14. Composites
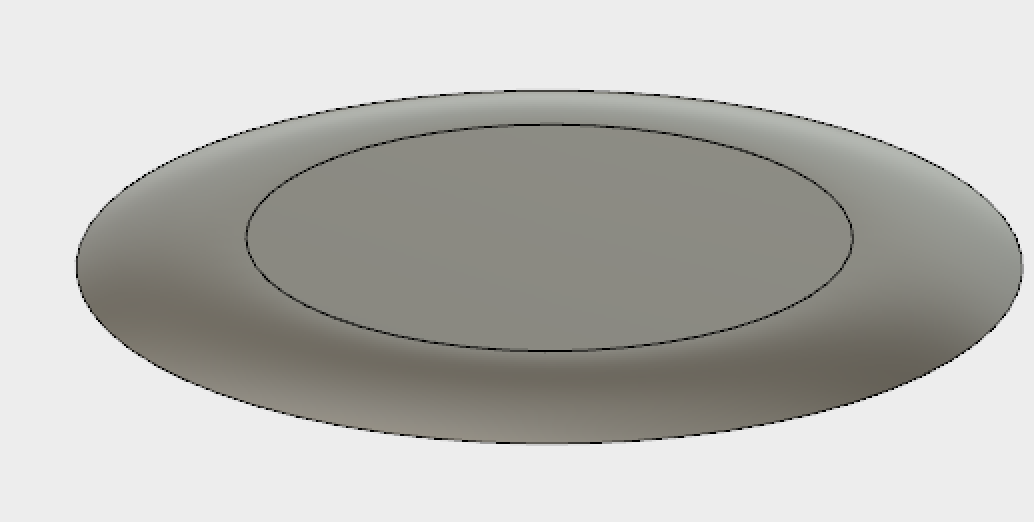
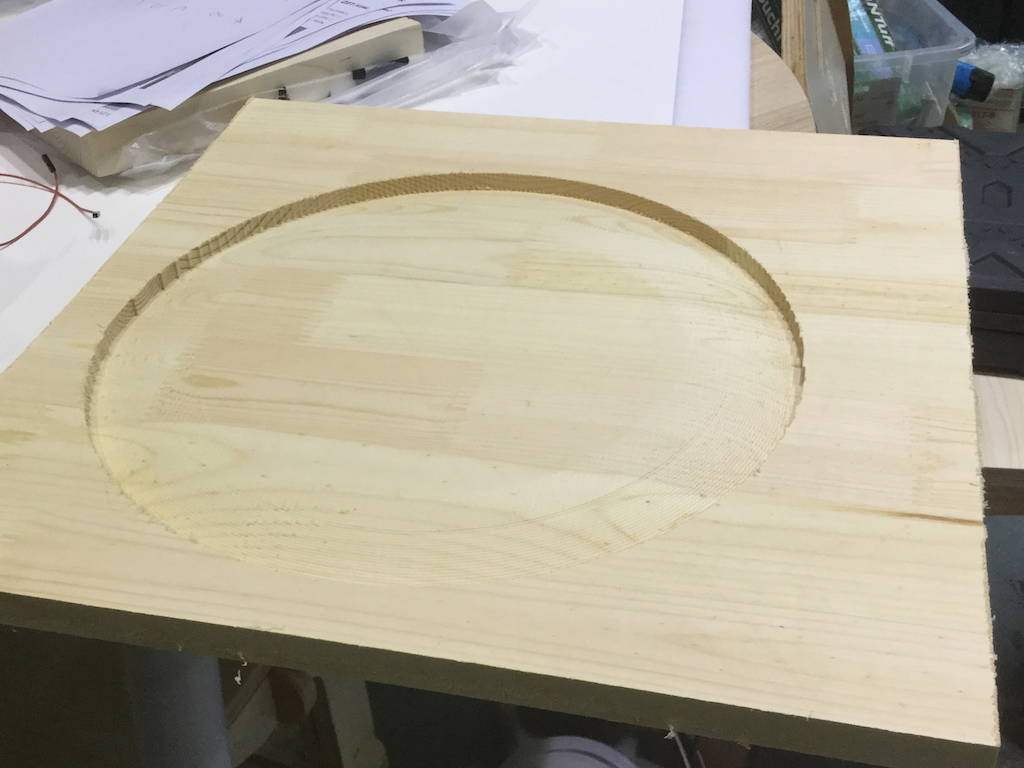
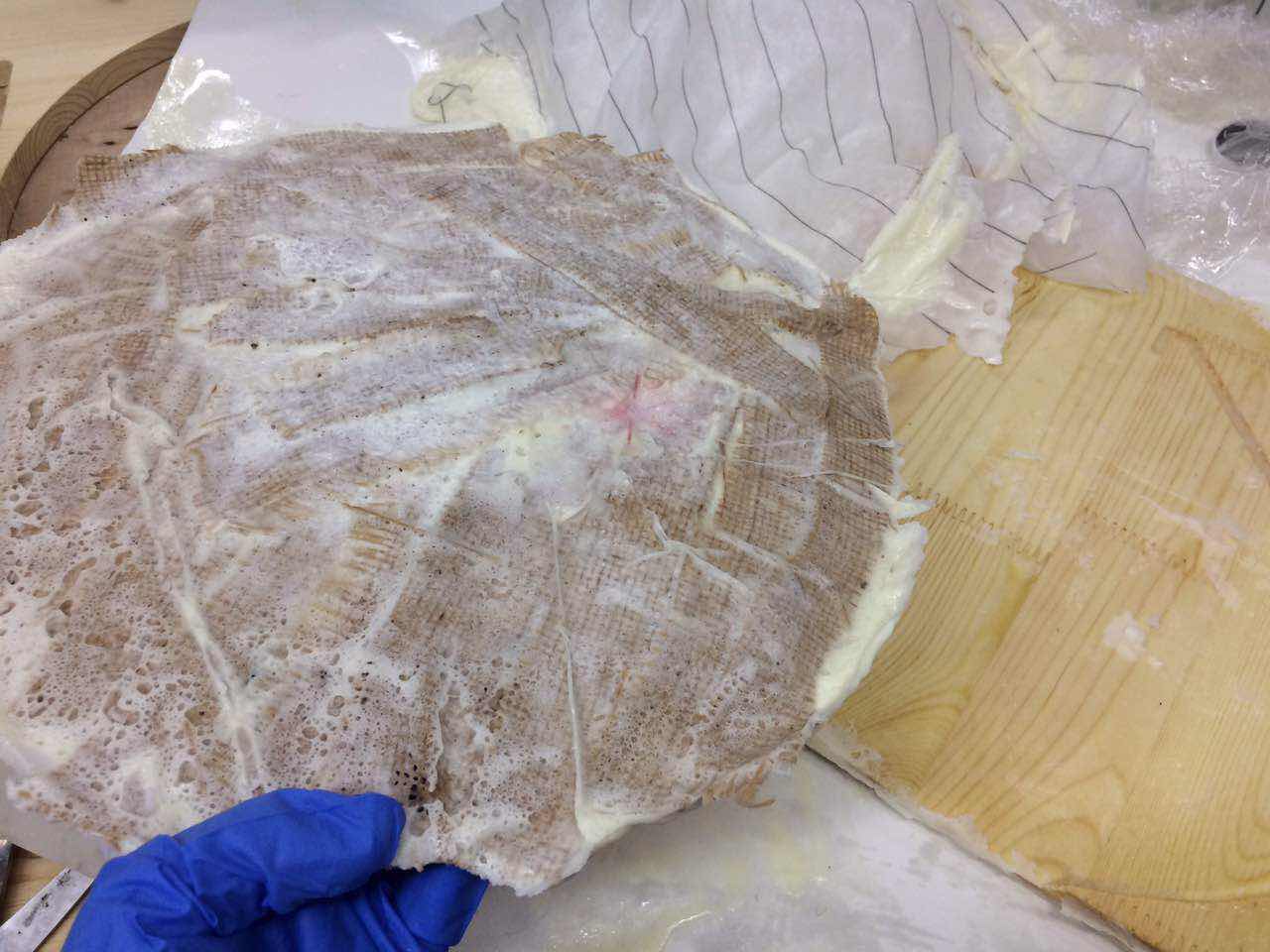
design the module
I used the Fusion360 to design the 3D module of my assignment.
