MOLDING AND CASTING
Molding or moulding is the process of manufacturing by shaping liquid or pliable raw material using a rigid frame called a mold or matrix. This itself may have been made using a pattern or model of the final object.A mold or mould is a hollowed-out block that is filled with a liquid or pliable material like plastic, glass, metal, or ceramic raw materials. The liquid hardens or sets inside the mold, adopting its shape. A mold is the counterpart to a cast. The very common bi-valve molding process uses two molds, one for each half of the object. Piece-molding uses a number of different molds, each creating a section of a complicated object. This is generally only used for larger and more valuable objects.
Casting is a manufacturing process in which a liquid material is usually poured into a mold, which contains a hollow cavity of the desired shape, and then allowed to solidify. The solidified part is also known as a casting, which is ejected or broken out of the mold to complete the process. Casting materials are usually metals or various cold setting materials that cure after mixing two or more components together; examples are epoxy, concrete, plaster and clay. Casting is most often used for making complex shapes that would be otherwise difficult or uneconomical to make by other methods.
I learned the basics of molding casting process from Luciano during my prefab training. He gave us an insight to various aspects to be taken care of such as the angle to be maintained in the outer walls, kind of materials we can use, the soft to hard and hard to soft potocol followed in selecting the materials etc..
I wanted to make a mould for a SMART PROBE . The mold design is done using Rhino..
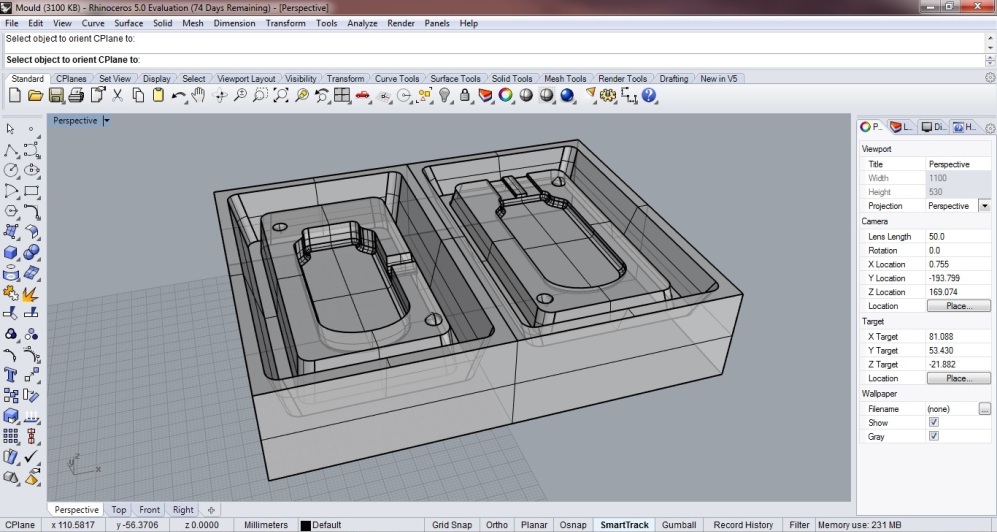
 
The wax milling is very much similar to that of milling a PCB so it was quite a easy job, but there are a few design considerations to be followed while using Wax for milling such as the clearence distance between the walls, angle to be kept on the mold design etc..
 
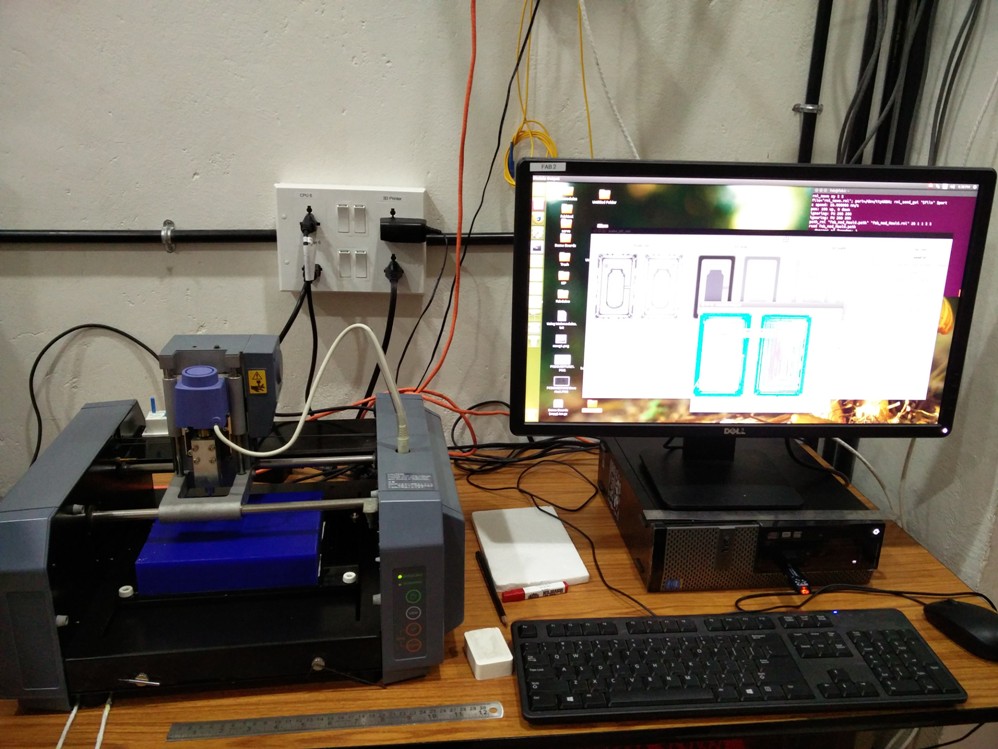
 
The wax milling consists of two processes,
As the name indicates roughing mills out the larger portions and finishing removes the fine unwanted areas.Appropriate bits are to used for each process.
The mold I wanted to mill required more than six hours of milling, Luciano suggested to keep the machine on through out the night. I left it to continue the process hoping that no power failuare will occour in between to spoil our good work..
 
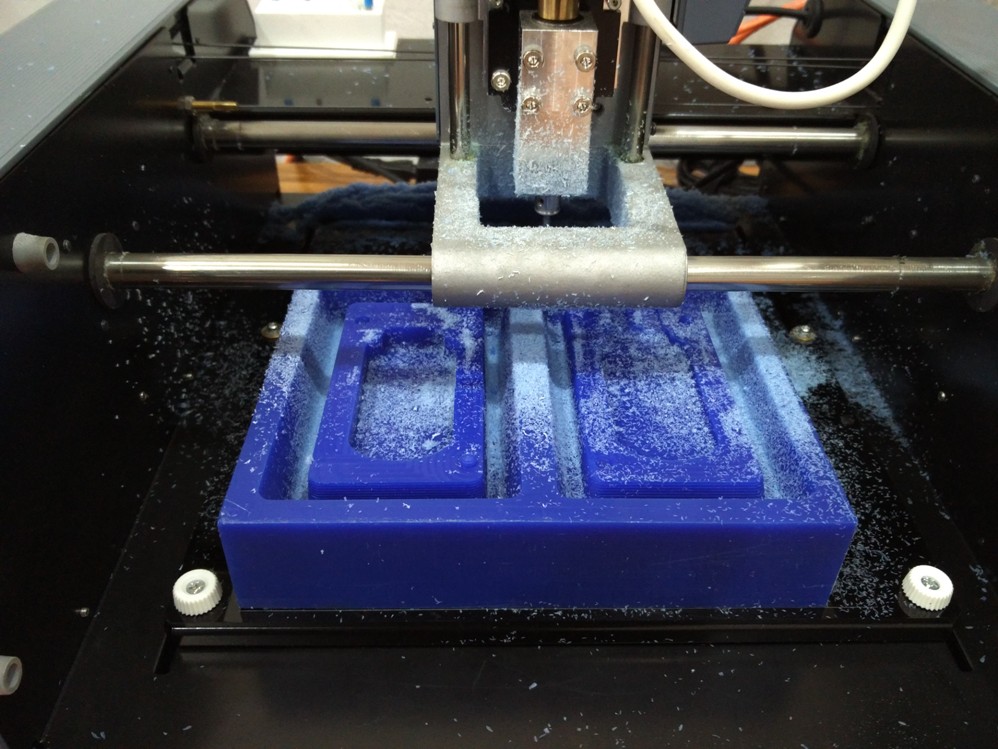
 
To my good fortune, there was no interruption in power supply during night and the mold was perfectly milled by the next day morning :)
 
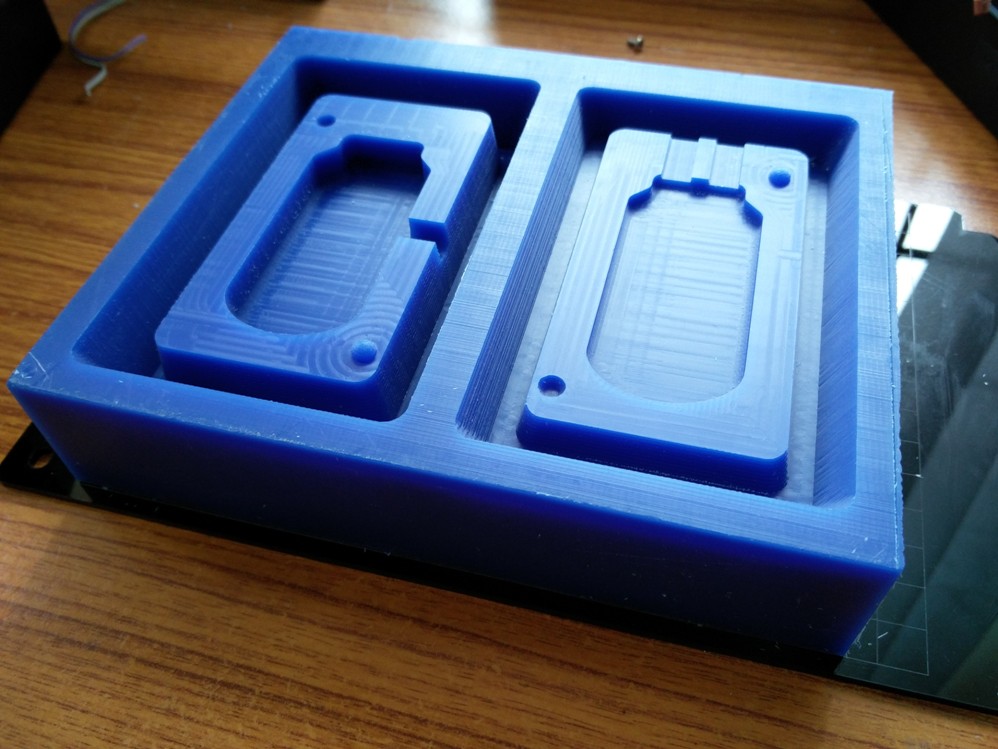
 
I used the SORTA Clear 37 Silicon rubber material for the outer mold.
 
