Fabacademy 2017
Nineth Week. Mechanical design
Index
Nineth task
Design a machine
Our group machine is a music roll perforator, the process of making your own music rolls is quite labor intensive as you have to punch the roll manually, we are designing a machine that will automate this tedious process. The machine would need to feed the paper roll foward, place the end effector in any of the 30 different positions and make clean punch holes. We will be using We took inspiration from inkjet printers and sewing machines for the complete mechanical design. Our music roll perforator is designed for 70mm width music rolls which is a popular format for the 30 notes music box like this one
We divided the machine into three main systems:
- The paper feeding system, consisting in a slotted base and a mechanism to roll the paper foward and backward.
- The gantry consisting in a linear axis positioning the end effector in 30 different positions or notes.
- The end effector which will punch the paper with 2mm diameter holes.
My individual contribution within the project was to design the end effector of the machine.
I have used Onshape for the header design as many dimensions are interrelated changing during the design process of the other components and the sourcing of additional materials and components. All header components have been designed to be 3D printed. Design is also adapted to MTM ball-screw steeper motor so no further modification is needed.
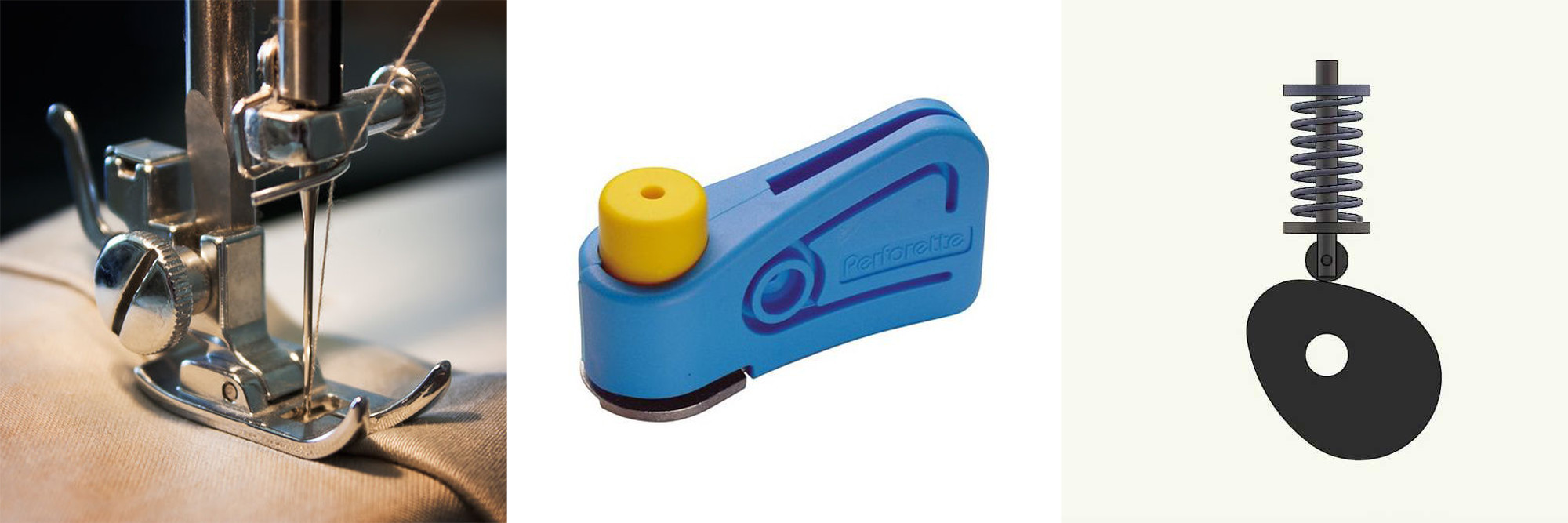
The references
For the Head design I used three main references: the foot of a sewing machine, which allows the needle to puncture the textile while keeping the textile fixed on the vertical axis, handheld paper perforators, which uses a spring to move the shaft up and down, and the cam and follower mechanism, which uses an eccentric piece to transform a rotational movement into a sliding one.
