| Home | | Weekly Assignments | | Final Project | | Photo Gallery |
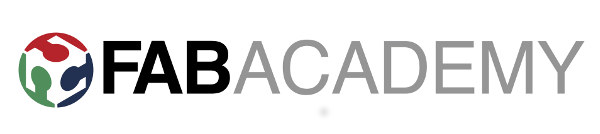
Week 3 - Computer-controlled cutting
1. Vinyl Cutter: Introduction
2. Assignment: Using vinyl cutter
3. Laser Cutter: Introduction
4. Assignment: Using Laser cutter
1. Vinyl Cutter: Introduction
Vinyl cutter is a very versatile device which can be used for a plethora of applications other than just sticker cutting such making flexible circuits, making screen printing boards etc
Our Fablab is equiped with a Roland CAMM-1 Servo vinyl cutter, a few rolls of vinyl sheets, few screen printing boards, screen printing ink etc. In pre fab workshop, Luciano tought us how design and cut sheets using Vinyl cutter and Fab Module.
Any png image desinged in any designing software like GIMP, Illustrator etc. can be fed to vinyl cutter via fab module. The input file should be a dual tone image in png format.
Loading sheets on vinyl cutter
I loaded a piece of vinyl sheet by pulling up the lever on the rear side of the vinyl cutter. This loosens the hold and vinyl sheets or peices of vinyl sheets was slided in and loaded.
Changing blade
Vinyl cutter bit/blade can be replaced unscreweing the bit with hand. I replaced the existing blade with a new Roland 45 degree vinyl cutter blad blade.
Positioning rollers
I made sure that the visible rollers on the front side are kept over the vinyl sheet and also double checked if its positioned on the white markings on the vinyl cutter.
Setting up Origin
As I was using a vinyl sticker piece, I selected the peice option. The vinyl cutter will measure the lenght and width of the peice by rolling in and out. Once its done. Orgin can be set by moving the head with the arrow keys and you are all set to go.
2. Assignment: Using Vinyl Cutter
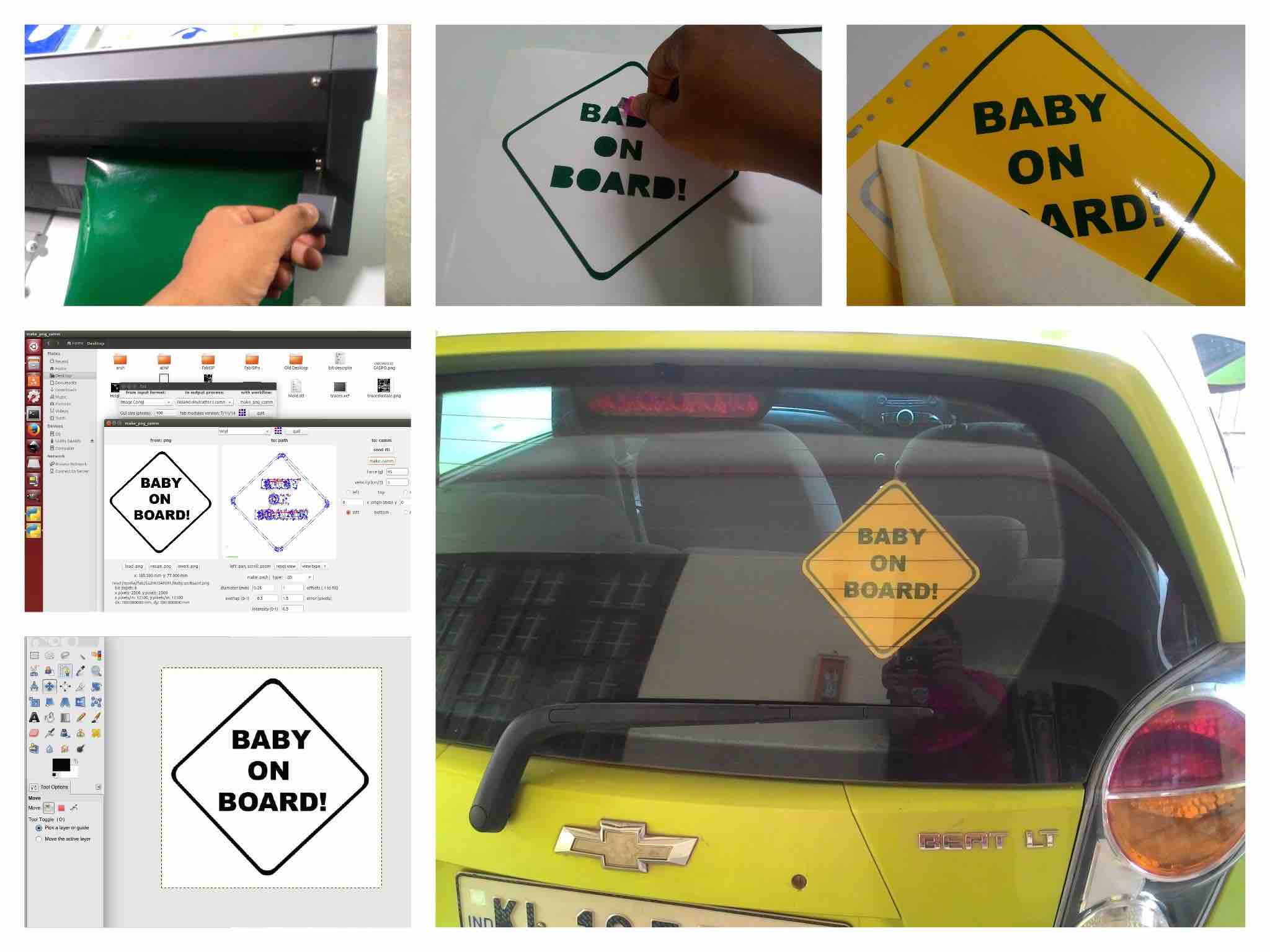
Assignment for this week is to create something with the Roland Vinyl cutter and I wanted to make something interesting and personal. I wanted to stick a "baby on board" sticker on the rear glass of my car so that whenever I am driving too slow, the vehicles following me will understand why I am driving slowly.