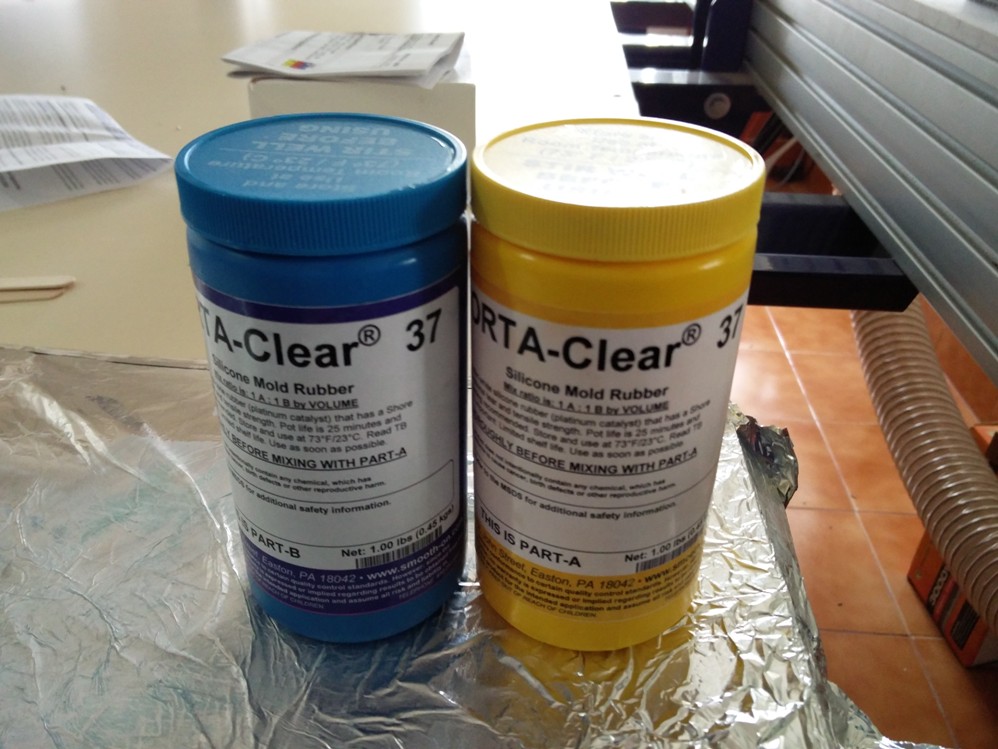
 
The material used for casting comes in two different enclosures and need to be mixed together in appropriate proportion for proper setting once it is poured in the mold. Depending upon the material used, there are two ways of doing this
Now it is time for me to try my luck with casting..
 
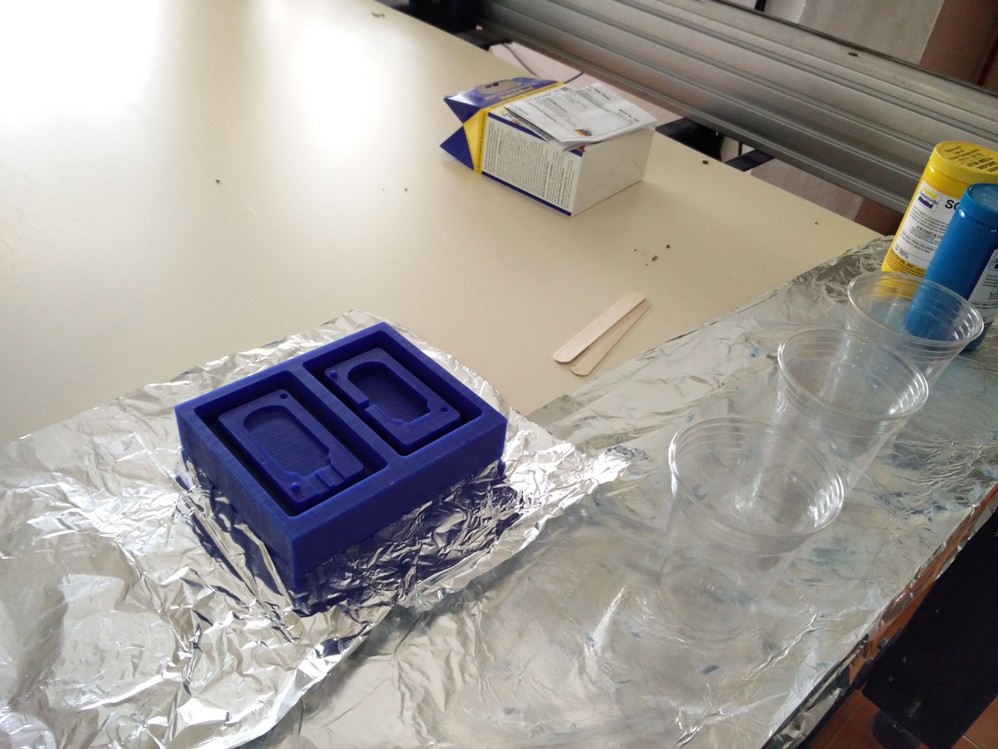
 
Next step is to to mix the A and B parts of the material of equal quantity,and after mixing it well.Care should be taken to minimize the air bubbles getting trapped. While pouring the silicon to the mold utmost care should be taken to see that no air pockets are formed in the corners. With utmost care fill the mould with the mixed silicon.
 
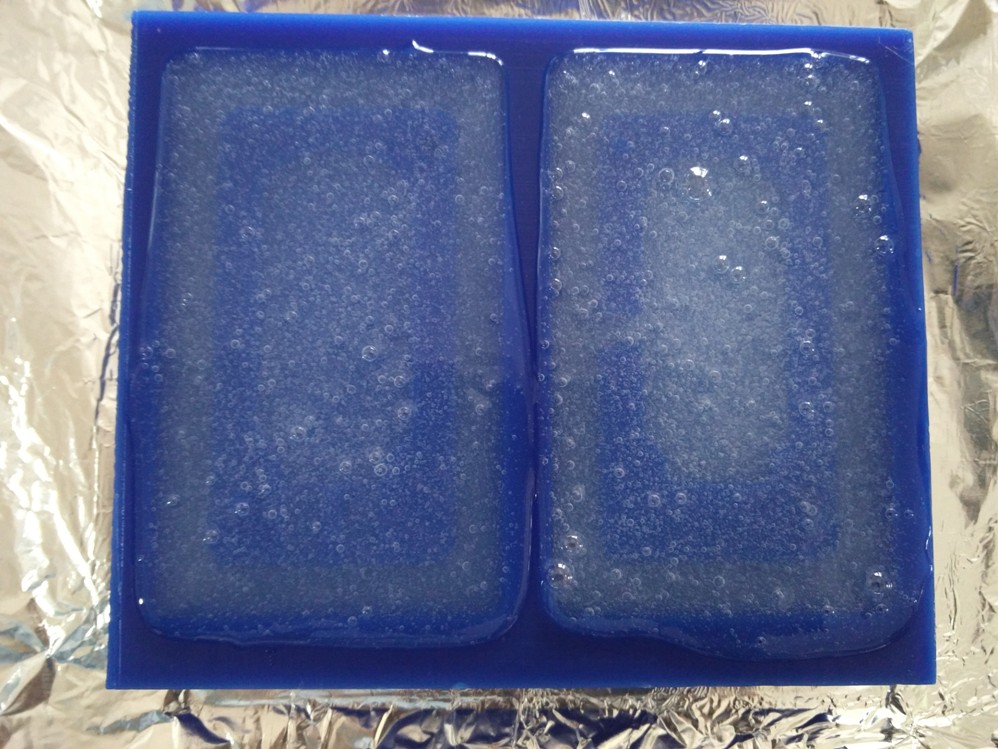
 
Though extreme care is taken, some amount of air will be traped as bubbles, this can be removed by gently tapping the mold horizontally with out distubing the silicon.
Once the curing time is over we can genlty remove the silicon mold from the wax as shown..
 
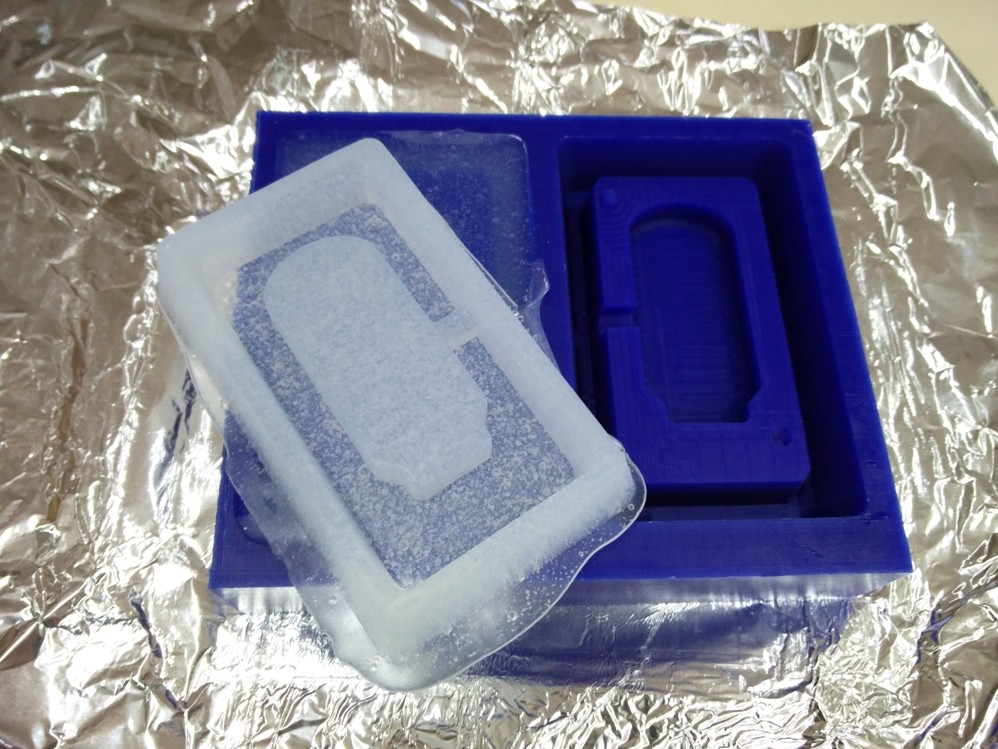
 
To my great joy, the mold seems to be perfect..
 
