Mechanical Design, Machine Design
The assignment to this lesson was to design a machine (mechanism+automation), including the end effector build the passive parts and to operate it manually. My team members were Ernest Kimani and Felicity Mecha.
We worked on fabricating a desktop sized milling machine whose structure was made of acrylic material and some 3D printed parts
My Contribution
3D Designing
My personal duty was first, to make the 3D model of the machine. I downloaded and used the Gear template generator program to easily specify and design the necessary dimensions for the rack and pinion. I then uploaded the file to corel draw for editing and eventually exported a dxf file for use on SolidWorks while 3D modeling.
The design was good but we decided to make a bigger one than the initial size. So I edited the model and increased the measurements.
Programming
To begin with, I tested the Pololu - A4988 stepper motor drivers that we were going to use together with the motors.I applied 12volts to the RAMPS 1.4
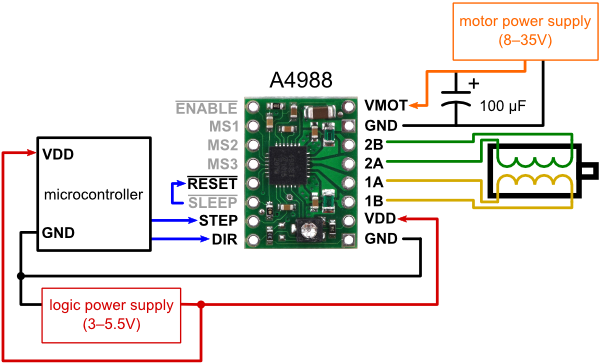
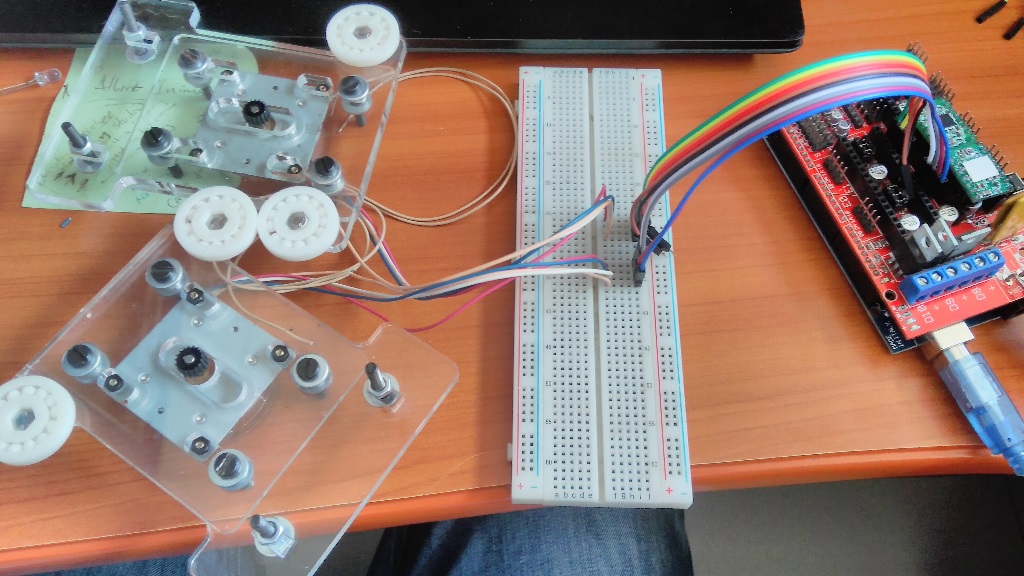
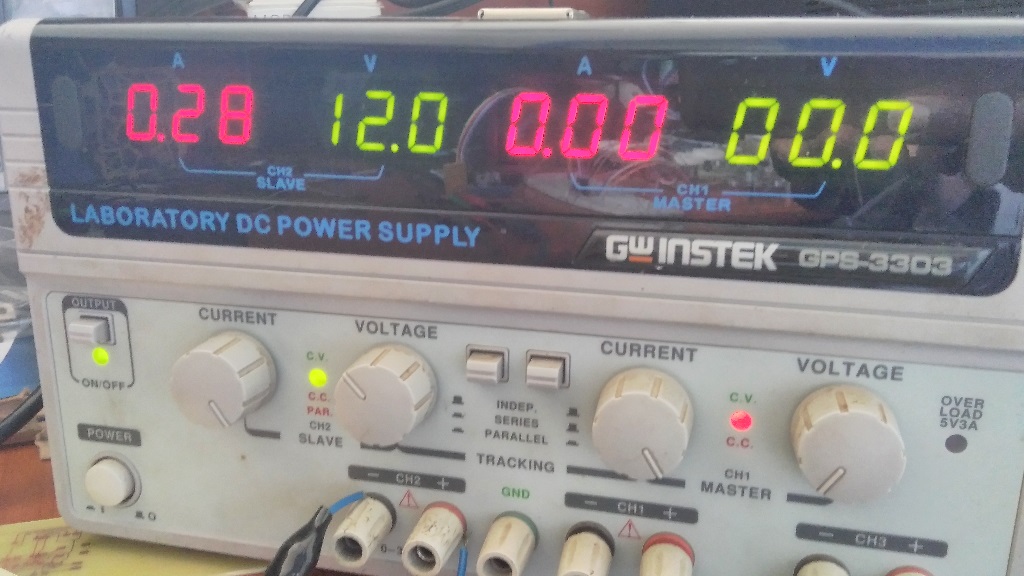
I used the test code from reprap wiki page and everything ran well.
Research
I did some research to find an efficient way to command a machine, communicate to it as you get feedback through an interface.
For this project, I thought of employing a G-code interpreter right on the control board, and communicate to it through serial interface.
Marlin Firmware is a beautiful open saurce firmware done especially for 3D printers. I went through it and atched afew videos to appreciate the impact of that platform.
Makelangelo software is also another open source code that provides a UI written in Java, which can be used to load images, process them and print them on the robot over a serial connection.
Eventually I found aG-code Interpreter by Marginally Clever. I edited this code and used it to communicate to the motors through the serial monitor.
Check out our group page for more information on this