Assignment:
A. Test the 3D printer
B. Design and 3D print and object.
C. 3D scan an object (and optionally print it).
B. Design and 3D print and object.
C. 3D scan an object (and optionally print it).
A_Test the 3d printer.
Not completed.
B_Design and 3d print an object.
I first started reviewing the assignments and the respectiv documentation of the diferent projects I did last year for this assignment.
I was very new to rhino so instead of designing something from scratch I downloaded a model - a knuckle box - from the web and customized it.
I imported the stl file in Rhino and edited it to customize the size (length and thickness), exported it back to .stl ans used Cura to generate the G-code and set the print for a Ultimaker.
See the rhino process and command I used HERE
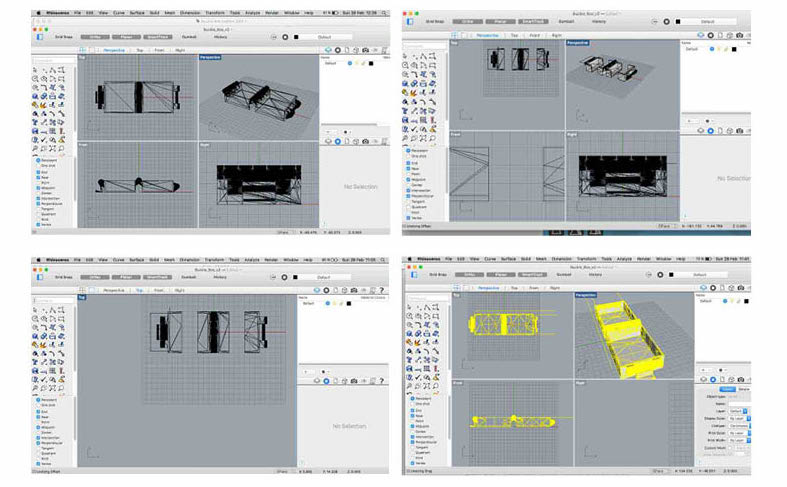
It was my first time with Cura so I used the preset for a low density print, threaded the filament in the machine and printed it. Once the G-code is generated with Cura the print can be launched from the printer's menu.
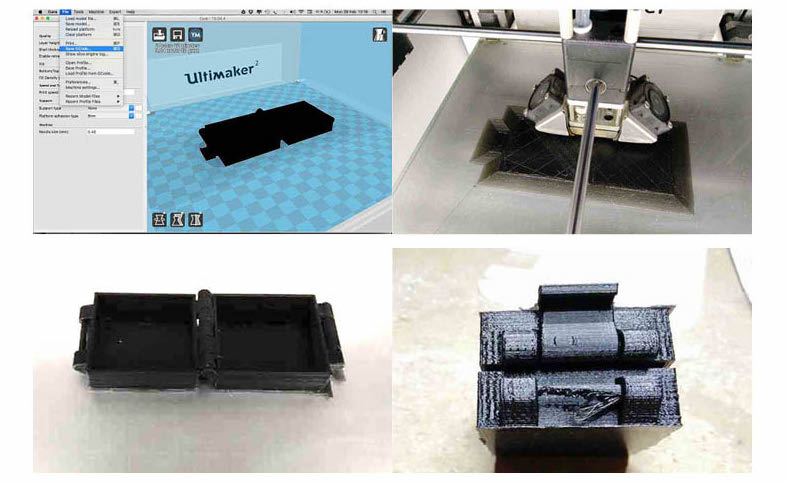
The print went pretty well except for the thin part of the "knuckle" where the material dripped a little bit. But the hinges worked well.A low temperature would have make a better job on those part where the material has no and cannot have any support.
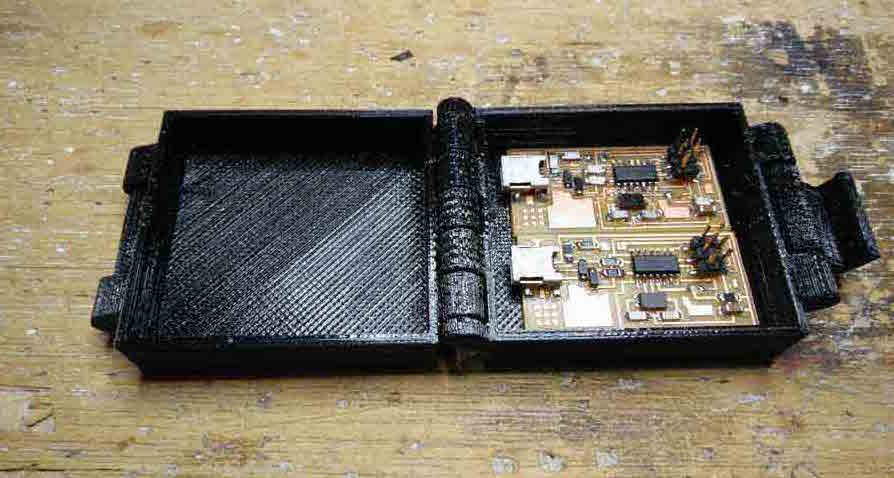
After I designed a front beam casing and the cap of a bike head-light (related to my last year's final project) from scratch in Rhino, sliced the stl file and generated the gcode in Cura, and printed it on the Ultimaker - again using presets.
