Week 14 - Composites
Produce a fiber composite part
Steps:
* Design something you can mill
* Mill polystyrene and prepare a mold
* Produce a fiber composite part in it
Design something you can mill
With composite materials we can obtained thin surfaces with good structural and physical qualities: so I decided to design free diving fins. I disassembled my fins, so I copied the attachment of the blade on the shoe.
Therefore I divided the fin molde, in order to
obtain a milled object: It was too high to be milled in our machines.
I also added the anchor points so my object was not moving at the
end of the milling operation. Most milling software help you with tabs (or tags) systems just when you do 2D operations.
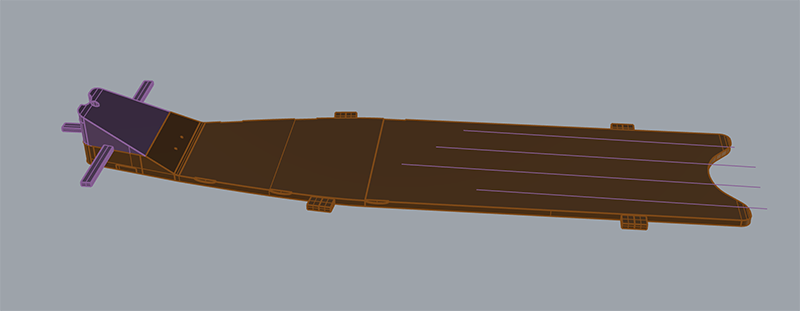
Mill polystyrene and prepare silicone mold
I prepared two separate files, and I machining them with the same tools: 6mm endmill for roughing and diam. 4mm spheric for finishing. Remember to selected Material Boundary for the Machining Limit.