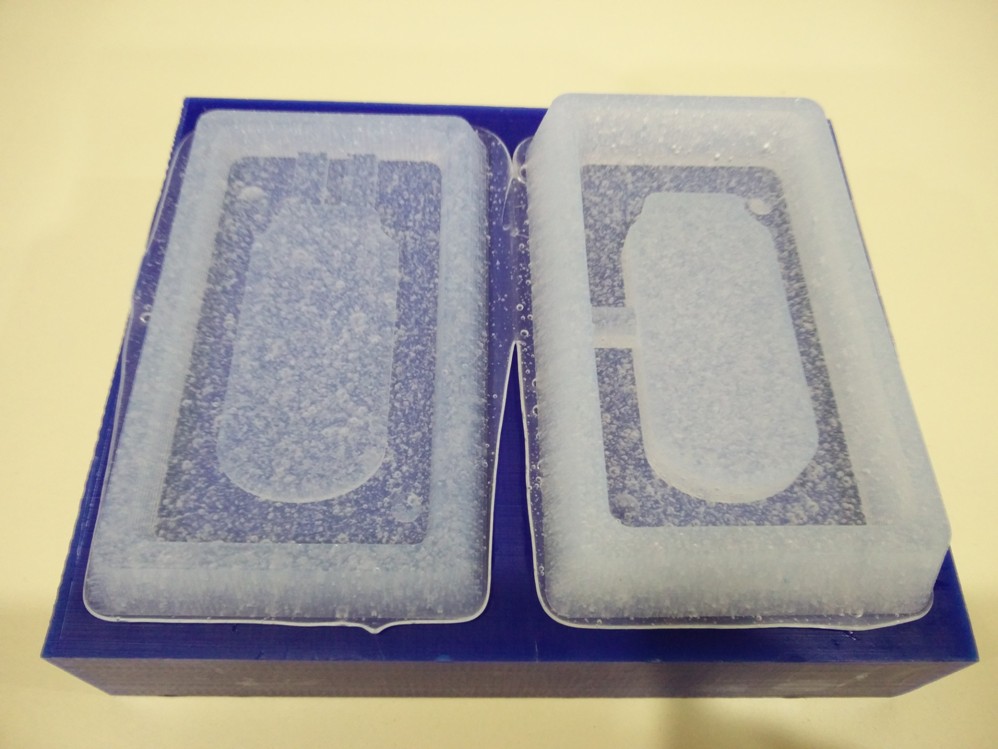
 
Now its time to make the Plastic mold using the newly molded silicon mold..
 
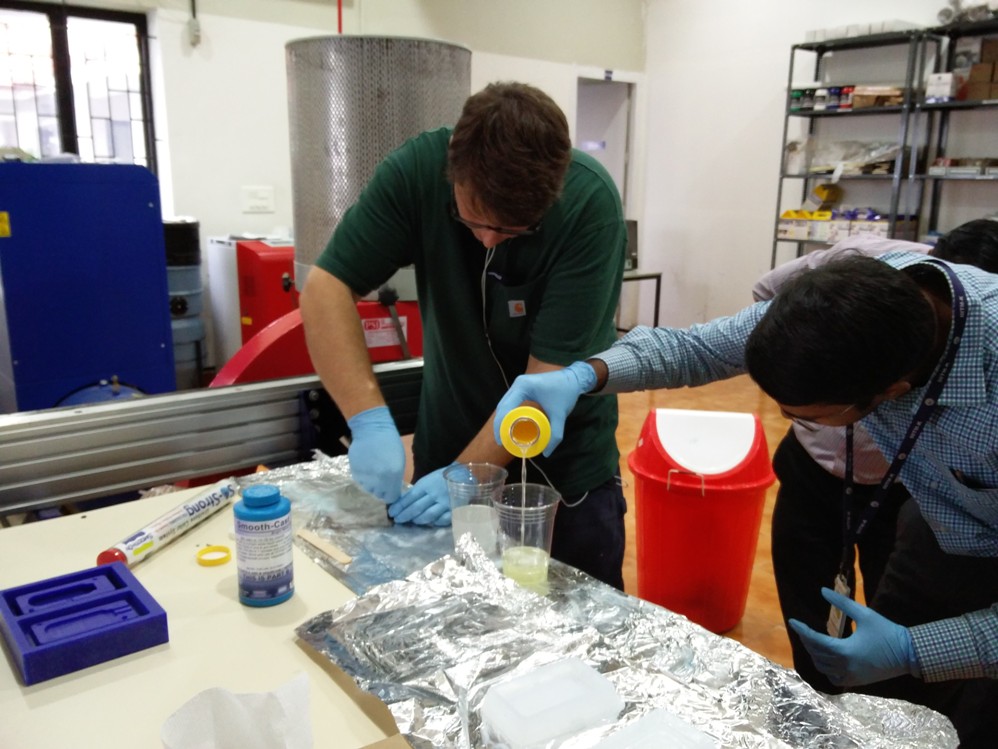
 
I used smooth cast 305 for this process. Here also the material comes in two parts which has to be mixed in proportion..
 
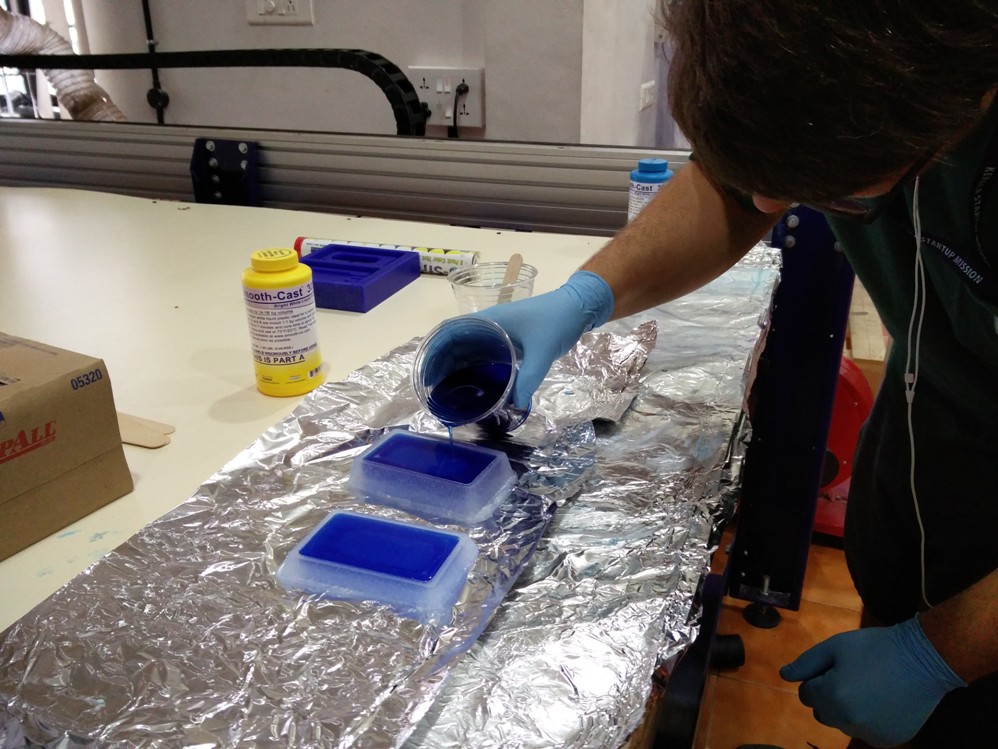
 
Here also the process to be followed is much the same but it has a extermly fast action compared to silicon.
 
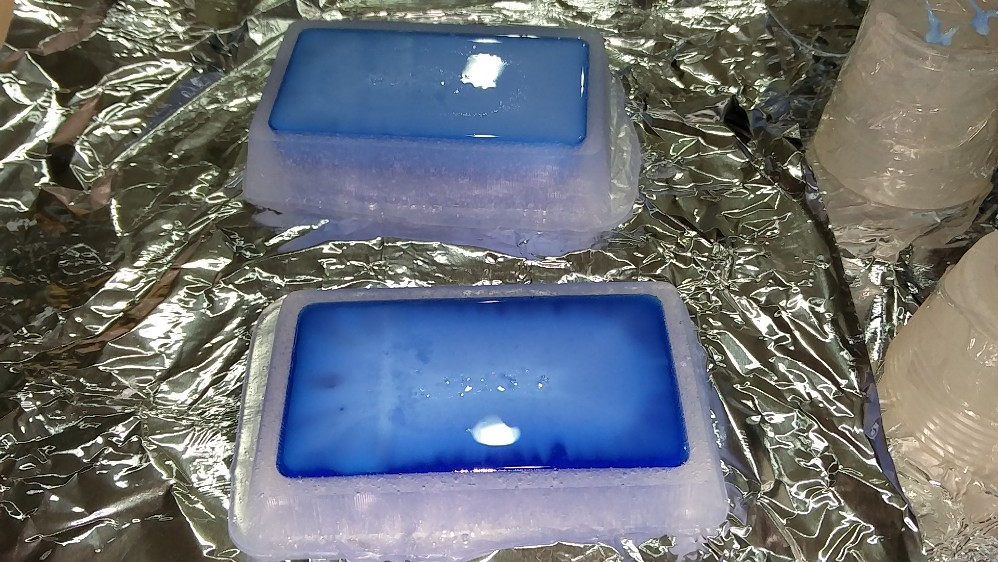
 
This material produces heat while settling down in the mold and hence extreme care has to be taken while using this.
 
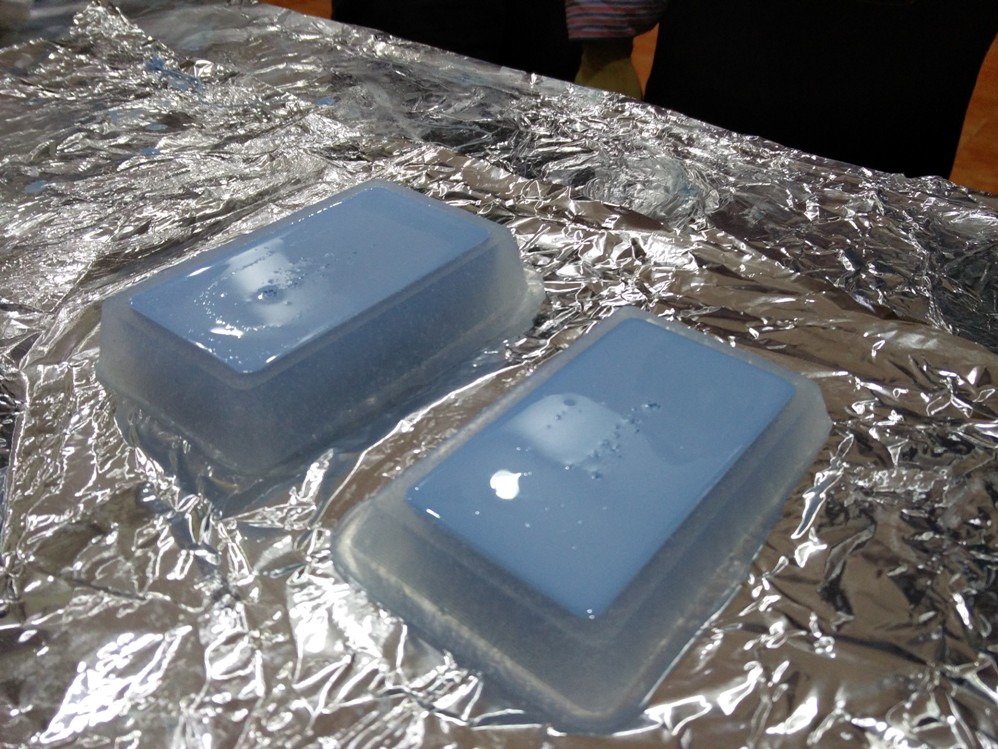
 
The mold became hard in less than half an hour and we are excited to see how it is..
 