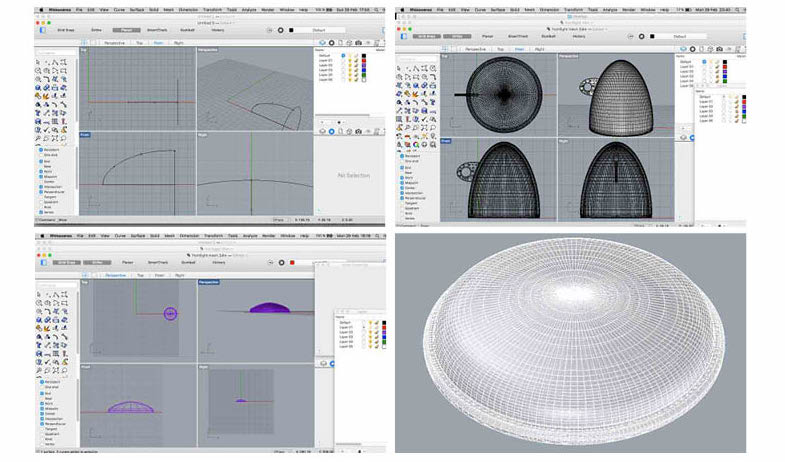
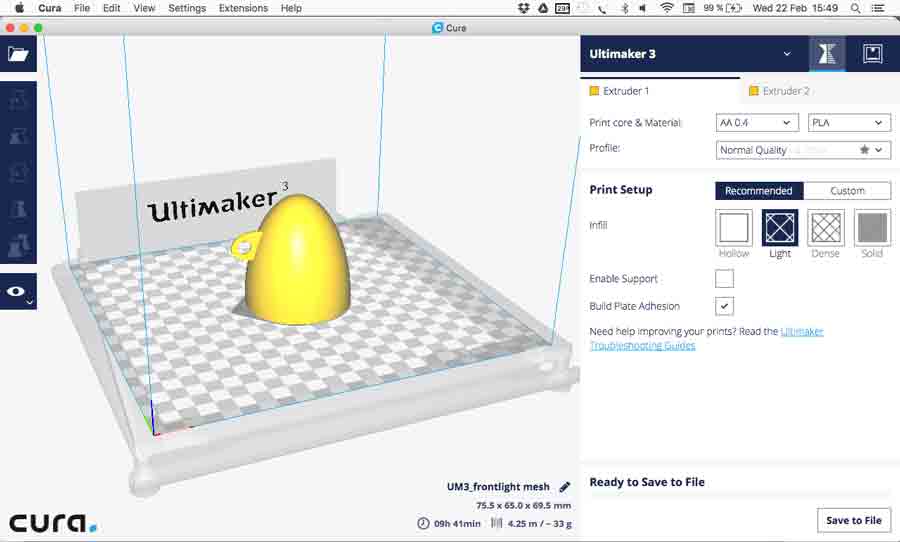
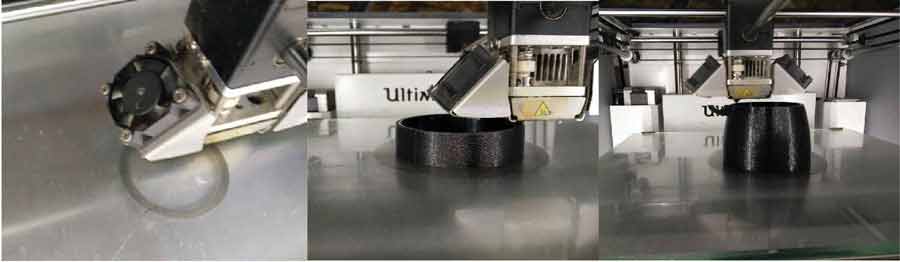
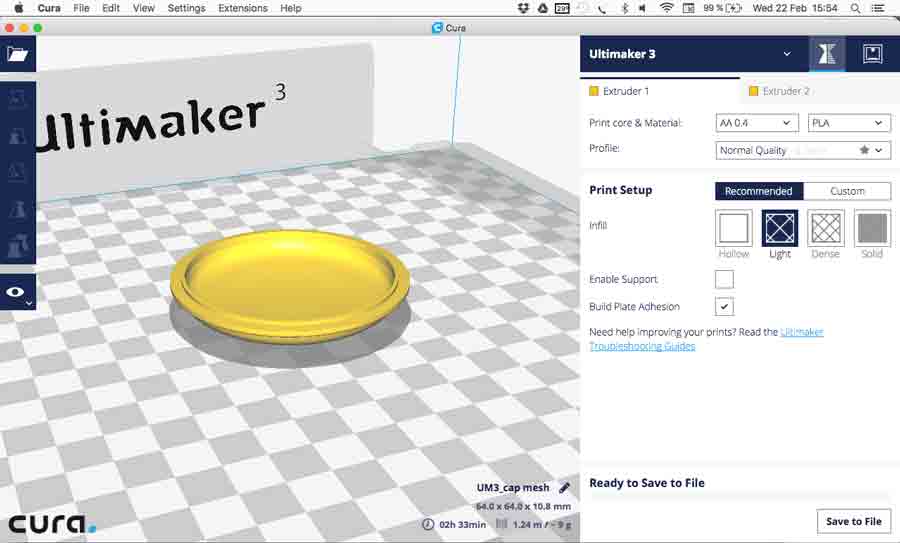
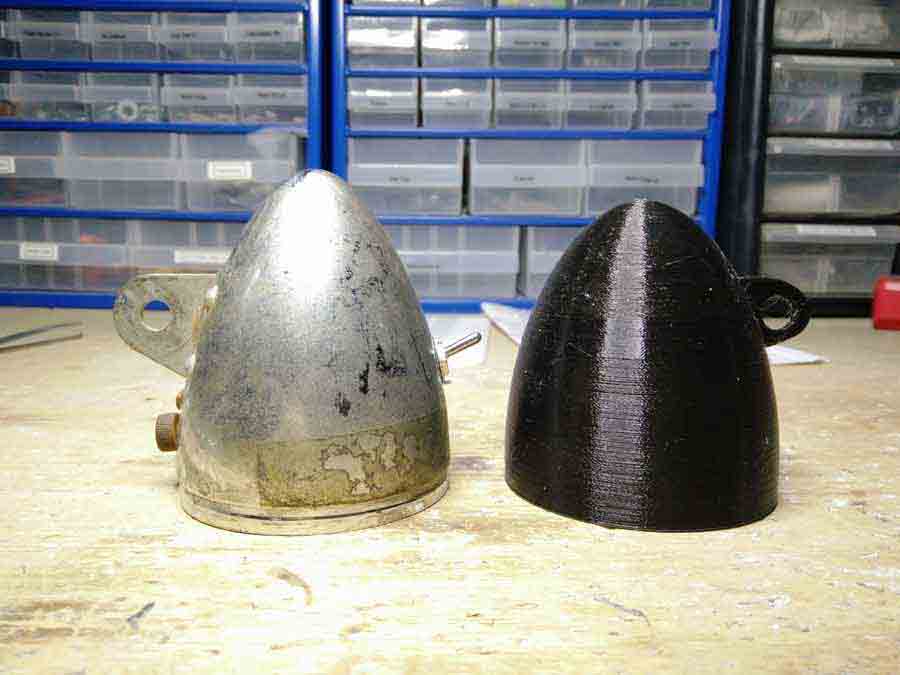
Here another exercise I did last year.
It is the handle of a rubber stamp.
Designed, meshed and generated the stl file in Rhino.
G-code and print in Cura.
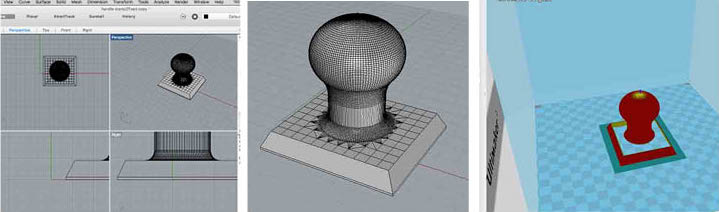
