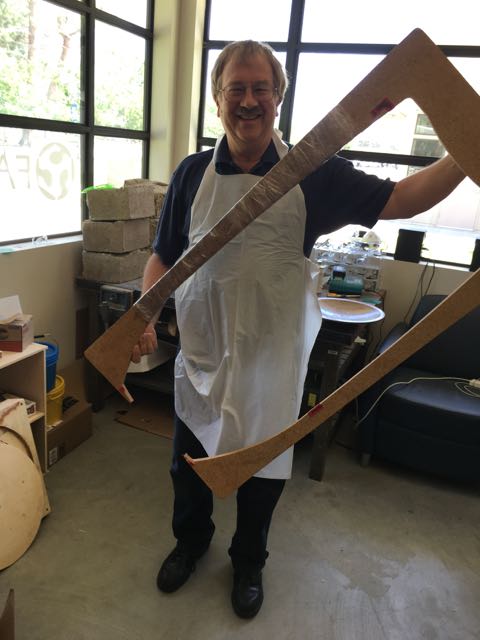
Week 14
Composites
The fourteenth assignment is to design and make a 3D mold (~ft2), and produce a fiber composite part in it.
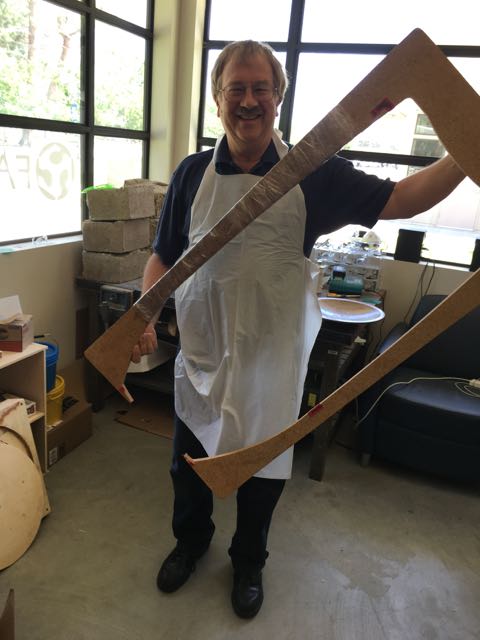
I am holding the scrap of a boogie board one of my students made. I want to make a teaching model of how strong and light a composite material can be. The boogie board blank is alread a composite of cork and nylon fabric. It is very light, and flexable. I want practice with coating a board and I also want to consider making our FRC robot out of composites. This example will show students how light and strong a composite robot frame could be. It will also give me practice on working with composites.
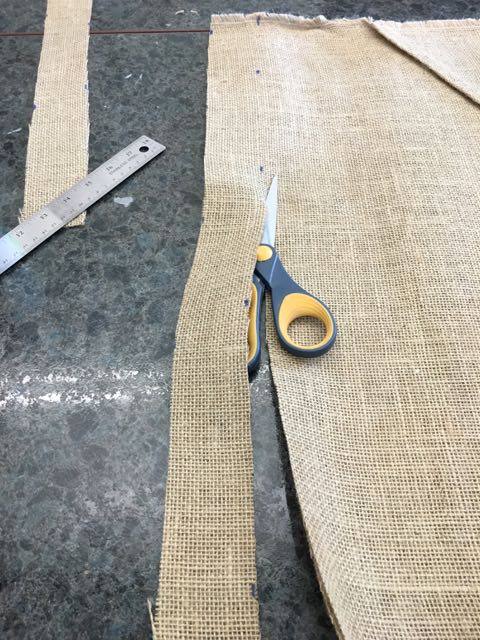
I cut the burlap into 2 inch strips.
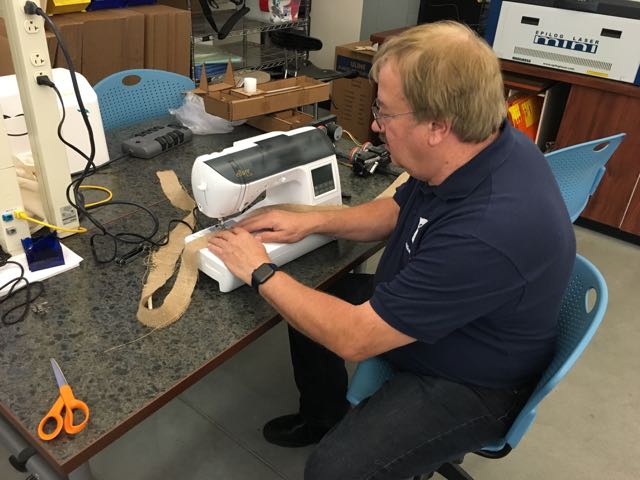
I sewed the strips together.