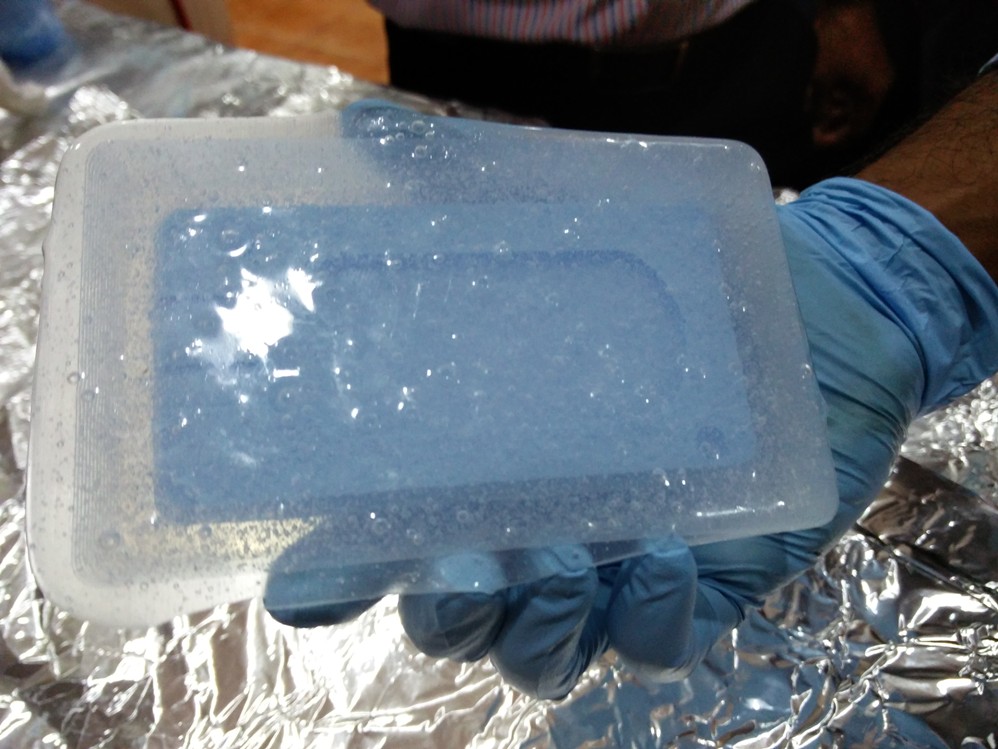
 
 
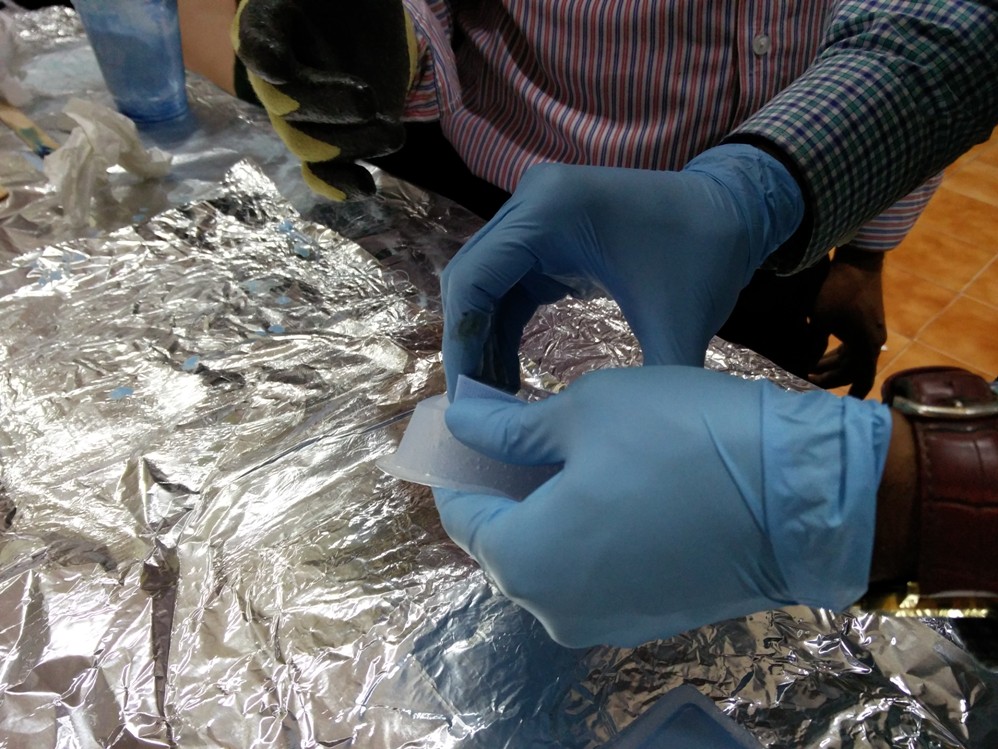
 
 
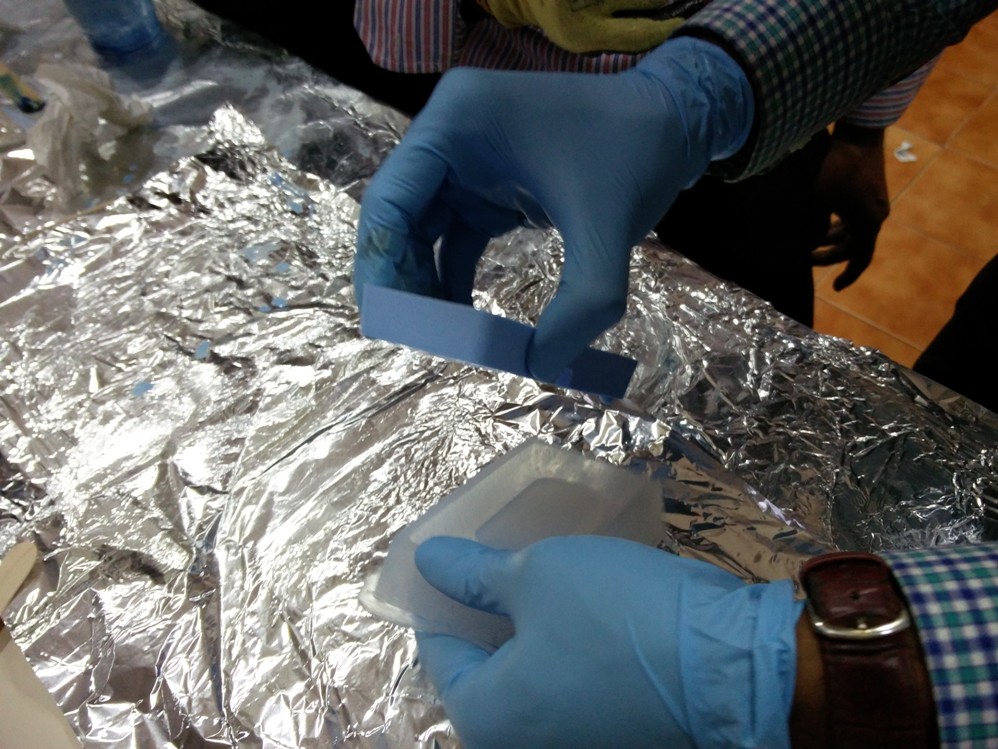
 
The mold seems to be perfect :) Thanks to luciano's guidence..
 