The first print did not come complete as the filament got stock because the roll got mixed up and stucked so the job did not complete.
I did send it again with a different color filament because there was no more transparent filament stock.
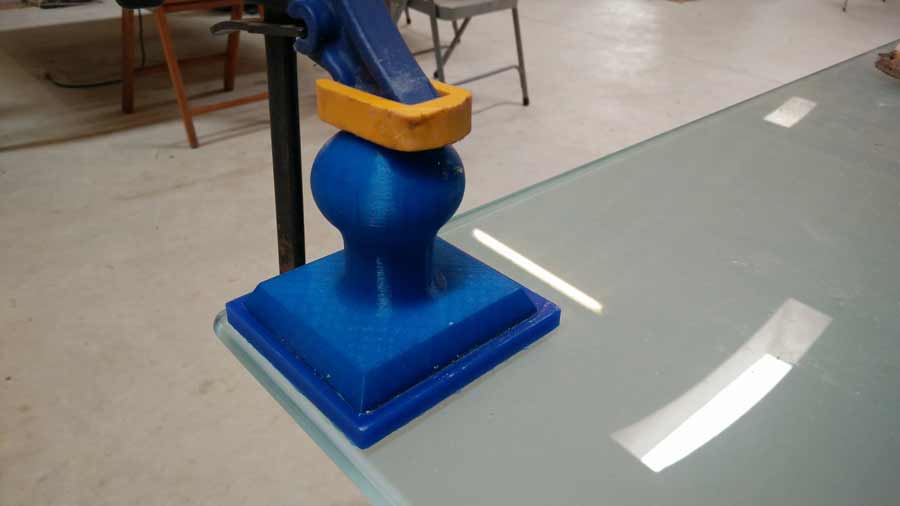
As can be seen in this next picture I have already done the casted rubber part with a logo but I will review it in the molding and casting assignment.