(diameter:30cm ; thickness: 1cm)
Here is what I design:
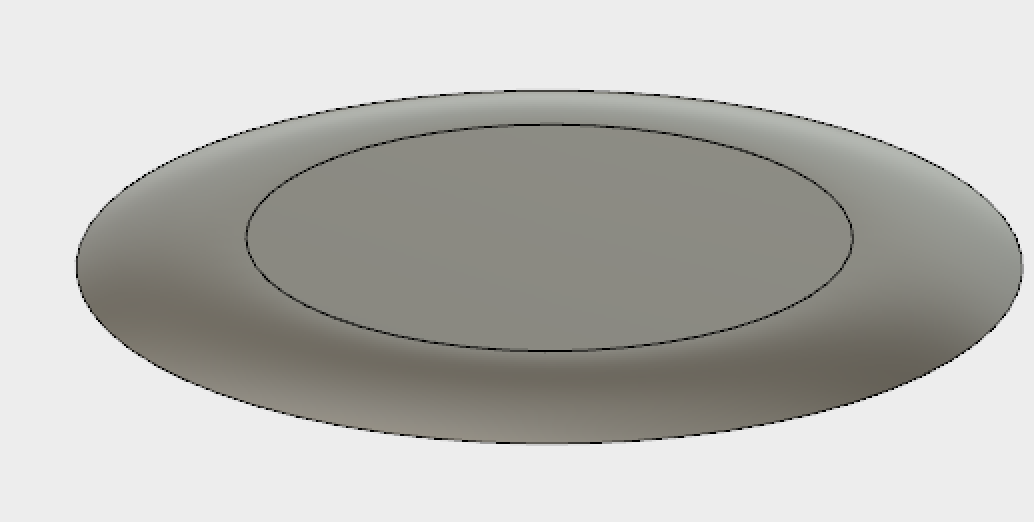
use the shopbot to cut the mold out
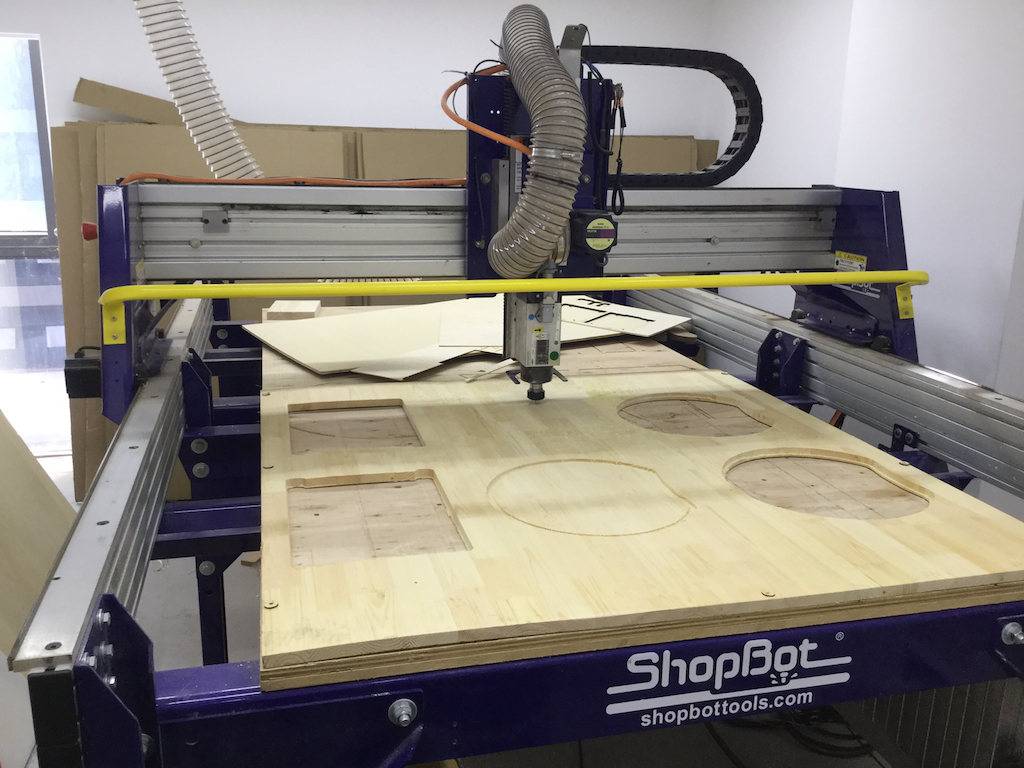
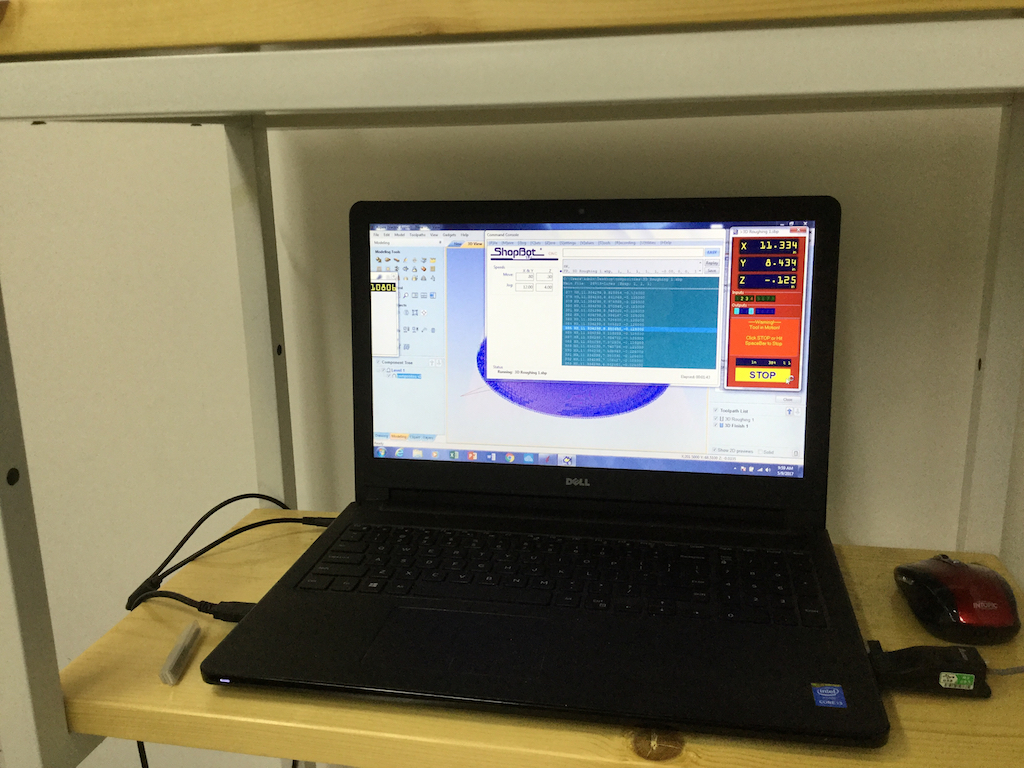
I used the Aspire to calculate the toolpath:
1. create a new file and import the 3D module - stl file2. set the module to the proper direction.3. set the toolpath and calculate it: I used the 1/8 inches endmill since I want to cut a great slope (and also, it let me to take a morning to mill the mold out.)4. save the toolpath and then start milling: (design a outline of it and cut it out from the wood board)
MSDS and TDS
The link to the product website.
The resin I finally used is 8017 A and B
1.I found that the heat it could generated is : Retention of properties up to 105 °C
2. Low viscosity - so I can easily fill my mold.
3.Long pot life|Good elongation|High toughness - it would be great for composities
4.It would gel in a very short time:
@ 150 °C (302 °F) 80 sec ------------------- @ 180 °C (356 °F) 32 sec ------------------- @ 200 °C (392 °F) 18 sec
So, I need to do my work fast.
