Composites
Drawing the mold in Fusion 360
Milling the mold
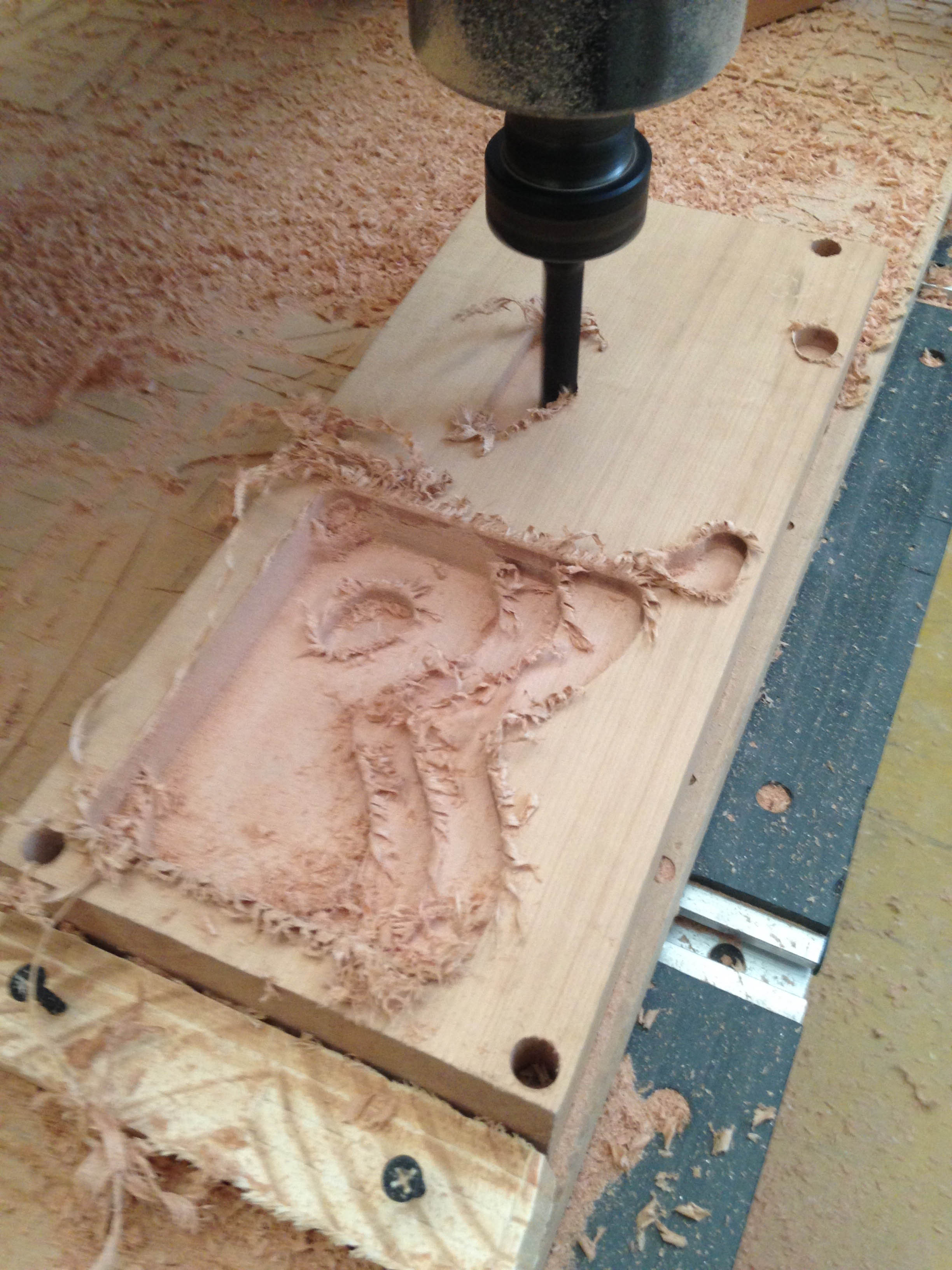
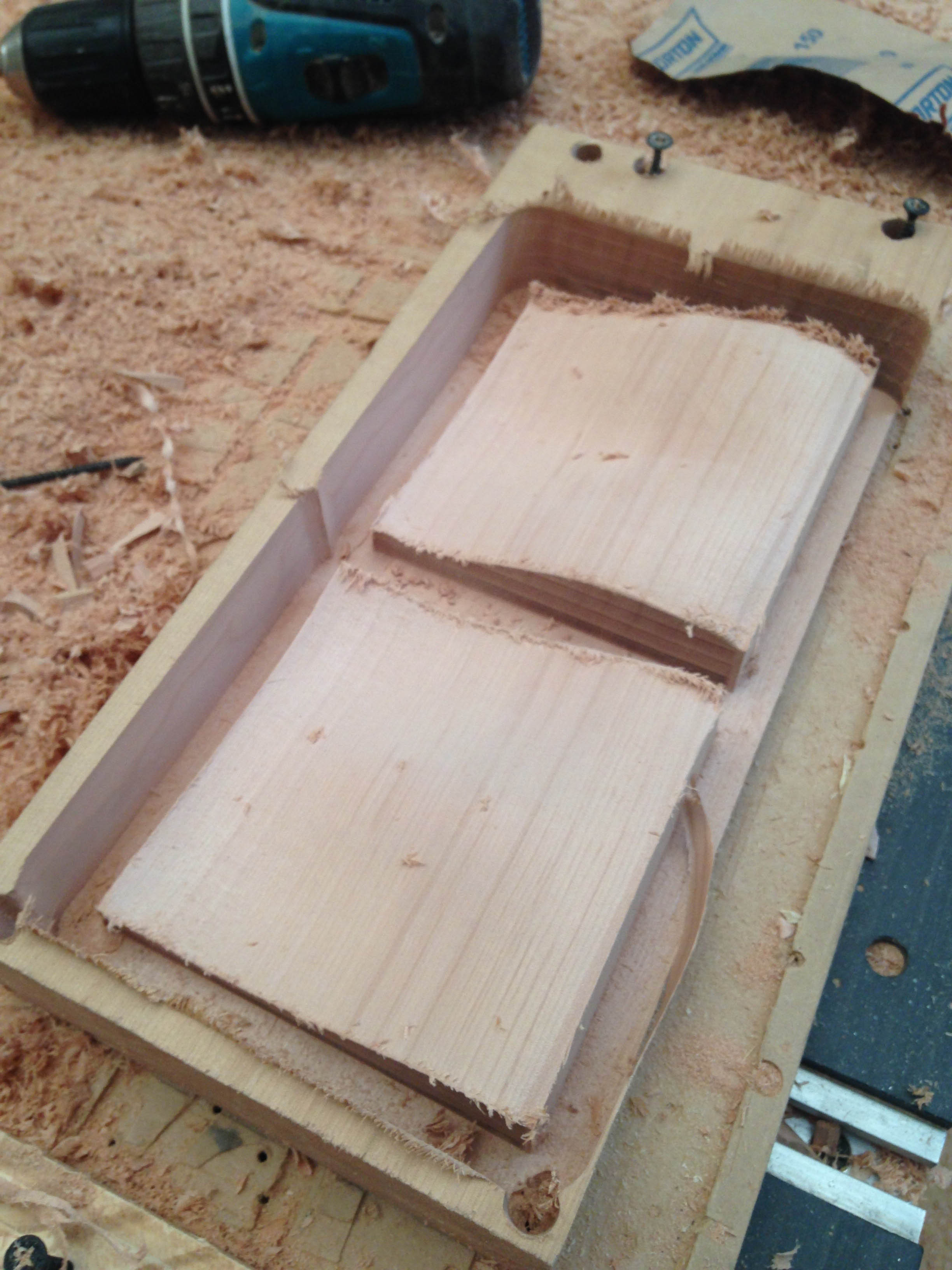
Preparing the mold and fibers
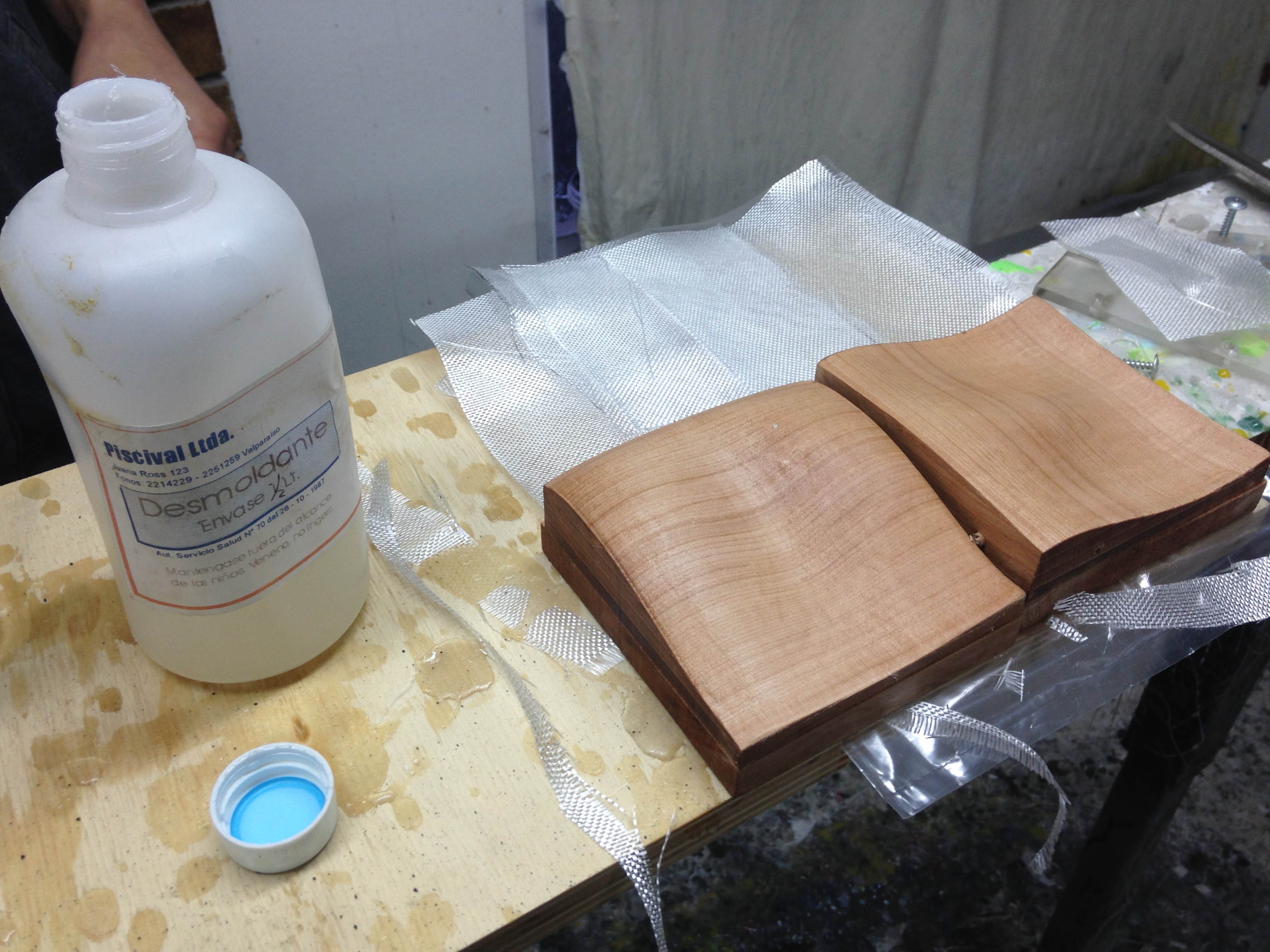
After having sanding about 30 minutes, I used a release agent for