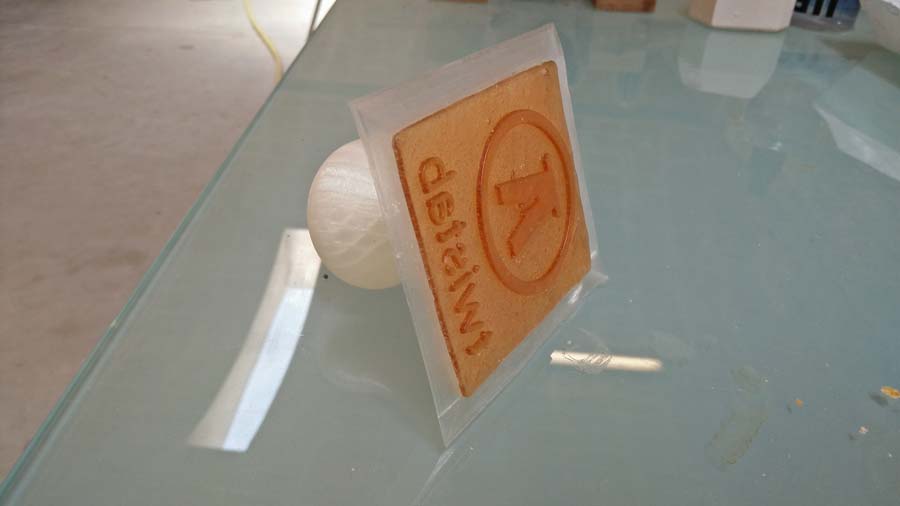
3d scanning
I scanned my-self (chest up) with the skanect.
p>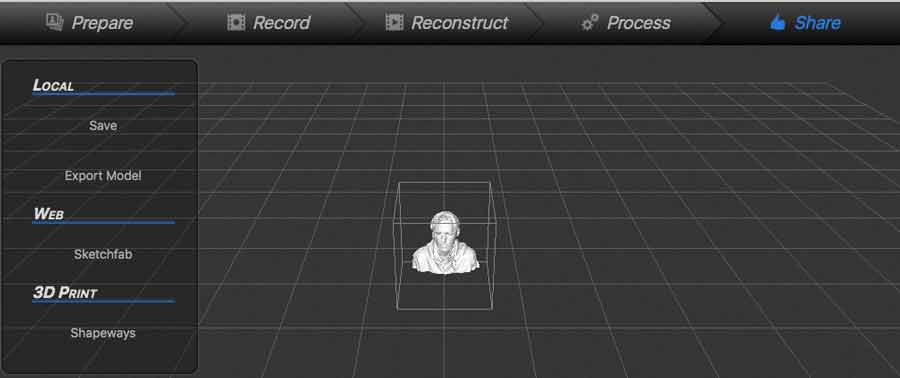
I opened the stl in Meshmixer to fix a blop on one area (right side of the forehead) of the model. I did not spend much time fixing it, just enough to understand the basic of meshmixer and see its potential.
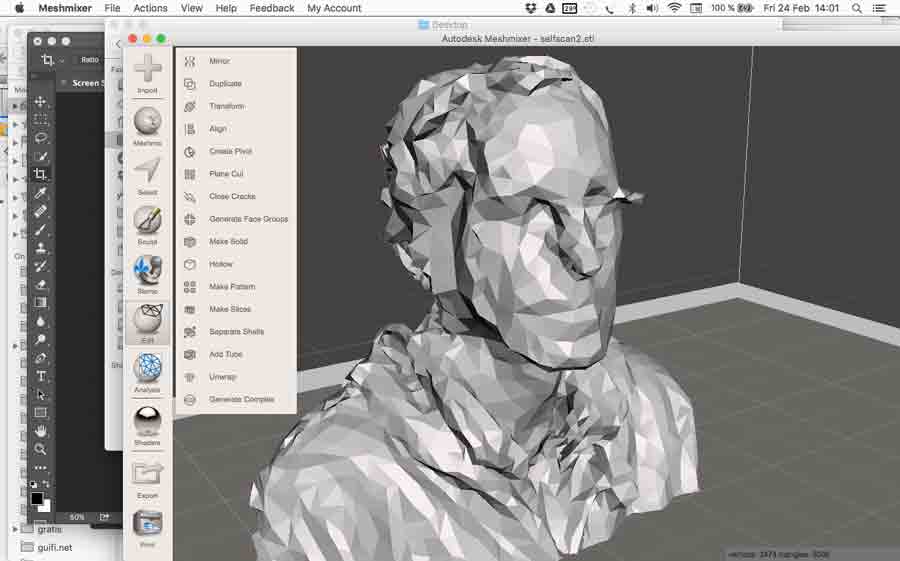
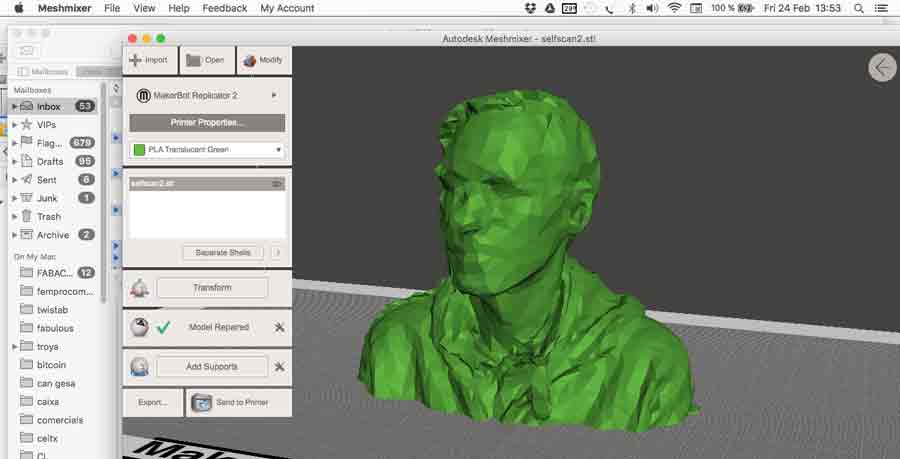
I imported the stl file in Cura and did my setting for a low-res quality. Did not want to spend too much time printing, just experimenting with the reprap PRUSA i3.

