The objective of this assignment is to design a 3D mould, mill it then cast it. The intention is to design appropriate objects within the limitation of 3 axis machine and demonstrate the workflow of the whole mould design process from constructing, milling and casting.
Requirments:
// Explained how you made your files for machining
// Shown how you made your mould and cast the parts
// Described problems and how you fixed them
// Included your design files and ‘hero shot’ photos of the mould and the final object
Released: 19.04.2017
Week12: moulding and casting
DOWNLOAD THE FILES
Experience
Moulding and casting is one of the interesting topics to explore and study in the design world.
For the moulding design process: we used monoFab machine to mill boxes of wax, a maximum dimension of 150mm x 100mm x 40mm using modela player 4 to create the strategies.
For the casting process:
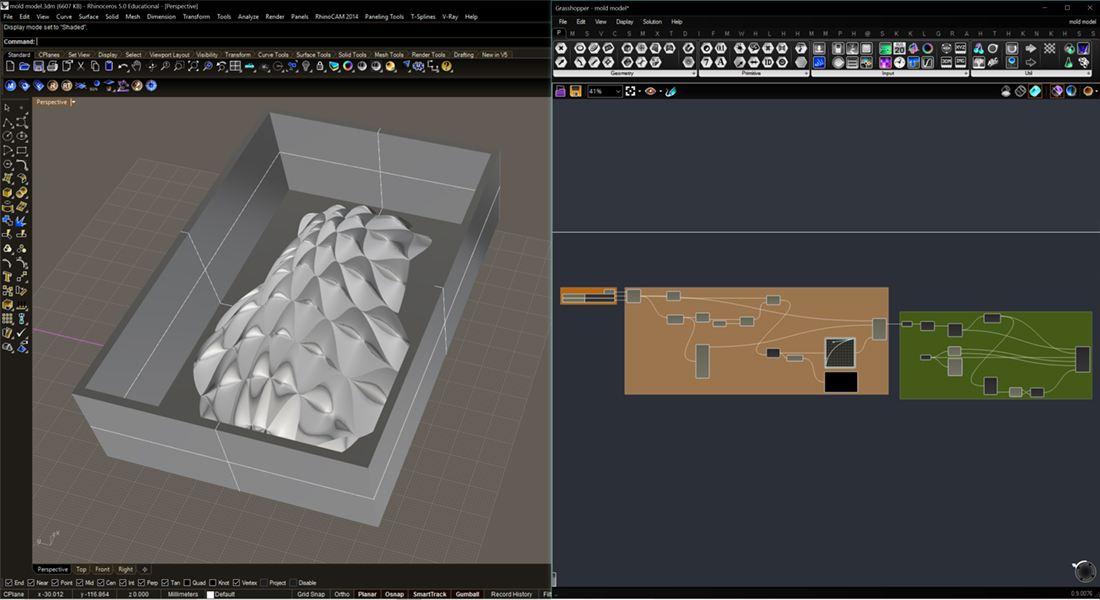
modeling using Grasshopper in Rhino and exporting it as STL.
the first strategy of milling would be roughing to remove the unnecessary material with a 3mm tool bit
I have used the 3.17 milling bit for roughing
cutting the area to the size needed for more efficiency in time cutting
for the finishing strategy you only shange the tool, and i have changed it to 0.79mm bit
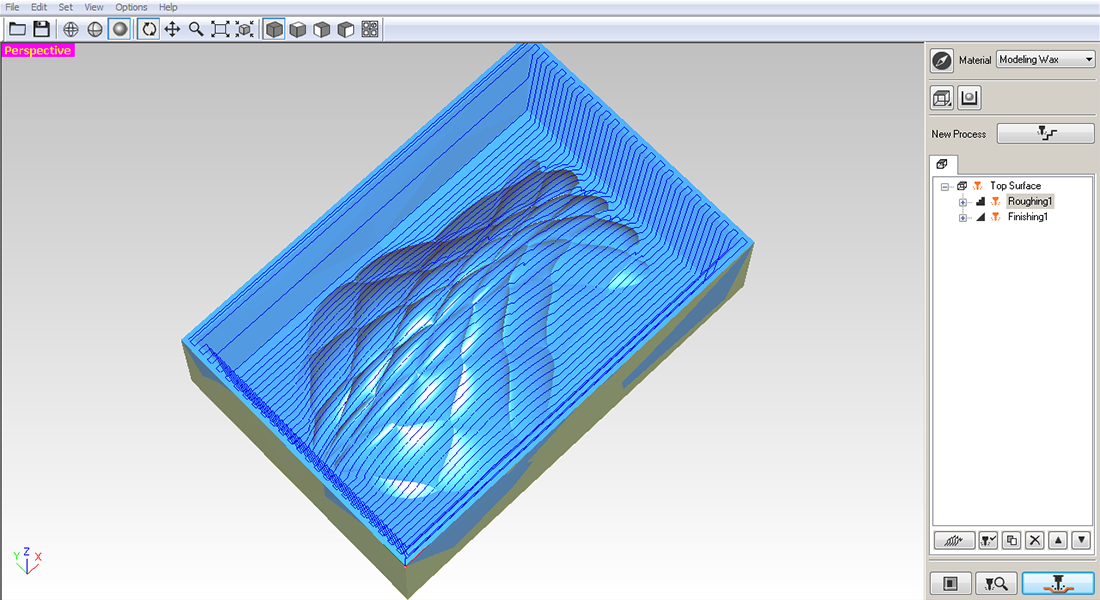
how roughing looks like
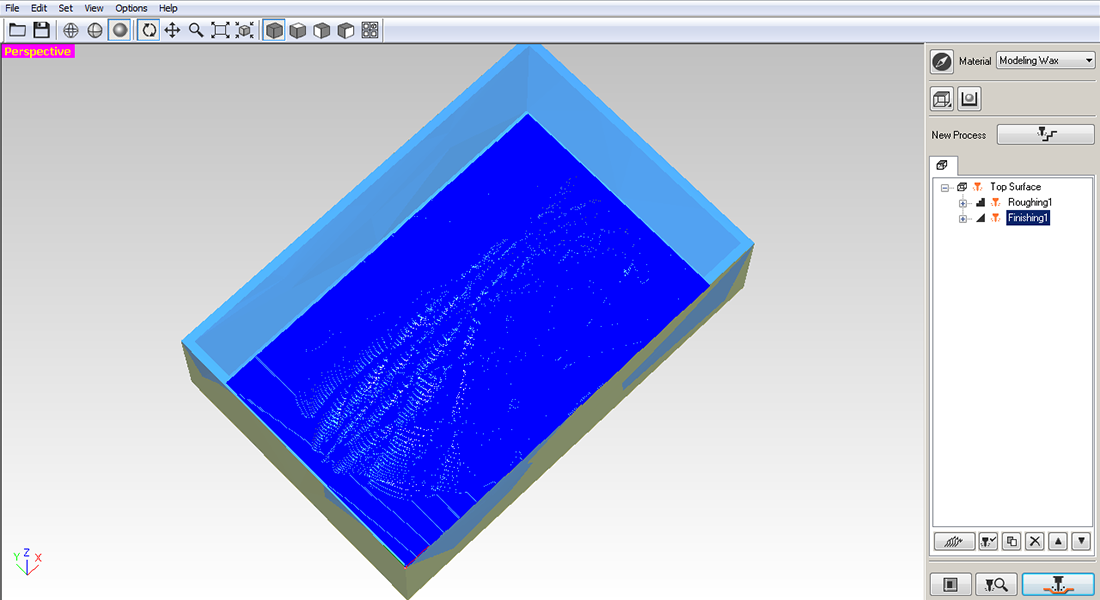
how finishing looks like
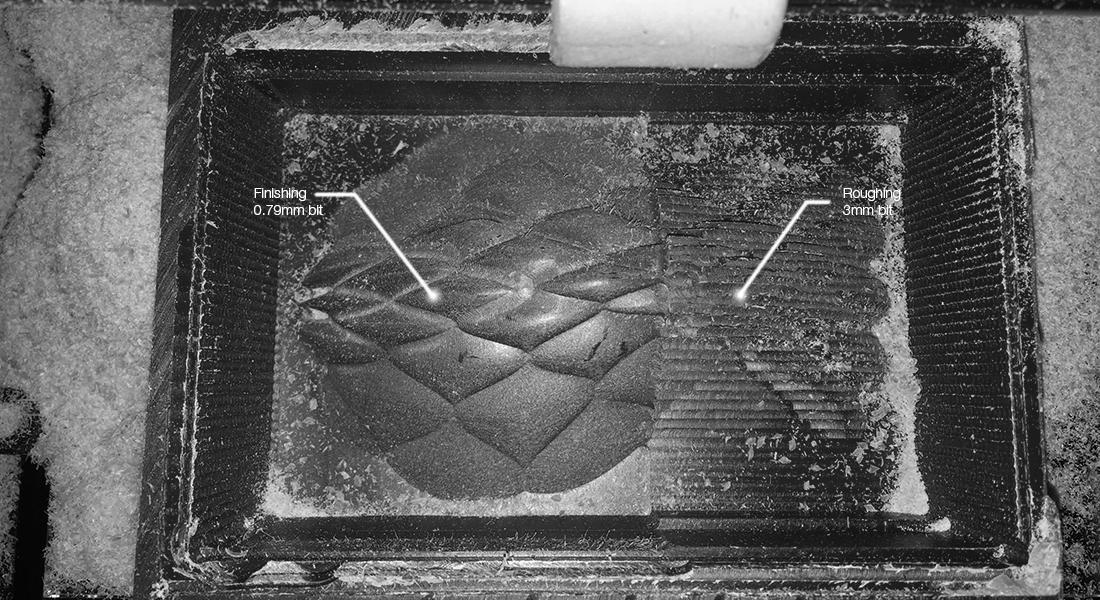
difference between roughing and finishing strategies on mould.