wood. I applied about 6 layers with a break of 15 minutes between each application.
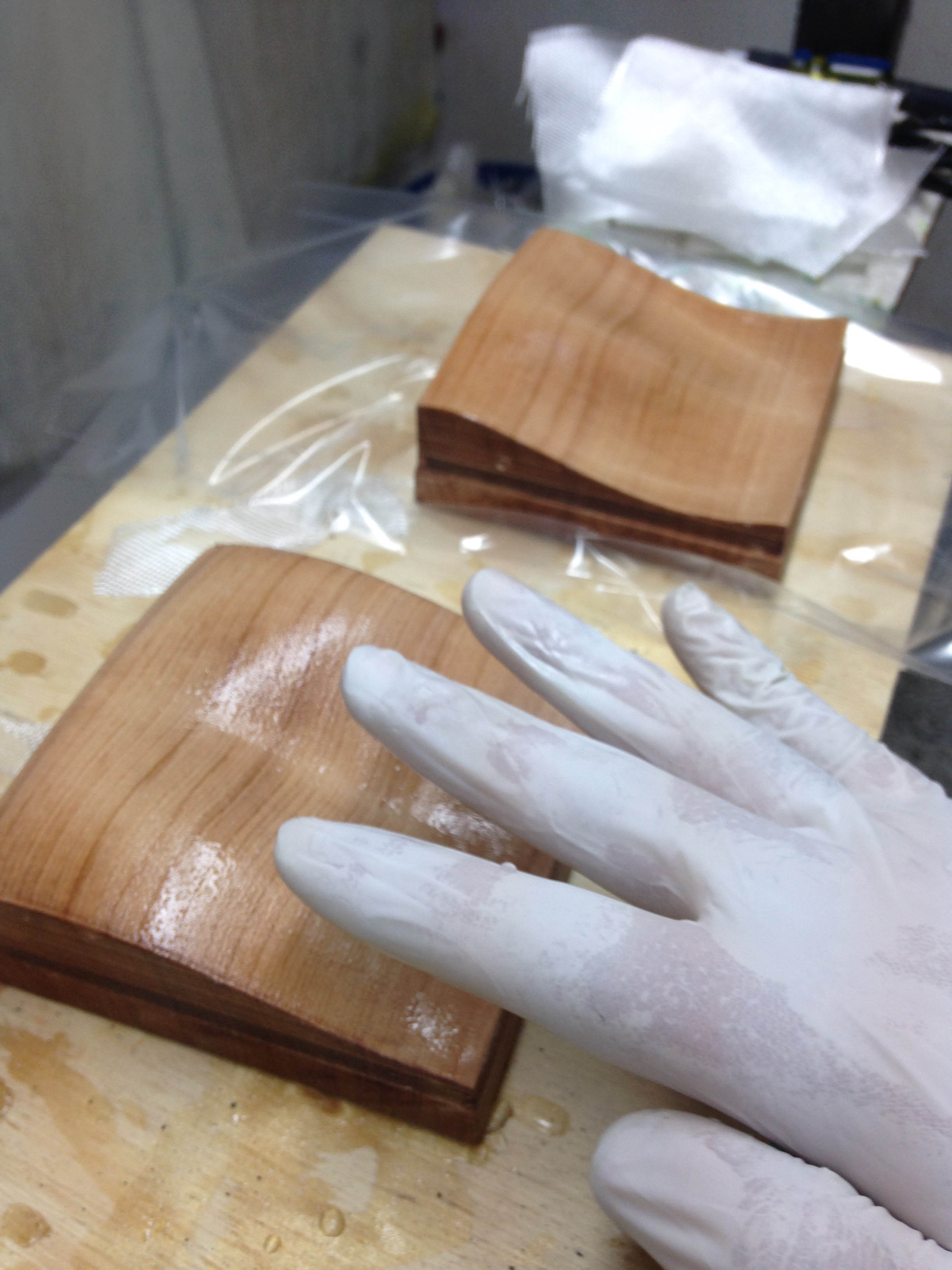
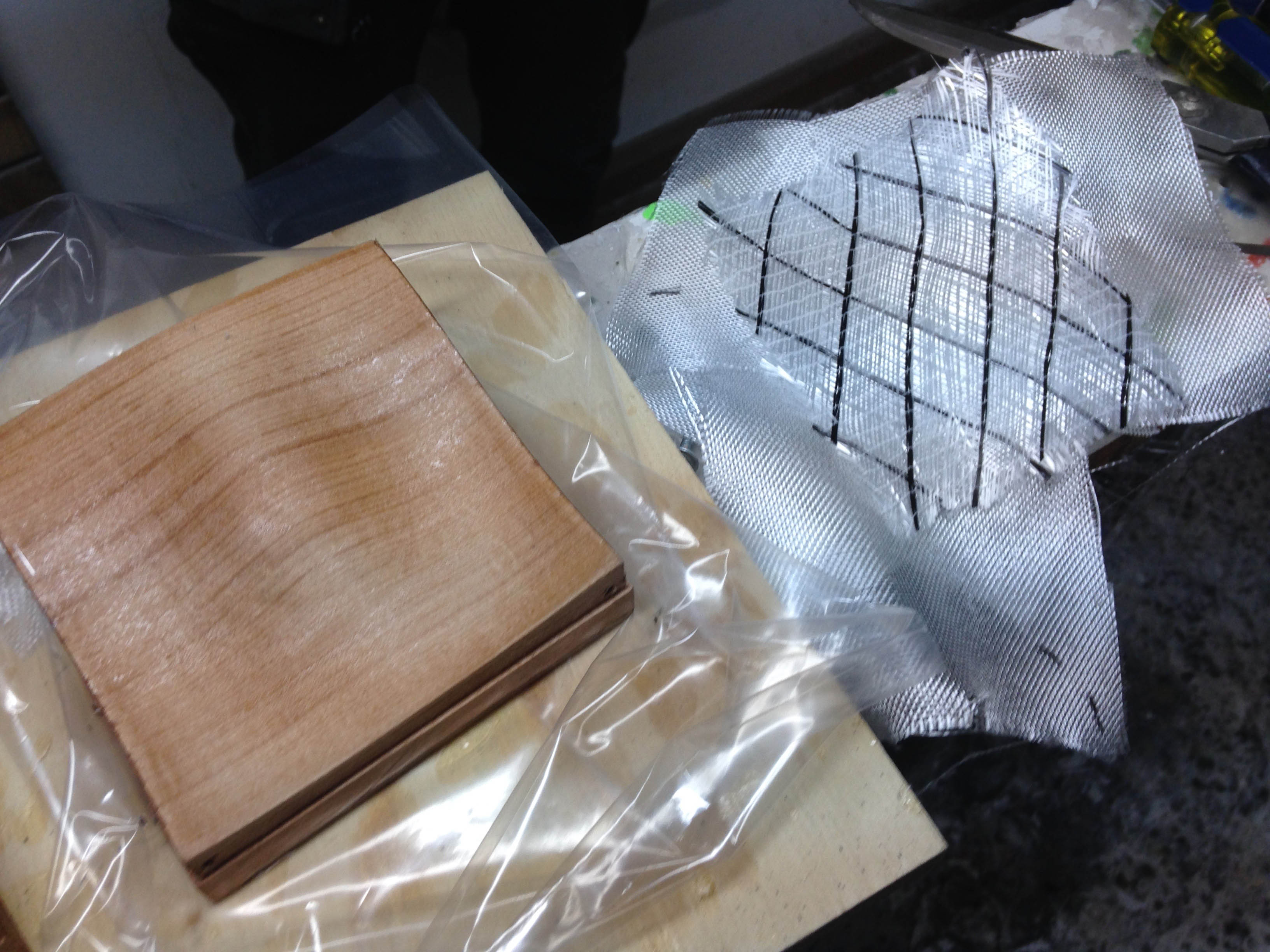
Once the dried release agent, we prepare parts of fiberglass and Fernando (my partner University which has a factory