For this assignment I am making a two layer vinyl sticker. The base layer is Yellow and the top layer is green.
Designing the sticker
I used GIMP to design a simple baby on board sticker. I made sure that I have used only two colours black and white and saved the file in png format. As mentioned above, I am using yellow and green vinyl sticker sheets to get my job done.
Fab Module
This time I used the web version of Fab Module. I opened browser on Ubuntu on our FabLab computer connected with Vinyl cutter and typed the following address in the address bar
Selected the input as 'png' and output as 'Roland Vinyl'(.camm) and click on load png. Once that was done, I used the resize option to resize the sticker to height 15 cm and width 15 cm.
http://fabmodules.org/
After resizing, I clicked on make path. This will show the path in which the blade will move while cutting the sticker and gives an idea how the job is going to be done. After that i cliked on make .cammm so that the vinyl cutter format for the resized image is generated.
Then I loaded green vinyl sticker sheet in the vinyl cutter and setup the machine. The setup instructions are available in this same page in my previous post. Once it was done, I clicked on "Send it". The machine cut the sticker precisely and it worked like a charm.
I removed the unwanted parts of the sticker using a stationary knife and used the masking tape to take the needed parts and sticked it on the surface of yellow vinyl sticker sheet!
My sticker is ready and it looks amazing.
The final step was to cut the edges out. Once its done I used two sided tapes to stick it on rear glass of my car.
Download sticker design file:
bob.png
3. Laser Cutter Introduction
Laser cutter is a brilliant machine. FabLab Kochi is equipped with a Trotec Speedy 100 CO2 laser cutter and engraver. Laser cutter is capable of cutting and engraving on a wide range of materials.
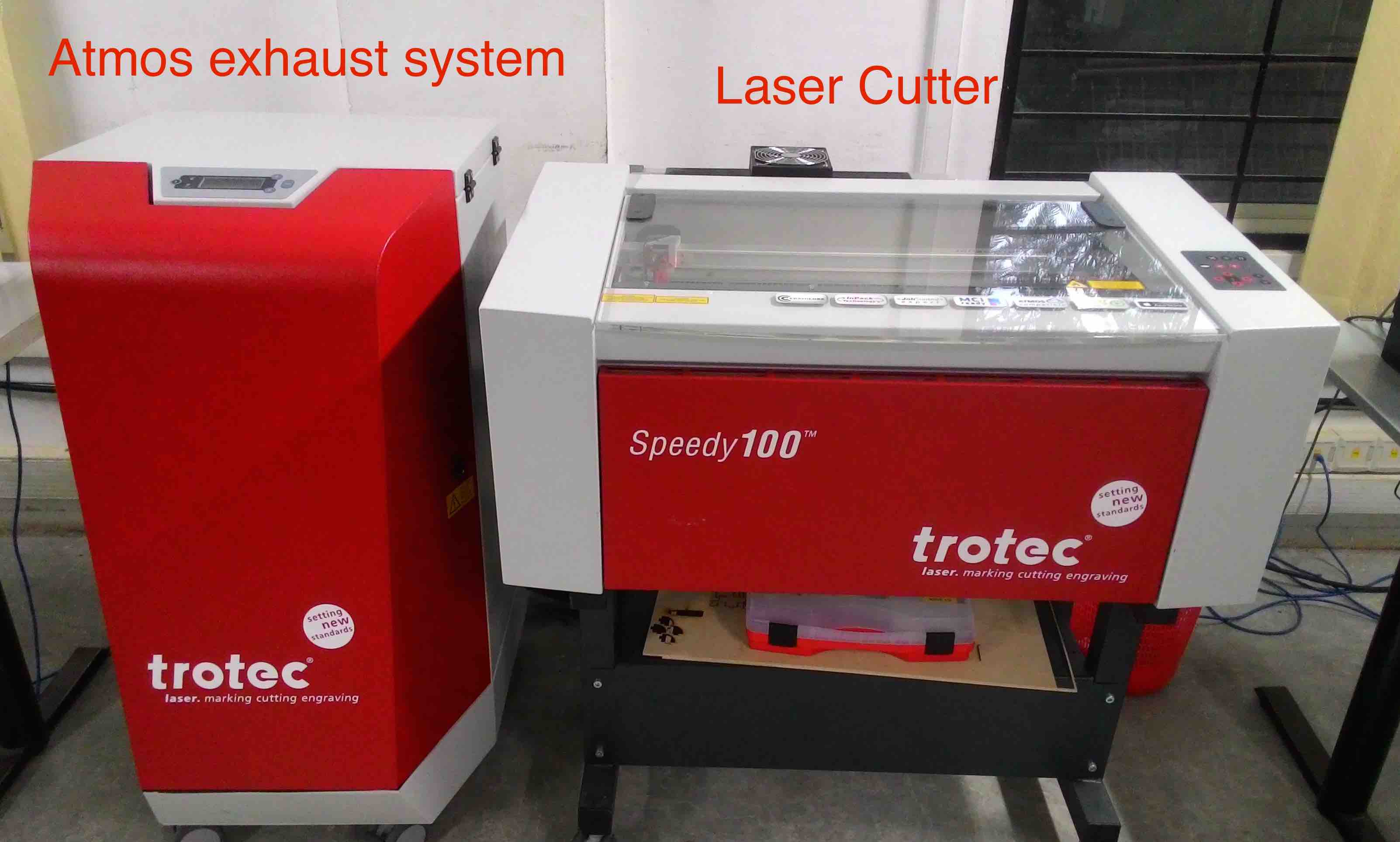
The laser cutter is mated with an atmos exhaust chamber which is capable of absorbing smoke/fumes that arise during cutting and engraving.