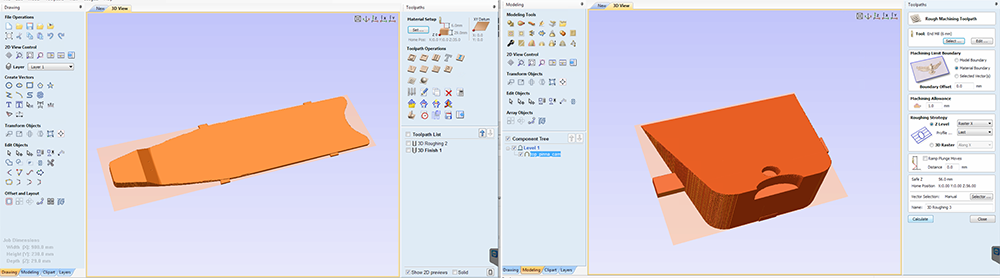
I set the machine very fast for milling this kind of foam material: feedrate 3.000 mm/min, plunge rate 1.200 mm/min, spindle speed 15.000 r.p.m.
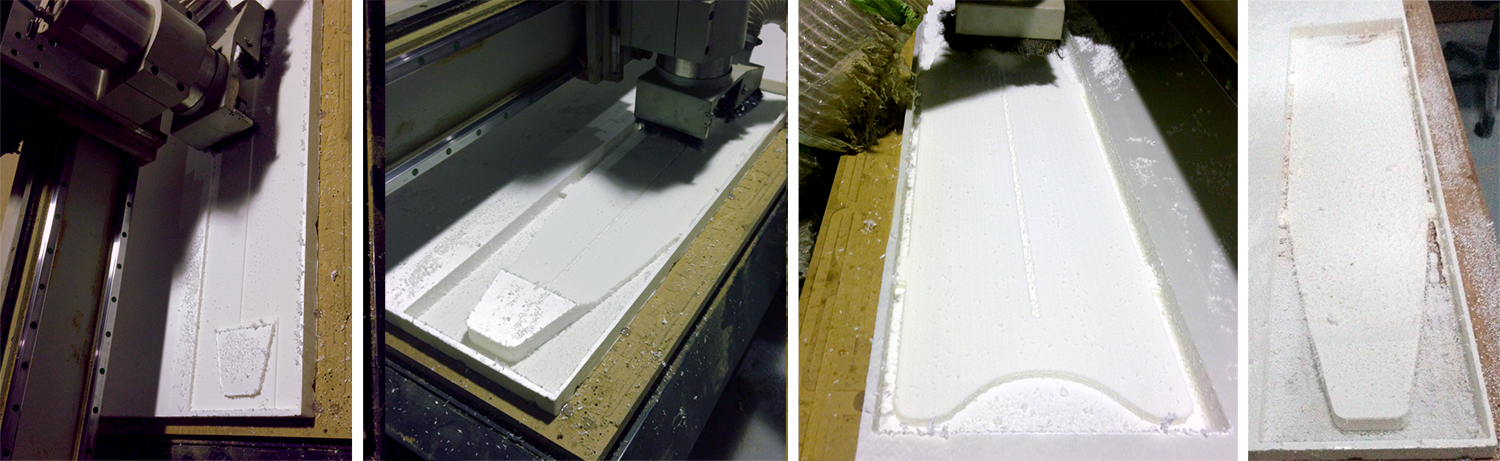
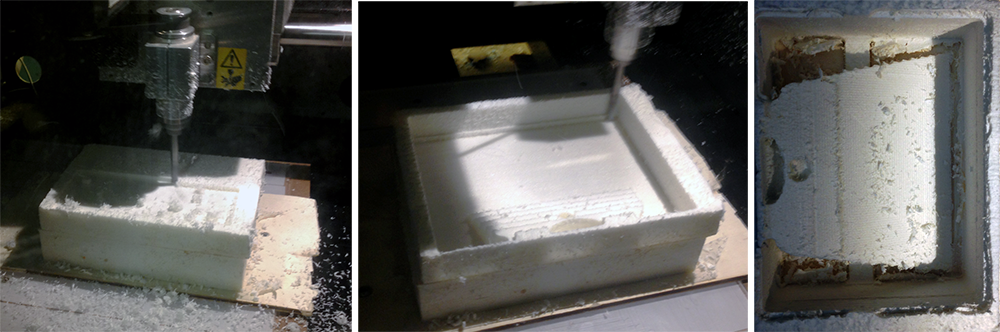
I glued the two pieces together and I waited 10 hours to dry well the glue.
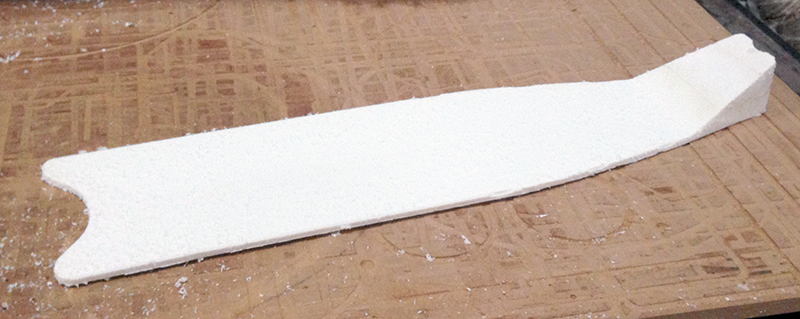
Produce a fiber composite part in it
For an ecological issue, I decided to experiment with linen: once I'll find the best solution I would like to repeat these steps
with the carbon fiber.
I cut 5 shapes of decreasing length, in order to obtain a shovel with different flexibility.
This solution should improve the movements fluidity, increasing the propulsion.
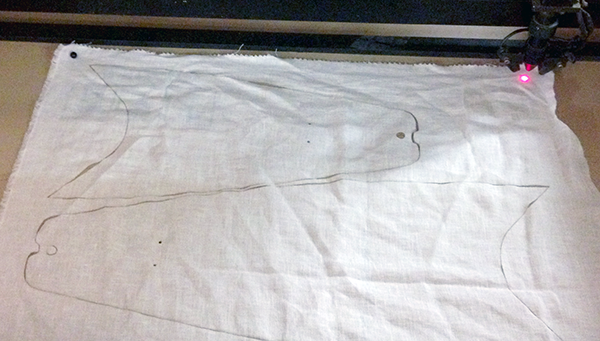
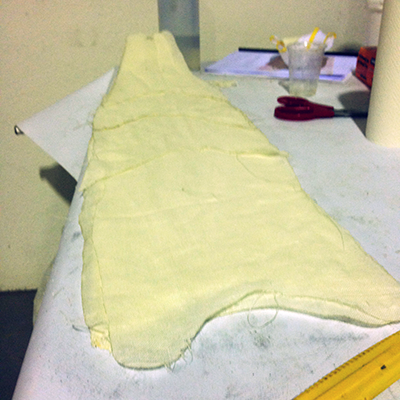
After cleaning well the surface, I sprayed the release. Is a compound based on wax, so after dried up I polished it and I obtained a smooth waxed surface.