surfboards) I shared a bit of fiberglass strands of carbon to give a better finish.
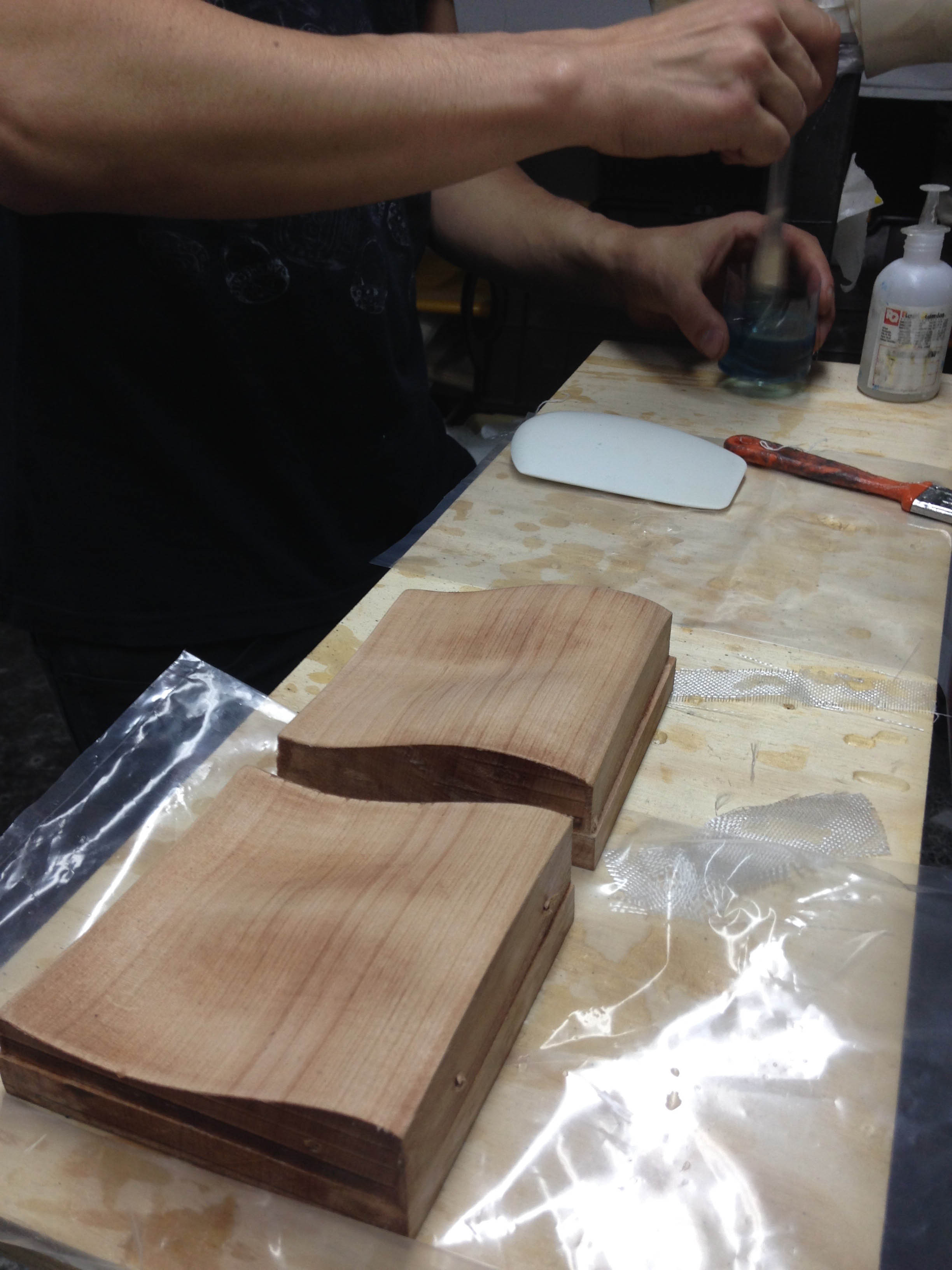
Then we prepare the resin, which had already added the accelerant, and add the catalyst then mix well to remove bubbles and ensure a homogeneous mixture.