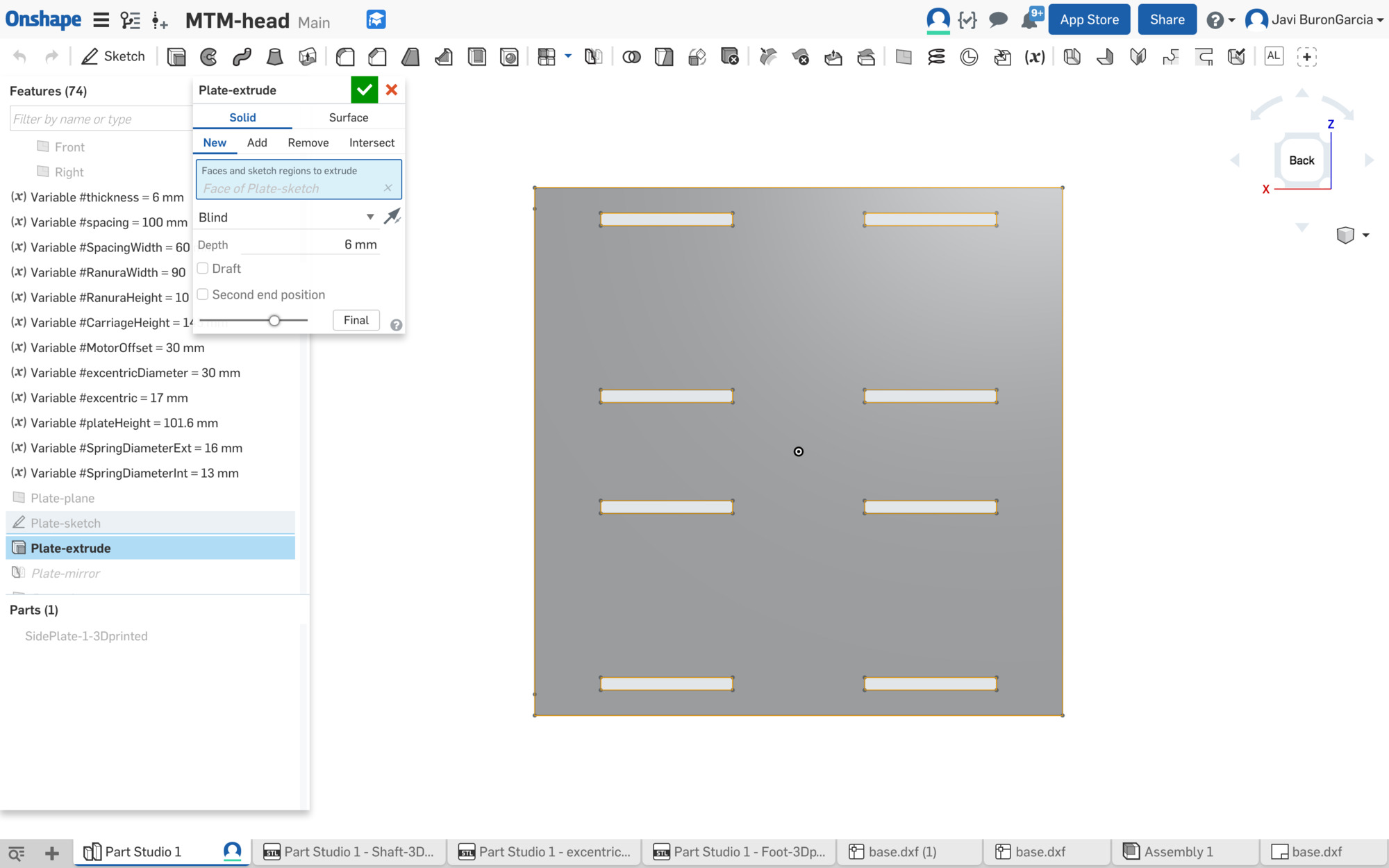
Interface with the other parts
The connection with the horizontal axis is resolved using a 3D printed plate following the same pattern than cardboard design. Horizontal slots allow fine adjustment of the head respect the axis.
