Exercise 10 Molding and Casting
group assignment: review the safety data sheets for each of your molding and casting materials,
then make and compare test casts with each of them
for our group assignment we chose to make two different types of molds: a food safe mold and a platinum silicon rubber mold.
For the rubber mold we used the Mold Star 16 FAST Plantinum Silicone Rubber mold. After looking at the safety sheet, we started to make a practice mold. Here is the procedure we used to mold a lego:
We measured out equal amounts of part A and B (approximately 36.2g) in plastic cups using a scale.
We mixed the two parts together and mixed them with a wooden dowel. We then put a lego at the bottom of a plastic cup and poured the mixture on top.
After waiting for a few minutes, we found that the lego was floating to the top of the mixture. So we put a fork in top to hold it down.
Unfortunately this wasn't as successful as we hoped given that after waiting for the given amount of time (30 min) the lego was only partially submerged.
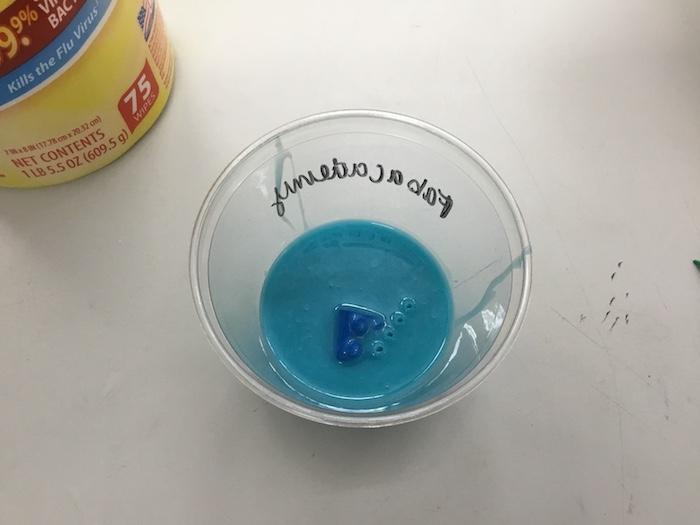
After this didn't work :( we decided to try one more time with something we could secure to the bottom. We used a key and used the same procedure as above. This mold came out much better. After we used a flexible plastic to cast the key. This took 24 hours to settle but came out as a clear plastic key.
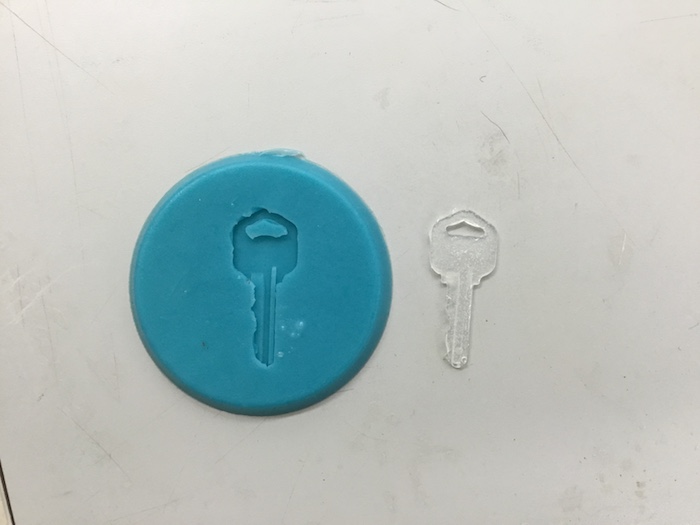
For the food safe mold we again read the safety and instruction sheets and then sprayed a lego and the cup it was in with food grade silicone mold release.