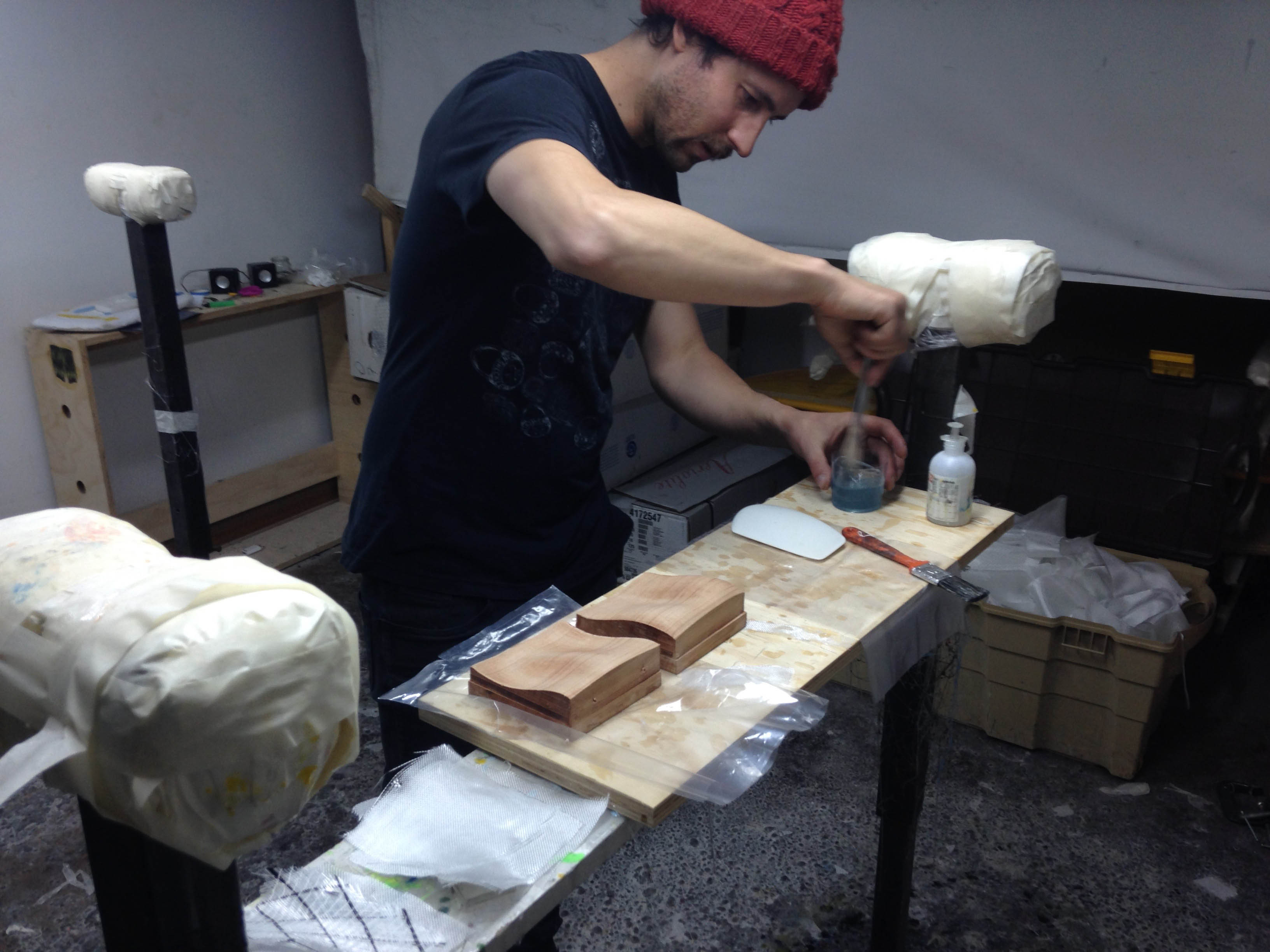
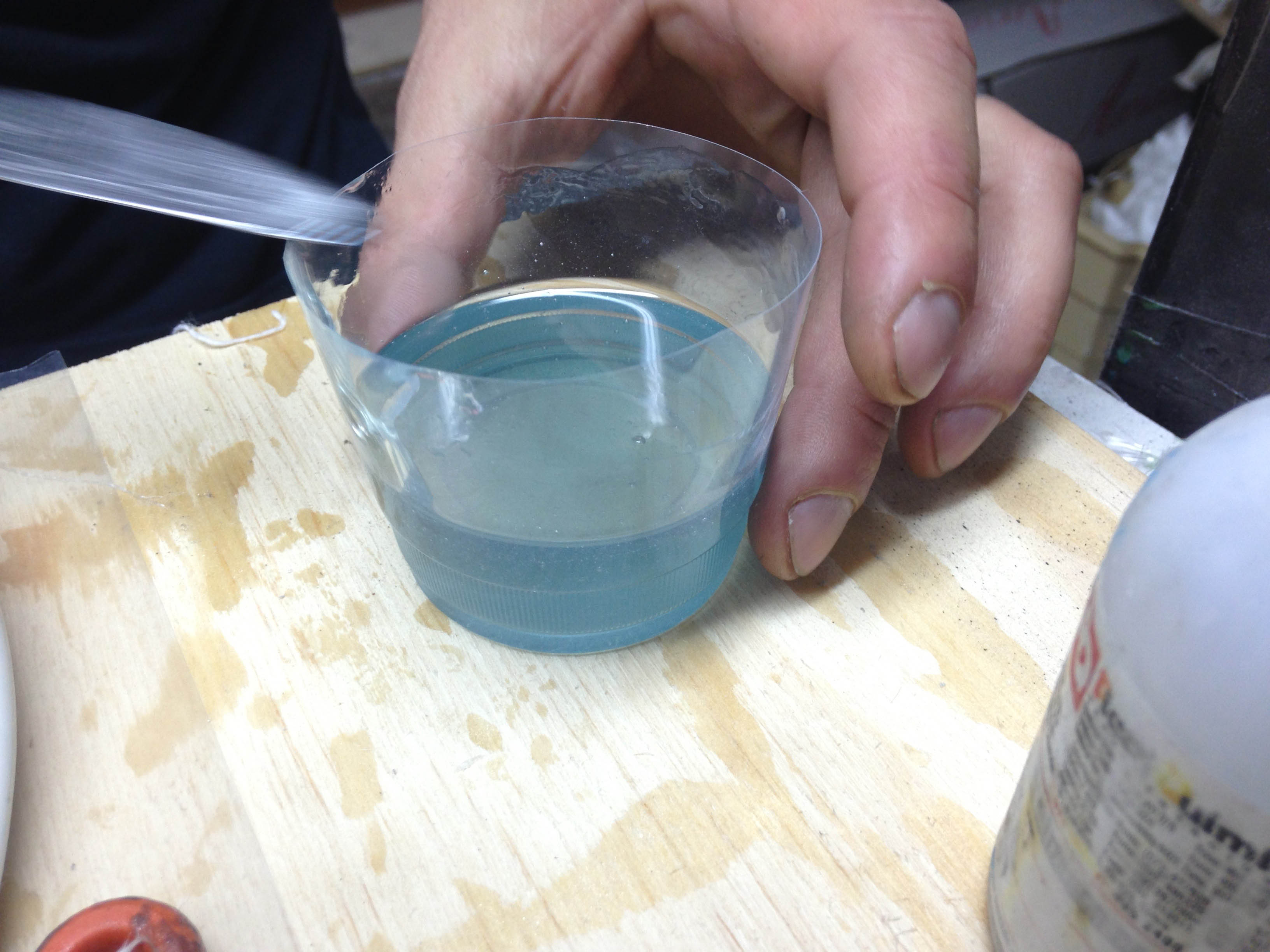
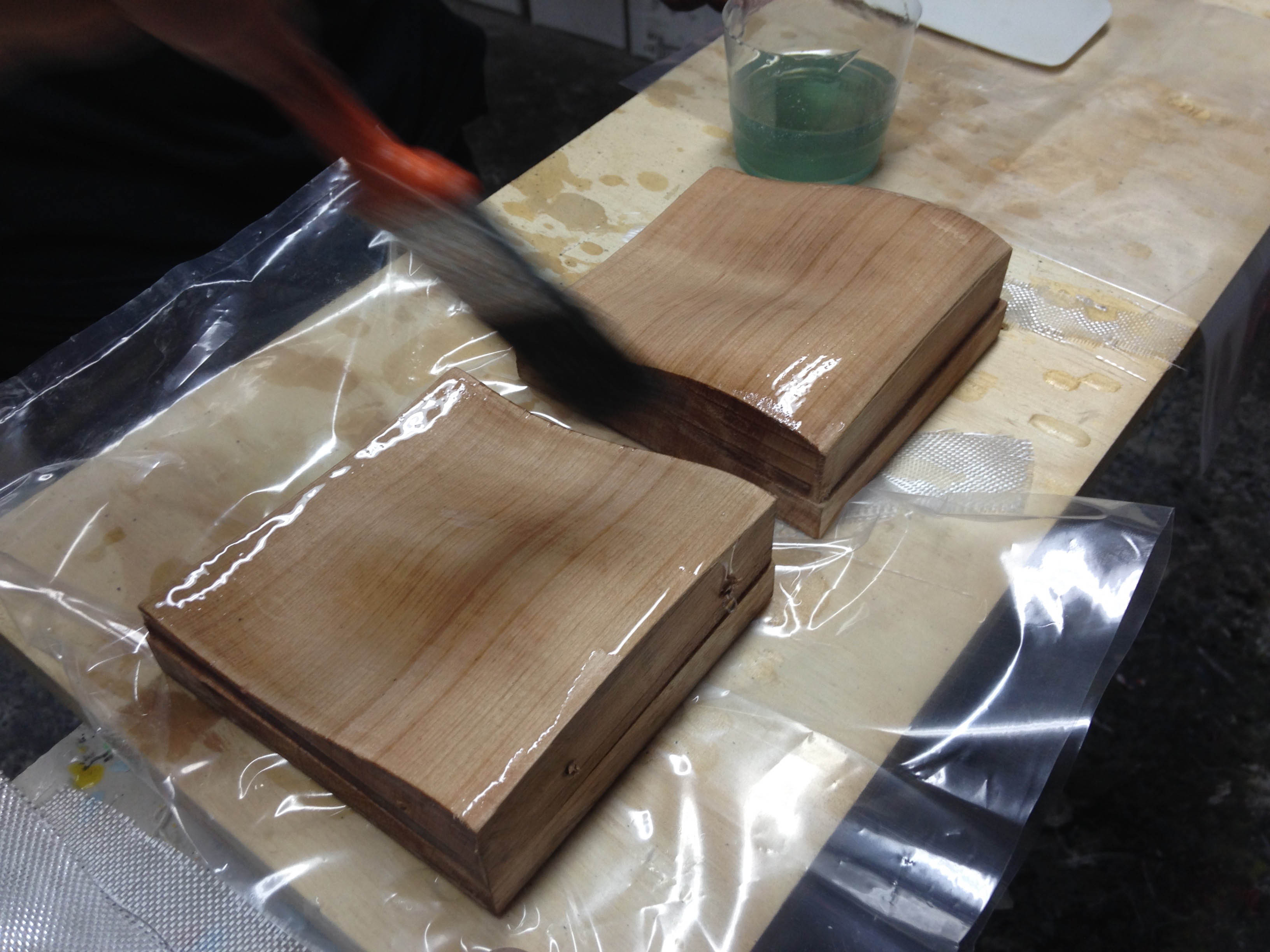
First apply a layer of resin on both pieces of wood, then we put the fiber layers on both sides, in total we add 3 layers.
