Composites
Assignment
design and fabricate a 3D mold (~ft2), and produce a fiber composite part in it
Plan
Since there is no epoxy in our lab we have to buy it from outside. So I decided to make the mould in advance and will make the fiber composite after we buy it . I wanted a simple and useful design in a medium size. It is mandatory that it should not be very small and there is no enough epoxy for a bigger design. Finally I decided to make a "Vishari" (Hand fan). I have a an image below.
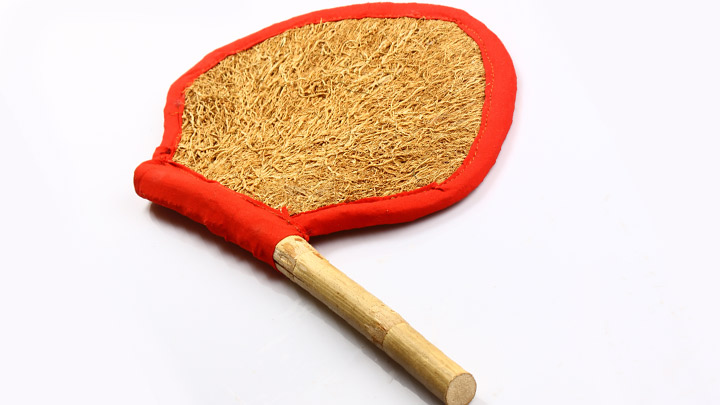
Design
I made a 3D design in Rhino (as usual :P). I don't have much screen shots for the design works since I always forget about the screen shot while designing.
I was warned by our instructor saying this look like a 2D mould and it should be a 3D mould. But this is 3D mould with difference in heights at different points. So i have to prove it by showing some snaps :/
Download the stl file here
Making the Mould
I am planning to make the mould in Shopbot. For 3D works we use Partworks3D for shopbot.
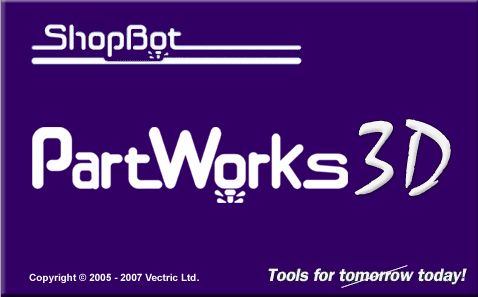
I have already explained using partworks in Moulding and casting week, so i m not going deeper now.
The first step is opening the stl file in partworks. Orient it and check the size.
Next step is to give the material size and margins
If you want to give a roughing tool path you can give. In some designs there will be no need of a roughing tool path, we can directly go to finishing tool path.
We have to select the bit and bit parameters like feedrate , spindle speed etc. The parameters I chose is shown in the image below
Once we do all these, we can save it as the .sbp file and start cutting using shopbot.
Making the Composite
I have told before, there is no epoxy in our fablab inventory. So we have to buy it locally.
This is the epoxy I used
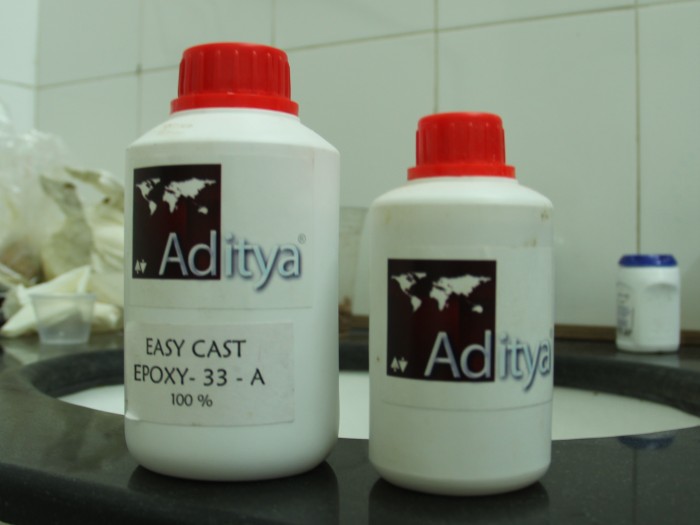
The fiber I used is Jute fibers.
I tried the putting some jute in the mould and estimated the amount and shape .
Then I started mixing the epoxy. The ratio for mixing is 2:1 by weight. The Part A is should be double the weight of the Part A. I took two glasses and poured to it. I took 50g Part A and 25g Part B, total of 75g.
I put the jute in the mixed epoxy
Then I placed the jute in the mould and poured the remaining epoxy to the mould.
This jute has many layer internally, but it has less finishing. So I took another soft cloth material which is in the fablab inventory and cut it in the shape of mould. I put it as the top layer and poured little more epoxy to it. Now I have to put some weight on it. What i did is i placed another piece of wood above the mould and clamped it using the clamps.
I kept it like this for a full night and opened it in the next day morning.
It was not properly rigid at some parts , so I tried baking it for some time. I put it at 150 fahrenheit for 10 minutes. When I checked it was becoming more stronger. SO i repeat the same again.
Here is the Final "Vishari:
Downloads Rhino file, .stl file