Assignment 14
2.5.17Composites
Objective of this weeks Assignment
I wanted to make a Table tennis shaped mould. I am very excited for this weeks assignment and I will be using both the laser cutting machine and CNC machine to complete this weeks assignment.
In the first try I will make a tennis bat shaped mould using acrylic sheets and laser cutting machine. In the second try I will be using the CNC machine and making a seat, with at least 3 glass fiber sheets.
So to kickstart, I took my tennis bat and started measuring it using a vernier calliper. I started by measuring my table tennis bat and noting down dimensions, so that I can quickly get started to design on tinker cad.
I used tinker cad to start my designing.
Step 1: Measurements and Sketches
Length = 274mm
breadth = 187mm
Height = 40mm
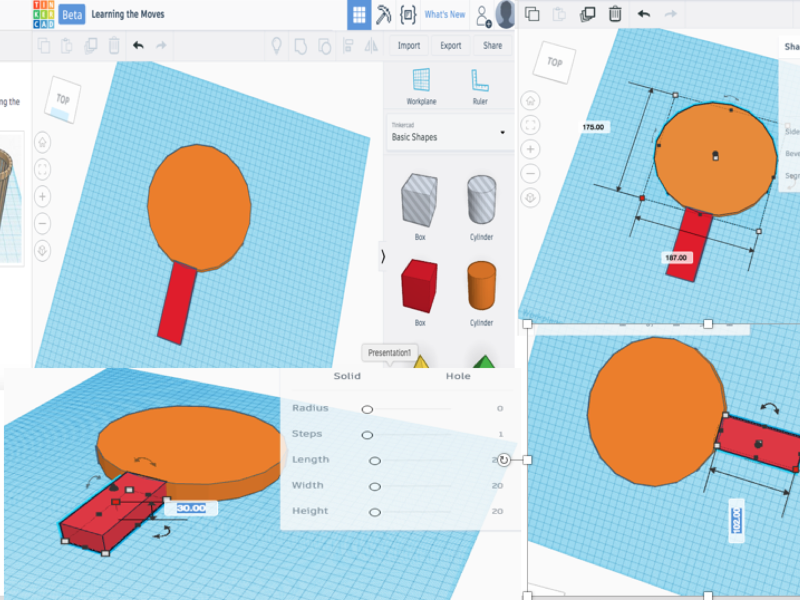
I used an 4 acrylic sheets, which was cut into the desired shape.
The purpose of making the acrylic stack was to make a casing for the tennis bat.
I measured the tennis bat and sketched a design on tinkercad. The dimension of the MDF is more than the dimension of the tennis bat so that it fits in nicely.
I extracted the .stl file
Step 2: Drafting on Tinkercad
Now I have everything in place. I booted up the SolidWorks and started drawing the shape and sizes of the things that I wanted to get machined.
I tried cutting the file on our Laser cutting machine, with Power 60 and speed 20. The cardboard was a 10mm thick cardboard.
This gave me a better idea of the shape.
I've thought of keeping the design less complicated and making the mold for composites in following way.
I've used top plane to sketch and then extruded to the required height of the case I'm aiming at which is 40mm.
I used an acrylic sheet to make my mould. I used 4 acrylic sheets of thickness 4mm each.
I used a composite : Glass fibre. Weight of the glass fibre sheet was 250gm.
I used a resin and hardner to cure the glass fiber sheet.
Resin: 65% and Hardner : 35%
The hardner and resin when mixed, cause an exothermic reaction.
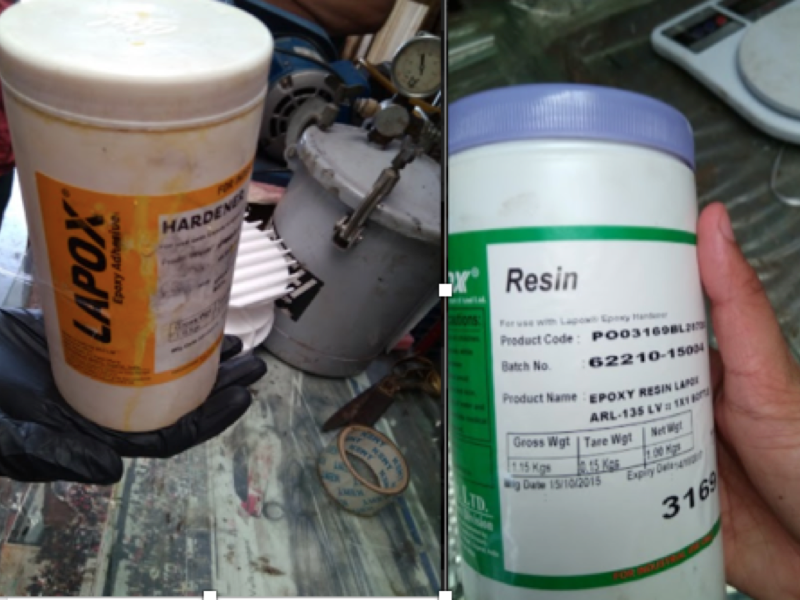
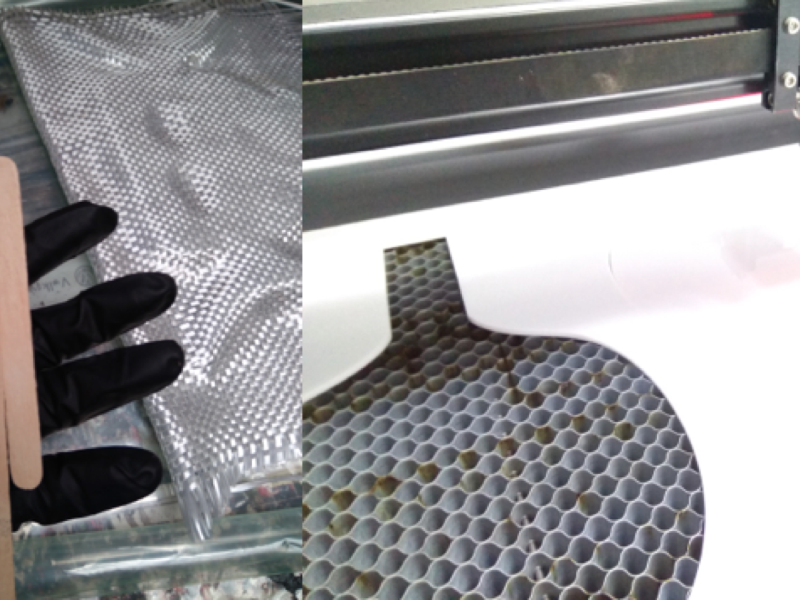
The quantity of resin used was ((weight of the 2 glass fiber sheets)250 / (formula from data sheet)132 ) * 100 = 189.39 gm
Weight of the glass fiber - Weight of resin used = weight of hardner used
250gm - 189gm = 60gm of Hardner.