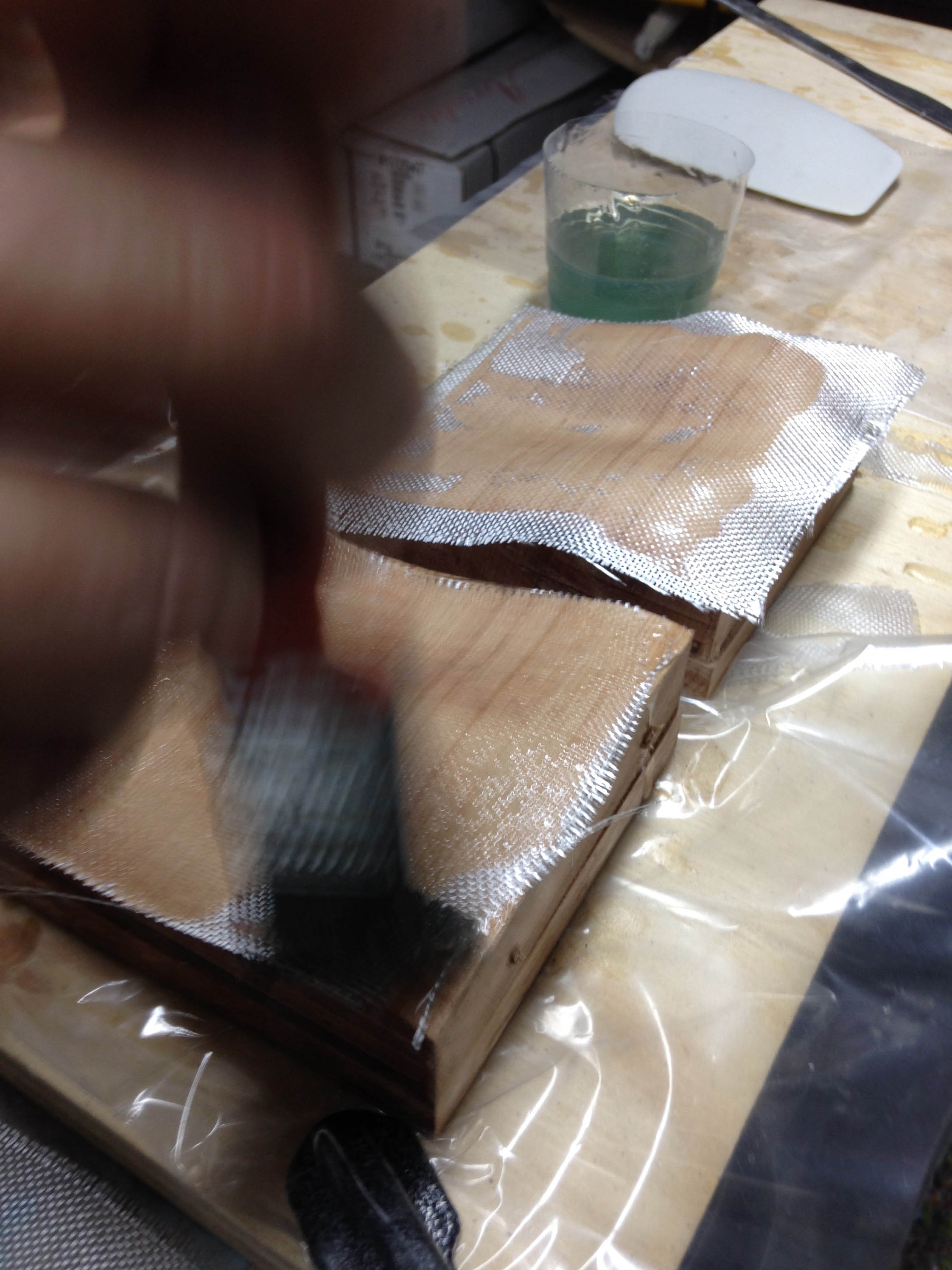
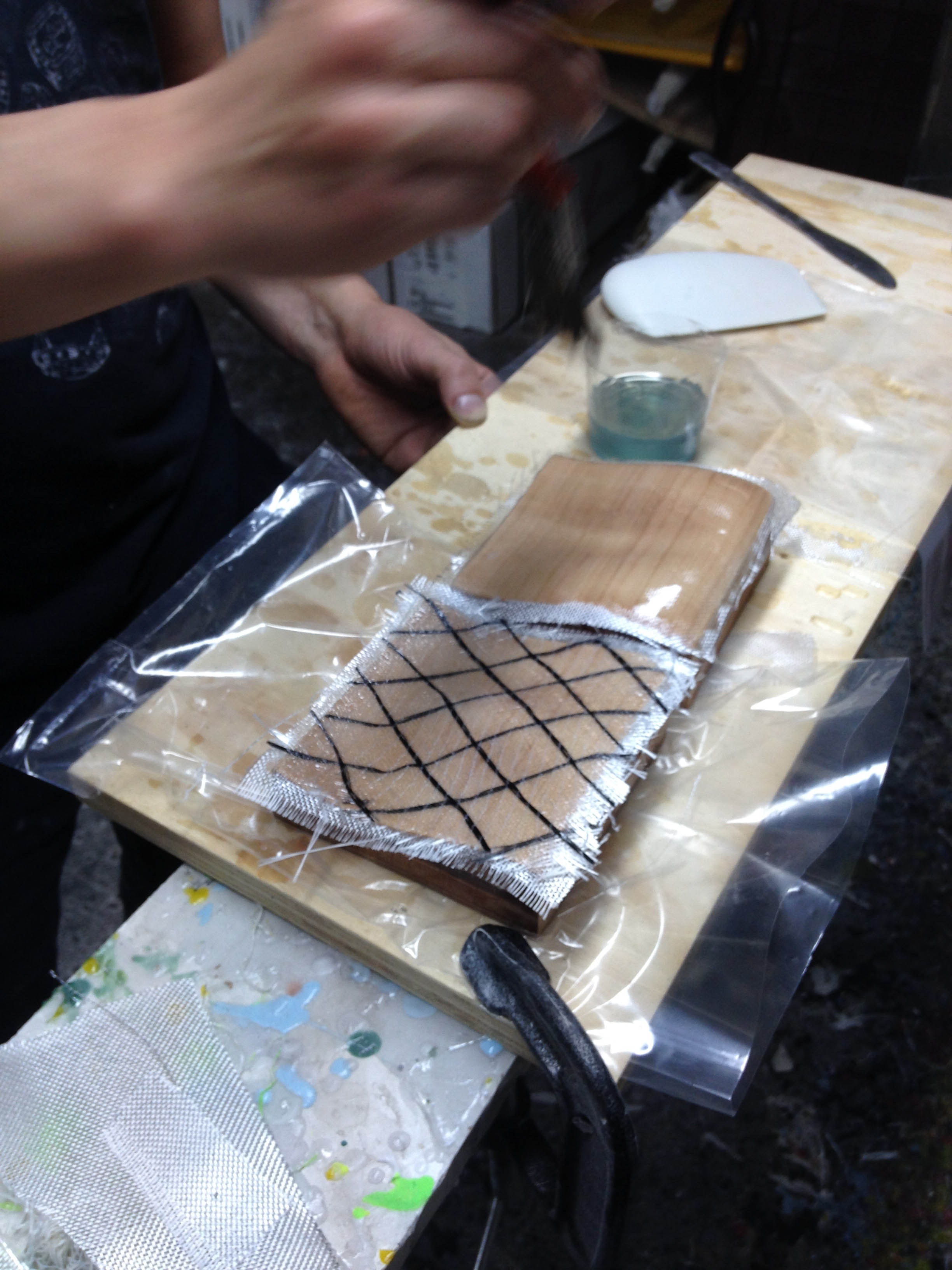
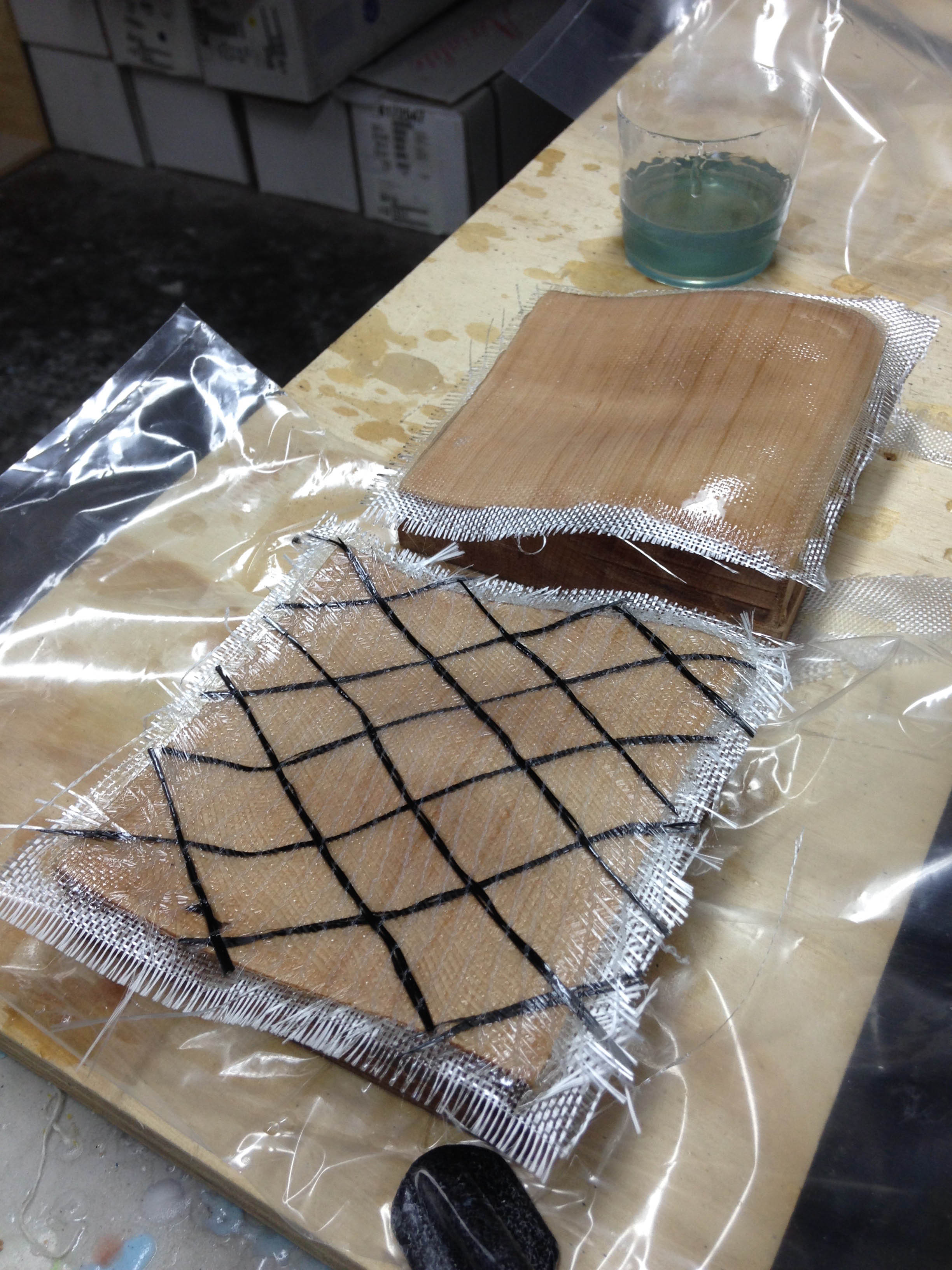
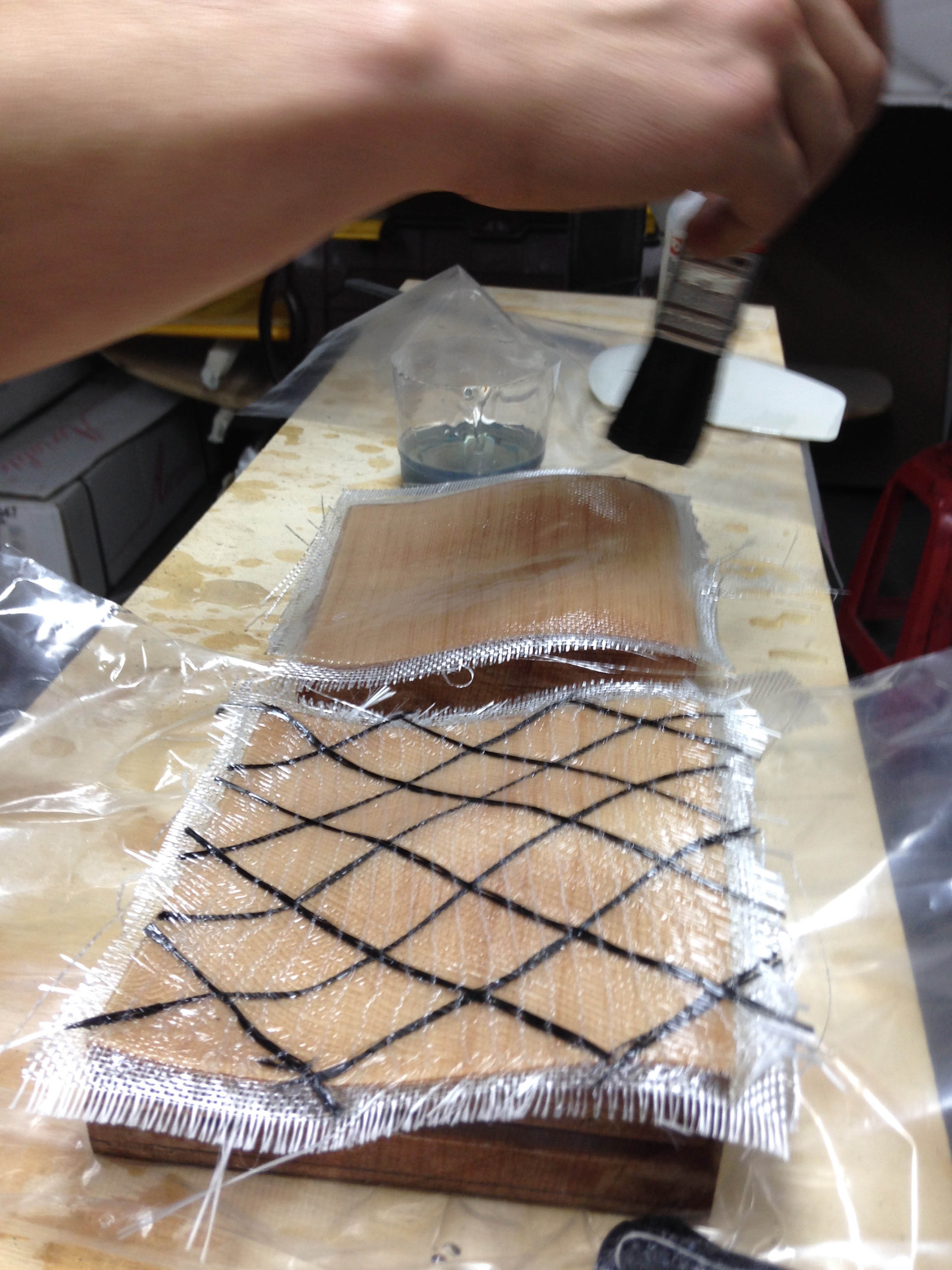
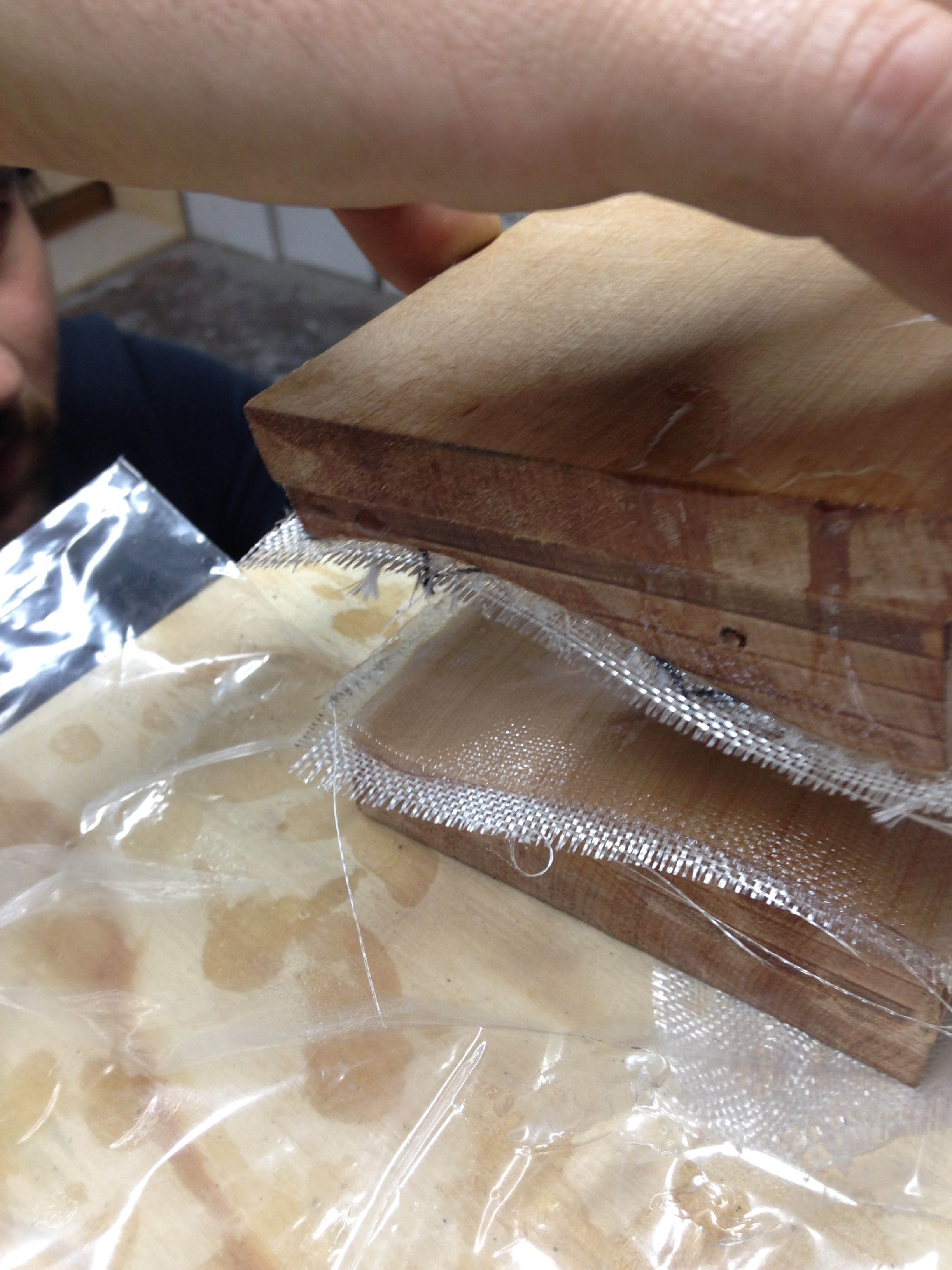
After the brush is repeatedly impregnates the resin into the fibers to penetrate all the material. Once the process can not be delayed much because the resin and the catalyst has finished molds