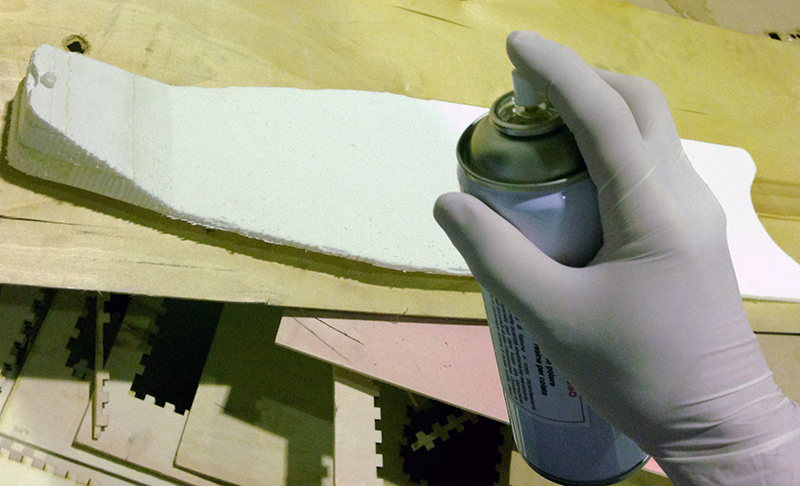
I followed the directions of the epoxy resin (a catalyst at 60%) and I prepared 380g (200g + 180gdi catalyst).
I have
spread a layer of resin and there I laid on the first layer of linen. So I brushed over the other resin and I applied with a spatula.
I repeated the operation for all five layers.
I chose to put five layers because measuring the material and estimating the
thickness of the added resin, I would like to reach a thickness of 2 mm in the thickest part.
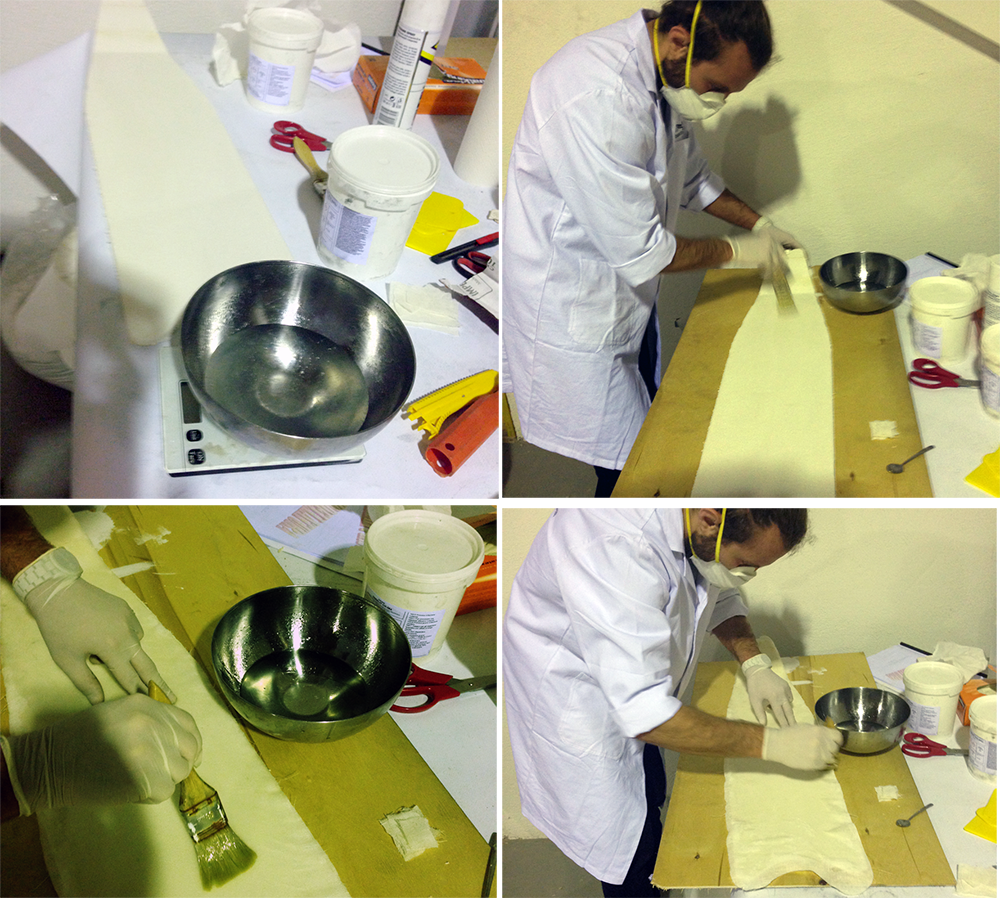
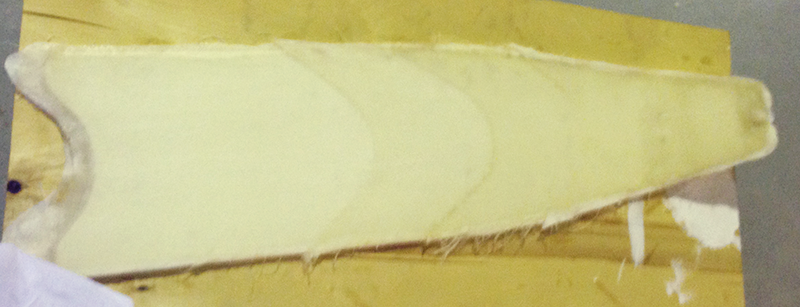
To get an accurate result, I decided to use a vacum system. I stretched a micro-perforated film on the fin, I added a layer
of absorbent material and then another film. I put everything in a bag and I placed inside a little tube. I connected the compressor
with the venturi valve to the bag and I pulled out the air.