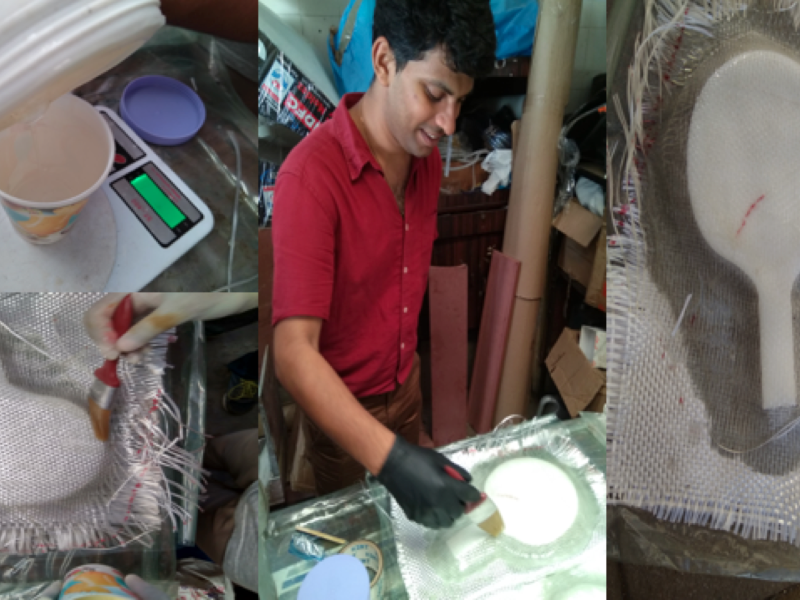
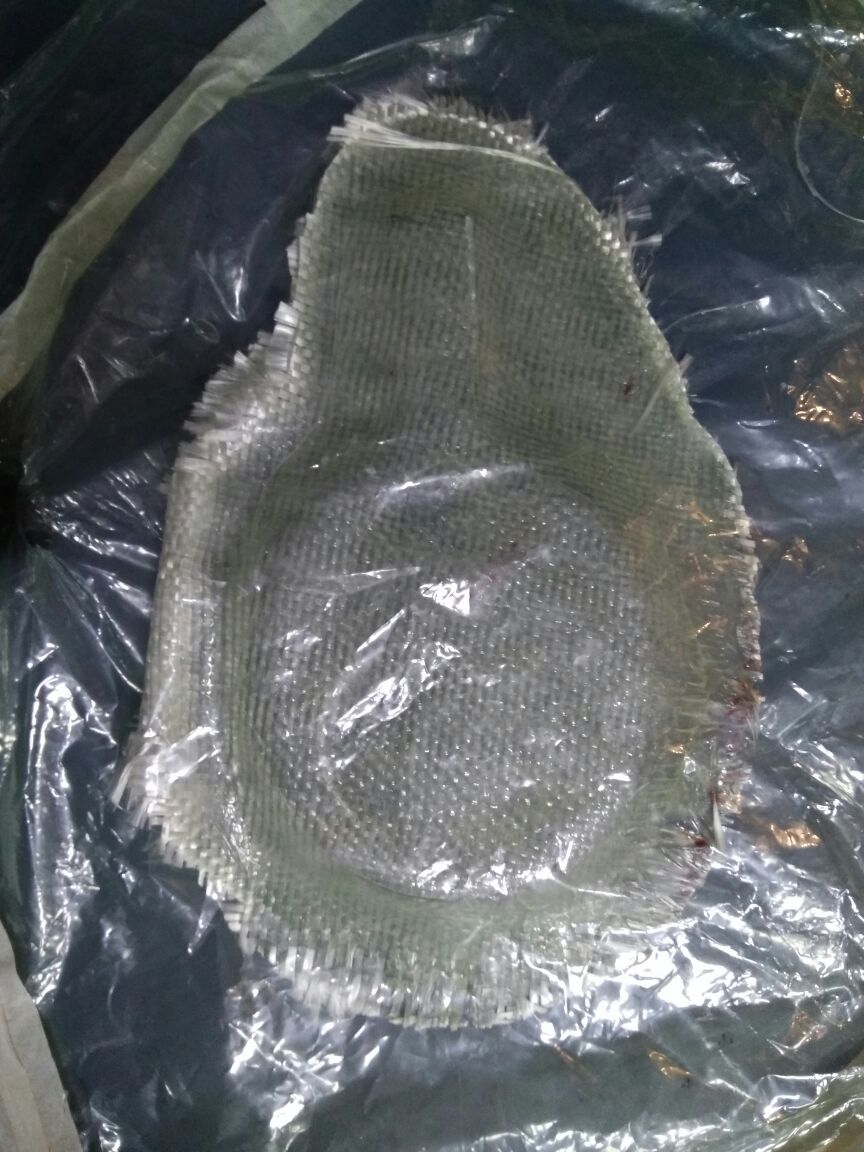
Vacuum Infusion
But, wait now I have to drain the excessive amount of resin left between the layer. Vacuum bagging does the same and it make the layer to get properly shaped. I used the vacuum pump to suck the air and epoxy out and regularly turned on and off the vacuum pump to avoid any mishaps. The pressure difference between the outside and inside pressure makes layers to take shape of the mold and helps to drains excess amount of resin from the layer.
To make the vacuum bag I cut the piece of vacuum bag film the size should enough to wrap the entire mold and space to stick ends together. Then I took the sealant and added it on each edge of the film and then kept small opening for vacuum cleaner hose to go in. then I kept the layered mold inside the bag, and used a piece of flat wood and pressed the sealant to ensure there's no air gap remained. It is important because I don't want to any of the leakage takes place.
As I've seen in several tutorials the pressure should be around 25psi. I used clamps to tighten the glassfiber sheet on the acrylic mould, so that it takes the correct shape.
Removing the mold
After vacuum bagging I applied pressure as mentioned above, and waited almost for 7 hours to cure the resin. I kept it in the sun. The resin was totally cured and the dried completely. Then with spatula I took the layer apart from the mold and then I stripped off the excess amount of composite using the scissors.
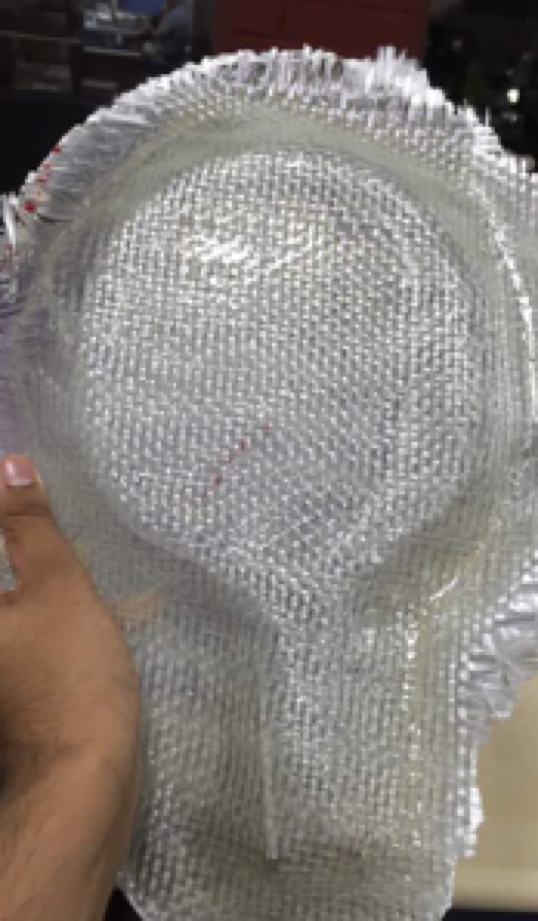
Using above mentioned procedure I made one composite object.