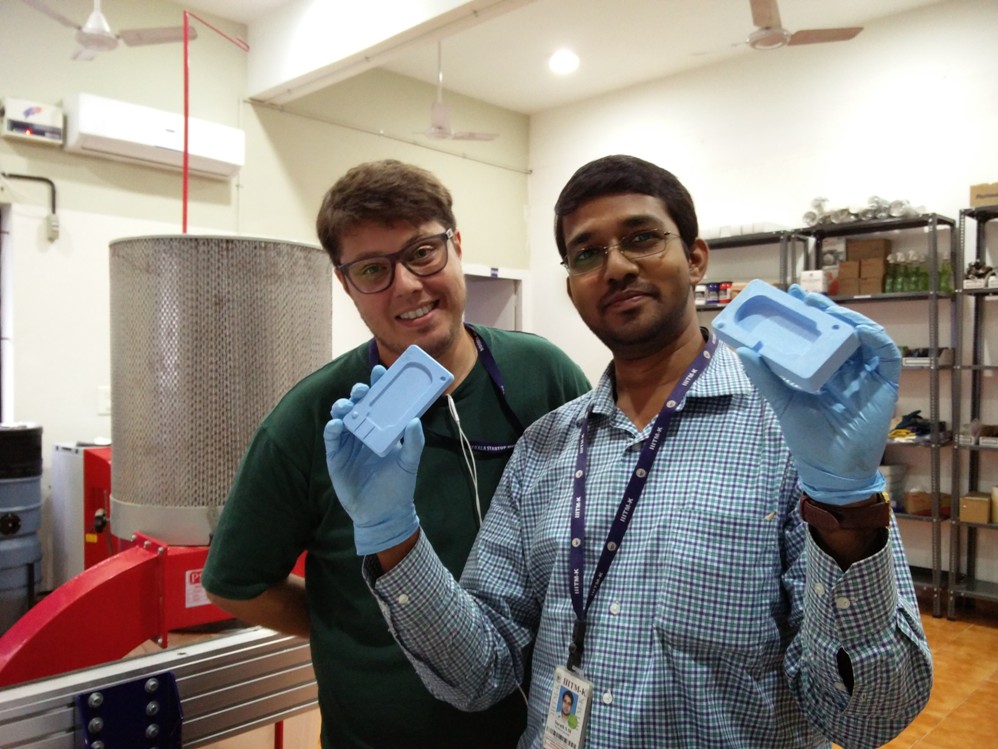
 
 
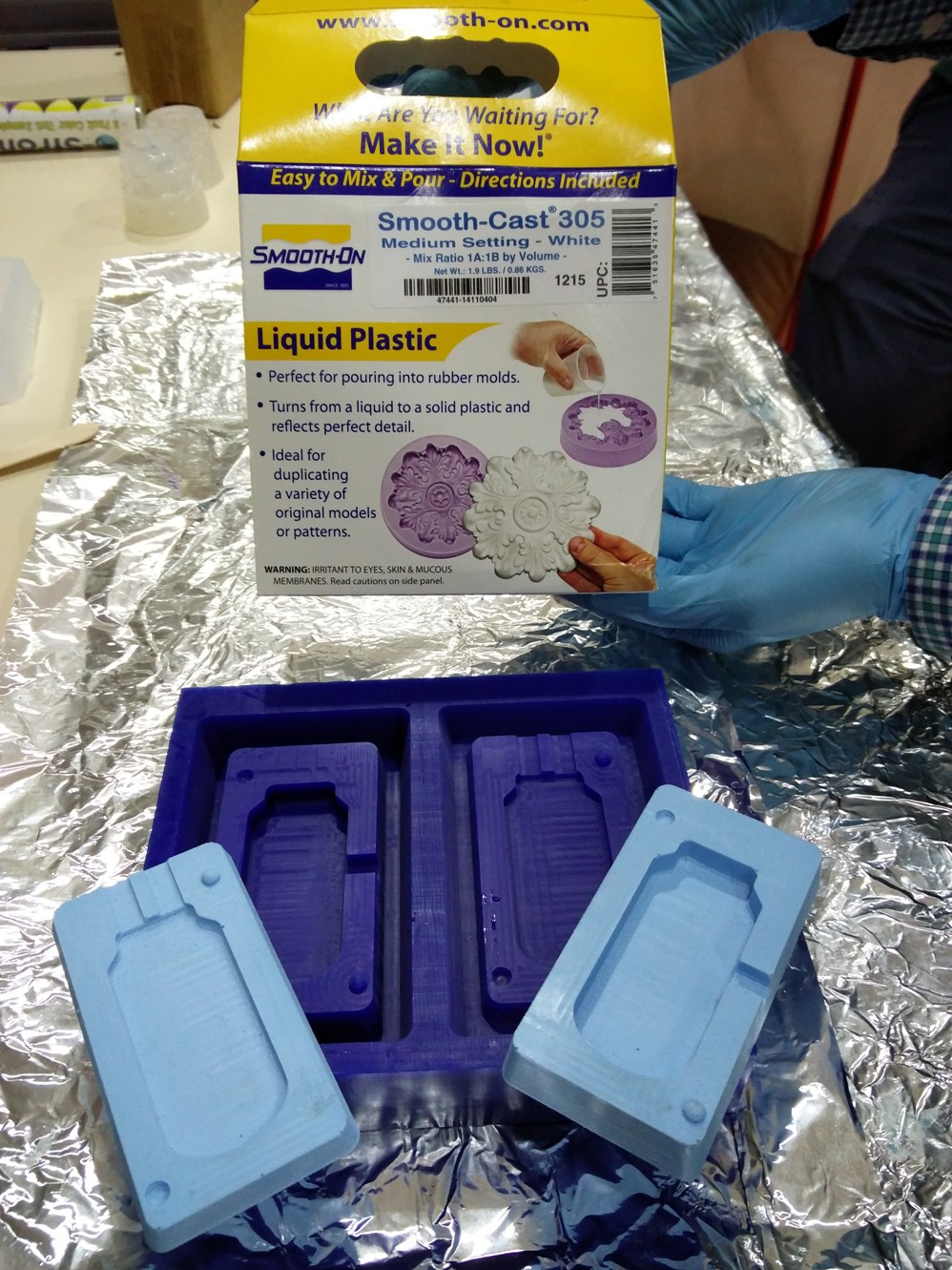
 
Now I am no novice to the casting process and was eager to fill our mold using silicon.. As the PCB for the SMARTPROBE I mentioned was not ready I decided to try with sticks..
 
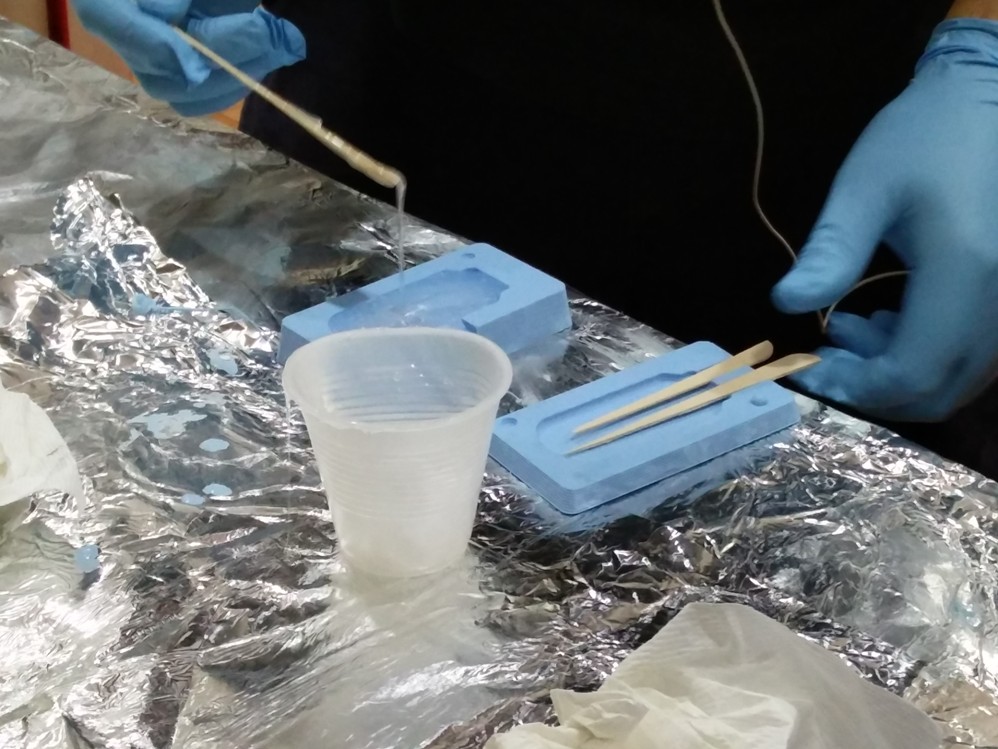
 
Since this is a two sided mold care should be taken to make sure that both molds press to eachother firmly..
I waited eagerly for the settling time to be over.. and now we are about to open...
 
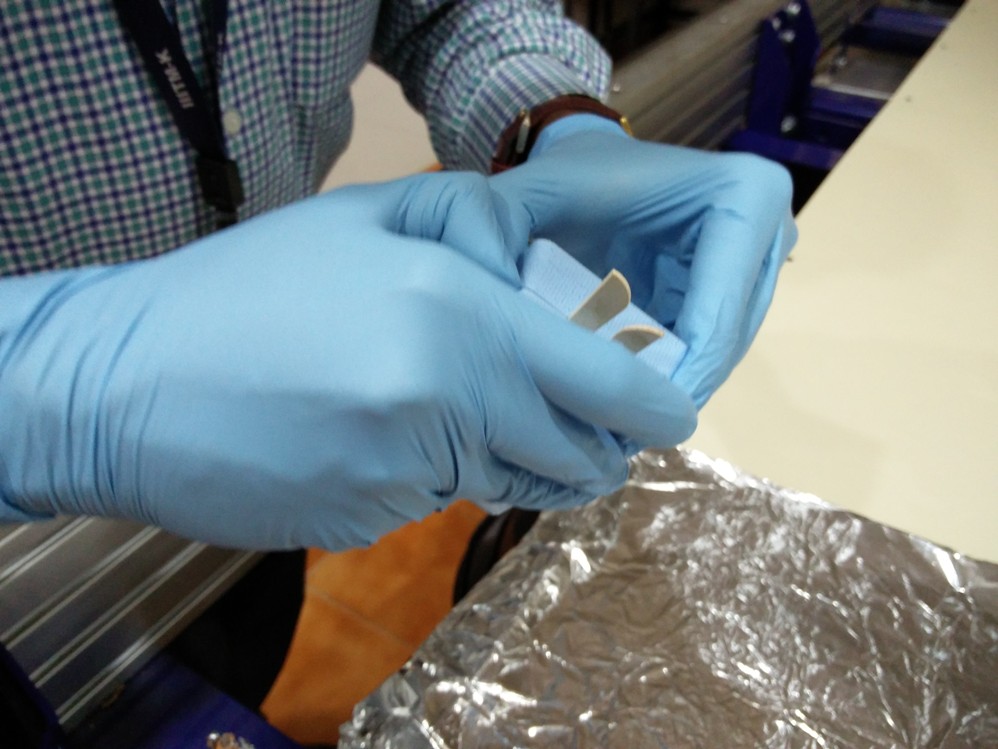
 
The mold looks perfect with the sticks embedded inside..
 
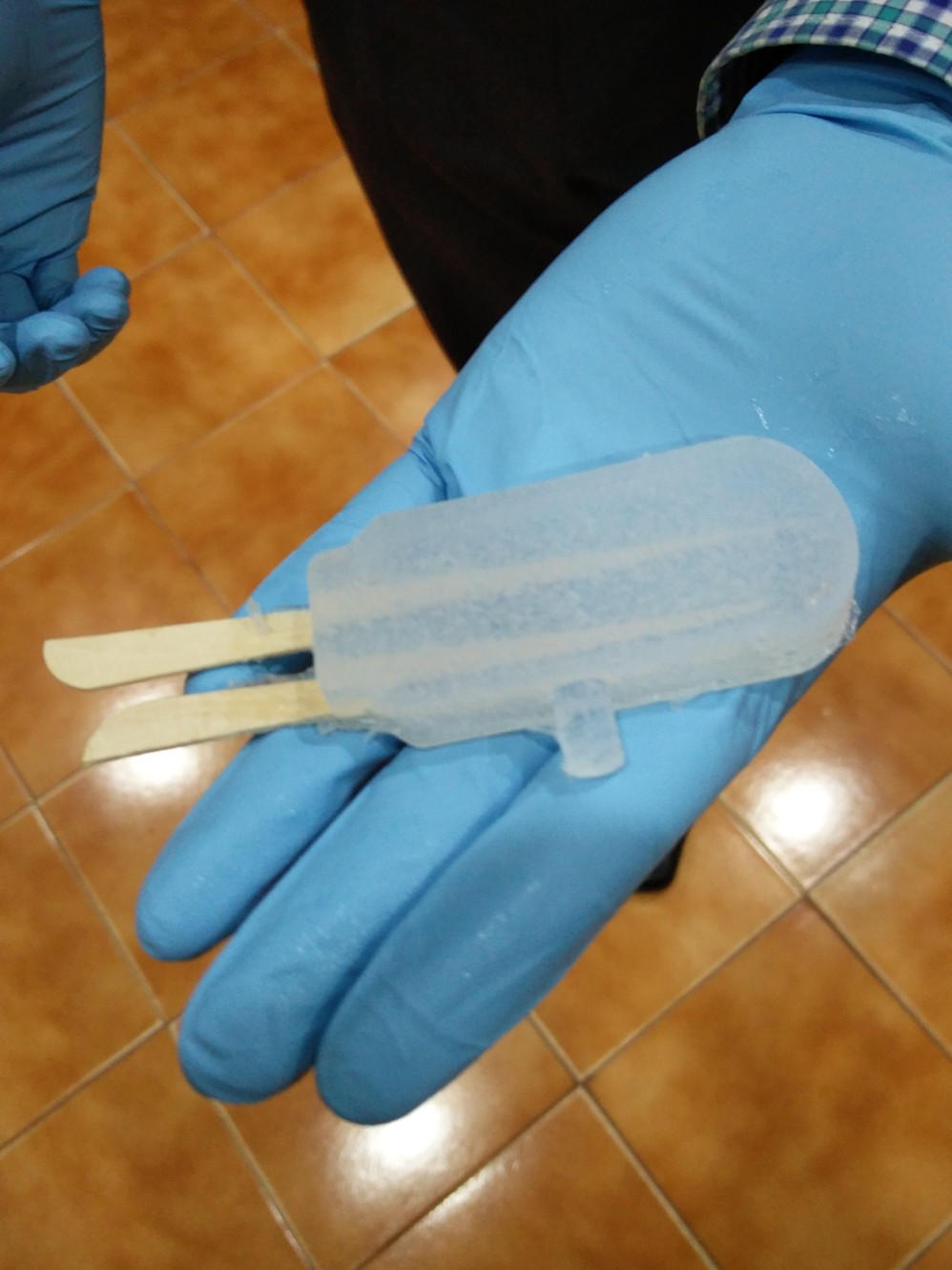
 
Well.. there the assignment ends , All the design files can be downloaded from here.
but real inspiration behind me in trying this is much more than the assignment, let me continue with the story behind this for those who may be interested to know more..
A HERO SHOT OF MY PROBE..
 
