Casting is a manufacturing process in which a liquid material is usually poured into a mold, which contains a hollow cavity of the desired shape, and then allowed to solidify. The solidified part is also known as a casting, which is ejected or broken out of the mold to complete the process. Casting materials are usually metals or various cold setting materials that cure after mixing two or more components together; examples are epoxy, concrete, plaster and clay. Casting is most often used for making complex shapes that would be otherwise difficult or uneconomical to make by other methods. Casting is a 6000-year-old process. The oldest surviving casting is a copper frog from 3200 BC.
To do list:
- Design a 3D mold, machine it, and cast parts from it
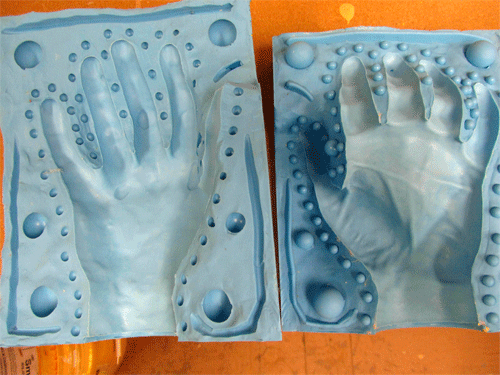
So while brainstorming on what to cast, I scoured through previous student projects to get my creative juice flowing. I stumbled across Ryan Dean's page. He created a moveable type for a letterpress. So I used that concept to create a Fab Academy stamp or movable type using the infamous RGB colored logo. Following along with Ryan's steps, I used Adobe Illustrator to re-work the logo. From there I created two separate inverted images to represent the different passes that the Roland milling machine will have to make.
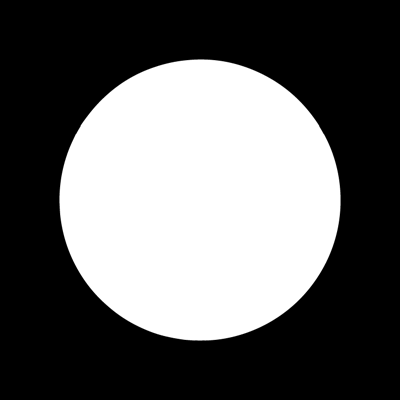
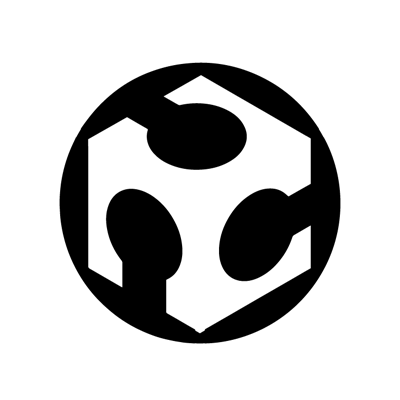
After my images was created, I uploaded them into fab modules to begin the milling process. To begin I used a 1/8 in end mill. However I must admit after this point, I became a little flustered. I was having difficulties figuring out the proper settings needed to achieve the end result I wanted. Ryan's reference assignment had used a previous older version of fab modules and I found it hard to follow. After some assistance for the instructor, I explored the use of grayscale. Fab modules reads grayscale to determine depth and intensity. I found this method WAY easier and understable. SO after I literally went back to the drawing board I revised my image.