I wanted to try the composite assignment again using a MDF mould made on our CNC machine.
I designed a seat on solid works. The solid works design files are as shown below.
I used the line tool. The distance between the lines are 523mm and height of the block is 50mm.
The desired design is of a trapezium shape with one side of 200mm and another side of 63mm.
The two sides are connected by splines.
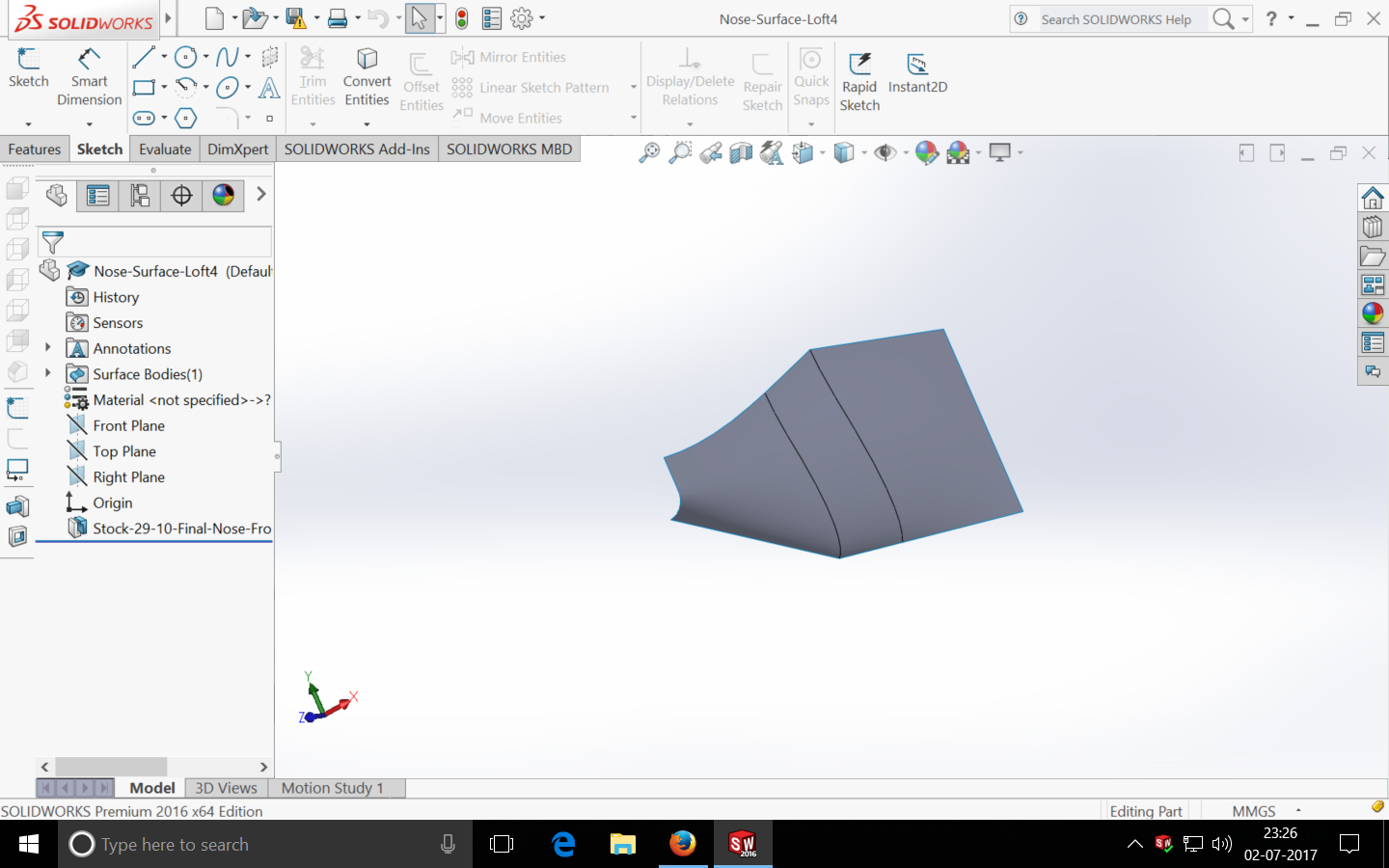
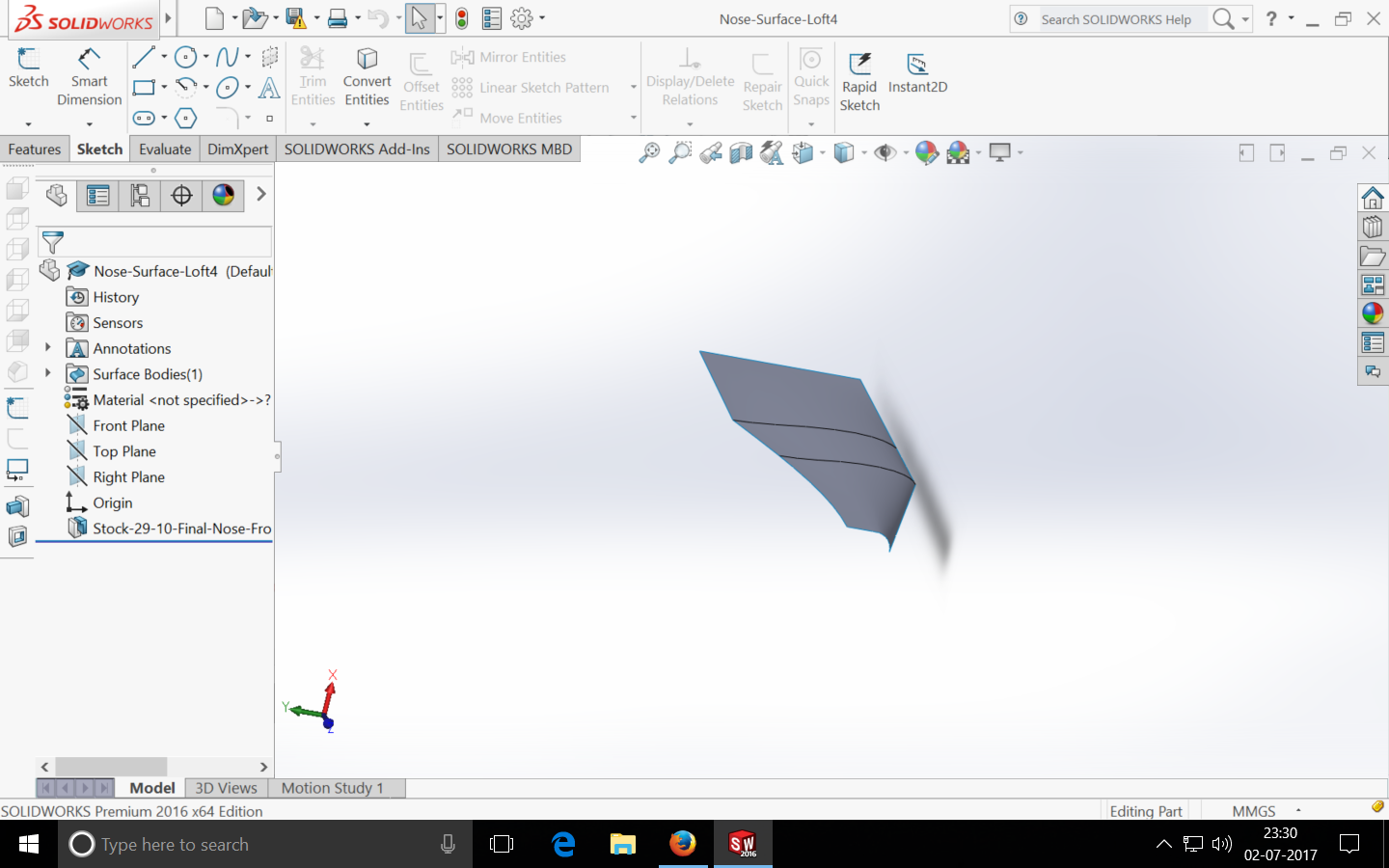
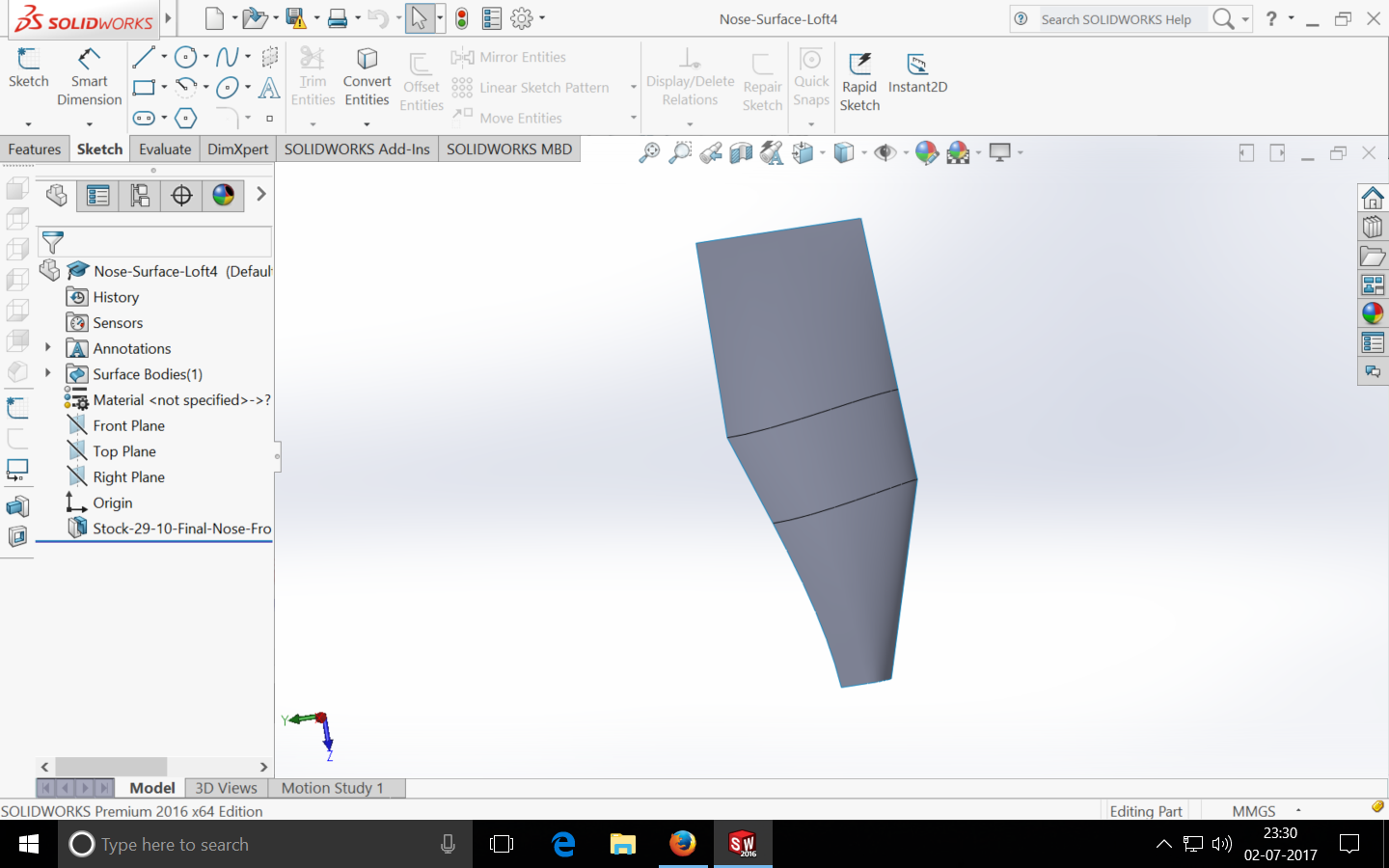
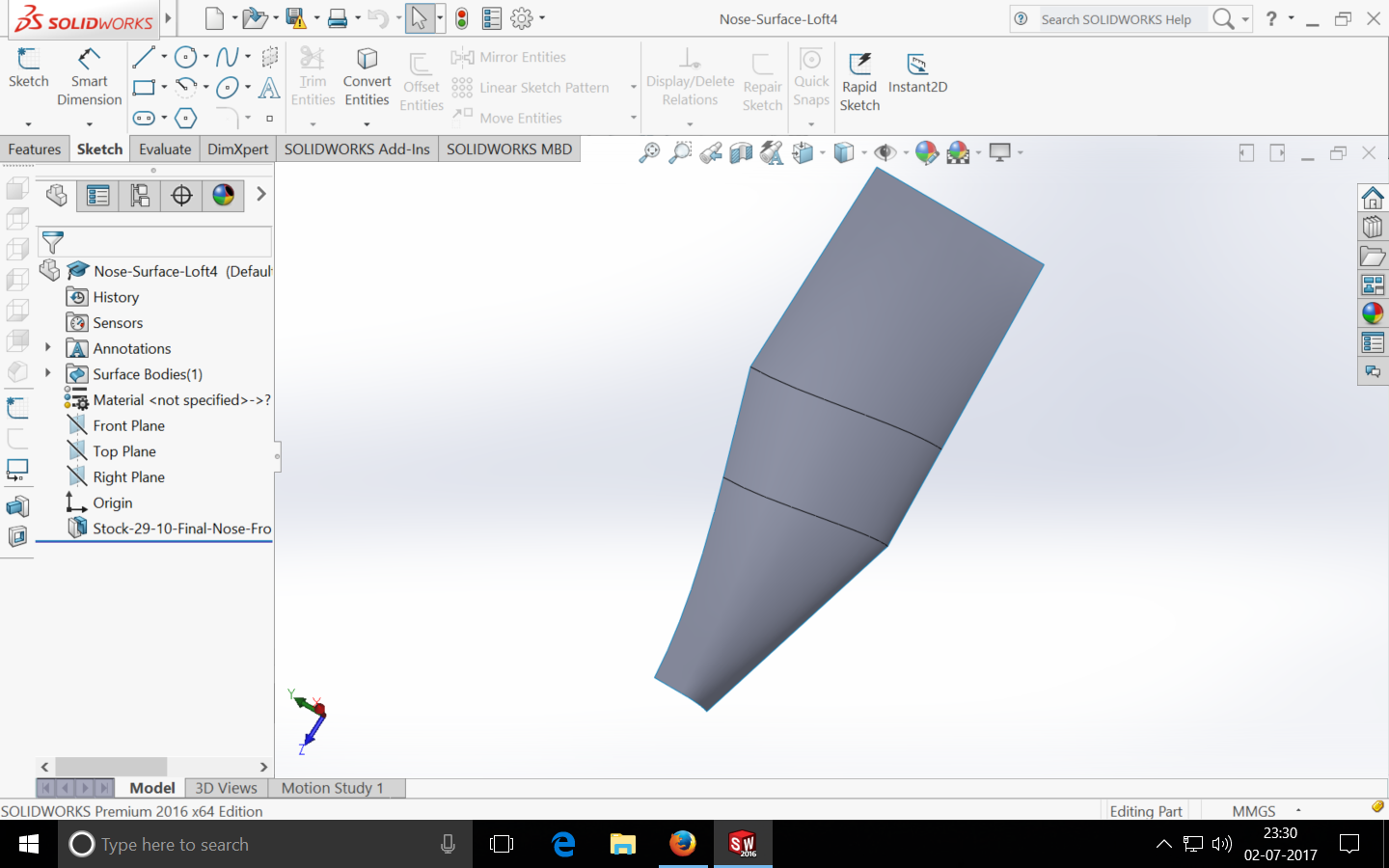
The art cam file and the machine parameters are listed below:
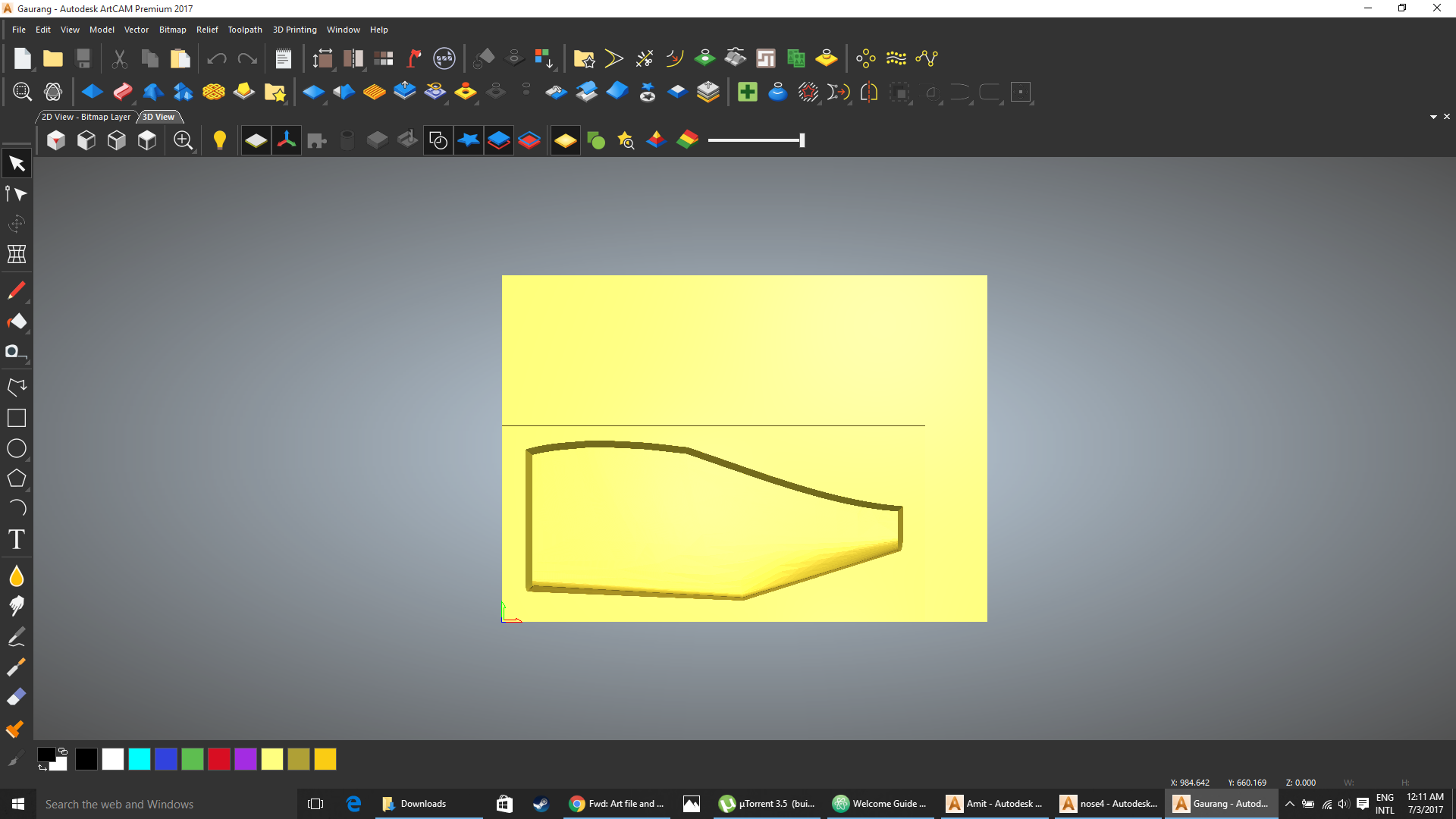
I used 1/4th straight cut bit at the following parameters:
- Spindle Speed:13000 r.p.m
- Feed Rate:1 inch/sec
- Plunge Rate:1.5 inch/sec
You can download the files from the green links below:
Downloadable file: seat.SLDPRT
Downloadable file: seatwall.mmg
Downloadable file: seat.mmg
Downloadable file: seat.art
I used a long sheet of glass fiber fabric. I referred the data sheet of the hardner and the resin and did the calculation accordingly.