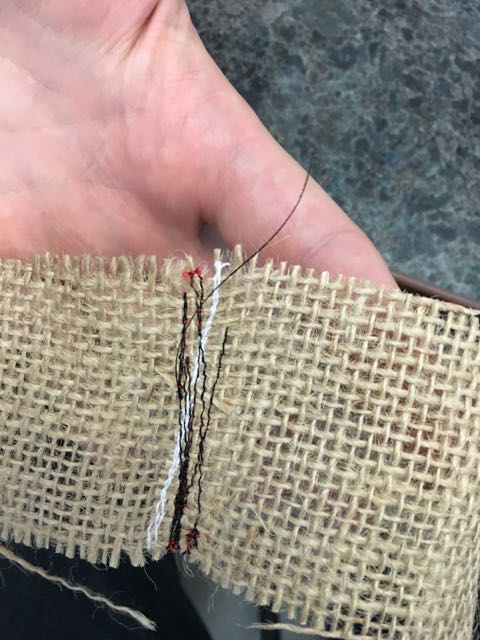
Sewed strips
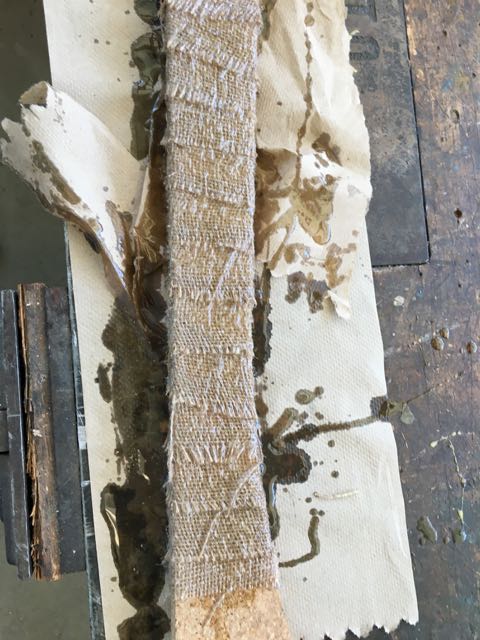
I used a flat piece of plastic to press the resin into the burlap. Messy process.
Prior to coating with resin, I wrapped the burlap strips around the target material. By staggering the wrapping, similar to wrapping a spained ankle, I achived mulitple (two to three layers) of burlap.
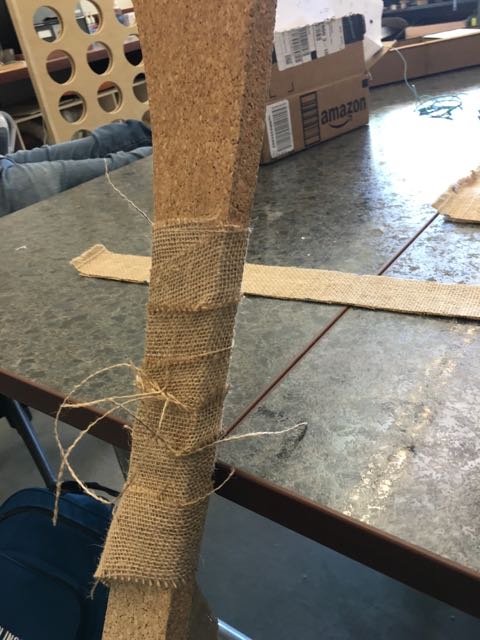
I wrapped the stiched burlap around the boogie board material.
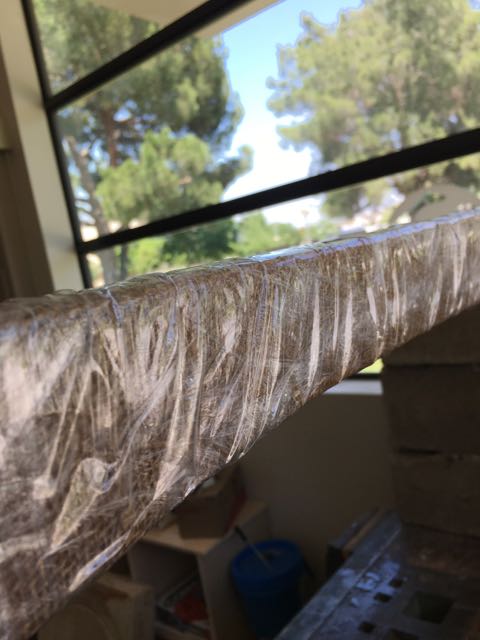
Since vacuum bags large enough were not available in our lab, I wrapped the burlap in plastic food film with a chemical coating that should keep the plastic from sticking to the resin. I then wrapped it tight with wrapping plastic to apply pressure to the resin and hopefully achive deep fusion into the burlap and cork. Hopefully it ends up with a surface that would be smooth enough to work with for making a FRC robot drive train or super structure. This process has a similar effect as a vacuum bag or a pressurized injection mould in terms of limiting bubbles and getting the compaction necessary to get the resin in all of the places you want it.