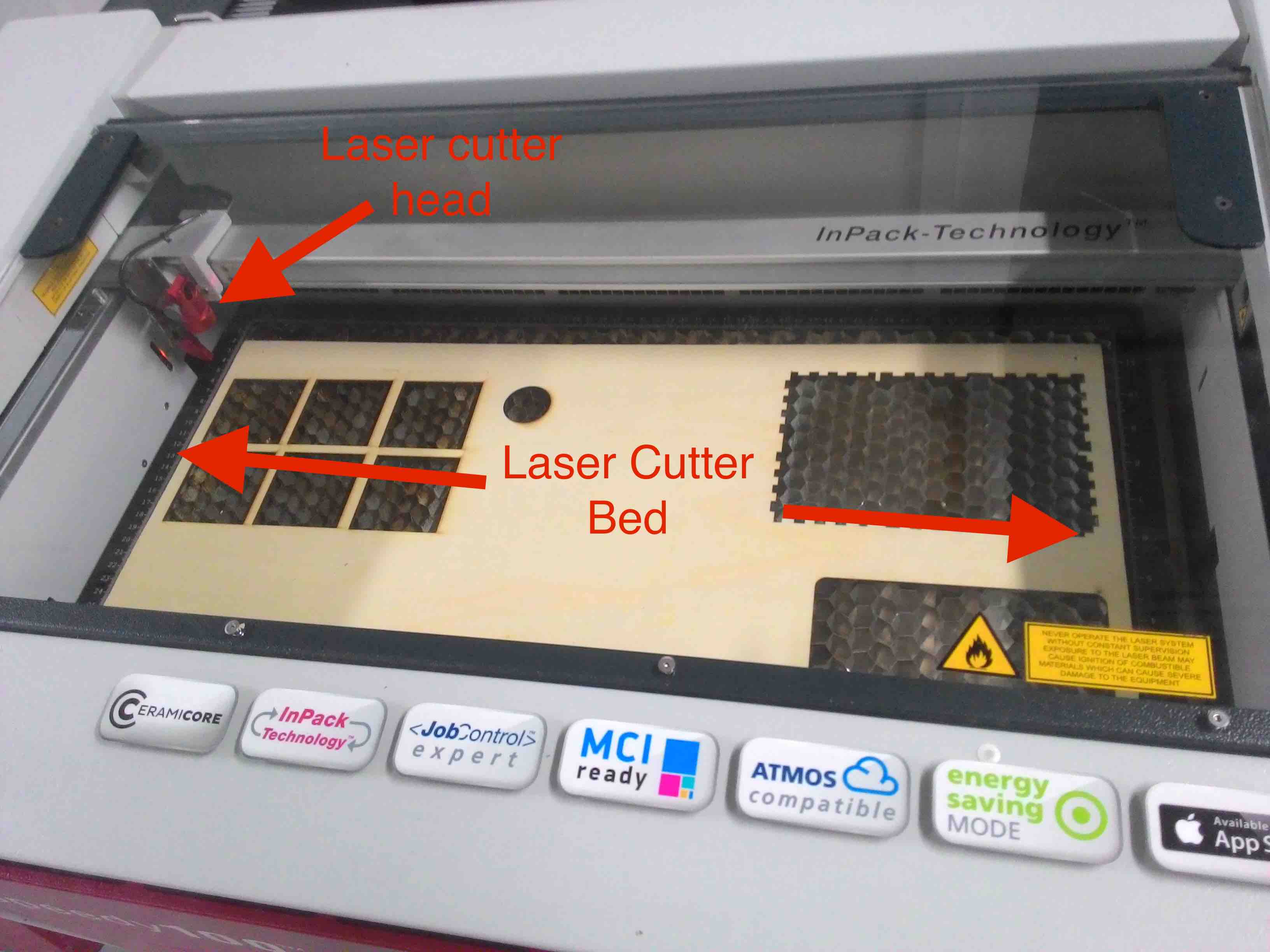
The laser cutter in our FabLab is capable of cutting soft materials like wood, acrylic, card board, paper, fabric etc. It is also capable engraving on tuff materials like steel, brass, tile etc.
The basic training on using the laser cutter was provided to me by the Trotec company representatives when they setup the laser cutter at this FabLab.
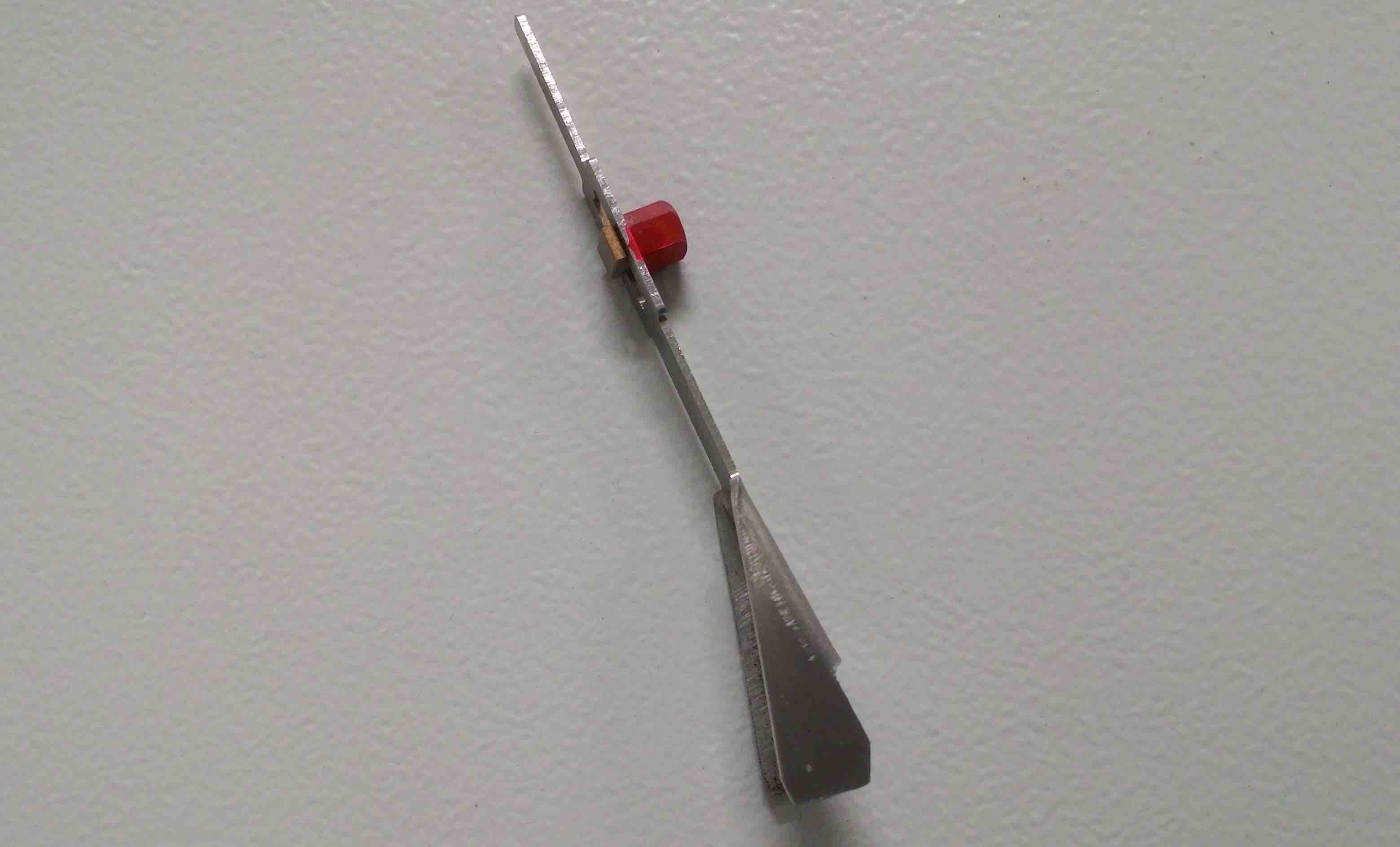
The head of the laser needs to be focused depending upon the kind and thickness