week 14
Composites.
Assignment:
Read the material safety data sheet (MSDS) and technical data sheet (TDS) for the resins that you're using. Design and fabricate a 3D mold (~ft2) and produce a fiber composite part in it.
Guillermo Jaramillo :: Fab Academy 2017
Fab Academy 2017
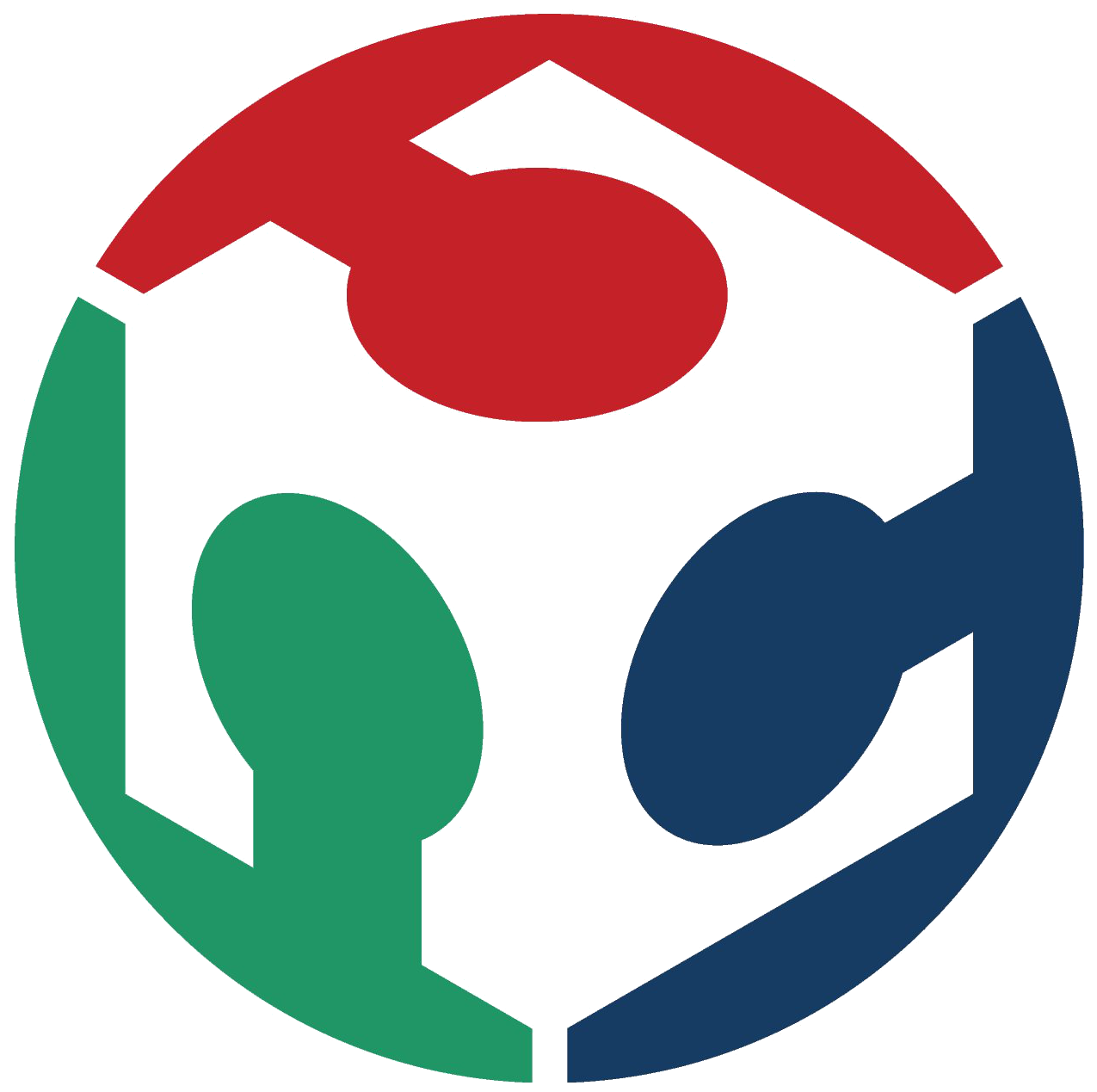
The first part is read the literature about the resin that i will use. The product is called PoxBak. Is an epoxic resin that has multiple use, like molding, making tools, ceramics and other.
Epoxy is thermosetting. That means that it cures depending on the surrounding temperature. Once epoxy is cured, it cannot be uncured. Epoxy is an epoxide, which simply means that it's more reactive to other chemicals. A polyepoxide such as epoxy is made up of unreacted epoxide. This basically means that pure epoxy is extremely susceptible to reactions with other chemicals. The other chemical in the case of epoxy is a hardening or curing agent which works to cure it into a very strong adhesive.
Epoxies are created through reacting an epoxy resin and a hardener or simply by reacting the resins themselves. The vast majority of epoxy resins are themselves an industrial product which are derived from petroleum and are also the result of an epoxide reactive process. All depending on the type of reaction that was used to produce them, cured epoxy resins can either be like honey, or something much more viscous. Their actual molecular weight will determine the uses that you can get out of them.
Epoxy resins are very stable at room temperature and only cure when reacting with some kind of curing agent. Epoxies are the most common coating that's used in the field of wastewater. These are based on reactions which are made with still further reactions.
The document with chemical, physical and use of the resin, can be readed here: http://www.esalasingenieros.com.pe/pdf/electrica/pb1206.pdf
The second task to do is design a mold to create a composite. I used Autodesk Inventor to design the mold. It is composed of five parts, both positive and negative plus a base that holds the negatives. All were fixed using 1-1 / 2 "self-tapping screws.
The idea is to do and object like a basket to put in it some things like chocolates. The material that i choose is MDF of 15 mm and i thought any layers to complete the mold. I started with a base and grow up i added any layers with different measures of same shape. The same process is with the positive part of the mold.
I use Vcarve to set the tool paths to cut the shapes and a ShopBot to do the job.
Here is the shopbot cutting the pieces.
When the shopbot finished the job, I finished too the parts independient with a jig saw and a sand paper.
The next step is to choose a fiber to fabricate a composite. My lab has two fiber, one called tocuyo is a cotton fiber, other is called yute is a vegetal fiber. I used the two.
And now the next step is prepare the mold using vaseline to prevent that the resin act as glue with the MDF. And prepare the scenario to make the compo process. I thought use plastic bags to shield the mold from resin.
When the parts are ready to ensamble, I fixed them with screws.
Using a ruler to measure the same distance between shapes.
I screw one to one, not at all. This is useful detail at time to demold the final piece.
And finally is to spread resin to the mold and put the fiber. And spread more resin now and put the other fiber, and finaly put the positive part of the mold to finalize the process. Its neccesary apply pressure to make the resin dont stay at the bottom so all around and between the fiber compo.
Now to see the final results. The process to demold the piece, is very hard because the resin when is in process to solidificate increase it volume and the positive of the mold cant goes out. So its necessary in most cases to break the positive part of the mold.
The positive parts had to be cut and removed because the composite would not let them free.
Finally here is the composite of fibers and epoxic resin.
Here is the couple of resin components. To manipulate these its necessary use protection gloves, so the resin is toxic for the skin.
A final 3D view of STL files.