- Weight of the fabric = 100gm
- Quantity of Resin = 75gm
- Quantity of Hardner = 25gm
- It requires around 6 hours to get cured. Th exo thermic reaction between the Hardner and Resin is visible approximately within 10mins.
I applied a sealer coat, primer coating: MechesterTM 9000G-PM and High gloss Coat: Mechster 8100(FC) on the block. The Primer coating and the high gloss coating is manufactured by Mechemco resins pvt. ltd.
Also, the resign and hardner details are mentioned below, they are manufactured by Atul pvt ltd. - Resin: Atul ARL135 LV - Hardner: ATUL AH 337
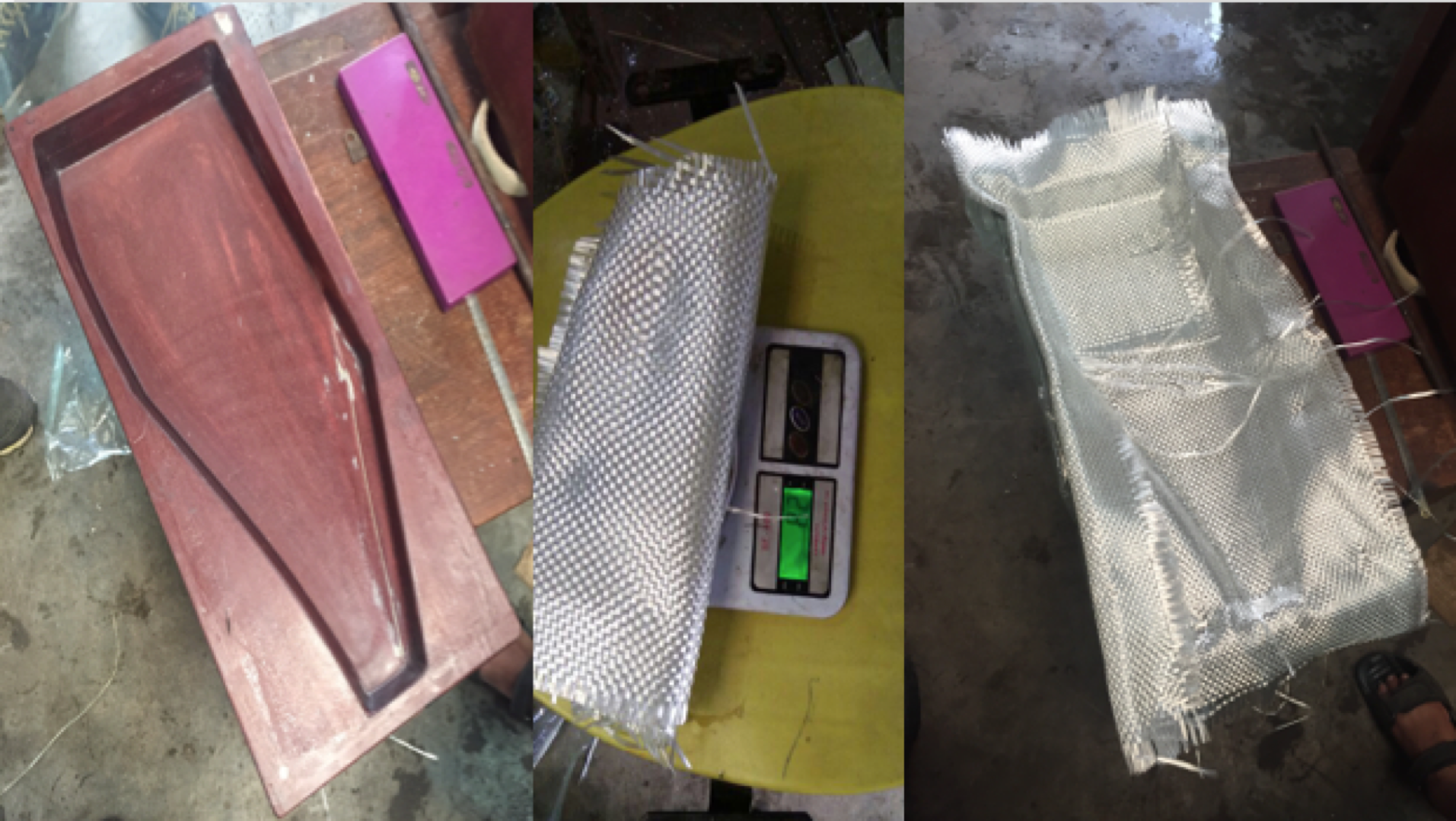