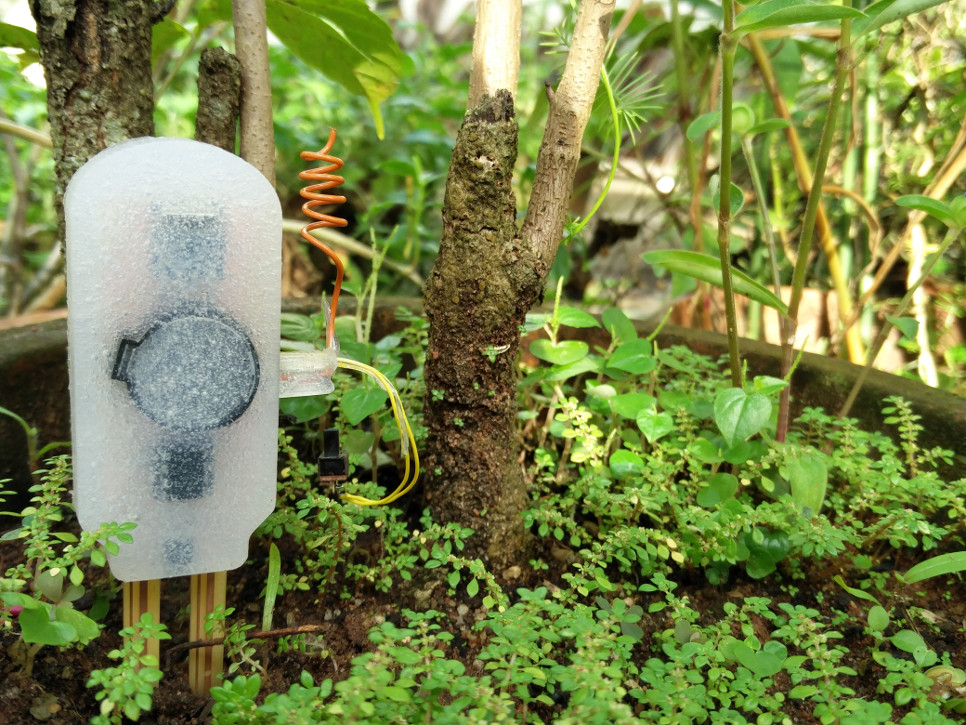
 
Now let me tell you the requirement behind this..Based on a real world requirement for an offical project I am working on, I wanted to design a SMART PROBE!!.. This is basically a low power microcontroller based battery driven wireless proble which will measure the parameters such as Humidity, Temperature , Soil Moisture etc and send this data to a central hub wirelessly. The hub is an improved version of my already developed Intelligent drip irrigation controller.Due to the limitation of time and components available, the first version presented here measures only the temperature and sends this data back to the hub wirelessly. Additional sensors for measuring humidity, moisture etc will be added in the upcoming versions.
Following is the picture of the Intelligent controller I designed earlier for your reference.
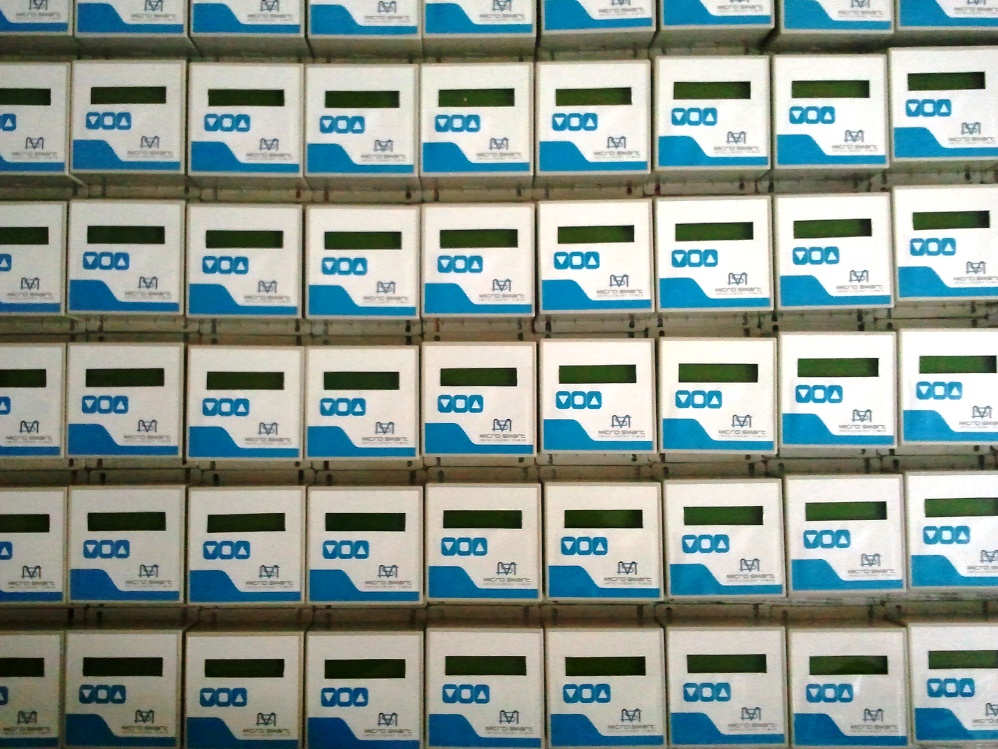
 
Processes Used in the SMART PROBE Development are,
It all started with a rough sketch in my notebook and collecting the correct dimensions as shown below..
 
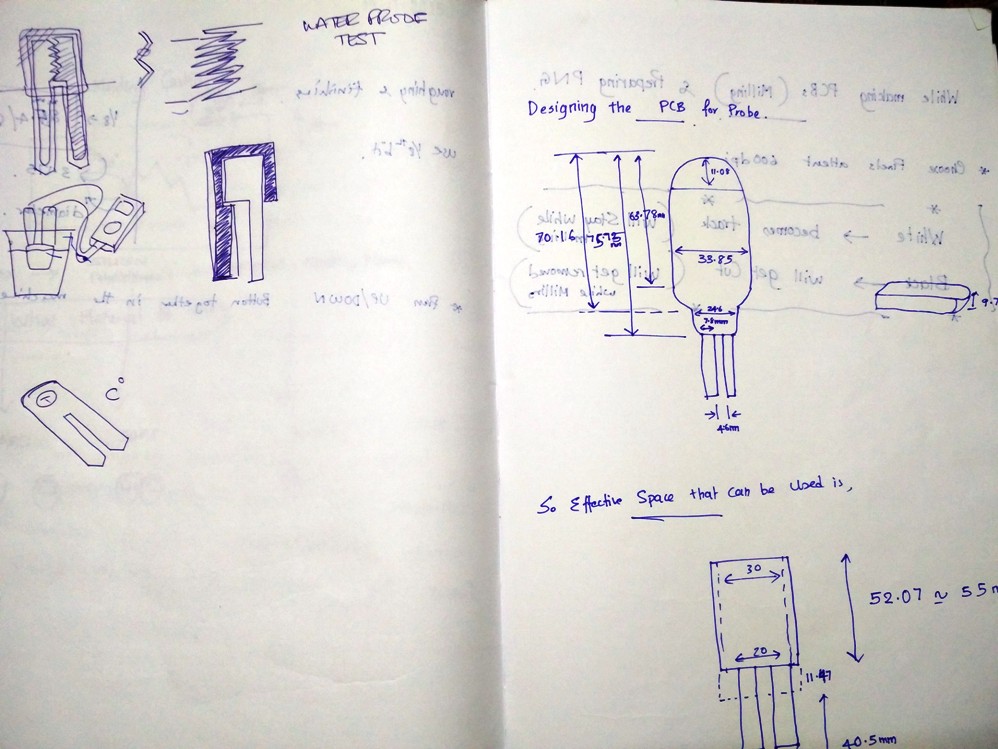
 
The schematic for the circuit is drwan using EAGLE.. and the PCB development process and circuit deisgn and programming will be documented in the respective week's pages.
This is a completly assembled probe, A closer look at the probe..
 
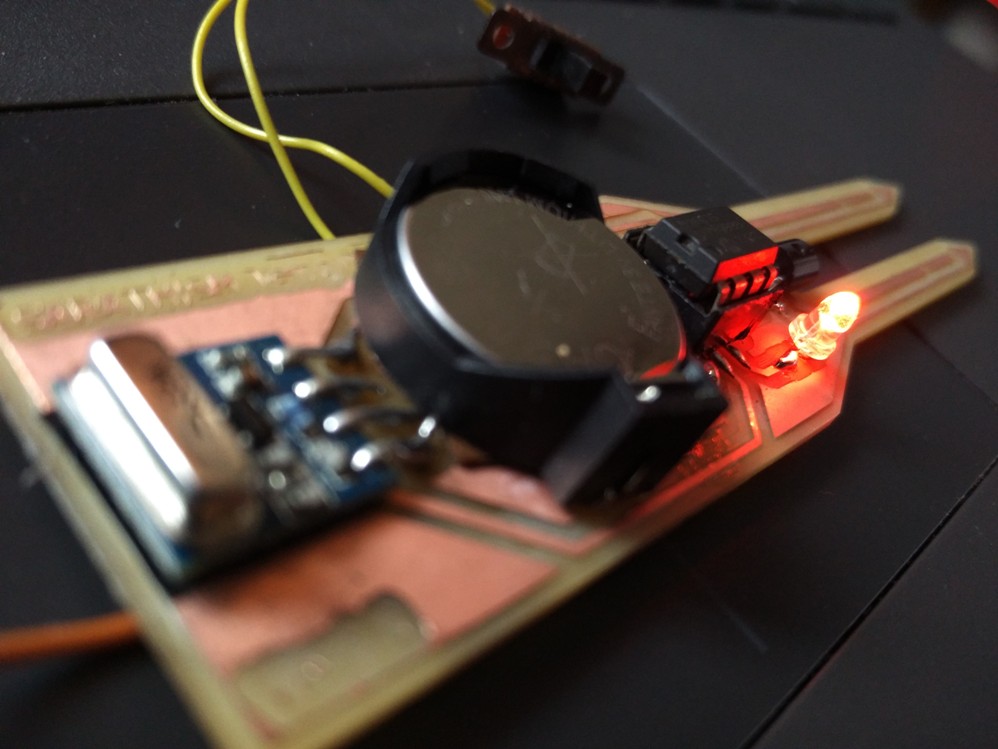
 
As no design for antenna is made in the PCB, I have used a small single strand wire for the time being to test the performance. I also missed to add a Switch in the initial design so two wires were taken out from the battery lead and a sliding swith was connected externally.
 