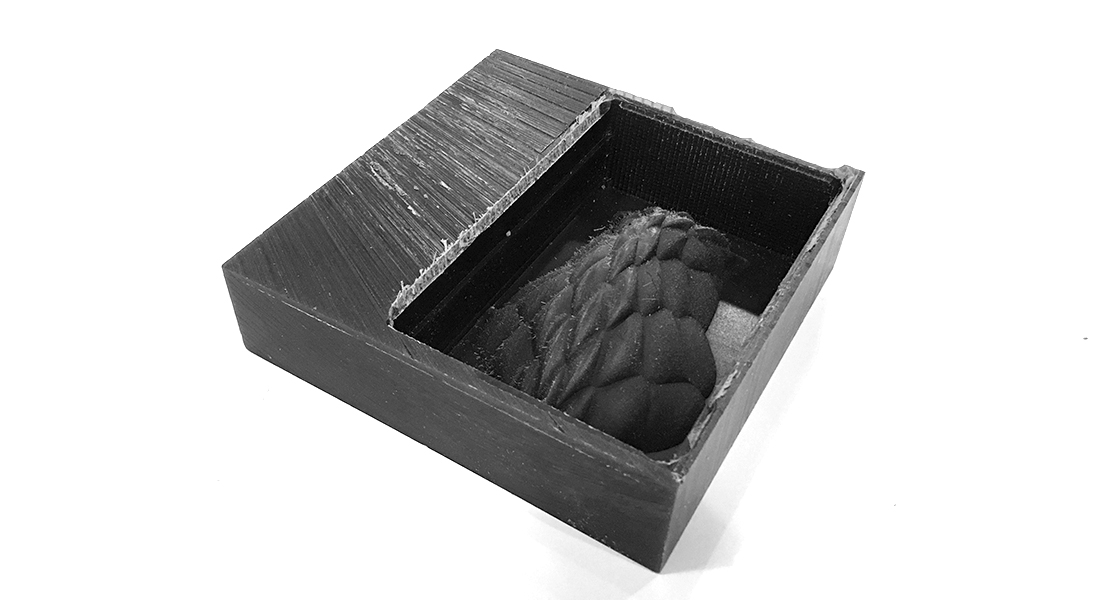
final result of milling a wax mould
MOULDING
FormSIL 25 check
FORM X for more information.
it is important to read instructions and specification but for this form silicone; I first filled the wax mold with water to measure the content of silicone required then added 3 % of hardner. Mixed very well; pored and placed inside a make shift vacuum untill all bubbles surfaced. The vacuum include a glass bowl on a plastic surface with rubber lining and an air pump to take out the air. I left it for 24 hours to cure completely.
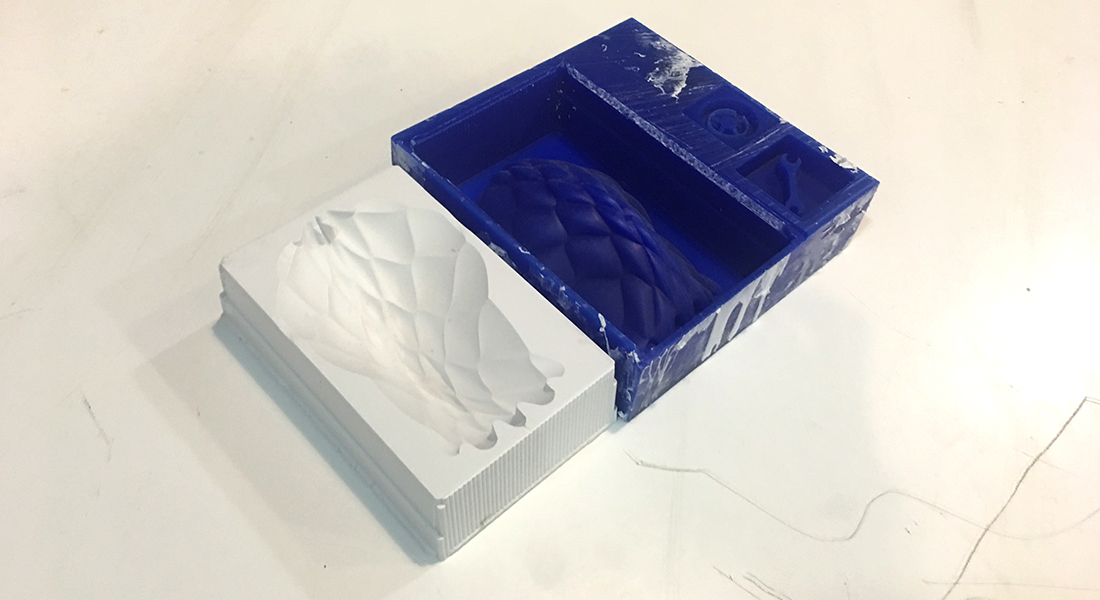
casted silicon mould
METAL CASTING I have used special metal kind called
Babbitt metal Whic has a melting point of 100-150 degrees.
I was afriad that i needed to use a special kind of silicon for metal casting and in theory i actually need to, but i tried to cast with the silicon we had in the lab.
NOTE: It dries as soon as you cast it. Wear heat resistant gloves always.
HERE is also an MSDS for
Babbitt metal

final model