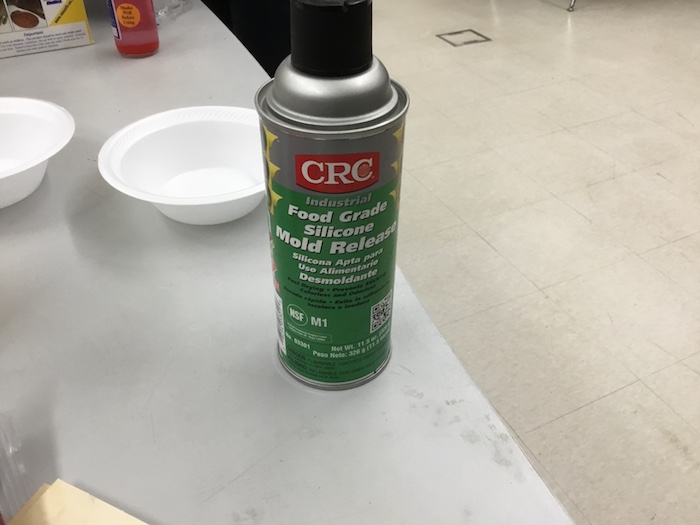
After we mixed equal amounts of Smooth-Sil 940 A and B. We then poured it over the lego and let it sit for 24 hours. We also had to hold it down with a fork and a rubber band but the mold ended up turning out pretty well.
individual assignment: design a 3D mold around the stock and tooling that you'll be using,
machine it, and use it to cast parts.
I made a design of four flowers in fusion360, then molded the design using quick drying rubber (Mold Star 16 FAST Platinum Silicone Rubber), and finally casted it with fast setting plastic (Smooth-Cast 300Q Very Fast Setting-White) . Here is the steps I took in fusion360 to make my design:
Before even opening fusion, I measured the wax: it was 3 in by 3 in by .5 in
I created a 3 in by 3 in rectangle in the zy plane (front)
I then found an image of a simple flower in the google images and saved it as a jpg
I imported the image by going to Insert--Attached Canvas
After rotating it and putting it in the top left hand corner of the rectangle I created and sizing it to 1.5 its original size, I used the Splice tool to trace over the drawing. I then hid the flower canvas by clicking on the lightbulb.
I then copied and pasted the flower three more times, so there were a total of four inside the rectangle.
From there I extruded the flowers .42 in out and the rectangle .24 in out.
I then realized that I needed some walls so I went back into the original sketch and created 4 rectangles along the edges with dimensions 3 in by .14 in.
After I extruded those rectangles and the squares in the corners where they intersected out .5 in.
For the CAM portion, I looked at this Autodesk Fusion360 tutorial to learn what toolpaths needed to be made for the mold.
I first created a new Setup. I changed the orientation to Model orientation and the Origin to Stock box point, selecting the bottom left corner at the top of the material. I also changed the Stock to 0 (so there was no stock in my design).
I then created a 2D contour and selected a new tool. I added the 1/8 flat end mill tool and put in the necessary dimensions and feeds and speeds I found on the bantam tools website. I also changed the Geometry to Chain in the stock selections section by selecting the top square (highlighted in yellow). I made the same changes in the 3D Adaptive toolpath.
I then simulated each toolpath by right clicking on the tab and selecting Simulate. everything looked good.
I decided not to do the 2D contour cut, since I am only focused on the inside of the mold, and only did the Post Process for the Adaptive cut.
I saved the file as a .gcode file and then opened it in Bantam tools.
After zeroing the x, y, and z axes I changed the bit to a 1/8 flat end mill. And then I cut it. I have never cut wax on the othermill before and I have to say- it was pretty cool!!
After I designed and milled the flower design, I made a fast curing rubber mold. After spraying the design with unstick spray, I followed the steps on the box, measuring out equal amounts of parts A and B using a scale, then mixing them, and finally pouring it in the 3d design. I waited for 35 min and removed the mold (it worked!).
I then used a fast curing plastic to make casts of the flowers. I followed the same procedure as described above. It only took it 10 min to cast (!!), going from clear to white and heating up.
To download all my files click here:
Flower mold .gcode file
Flower mold .f3d file