Week12: Molding and Casting
Assignment
- design a 3D mold, machine it, and cast parts from it
Design 3D mold
I designed a double sided "FabLab Medal" by Fusion 360.
This is what I am going to make finally in this assignment.
3D modeling
Import SVG file to Fusion 360.
I modeled "FabLab Medal" first.
Second modeling is like "silicone mold" from first model.
Third modeling is like "wax mold" from second model.
Sprue and vent and marks are added.
download.f3d
Milling
I used "MODELA Player4" and "VPanel for SRM-20".
I used these endmills.
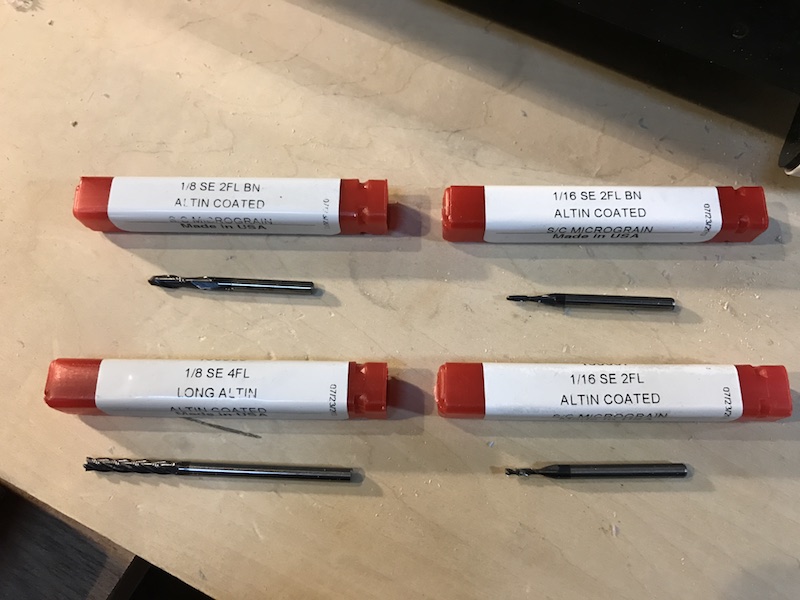 |
1/8 2FL BN(BALL) and 1/16 2FL BN are for finish cut.
1/8 4FL LONG and 1/16 2FL is for rough cut. |
Open STL file in "MODELA Player4".
Choose material "Modeling Wax"
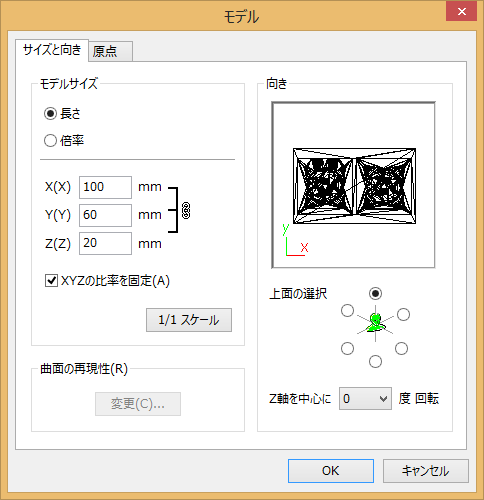 |
|
|
Change the origin from center |
Open VPanal and move endmill to origin point. Set X/Y and Z as Zero.
Rough Cut
1/8 4FL LONG endmill is used.
Milling machinable wax
After rough cut is finished, I found that holes are not made. So I used 1/16 2FL to make holes. Start cut depth which is -9.1mm, is from Fusion360's model measurement.
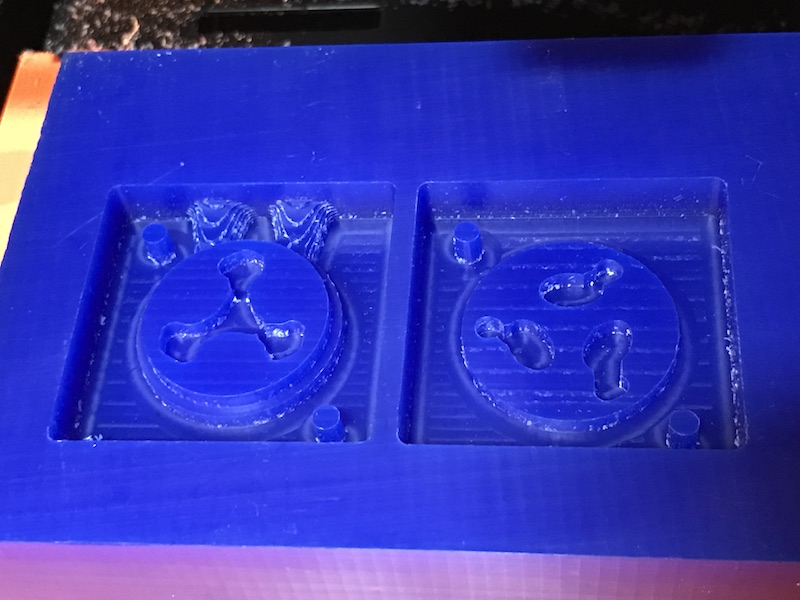 |
|
1/8 4FL LONG (holes are missing) |
1/16 2FL |
Finish Cut
Press "New Process" and set parameters
Make "tool path"
Open Virtual MODELA
Path Simulator started.
Show Process time
1/16 2FL BN is used for finish cut.
Casting
To make a mold from wax mold, Silicon is used for casting.
MSDS ( main agent,curing agent )
More than 6 hours after pouring, I got silicone mold.
To make "FabLab Medal" from silicon mold, resin is used for casting.
MSDS ( A, B )
After first casting, I found missing part. The cause is position of sprue and vent. One of them has to be designed top of casting object. In second casting, I pre-add few drops of resin on mold where missed in first casting, then I pour resin normally. Then I got second cast in the picture below.
I had to design...
or angled
Fail design
This is fail design I made before blue wax. Distance between each parts was very close. When re-design the mold, I kept distance between them more than 1/8 inch (3.175 mm) and hole size is larger then 1/8 inch,too.
FabLab resin medal