Knowing more about Vacuum Infusion
I wanted to make a simple seat using a glass fiber sheet. I used the vacuum infusion technique for the same. The technique is time consuming and has to be done with perfection to avoid any irregularities or mishaps. In its simplest form the vacuum process can be broken down into the following stages:
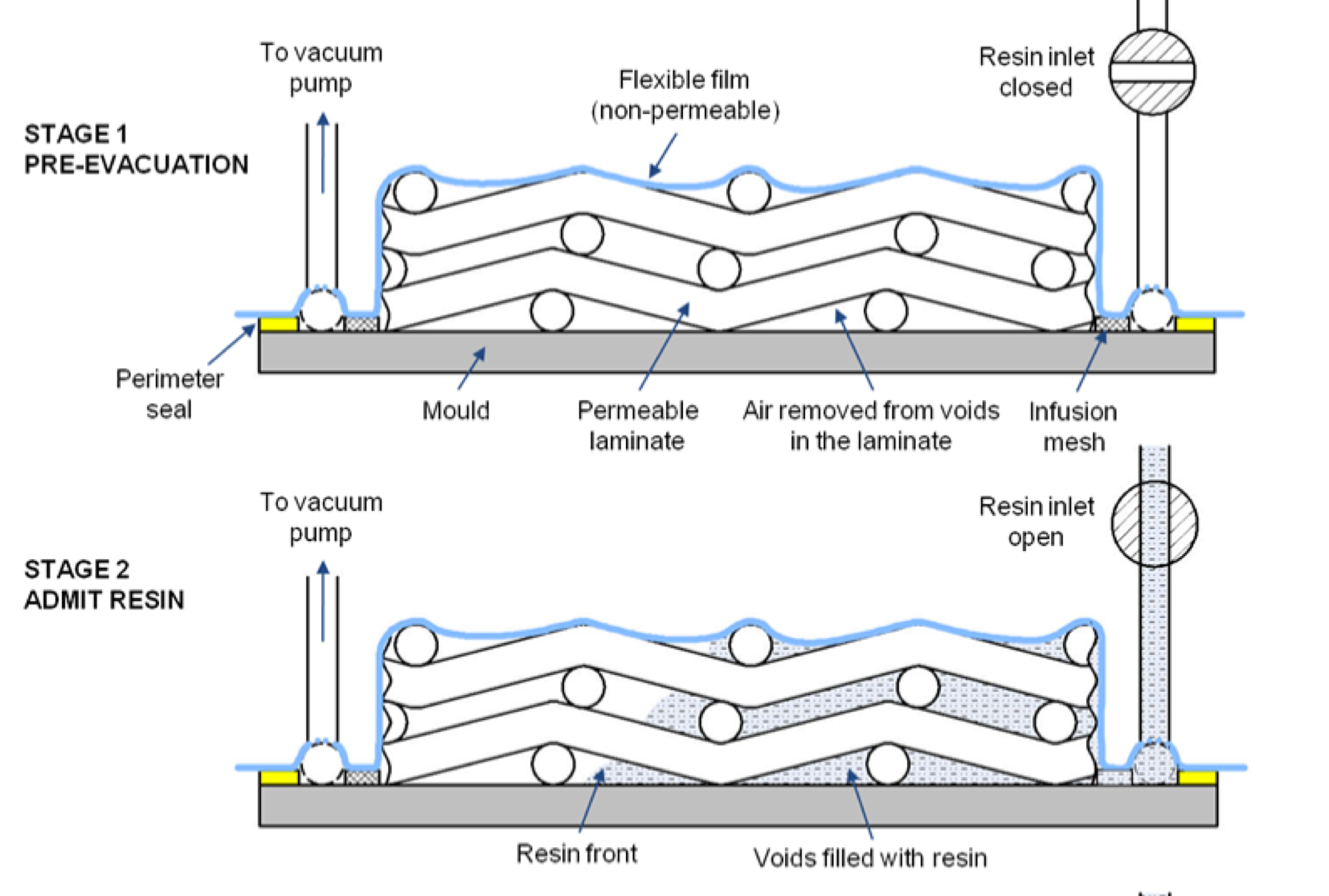
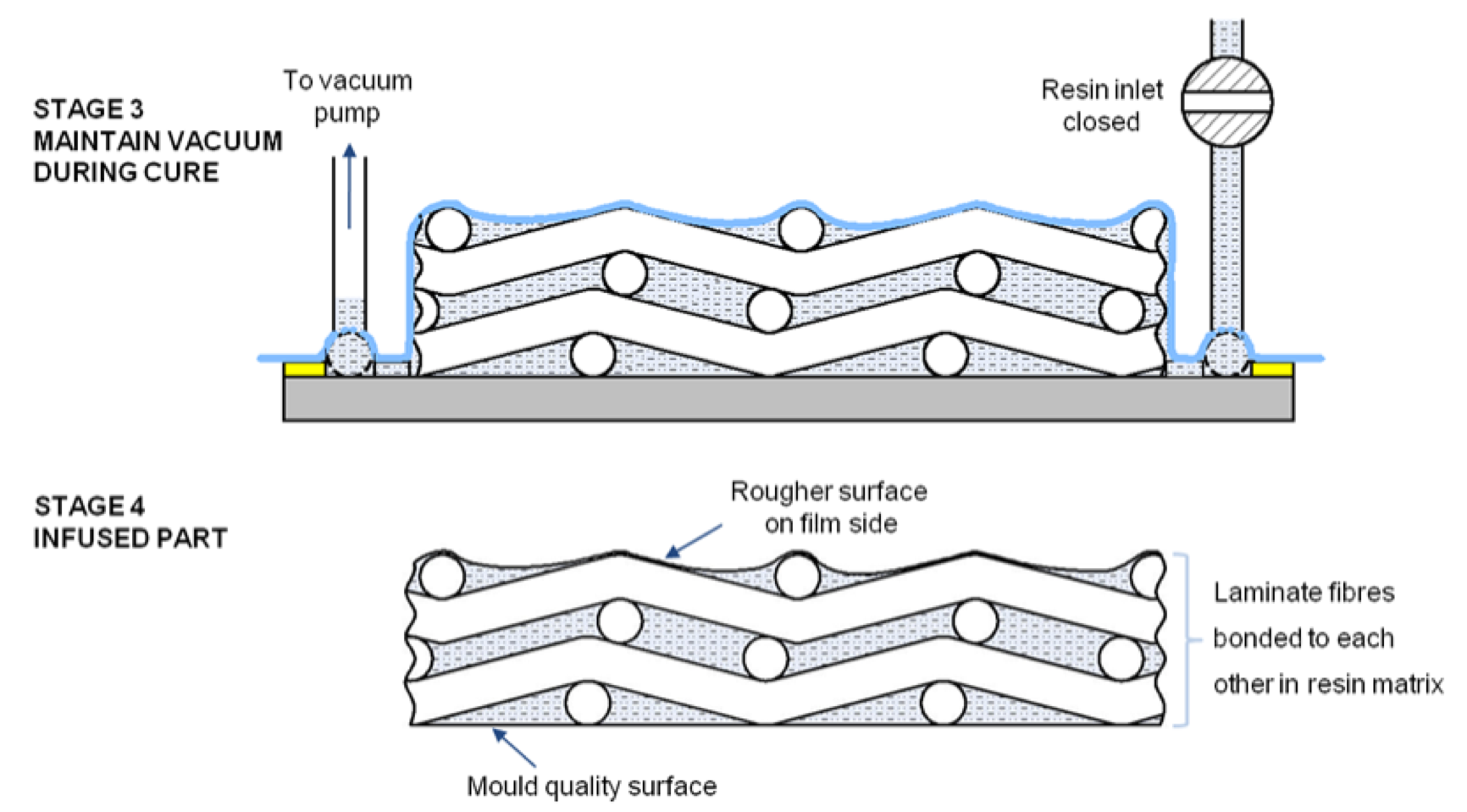
Infusion is a relatively slow manufacturing process. It is usually not worth considering for applications requiring high production rates where another manufacturing solution is feasible.