of the material used. Focussing is made possible with the focus tool shown in the picture above. This tool is hanged fon the head and the bed is moved closer to the head using arrow keys on laser cutter till the tool touches the material in the bed and falls down.
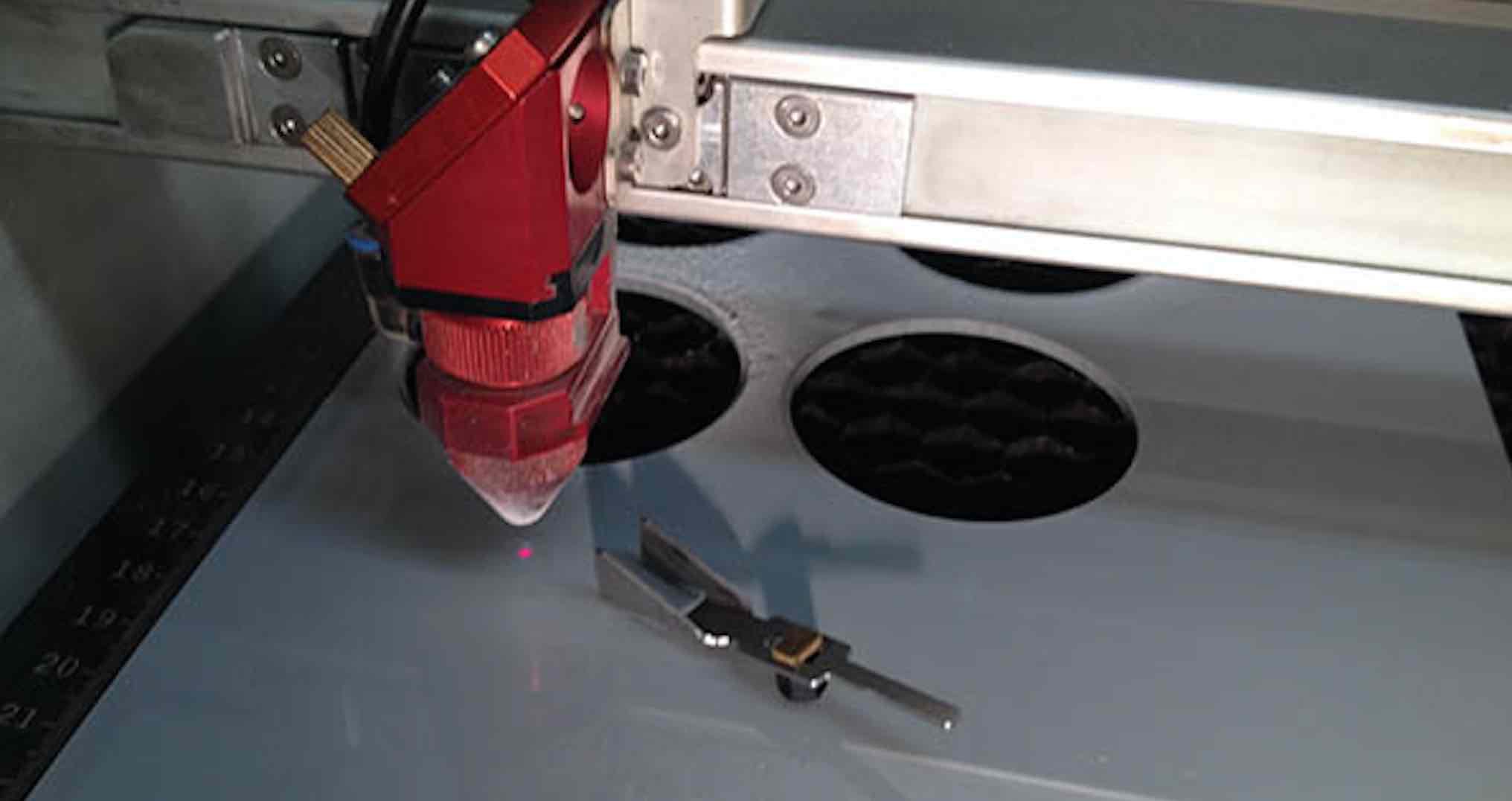
Once the tool is fallen down, The current position is said to be the optimal focus position for that material in the bed. Once the focus is right, the user can proceed with cutting or engraving.