Here is a brief summary of the safety:
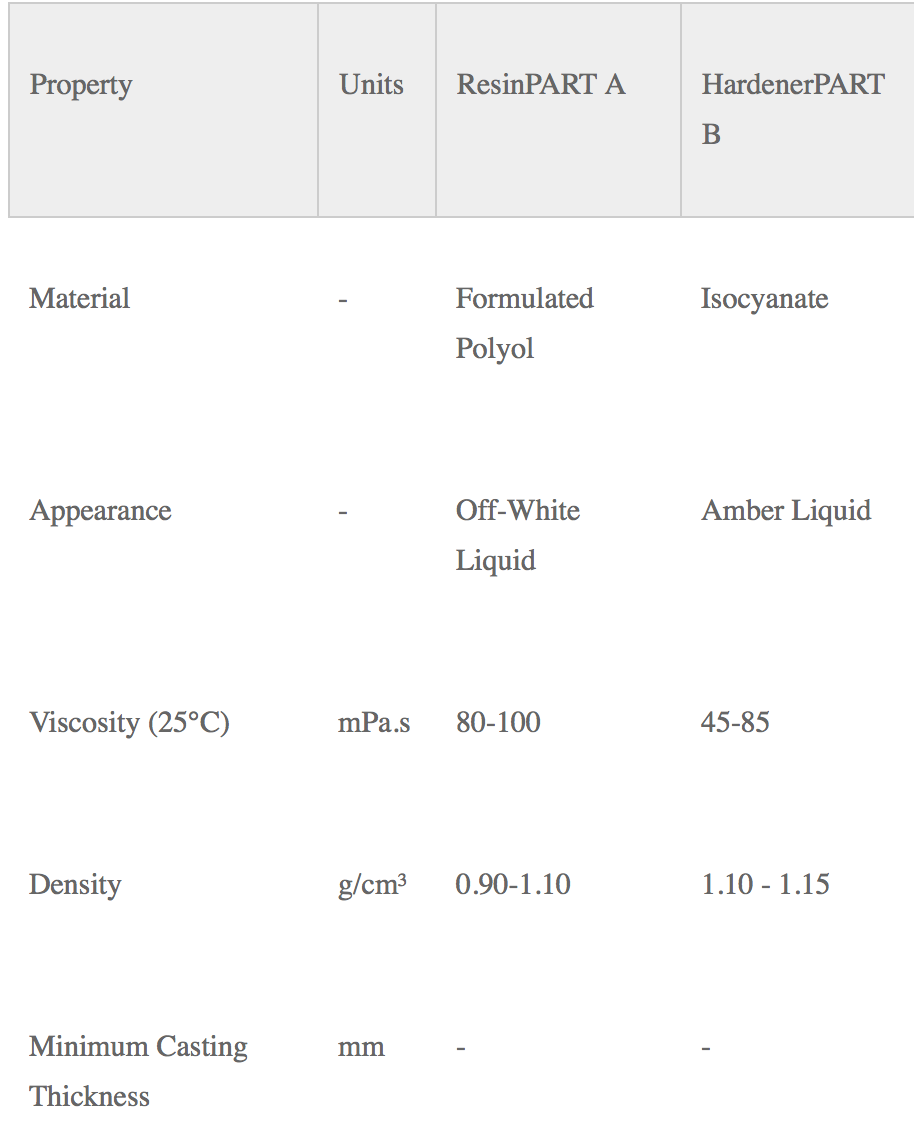
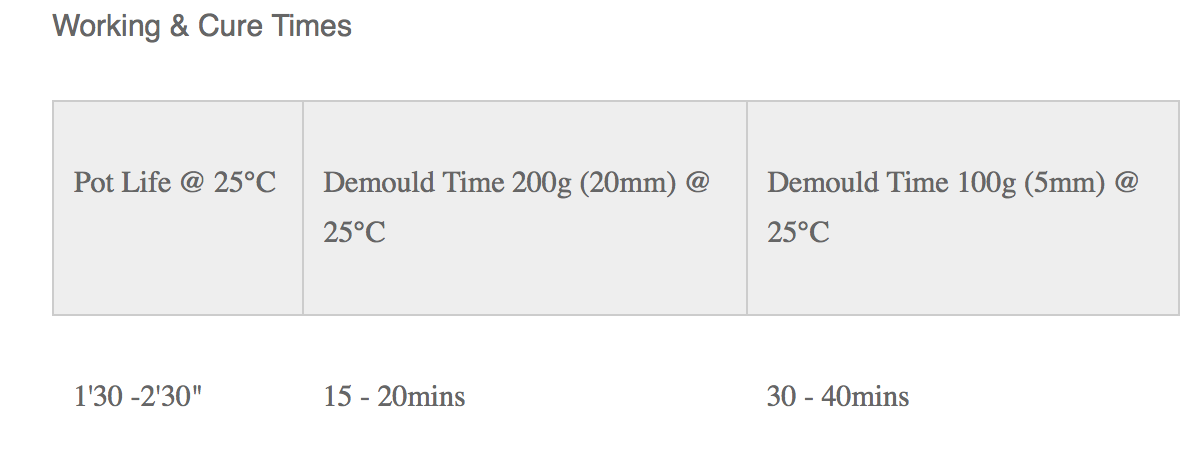
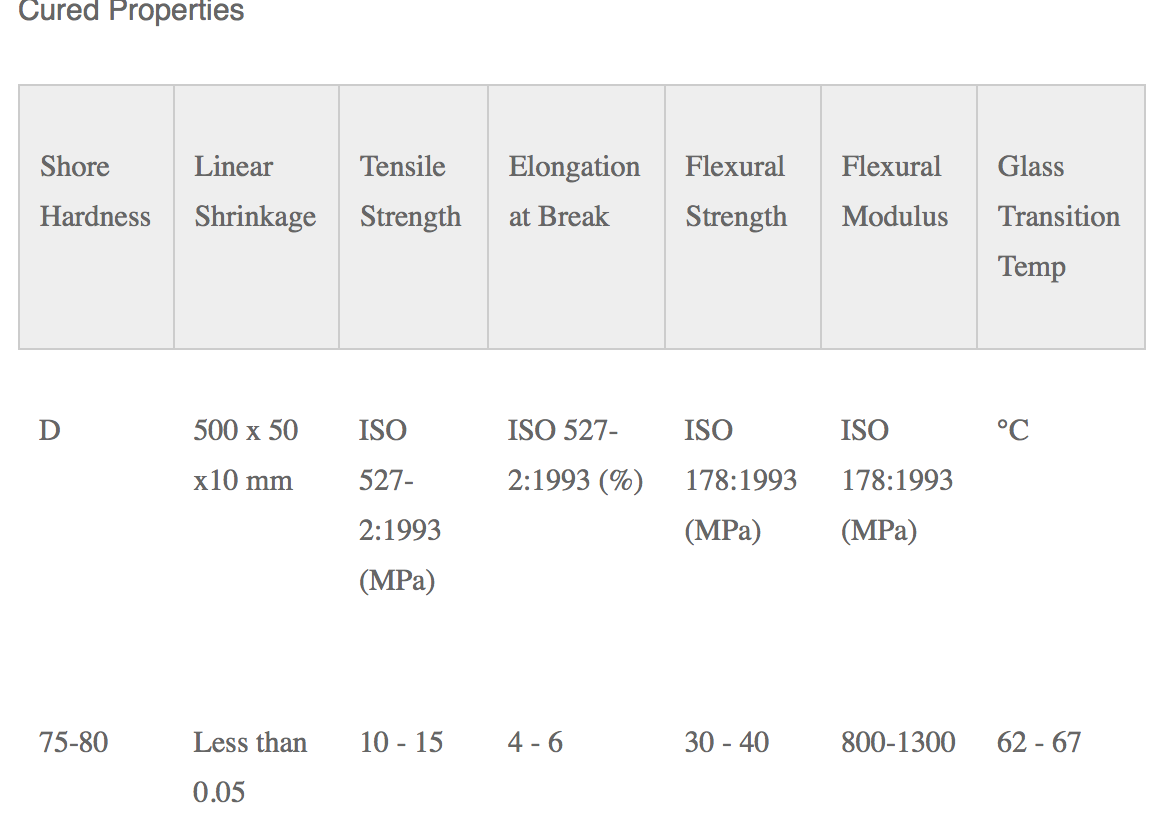
make the composities
Preparation: resin | WHITE VASELIN | sackcloth | (saw