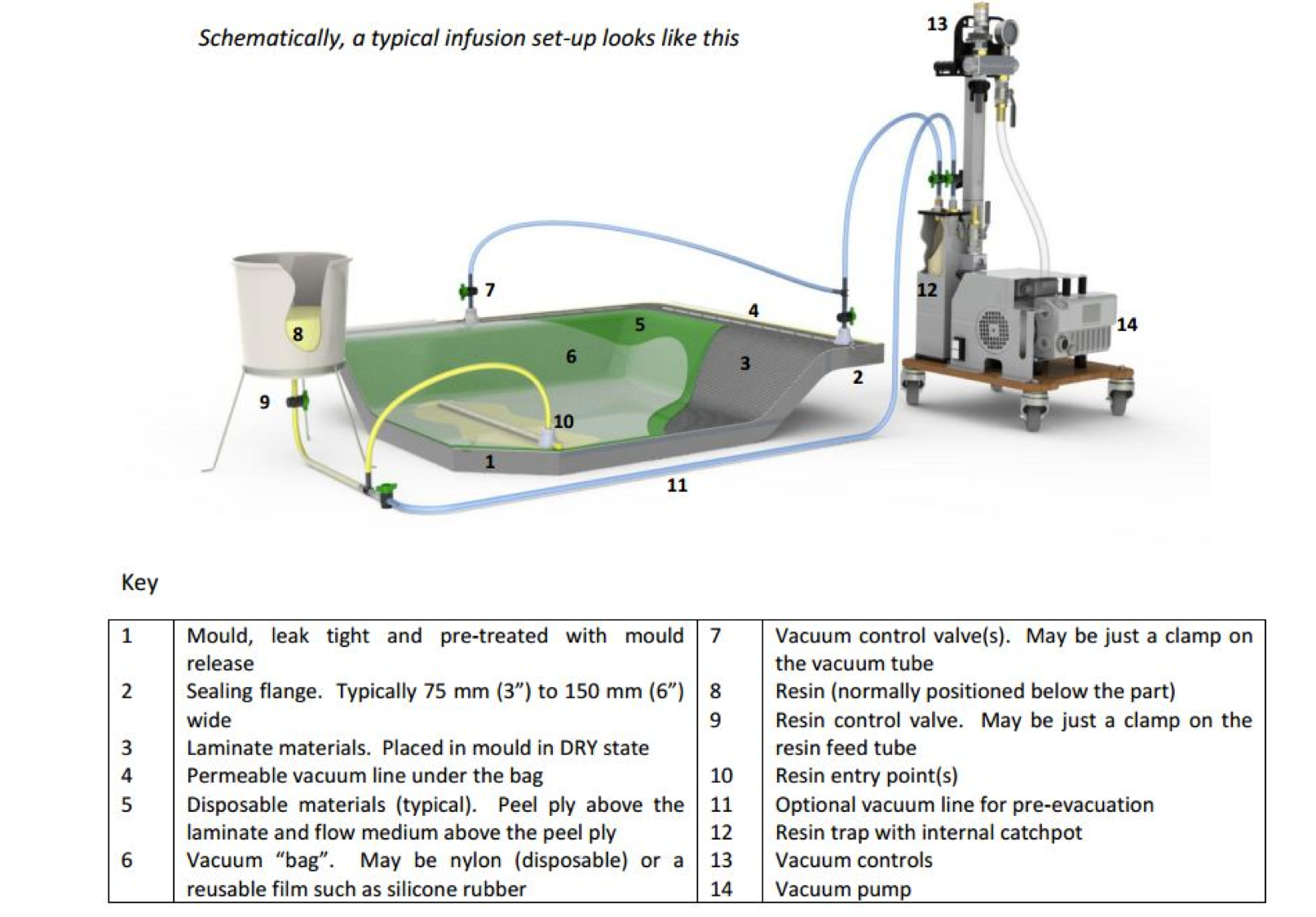
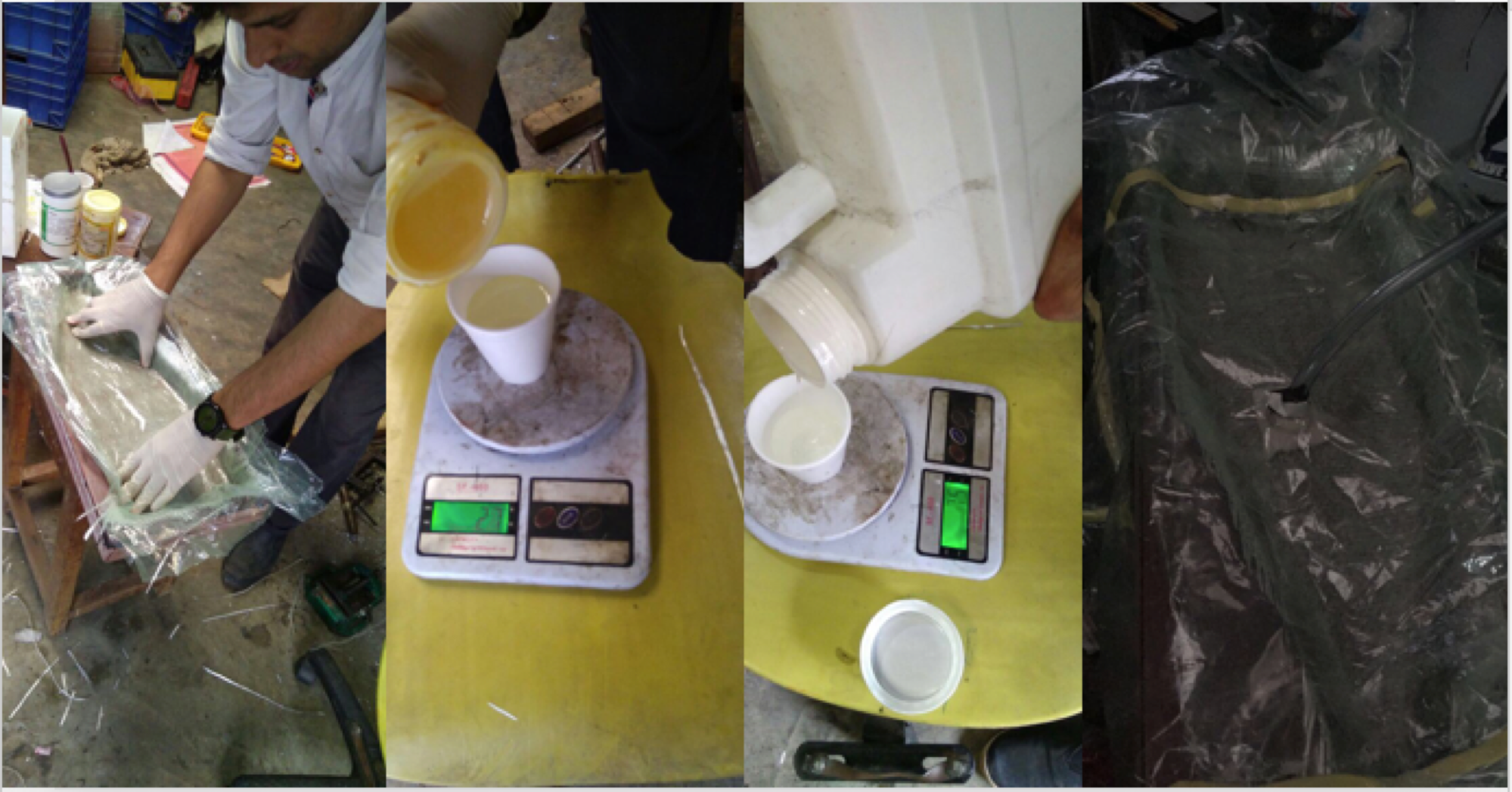
A key part of the process is the evacuation, or removal, of the air from the porous material prior to admitting the resin. The air needs to be removed from the porous material to allow the resin to take its place.
I cut the remaining glass fiber sheet using a pair of scissors.
References:
- What are composites?
- Vacuum Infusion Technique