The machine cuts and engraves based on its speed to power ratio. - Cutting can be performed by setting high power and slow speed. - Engraving can be performed by setting low power and high speed.
This weeks assignment is to design and laser cut a press-fit kit using laser cutter. My final project is a mouse trap and I will be making the outer box for the mouse trap with plywood on Shopbot CNC. But before that, I decided to laser cut the cardboard version of the same desing on our Trotec laser cutter. The following image shows how it should look like once its done.
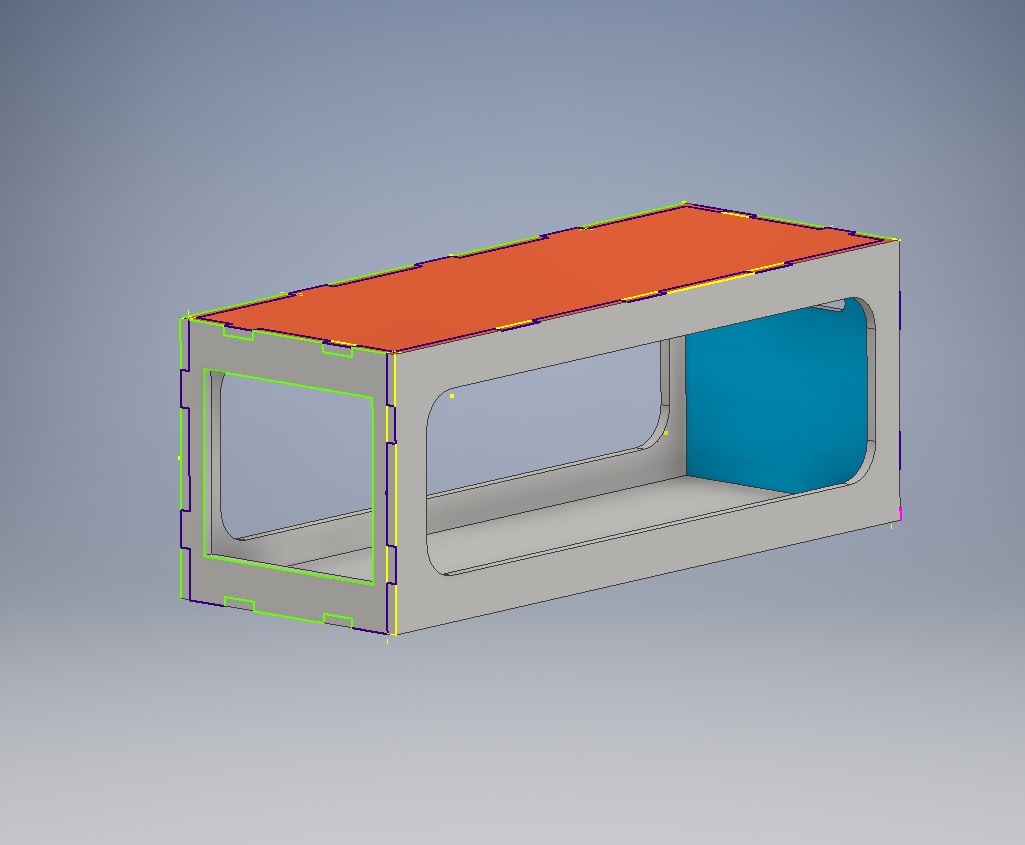
I designed the file in Autocad in dxf. Since our laser cutter bed size is 600mm X 300mm, I split the desing into different files.
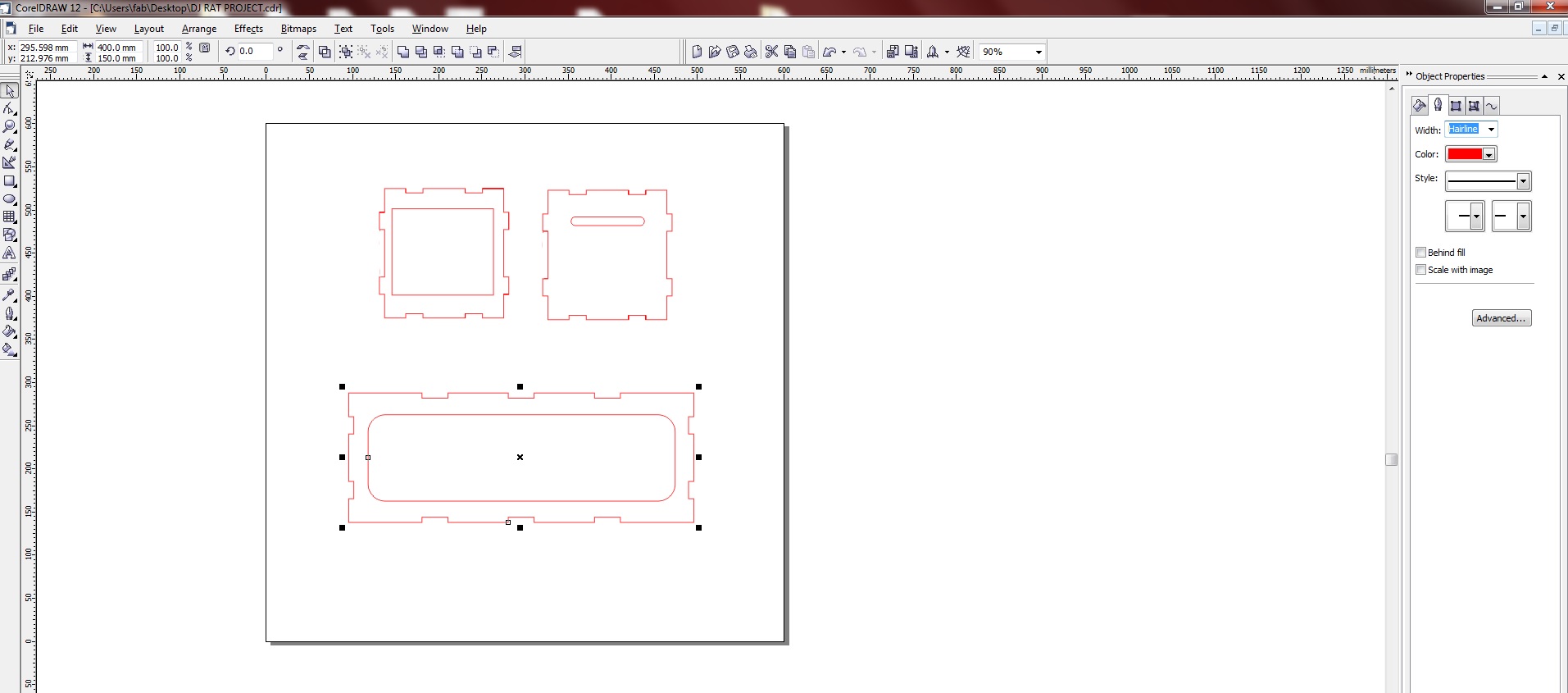
I have set red colour in desing to cut in Job control and set the power as 100 and speed as 3. The laser cut the carboard precisely.