dust)(I just tried what will happen if added it on) | cloth | vacuum pump| plastic bag | safety - glass and the glove and the mask
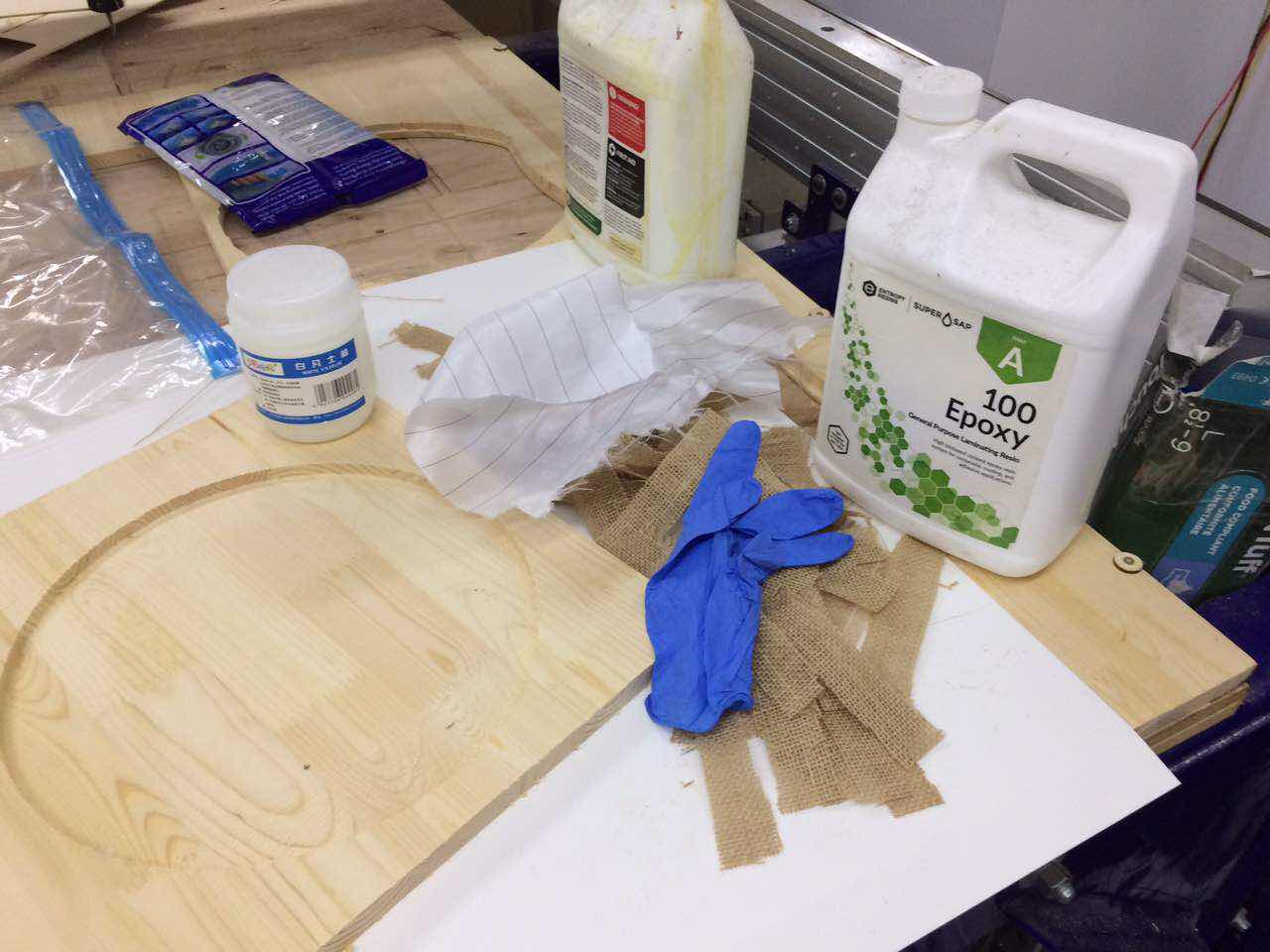
paint the WHITE VASELIN with brush to the cloth and put it on the mold