I waited 30 min, the excess resin was visibly absorbed by the
absorbent material. Then I carefully pulled out the tube without let escape the air and I left it to dry for two days (were raining days,
high humidity, That's why I waited so long).
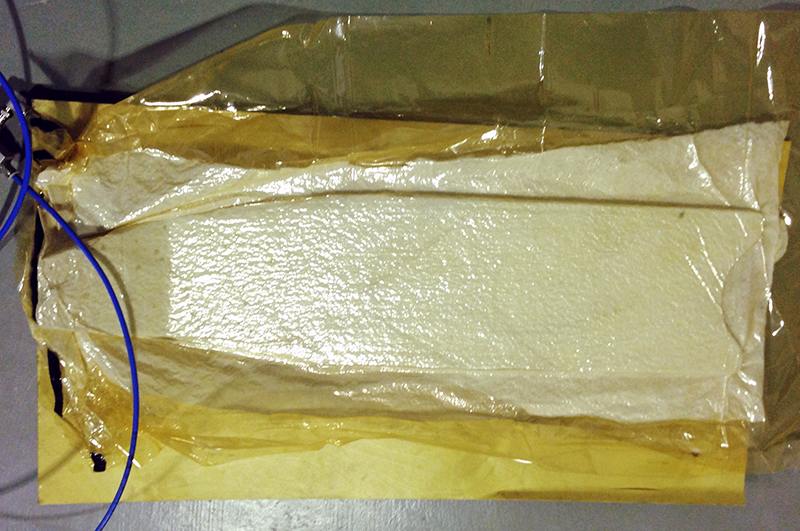
I extracted the product, cut off the excess edges and slightly sanded.
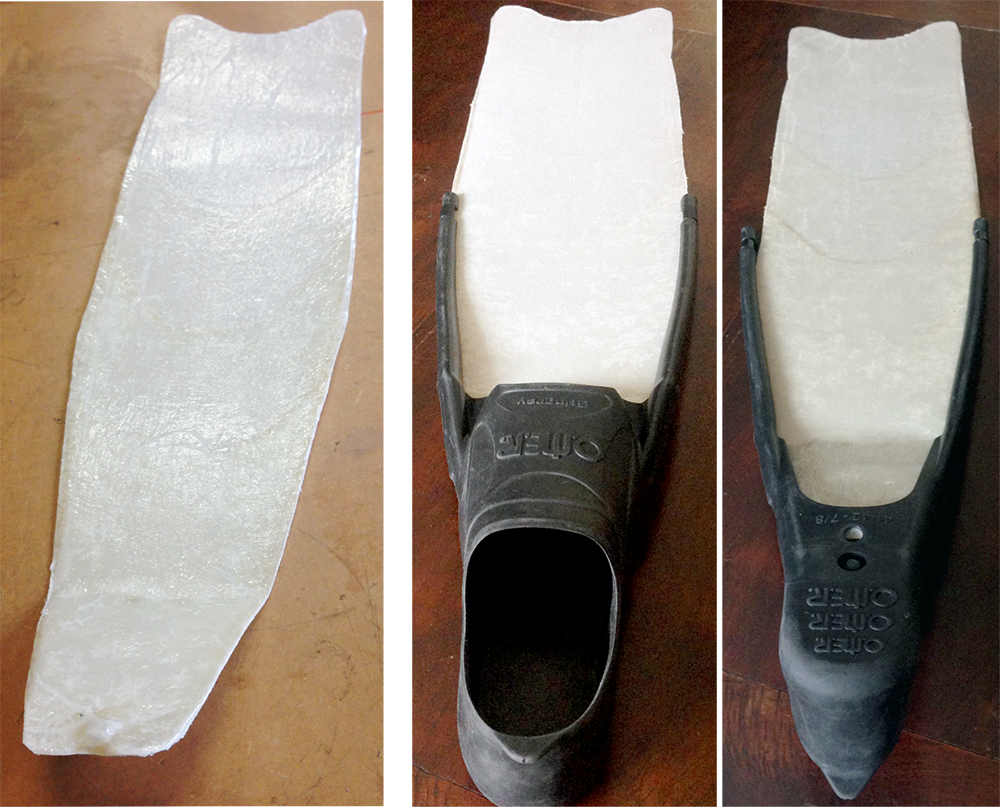
RETURN UP
← week 13 / Output Device | week 15 / Networking and Communications → |
---|