are brought together and leave for 12-24 hrs. Fernando told me it is best to wait a week since the resin continues its hardening process. The he told me that surfboards must rest at least a week.
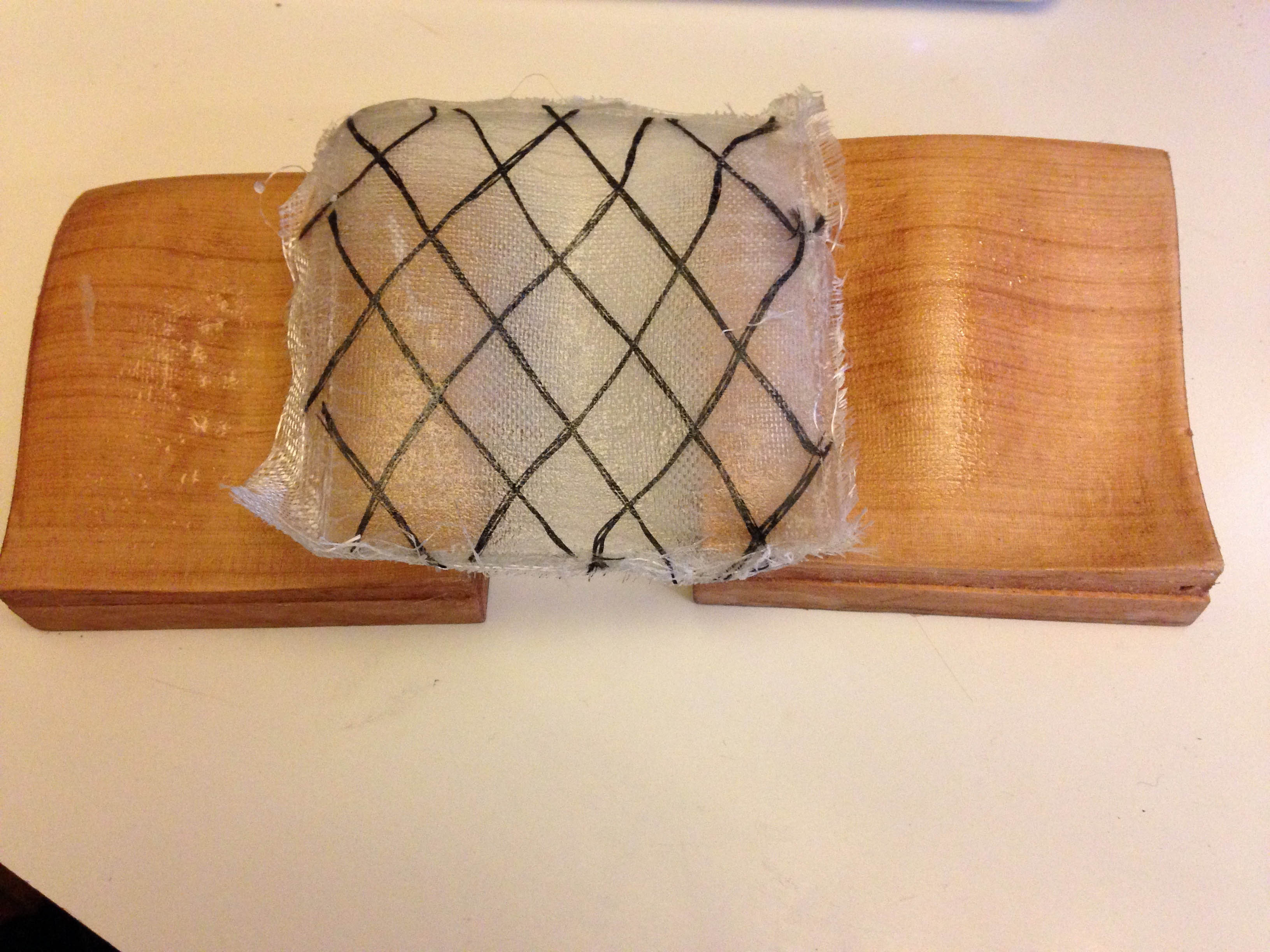
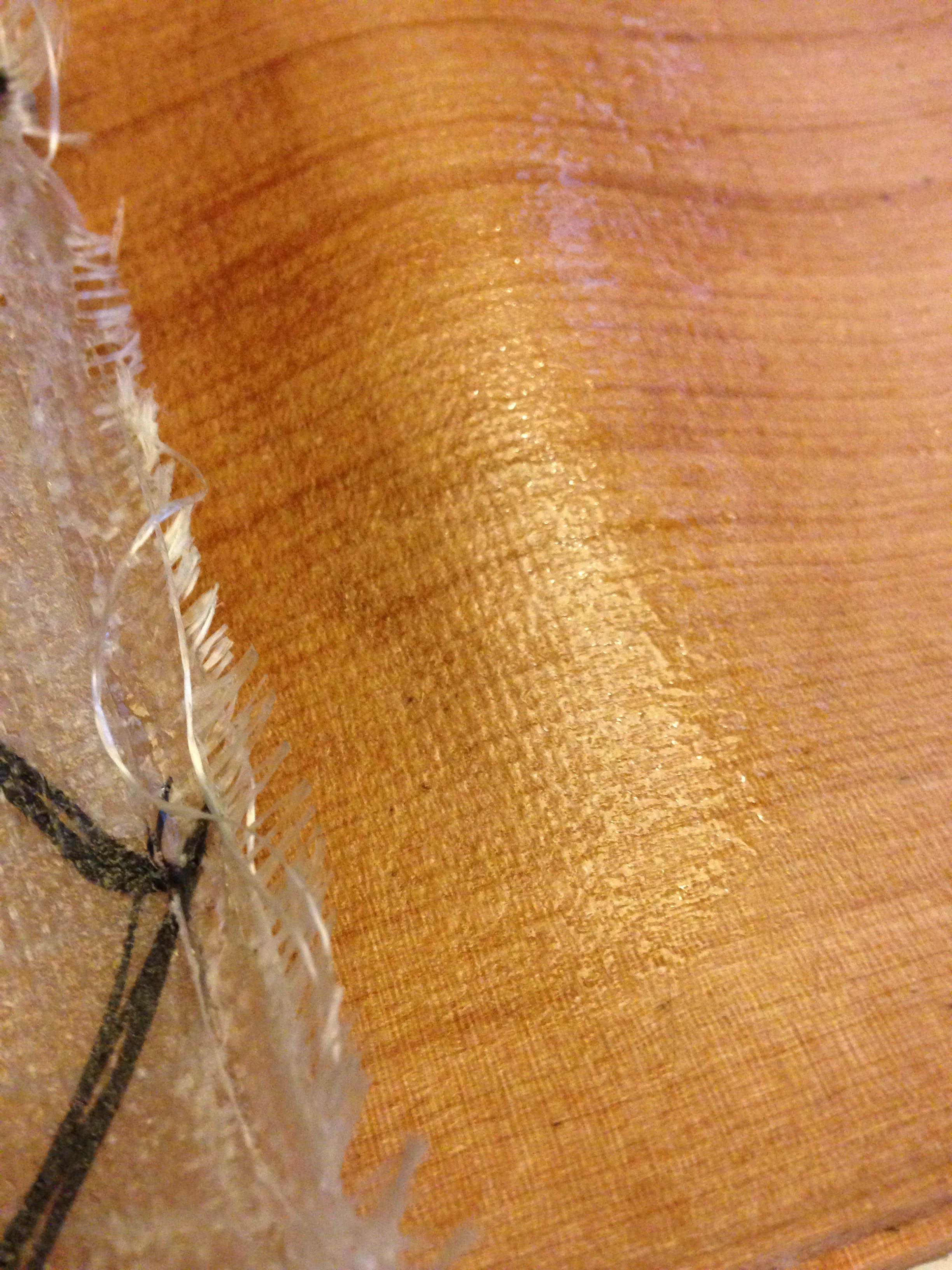
The mold is left pressed for 24 hrs after this process was quite simple release agent, which allowed seeing the release