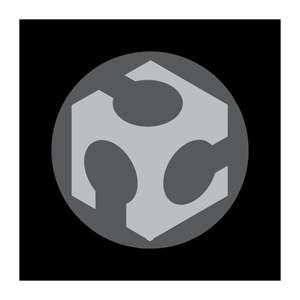
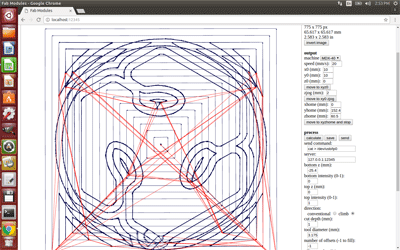
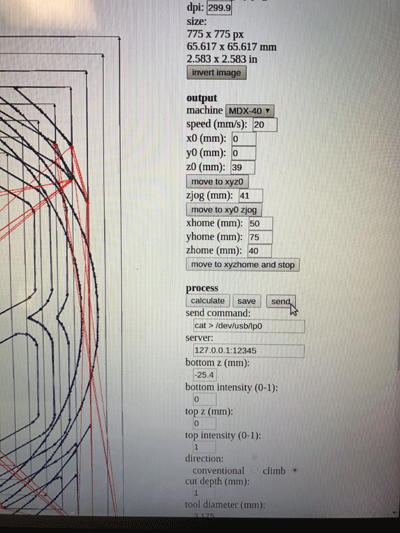
The milling process was successful. However, due to rushing, I TOTALLY forgot to run the "finish cut" process. I will update and document my mold with a finished cut later.
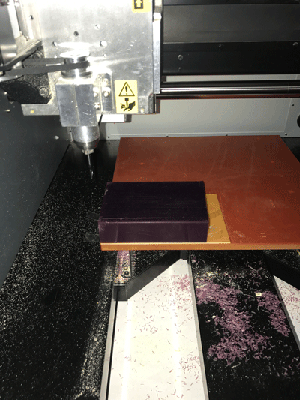
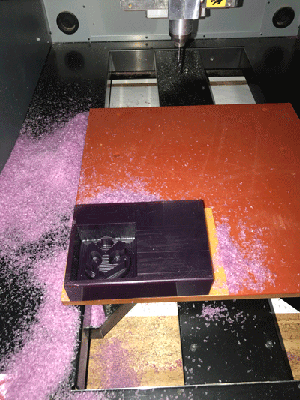
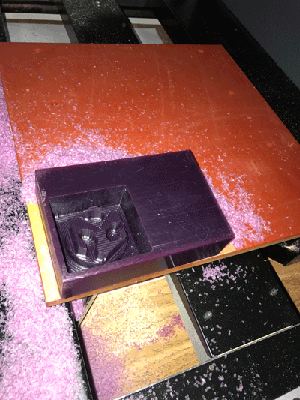
I decided to use Sorta Clear for the wax mold. I was reminded by the Fab Lab Tech to mix the solution evenly and carefully. Sorta Clear requires you to mix the two mixtures at a ration of 1:1. Once mixed, it is highly recommended to stir adequately to avoid dreaded air bubbles. After mixed and stirred I carefully poured into my mold and set it to solidfy. I WILL UPDATED WITH CONTENT once Sorta Clear has been solidified and I pour in the casting material. I will use Hydro-Stone.
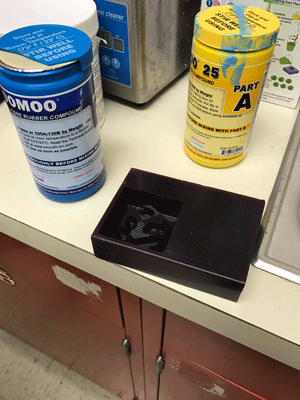
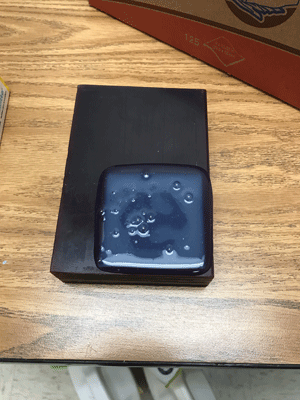
Things to remember:
- Run "finish cut" process after rough cut.
- Mix solutions according to recommended ratio on bottle.
- Avoid air bubbles and stir properly
- Using grayscale will determine depth in fab modules
Problems I ran to:
- Our Fab Lab was disconnected from the original lecture and had to watch the recording at later date.
- I was working with a slight learning curve and ran out of time. I will update once casted and formed.
- Molding material is messy.