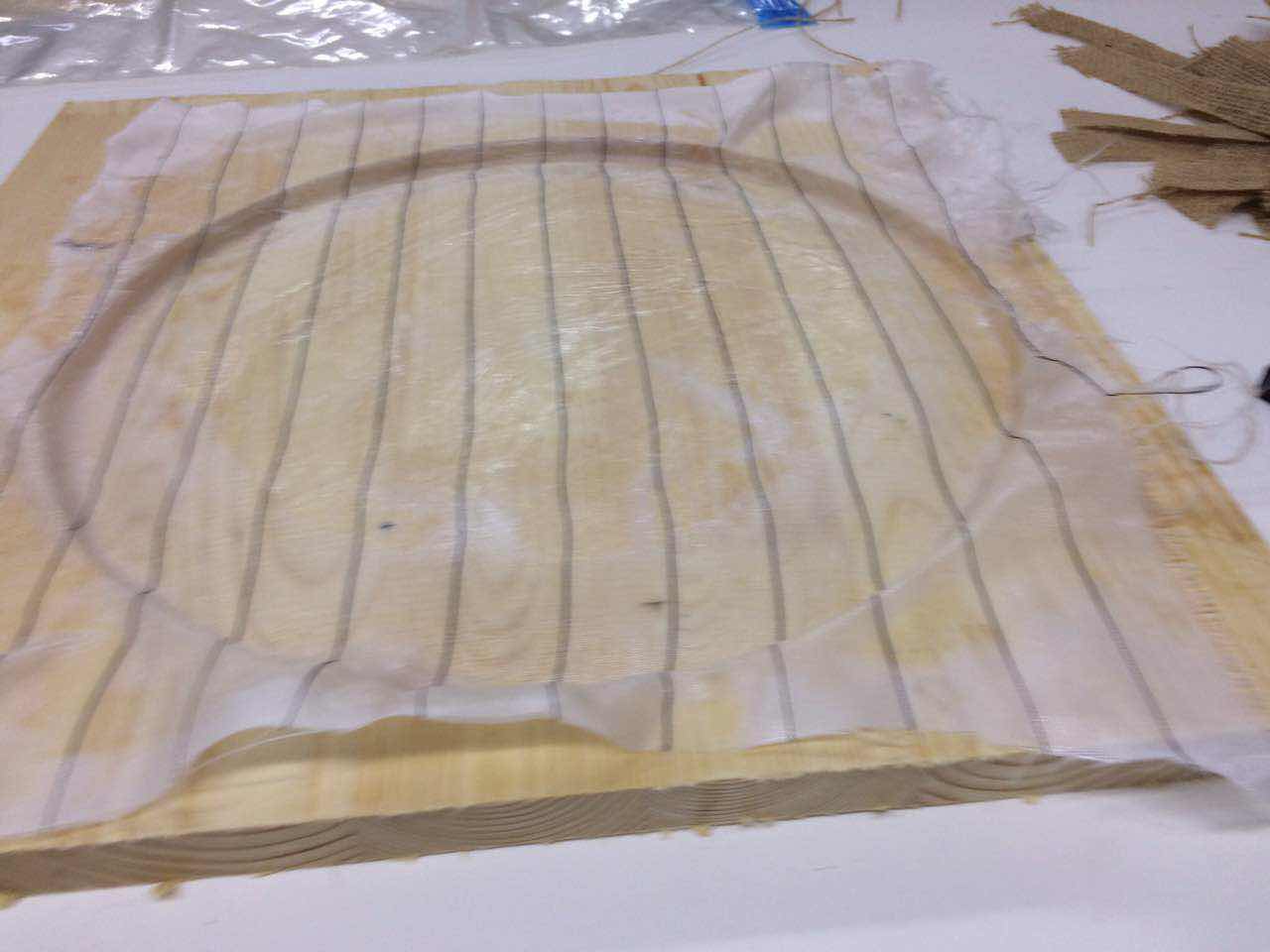
Then put the sackcloth on it (and then saw dust)
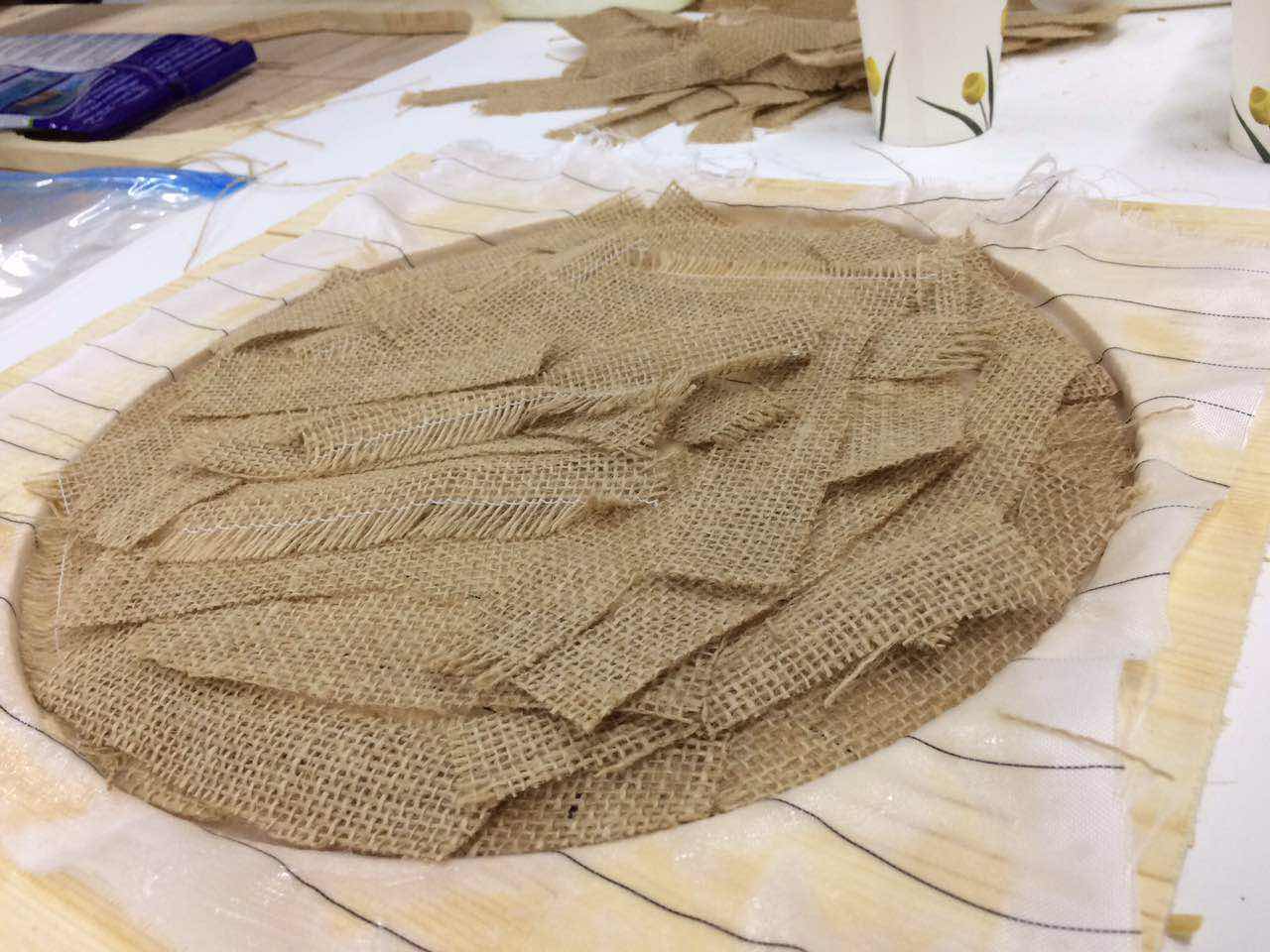
**Foremost, read the material's datasheet.
mix the resin and put it on the mold and then put the mold to the plastic bag