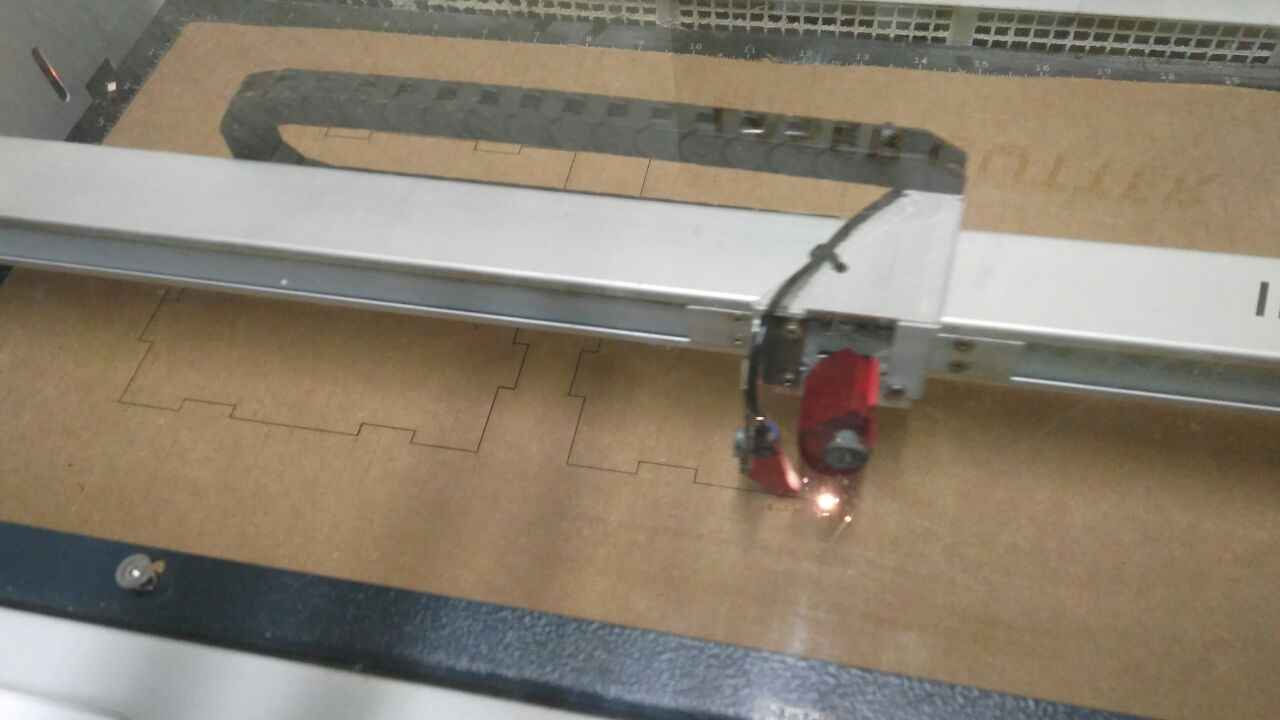
I had to load mutiple files to cut different sides of the press fit kit.
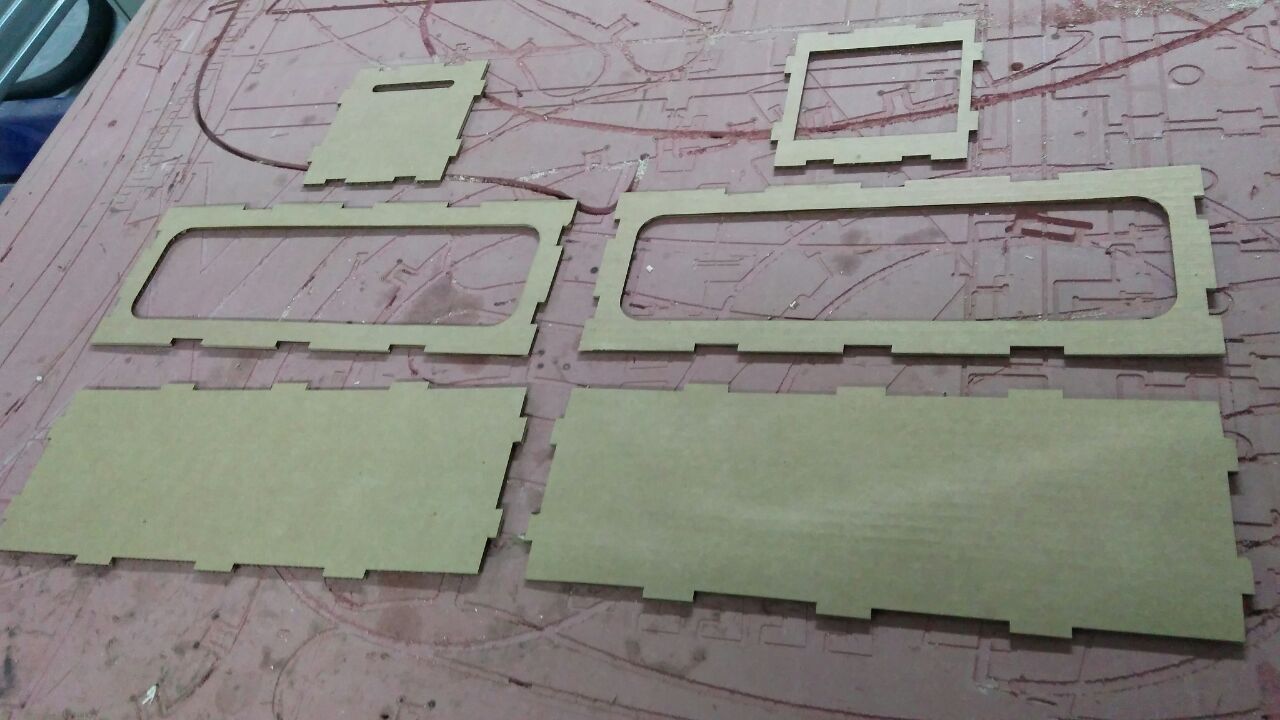
Once the pieces are joined together, it fits perfectly.