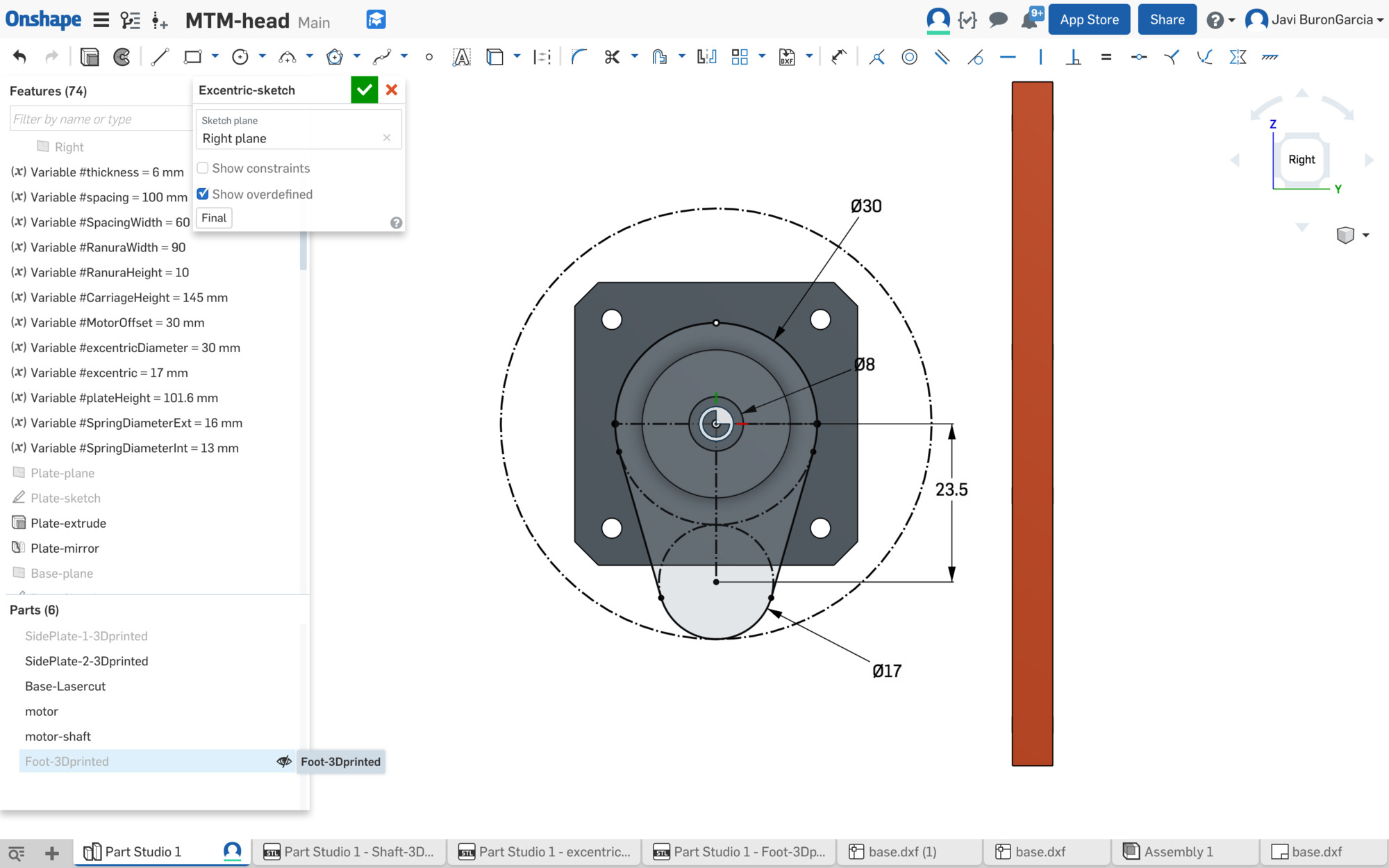
The perforation mechanism
Excentric design is based on the cam and follower mechanism. The parametric design allows for fine tuning of the distances once horizontal axis, shaft and cutter height are defined.
Foot allows paper roll to slide easily underneath the shaft. chamfered edges prevent jamming.