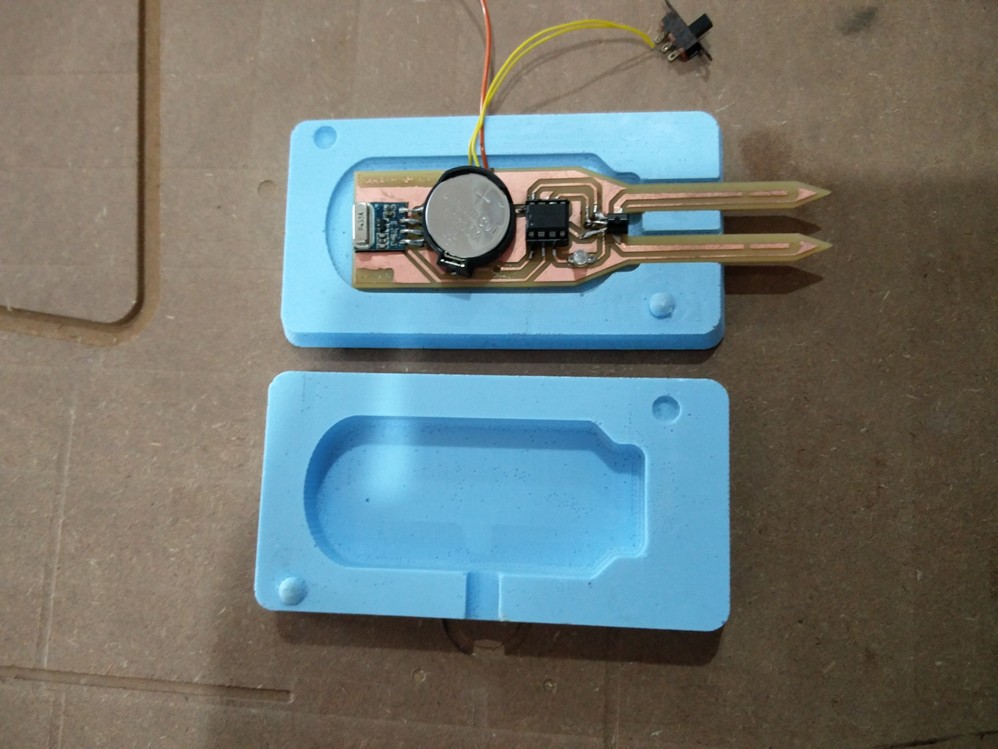
 
Now it is time to do the final casting process with the moulds that was made.. I prepared the silicon repeating the previously used process..
 
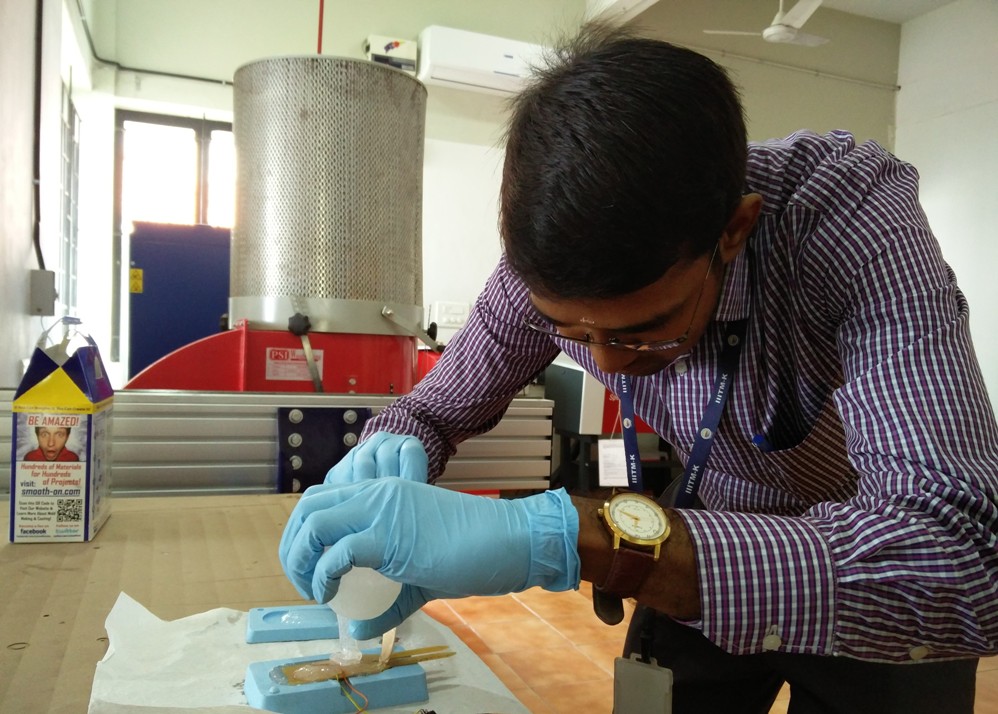
 
This time the calculation with quantity of material required was not perfect and a little amount of overflow of silicon through the sides can be seen while pressing the molds together
It was quater past twelve and I left it for curing while I take my break for lunch.
 
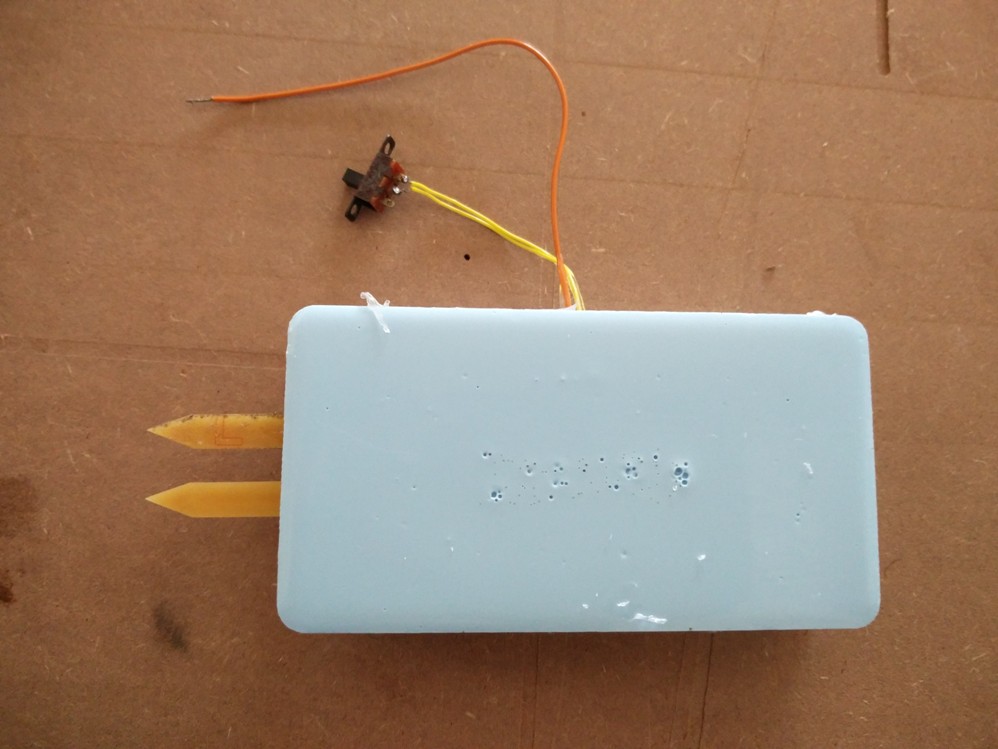
 
With lots of eagerness I opened the mold after the curing time.. well, it did not disappoint me.. The circuit has got fixed inside the silicon firmly..
 
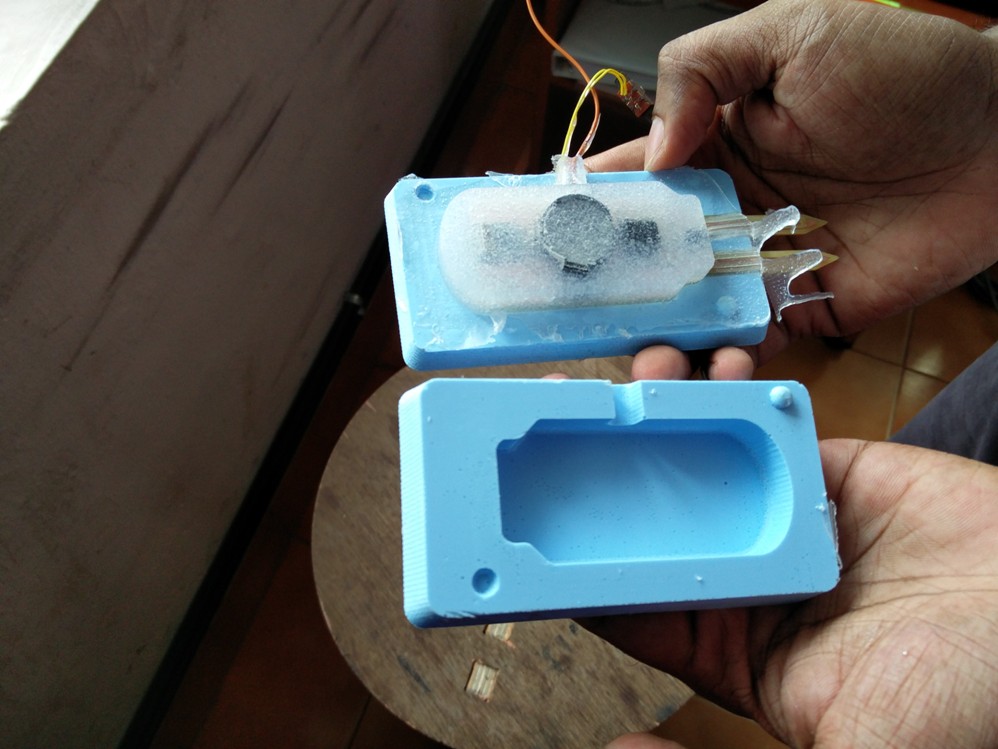
 
I slowly pulled the silicon mold out of the plastic mold.. it looks fine other than the little extra silicon attached to the sides due to overflow
 
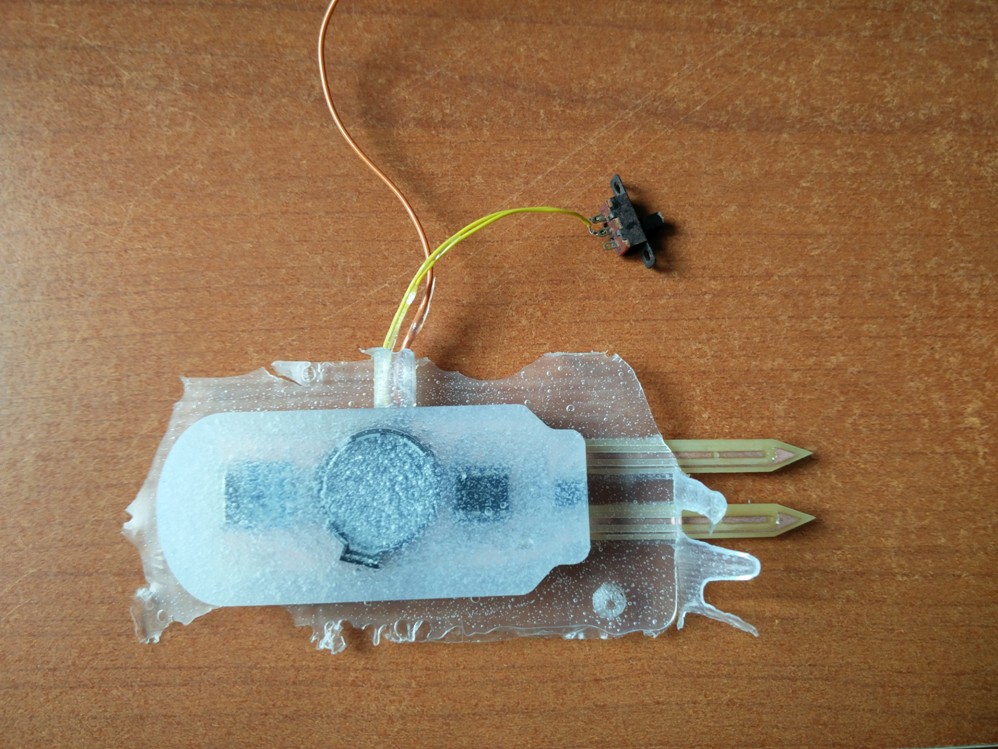
 
It was time for the ultimate test, I moved the sliding switch to the close position, but the LEDs which are supposed to light up once in five seconds did not light up, I tried to bend the silicon a little bit near the battery holder and to much of my relief, the controller started working, the LEDs are blinking now and it is trasnmitting data. Though I could not figureout exactly what caused the problem, the trick of bending it worked.
 