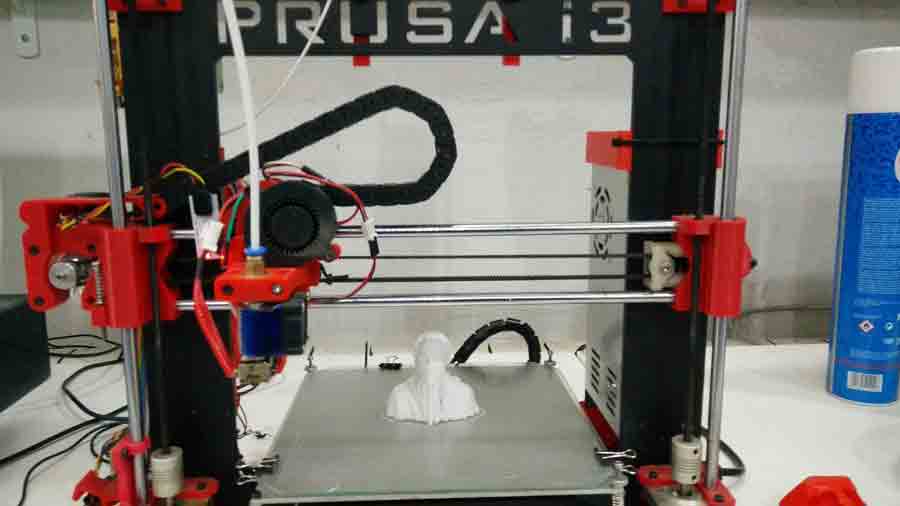
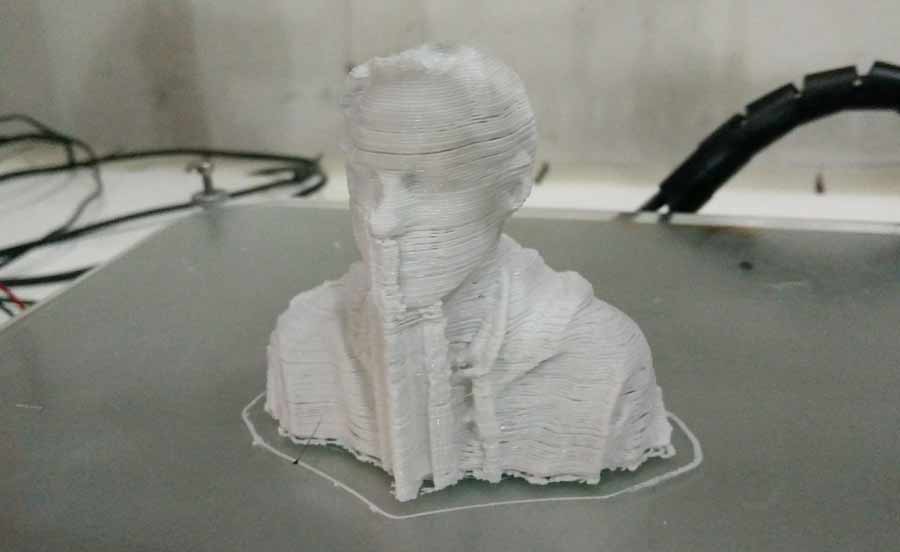
Even though I had set up the print at a low quality I thaught the print would come out better than that. The extruder has a leak so apparently it was not extruding as much filament as it should have and therefore left a slight gap between the layers.
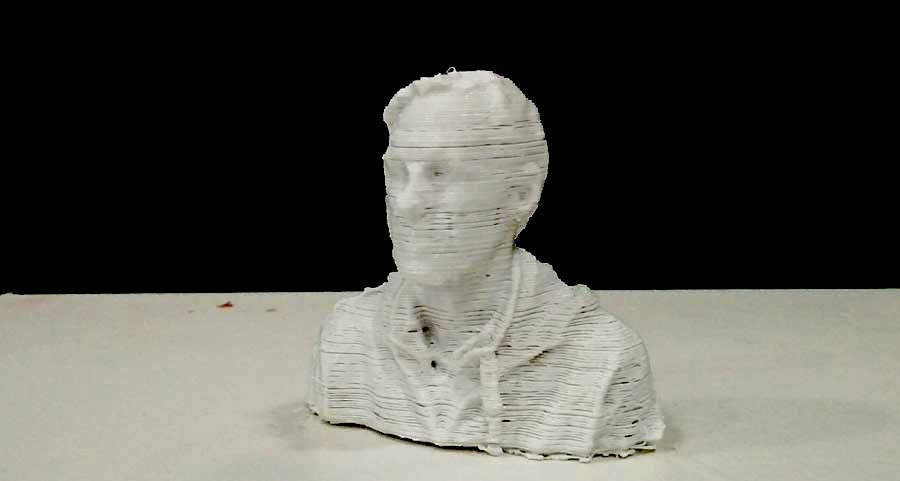
The last exercise I did was to scan a coin using the Modela and Dr Pizca application. I did tests with 3 different resolutions:
One at 0.5 x 0.5mm
One at .25 x .25mm>br> and one at .025 x.025 mm. The hi resolution took about 7 hours.
