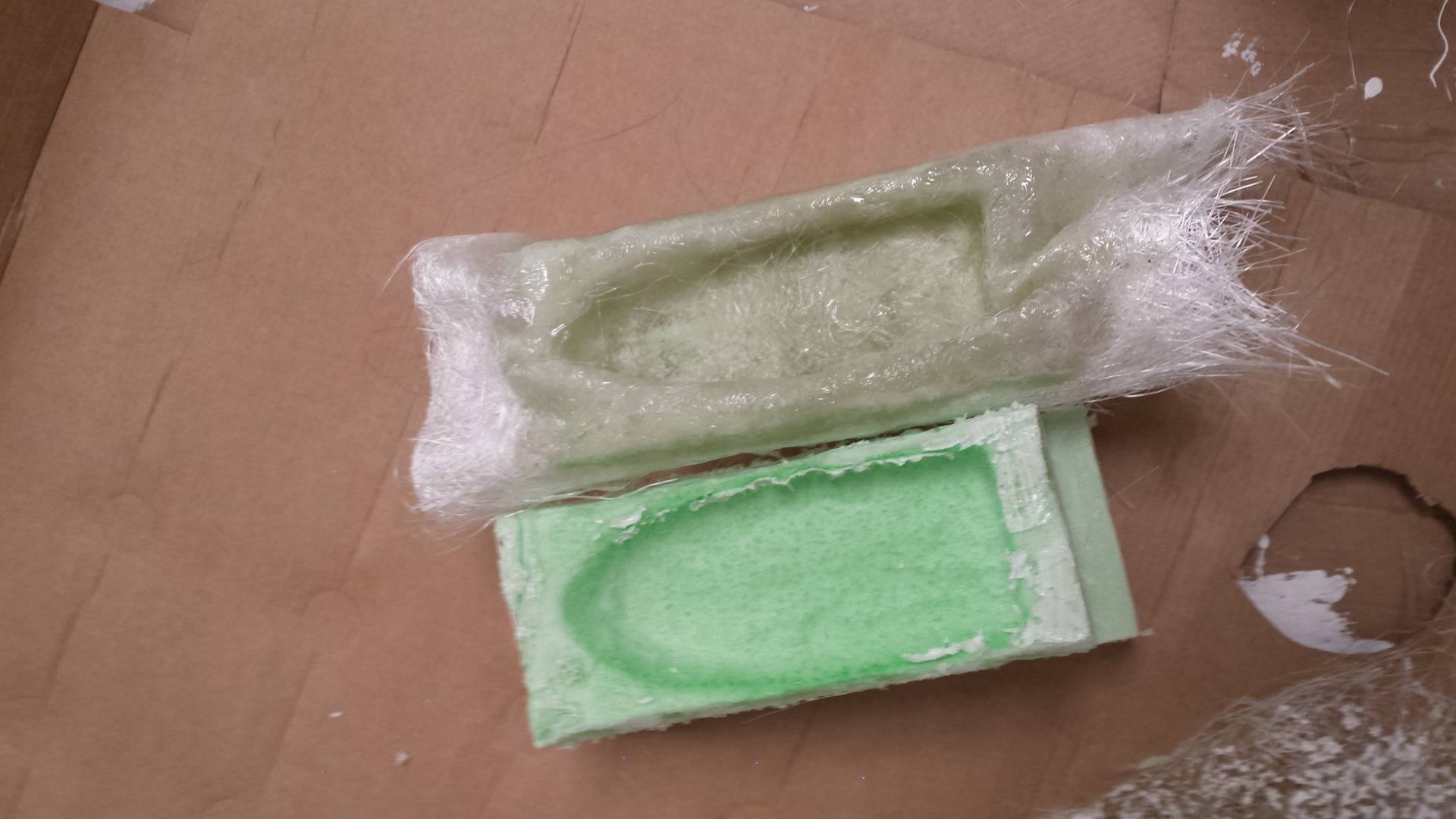
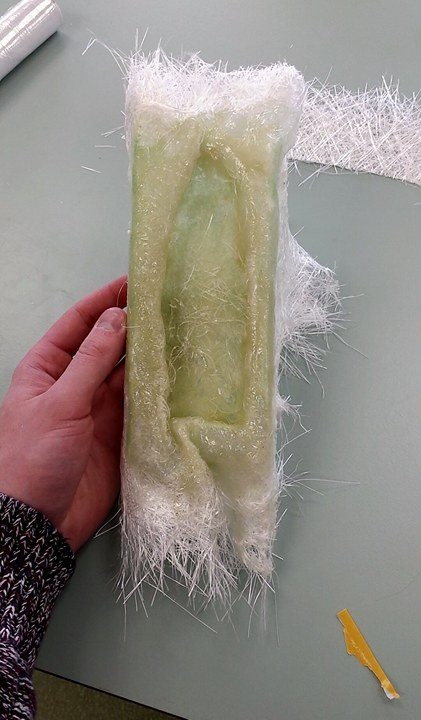
Files
Shopbot FileVcarve File
Tinkercad File