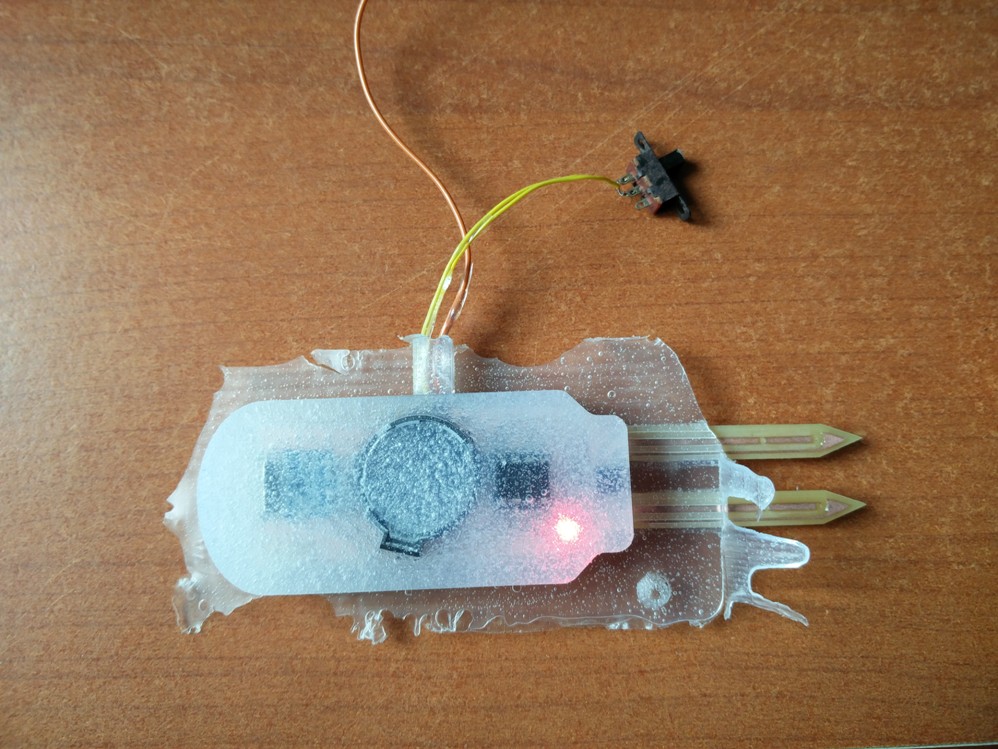
 
There was little bit of silicon sticking around its sides due to the overflow while casting, I removed it and now the probe looks just as what I intented to :-)
 
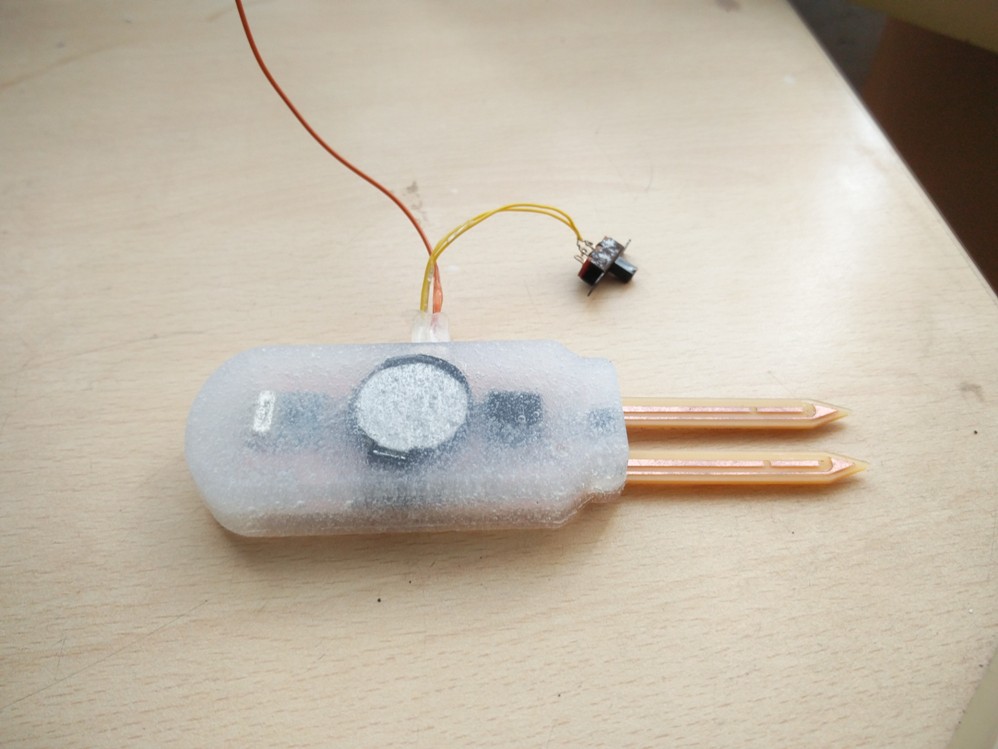
 
 
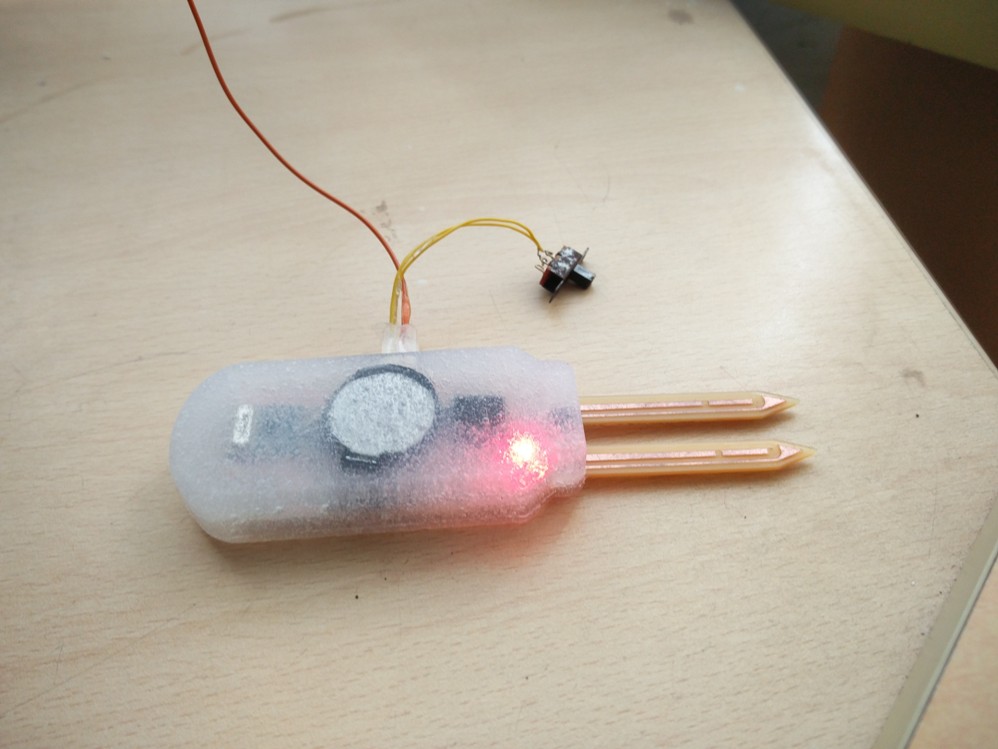
 
 
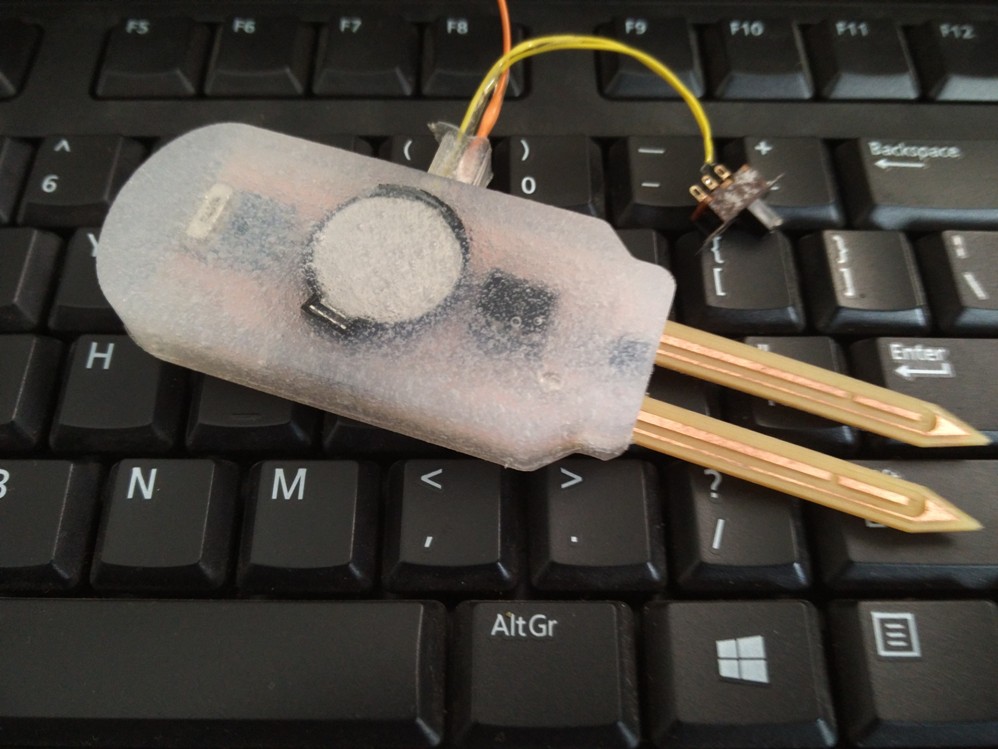
 
Your interest to go through my story is much appreciated :) Thank YOU!!