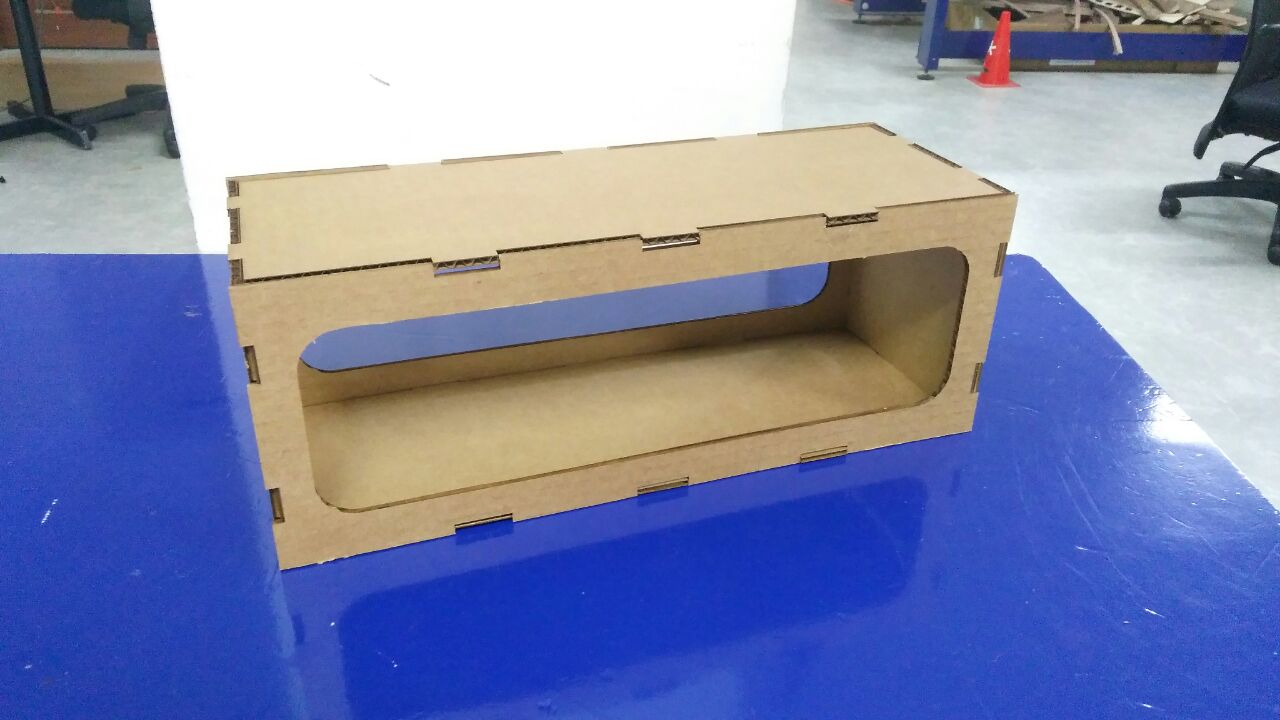
It looks nice! :-).
Just to do something additional, I designed and laser cut a craft plywood based coffe mug stand.
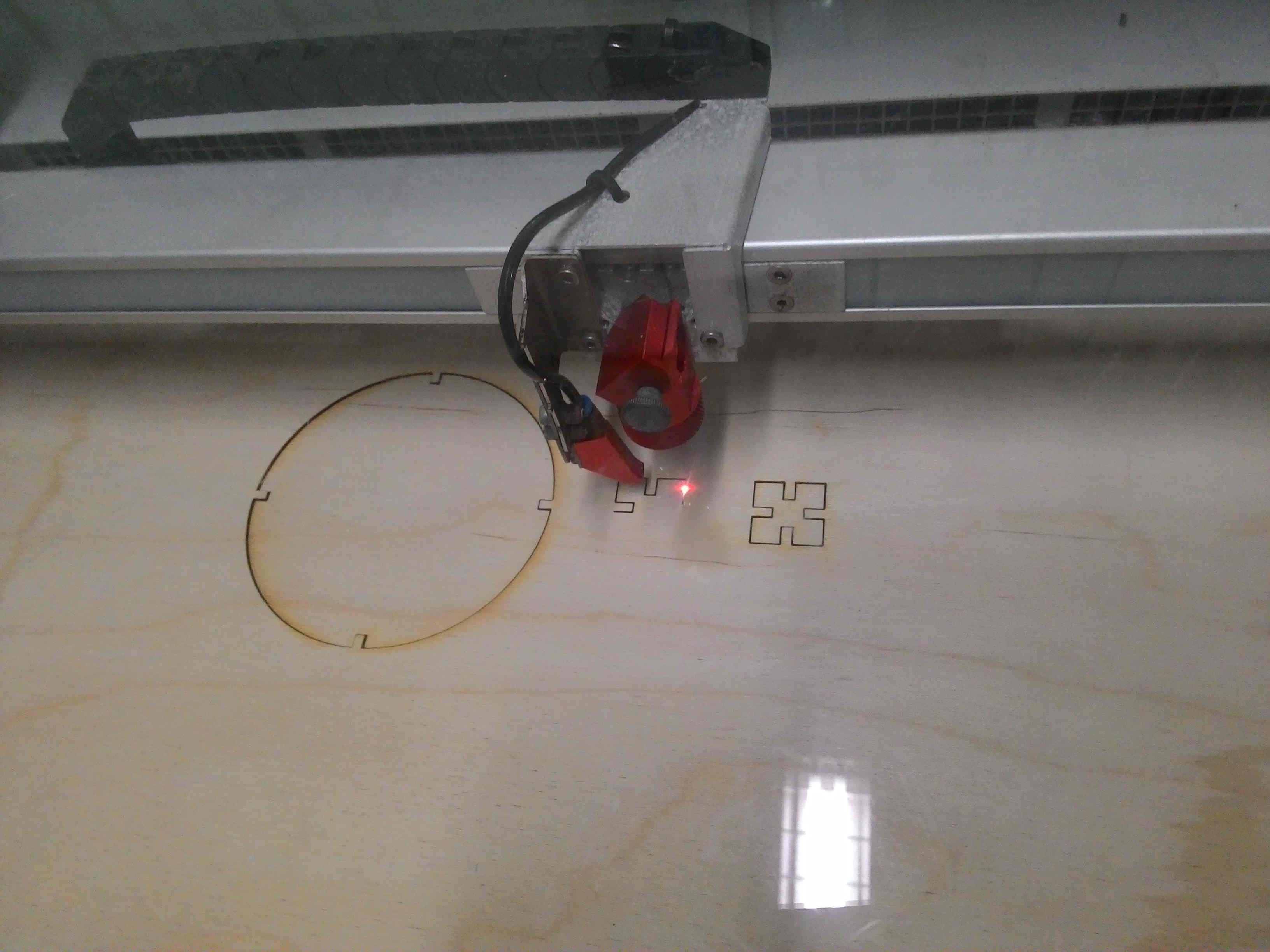