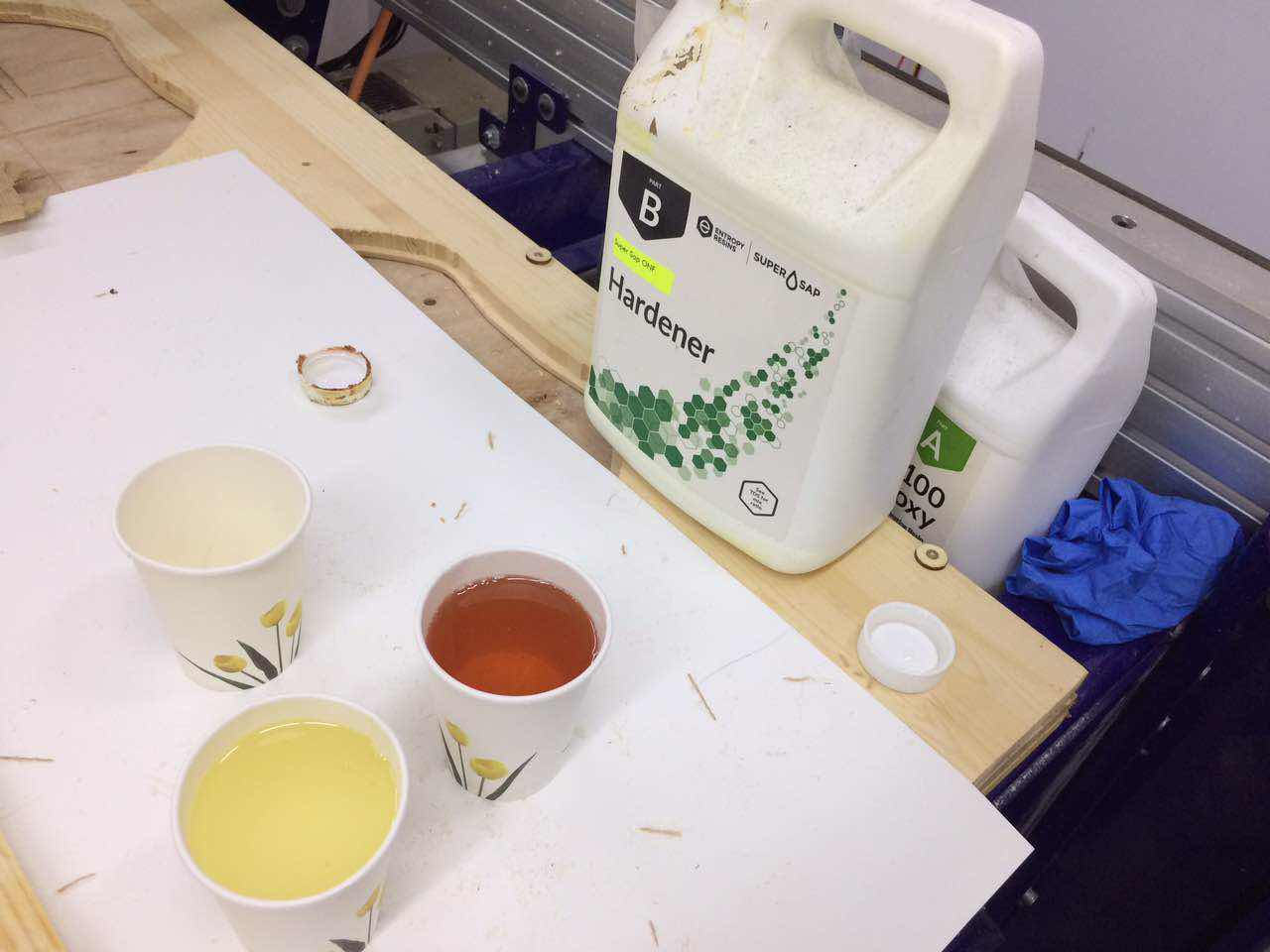
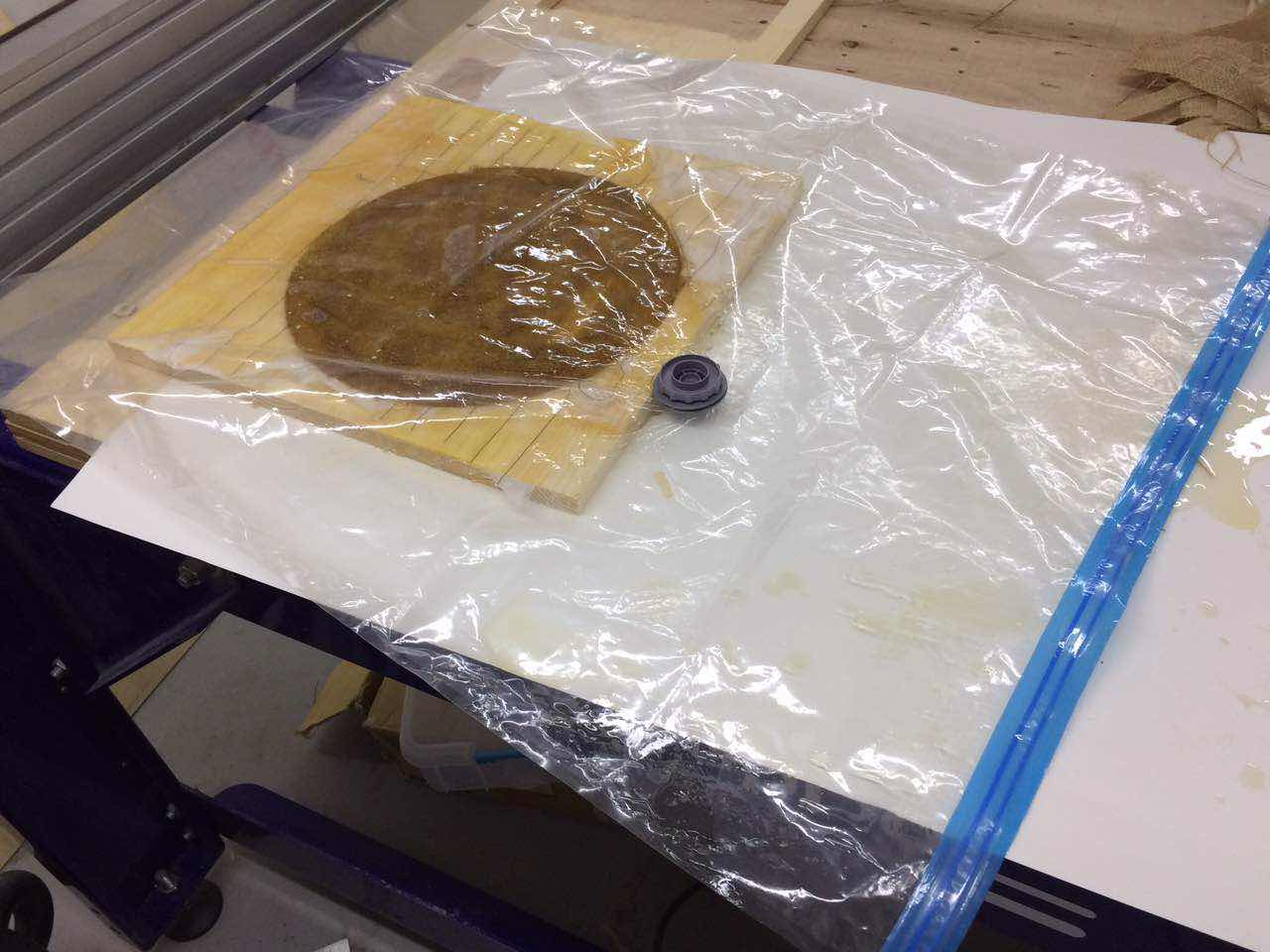
sink the air using the pump
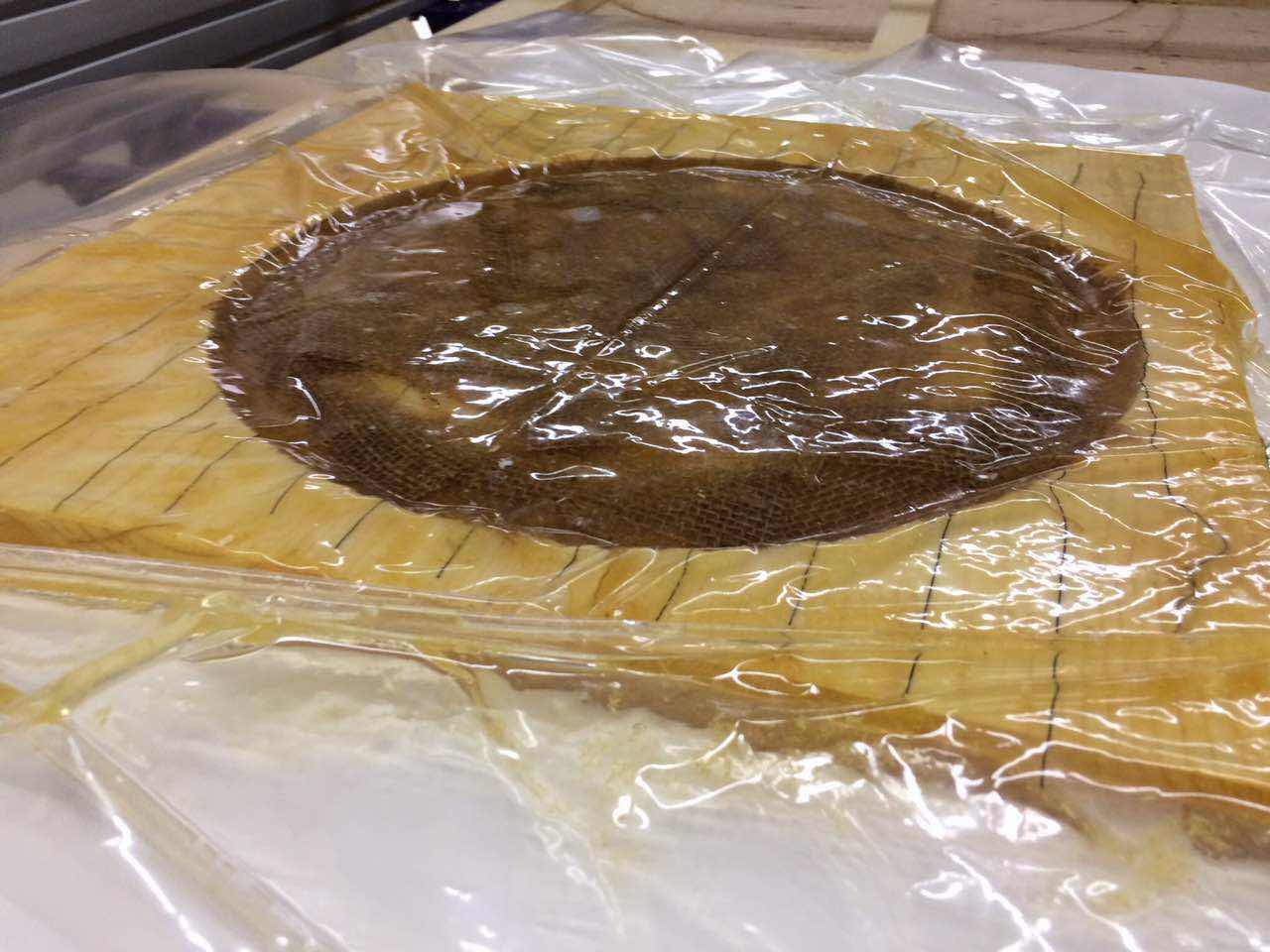
wait for the resin's drying up and get it out from mold and plastic bag