agent worked perfectly. What could be improved on another occasion is the quality of the surface, I have the idea that the release agent should be applied more evenly and also increase the time sanding or change material milling wax, but here in Chile is unobtainable, so we use native wood stored for 2 years at the side of the router, so it is dimensionally stable.
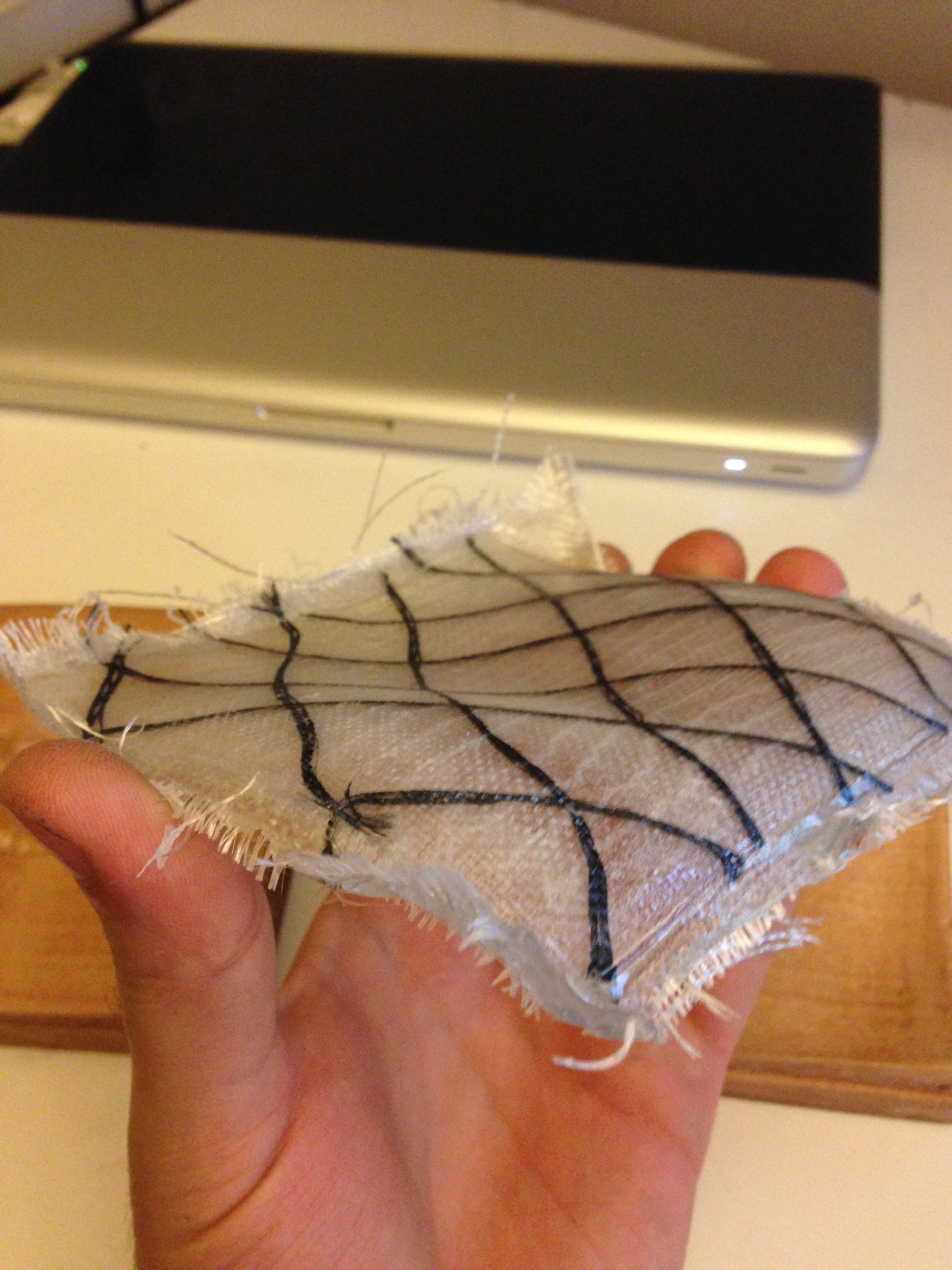
Work info:
References: RhinoCam,Fusion360,OC Surf,
Description:
Assignment: design and fabricate a 3D mold (~ft2), and produce a fiber composite part in it.
For this assignment, the idea was to test the feasibility of a future seat chair, like the one developed in the week computer-controlled machining. For this reason I made a scale model with exaggerated curves to better see the results.