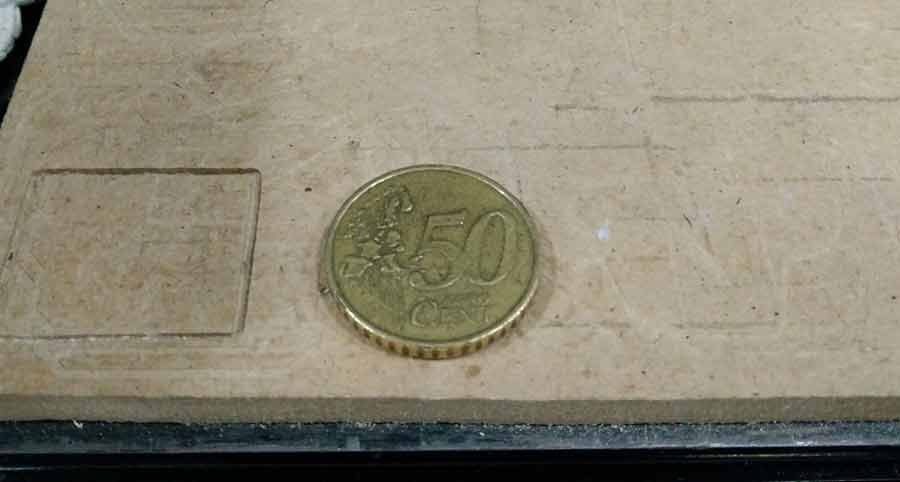
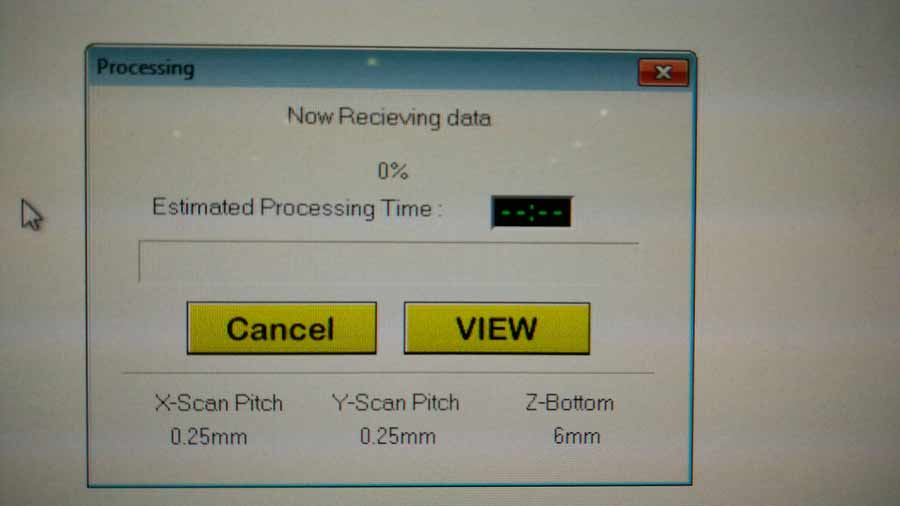
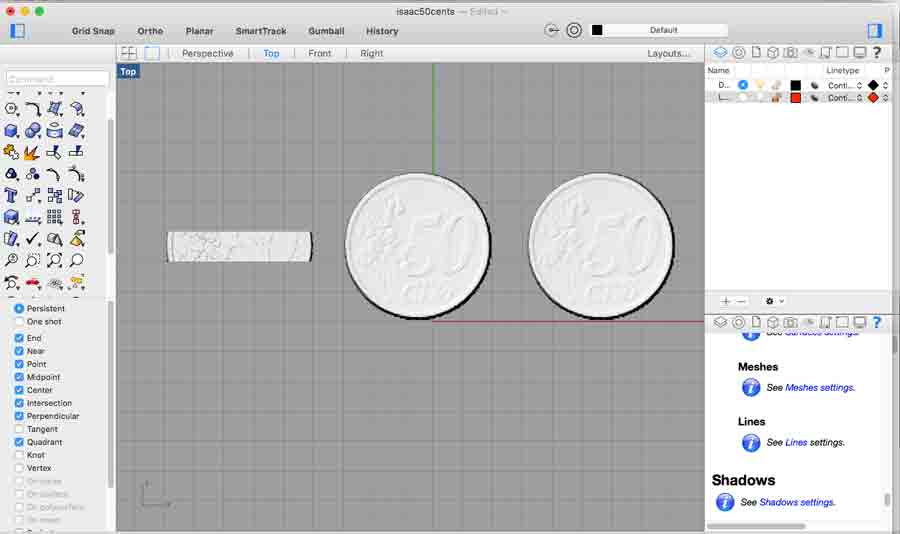
Than I designed a lamp holder - the typical plastic piece used to clamp a flexo lamp to a table or to be screwed to a wall - to replace one that had just broken.
I created the model in Rhino, exported the stl file and made the g-code in Cura for Reprap. I set it for dense infill (to ensure the strenght of the object).
The first print did not come out well because the printer plate had a wabbly movement on the X axis. As shown in the next image some layers at the bottom adn the top are offsetted by the printer.
Anyhow I also realized after having printed that the lateral big and small holes were not lined up to the center. The big one beeing offset.
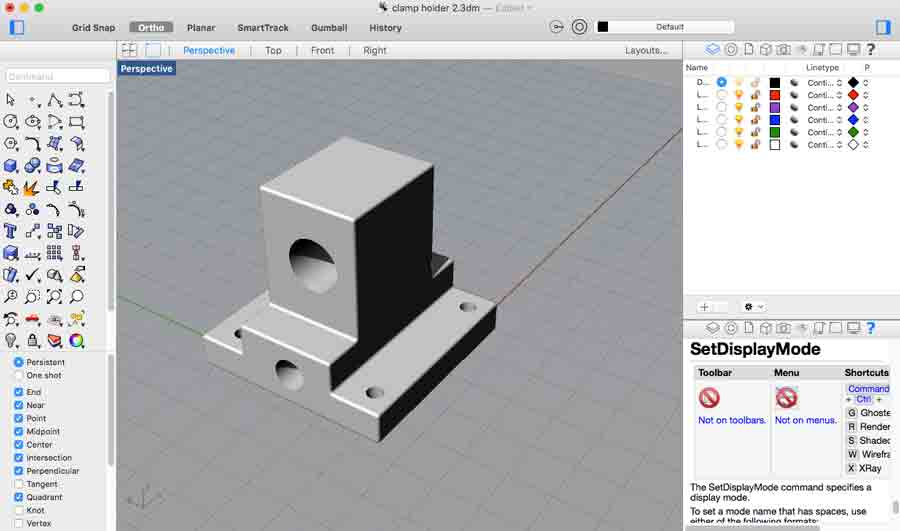
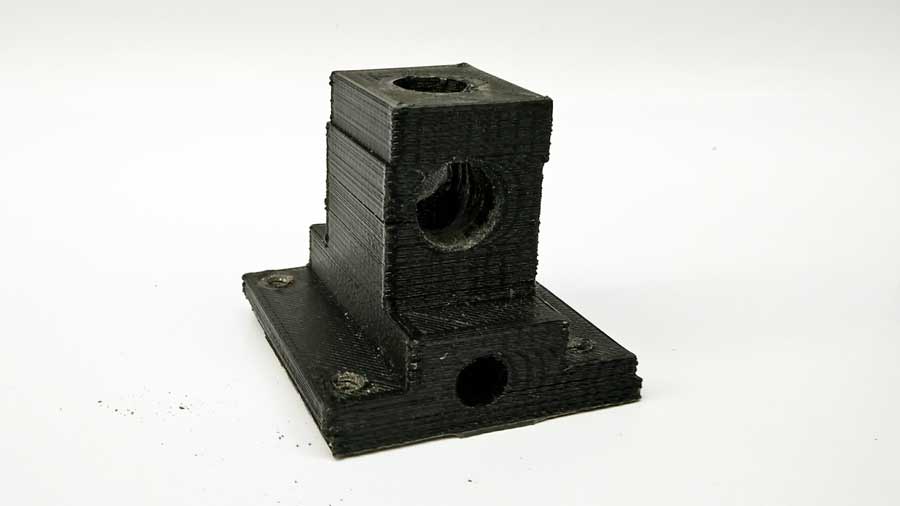
I corrected the model, added a bigger fillet (3mm.) and reprinted it.
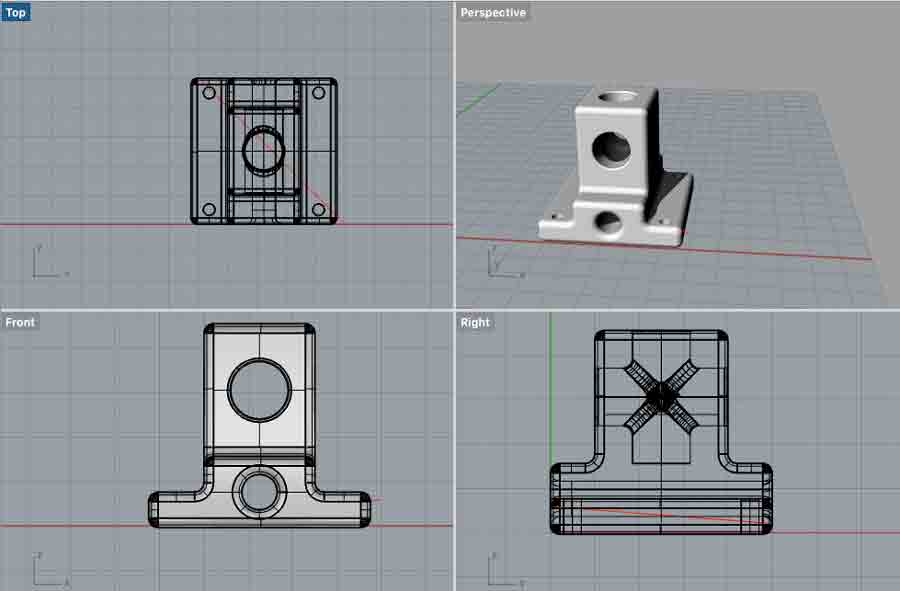
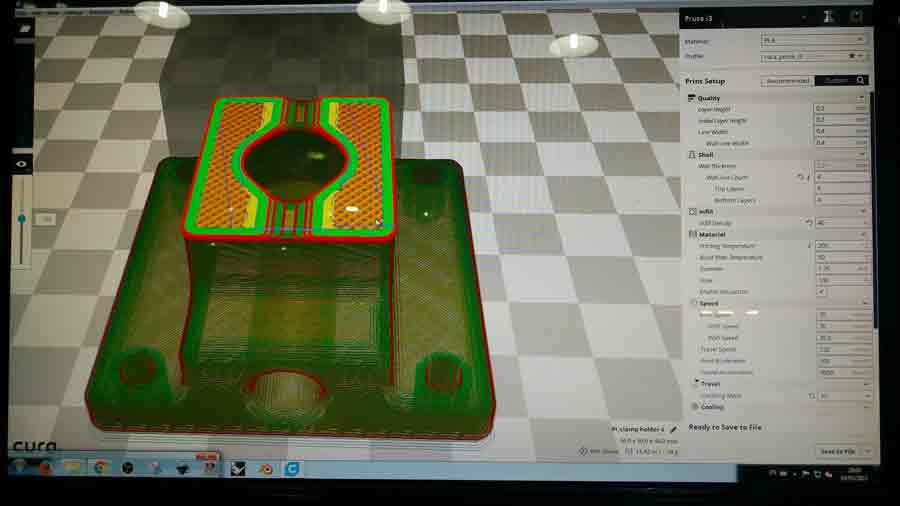
I also designed a hollow shape using the Grasshopper file I had done in earlier exercises. The idea is to experiement with very thin double wall and no support. I also printed with the Reprap4 using a minimal layer height (.2mm).
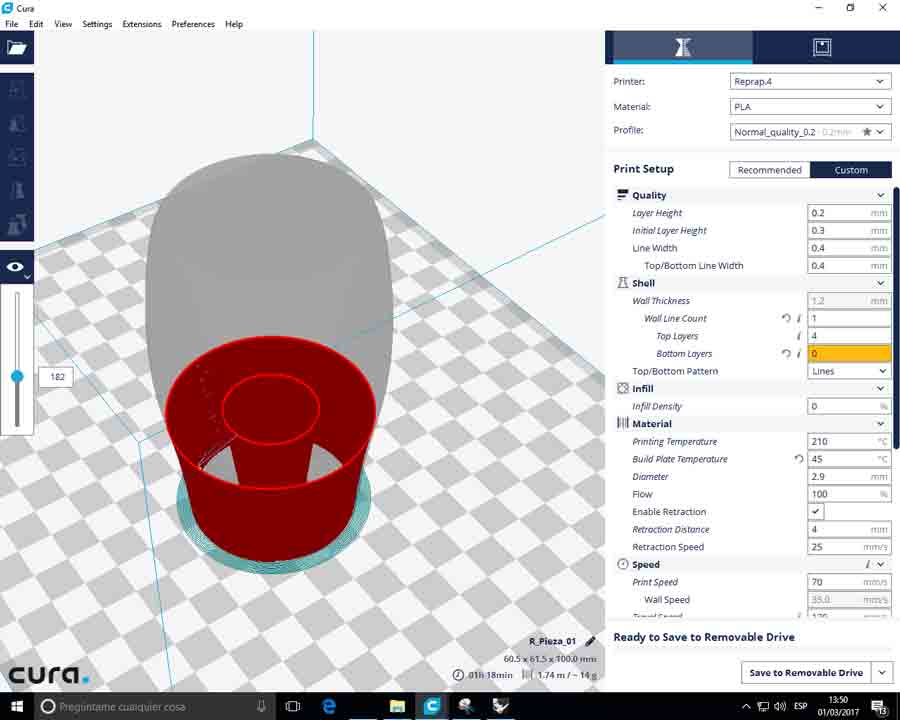
The print came out well though in the interior part there was a lot of hairy remainers from the prints and because of the hollow shape it was difficult to get to clean it up. Having set a stronger retraction speed I could have avoided it.
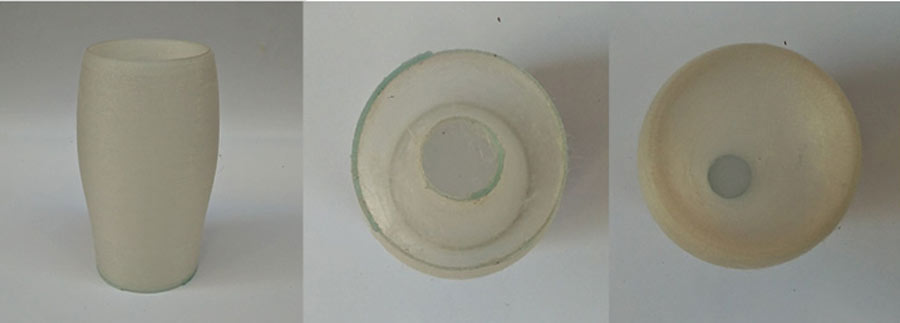