Here is what I got:
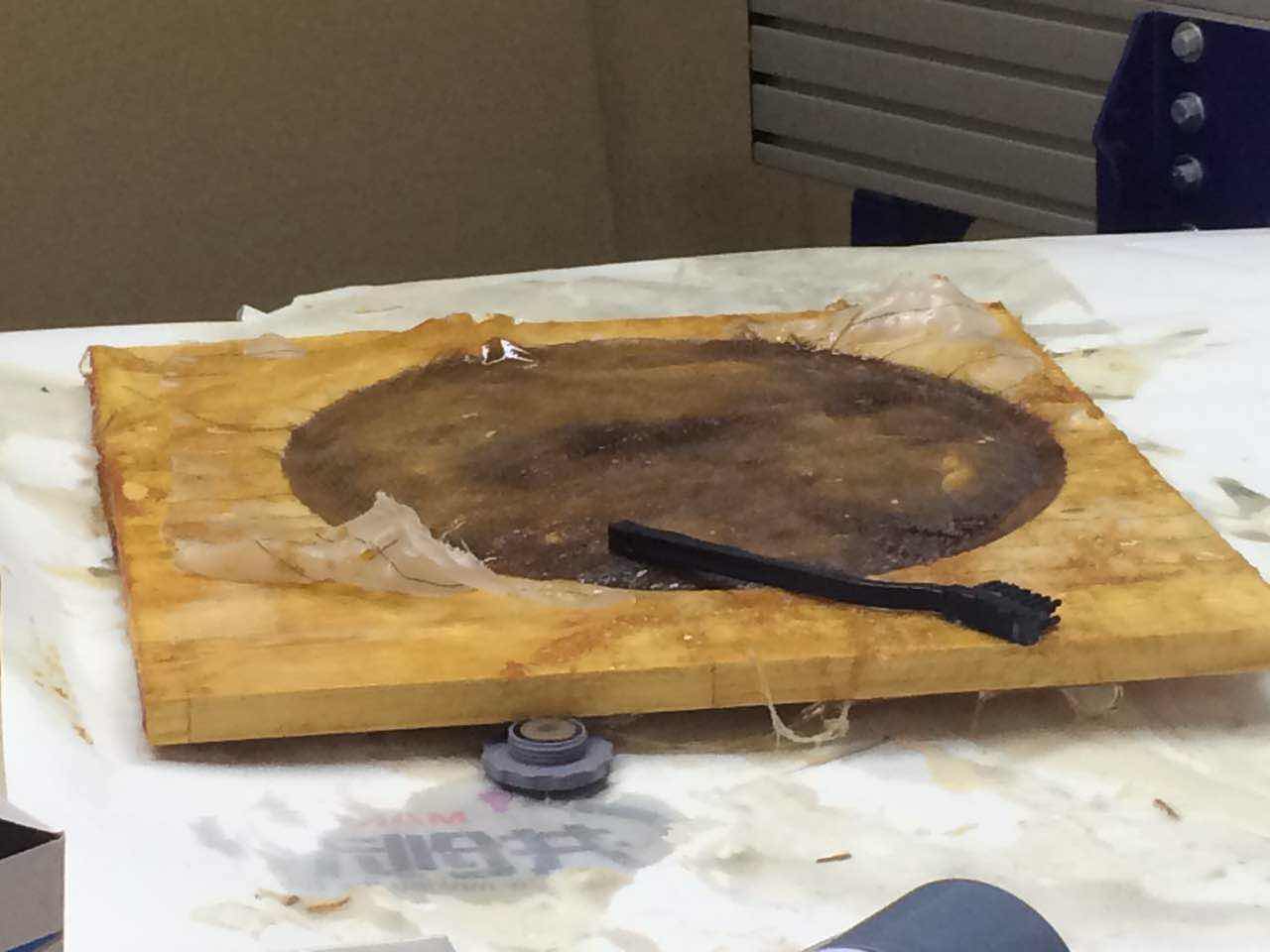
It is obvious that it failed! My instructor told me that I must mix it disproportional. Thus I need to make another one.
Try it again!
I use another types of resin and remake a mold for it.