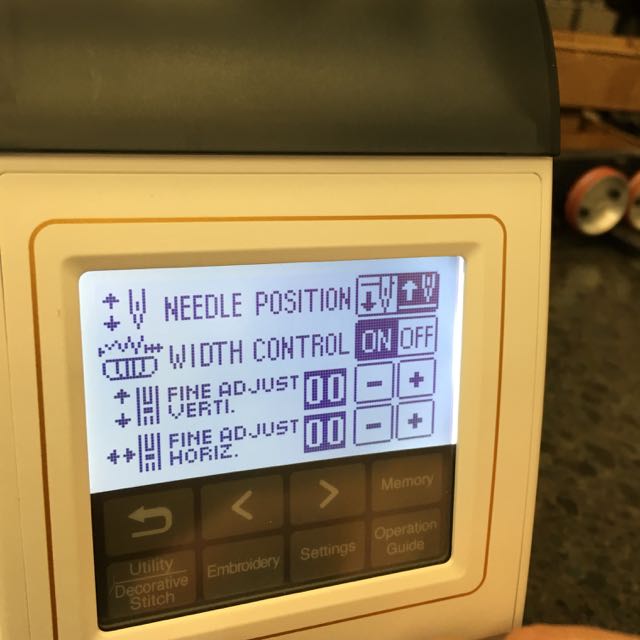
I was impressed with a new fablab tool. The digital CNC sewing machine. It moves the bed around based on the input. Very similar to a vinyl cutter or router. It can sew embroidered patches as well as work with embeded circuits in clothing.
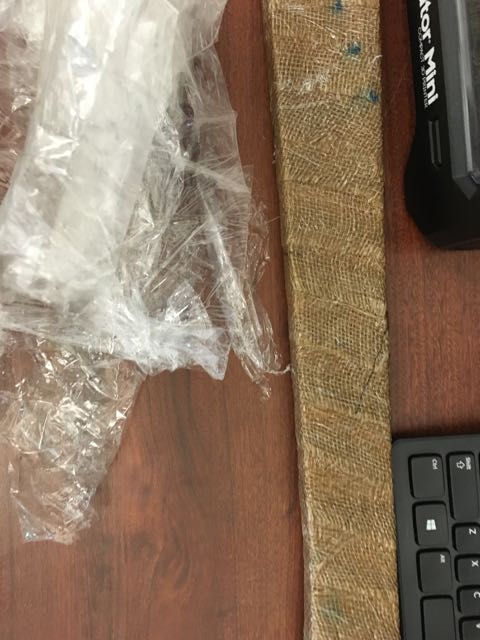
This is what it looks like after drying over night. It is very strong! Only a few layers. I can bend it, but very hard to do and it does not bend much at all. I am not able to twist it at all. Prior to adding the composite I could twist it 180 degrees. If I added more layers, I seriously doubt that it would bend more than our currentl 6061 eighth inch walled aluminum rectangular tubing. Technically I did not make a mould, but the issues of getting the air bubbles out of the resin in the form and getting deep resin infusion in the burlap would be very similar. I look forward to getting the proper vacuum equipment to fabricate larger scale forms and moulds using composite materials that could be used in our FRC robotics program.
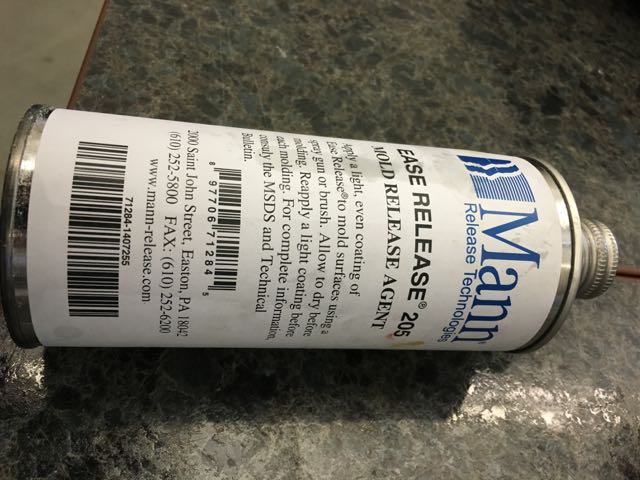
This is the solution I smeared on the plastic wrap prior to wrapping. It keeps the plastic wrap from sticking to the resin. It would also be good to put in a mould so that it would be easily removed. It worked well. I had to scrape, clean a few spots...but overall..it worked well.