The desing for cut was made in solidworks and craft plywood was cut with trotec laser cutter. On joining the parts, this is what I got.
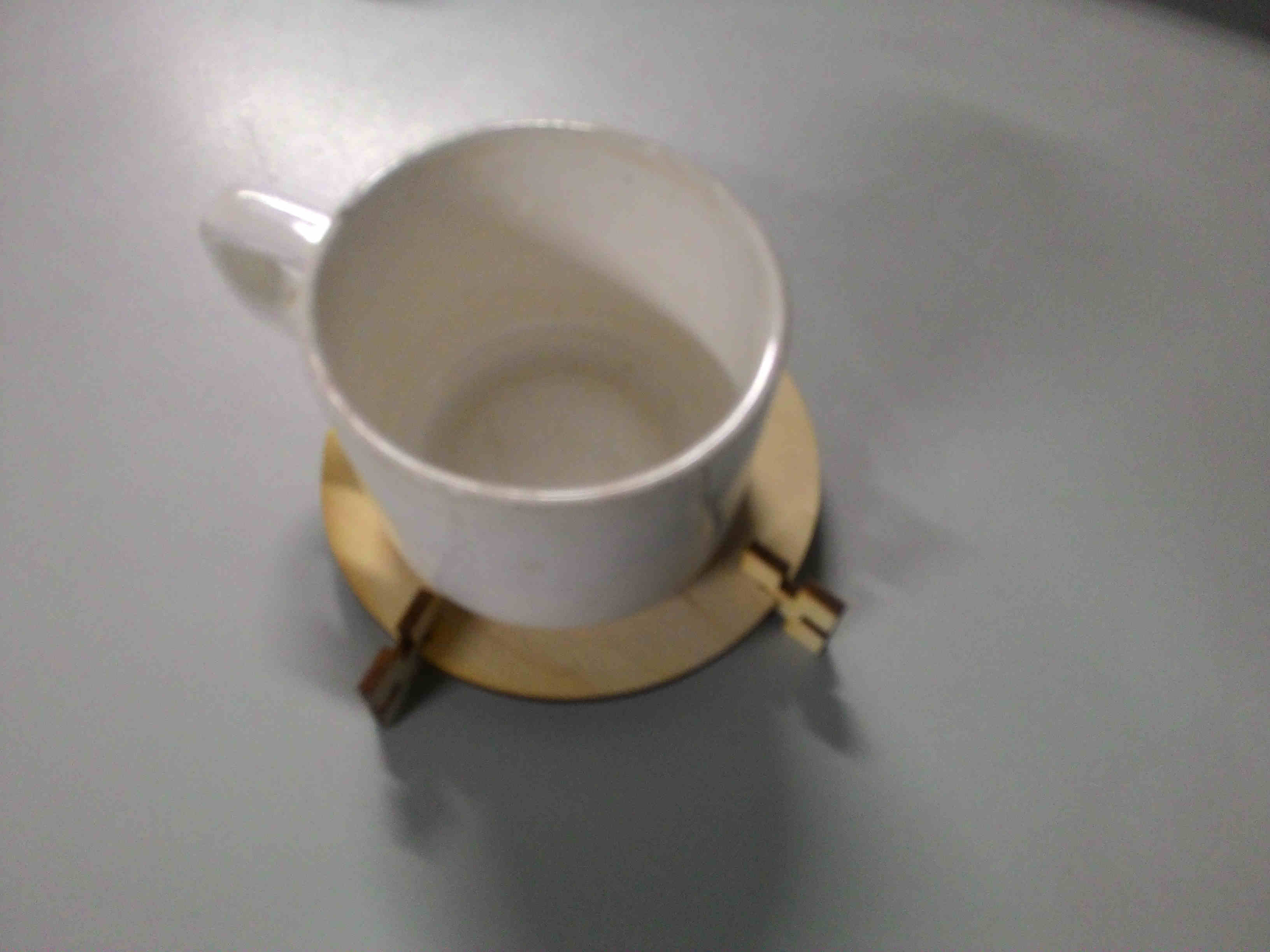
Download design files:
inlet.dxf
side2nos.dxf
topandbottom.dxf