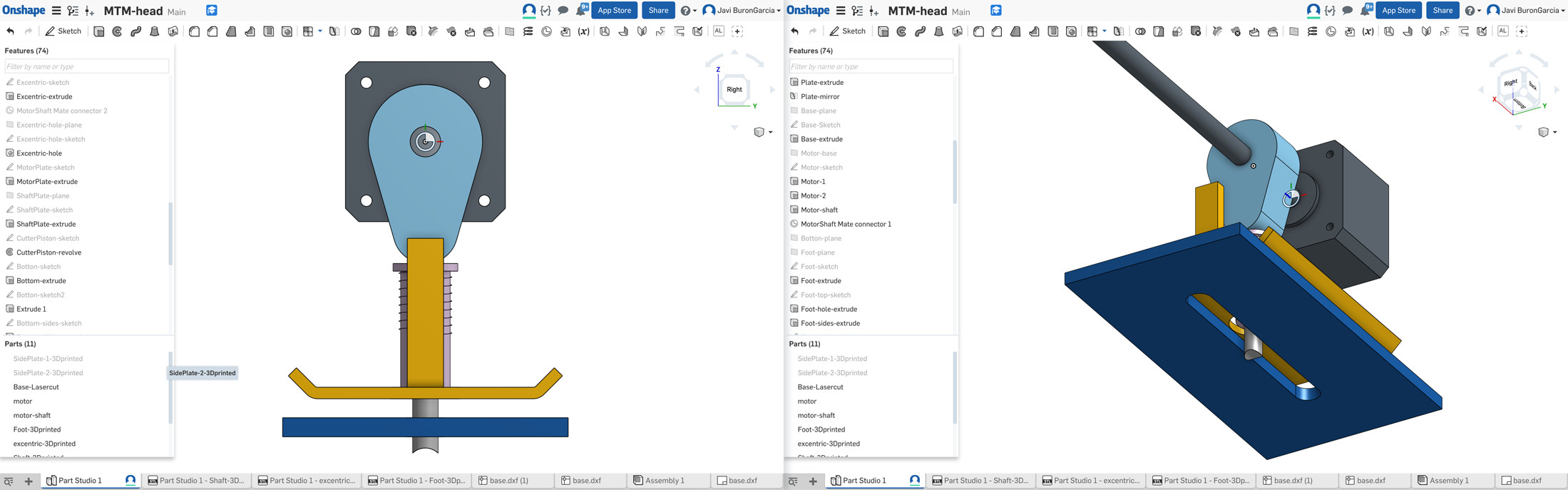
Parts configuration and final assembly
Once the basic dimensions and relationships between parts have been defined, a number of fillets and changers are introduced to remove material in areas that are needed, allow a better view of the paper roll and the puncture mechanism and facilitate tool access for assembly and fine adjustment.
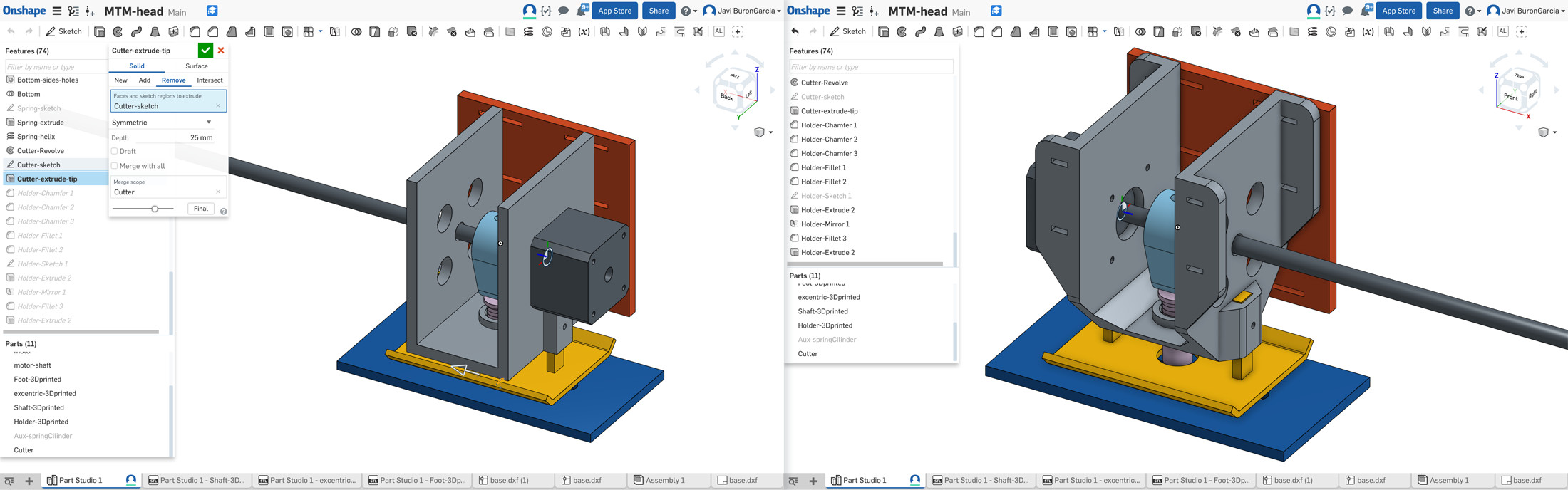