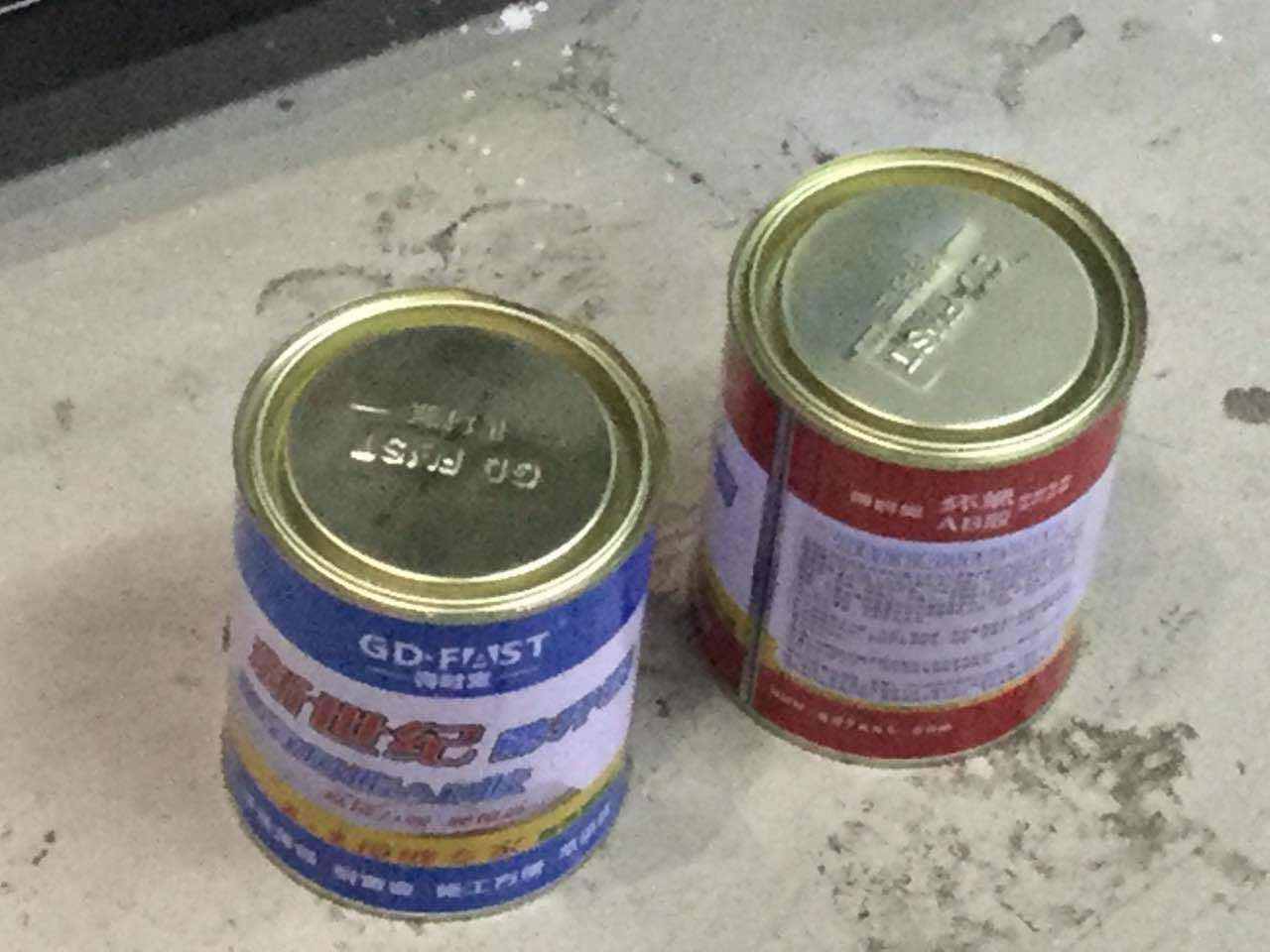
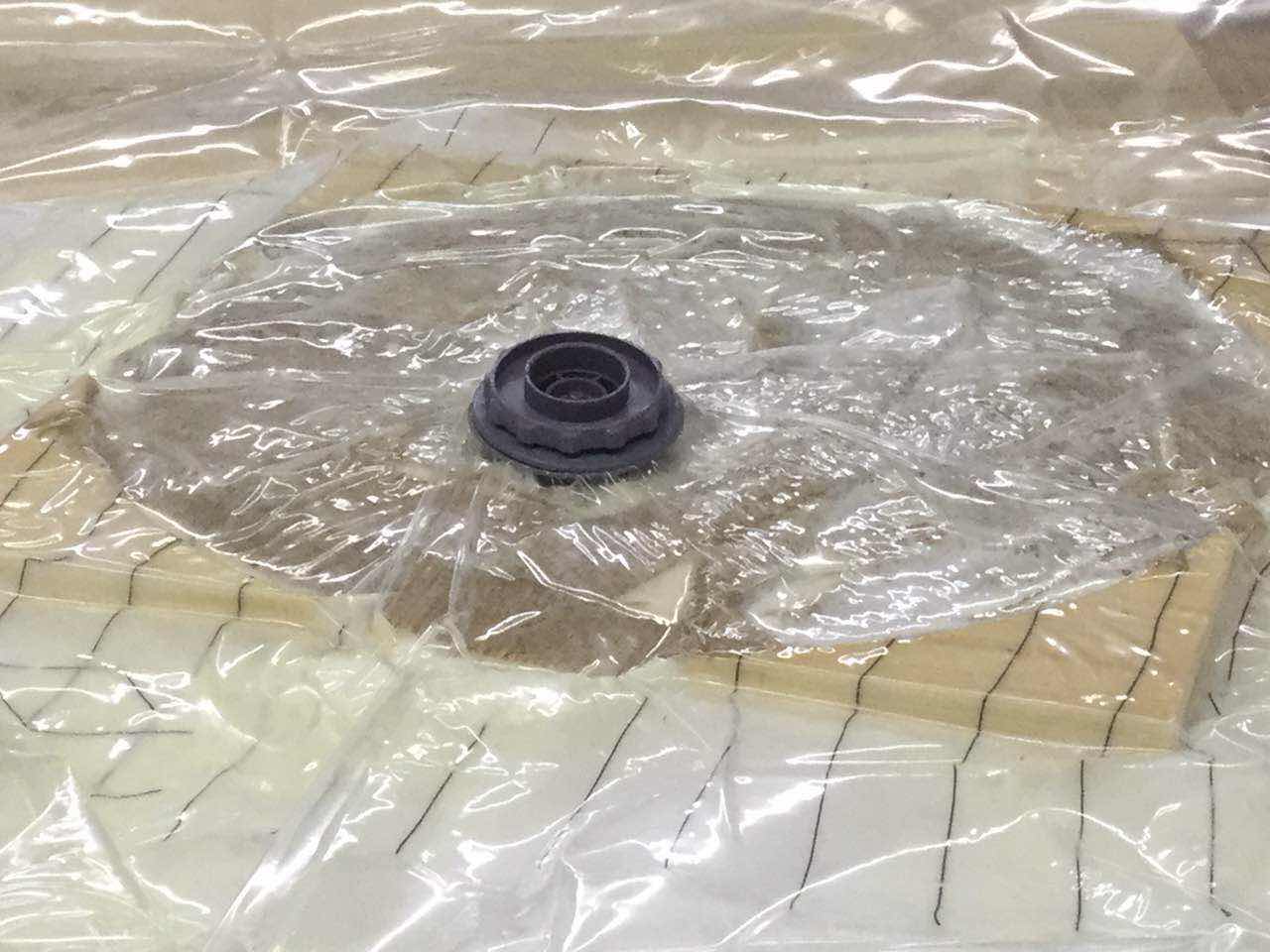
And this type of resin is solidifying in a really fast spead!
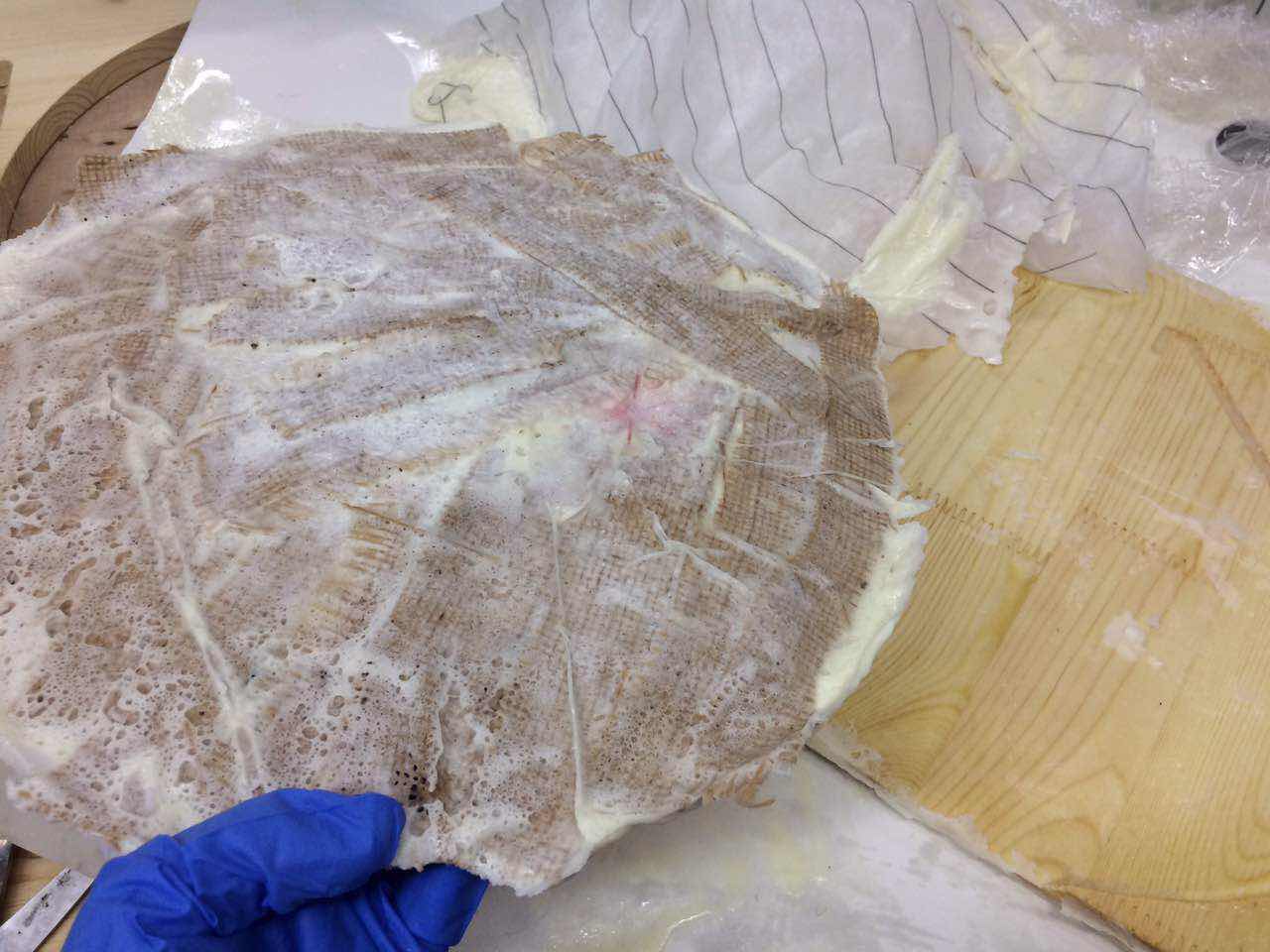
And here is a vedio of the finish work: