Until 29 Feb 2017
3D 스캔 + 프린트
3D Scanning and Printing
Contents
- Basics on 3D Scanning and Printing!
- 3D Scanning
- 3D Print Tolerance Test
- Design & 3D Print an object
- 5th The Fab Academy meeting
Basics on 3D Scanning and Printing!
Constrains:
- Materials (ABS: hard plastic, HIPS, acrylic, PLA: bio product plant base)
- Resolution: most comment process: Fused definition molding(FDM)
- Time
- $$
3D Printing has pros and cons.
- Allows to print micro size components.
- assembling:
- Machines: ultimakers(ultimaker elephant), makerbot, Sindoh, formlabs(high res/messy), MTM, and etc.
- Service Bureaus: Pinoco, shapeaways, additively.
File Formats:
- STL(turn it into mash, triangle surface/lose resolution, Binary/more compact, doesn’t contain units, color)
- OBJ
- PLY
- G-codes (emergingobject.com)
3D modeling Software: Fusion 360, SolidWorks, Rhino, Openscad, Antimony, and etc.
Slicers: Replicator, Slic3r, Cura, Skeingorge
Sharing Websites: sketchfab, Thingiverse
Turning object into datas! 3D Scanning
Micro-CT($$$$ BEST), Point cloud, Laser Scanning Microscopes, Milk Scanner(Fluid scanner), Photogrammetry: photo base/cons no good for quantitative reconstruction. better qualitative construction.
3D Scanning
3D Scan using Kinect by Microsoft
The first time, I used Kinects was in OpenFit Lab: Generative Patternmaking workshop in Eyebeam, NYC.
It was used to gernerate custom body measurement using software to quickly determine and export them to Processing, where it could be used to draft clothing patterns.
In Fablab Seoul,
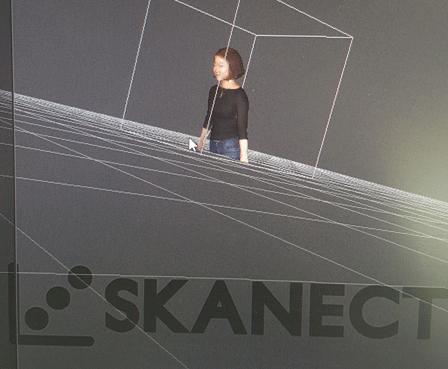
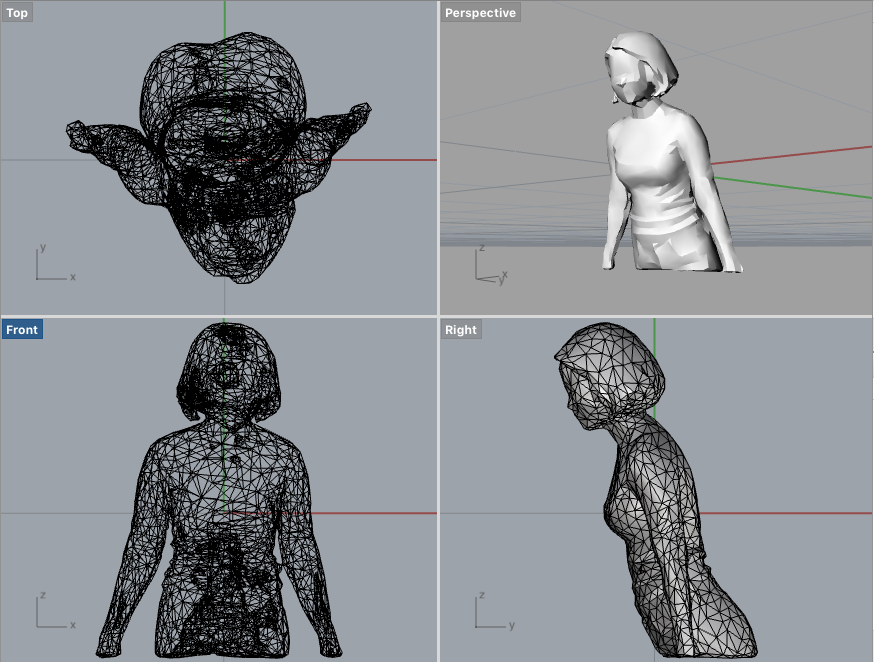
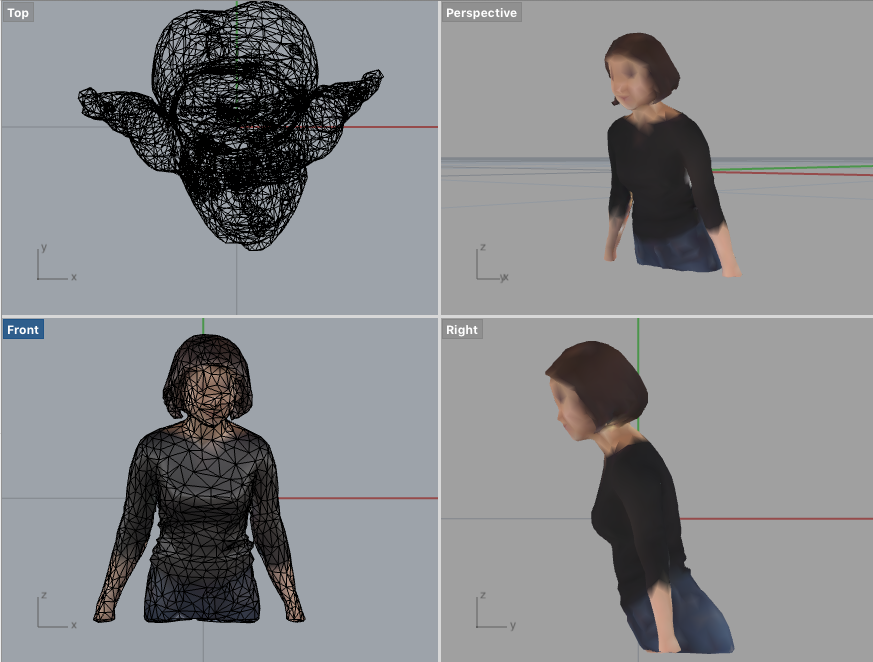
Test scan with MakerBot Digitaizer
I tried to scan my USB, and it failed. I guess it was too small and metal part weren't scanned.
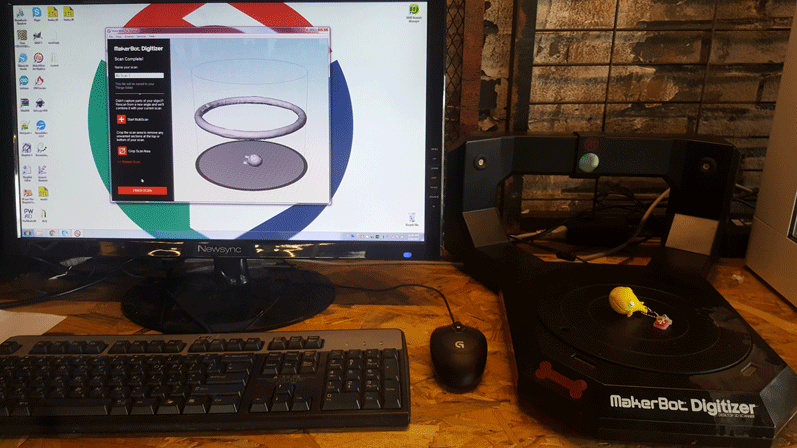
Second scan with 3D printed skull from fablab
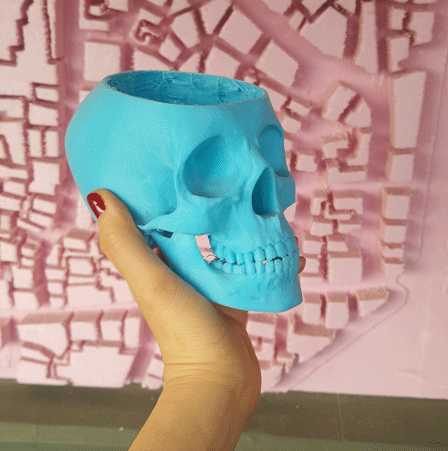
It's not clear scan and lot of errors.

3D Print Tolerance Test
Printing with Ateam's Creatable D3.
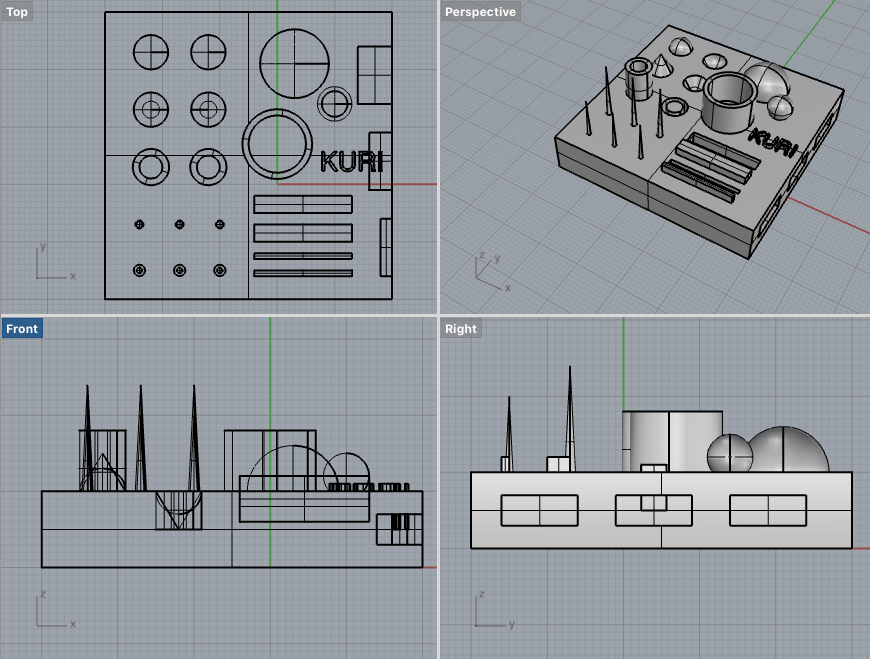
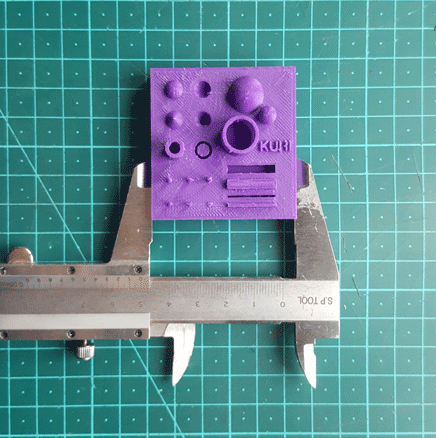
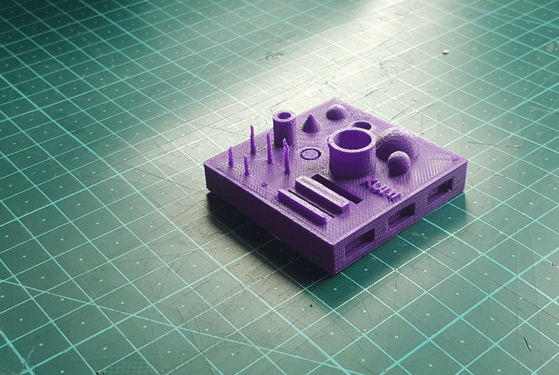
A visual Ultimaker troubleshooting guide
Design & 3D Print an object
Design and 3D print an object (small, few cm) that could not be made subtractively. Additive design allows to build/ access to inside structure. So I designed an object that has inside parts. Also, I wanted to experiment with 3d printer by putting rings on the plateform rather than flat surface.
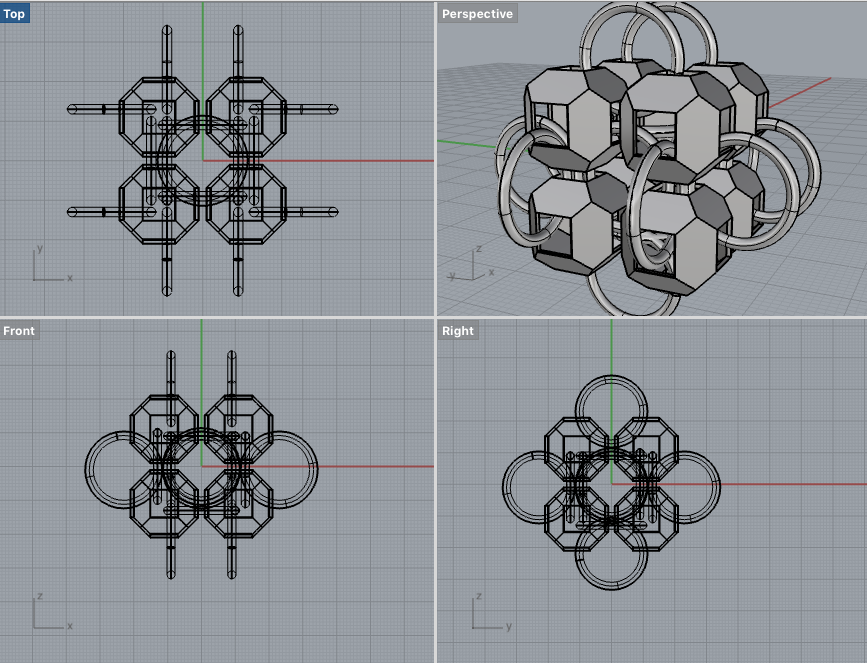
Using Cura Support: I wasn't satisfied with the result, so I've tried Meshmixer's suppert.
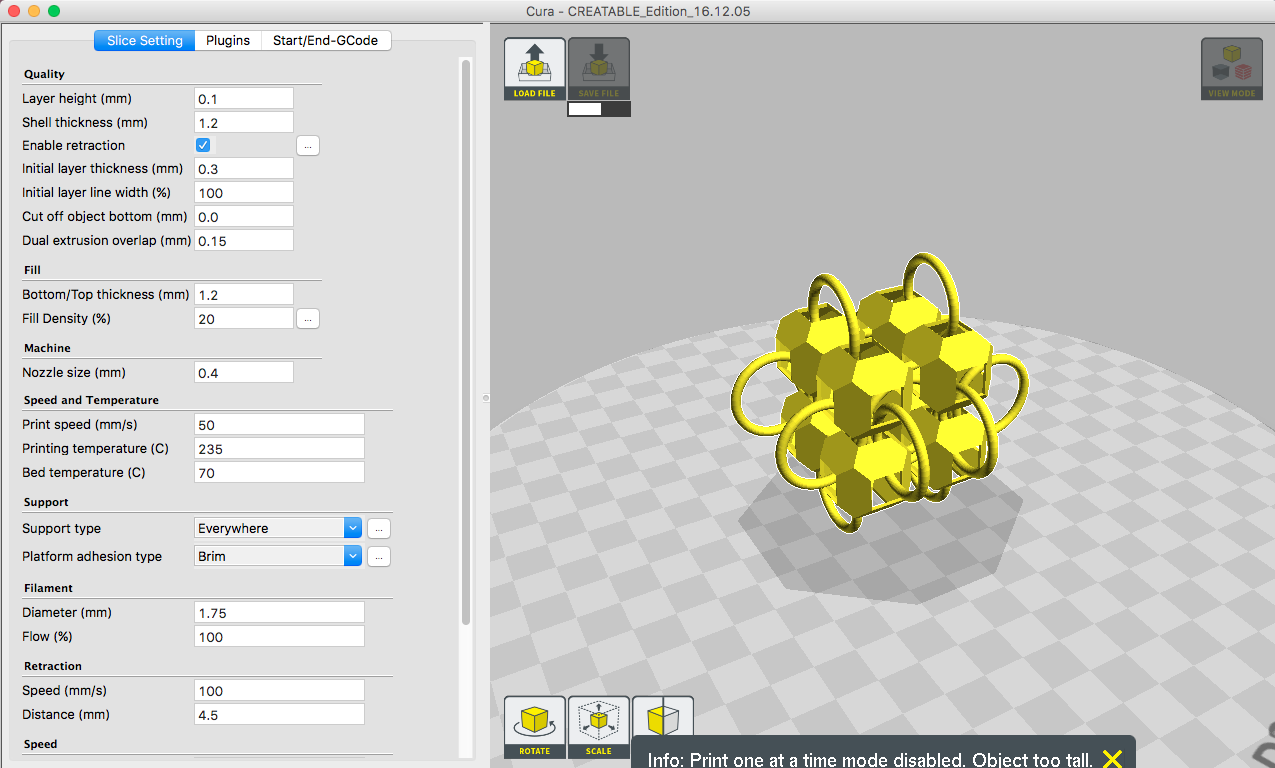
Using Meshmixer Support
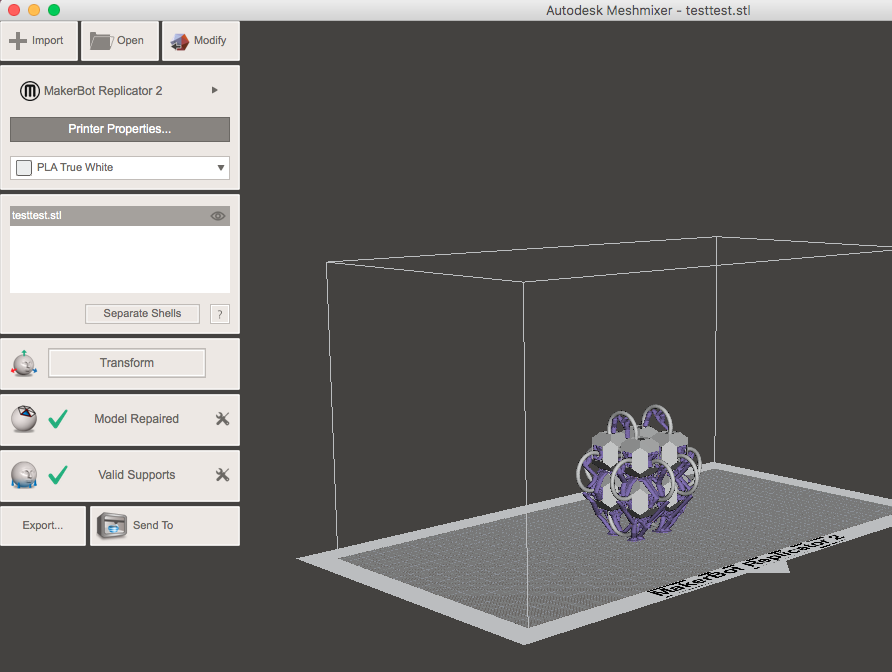
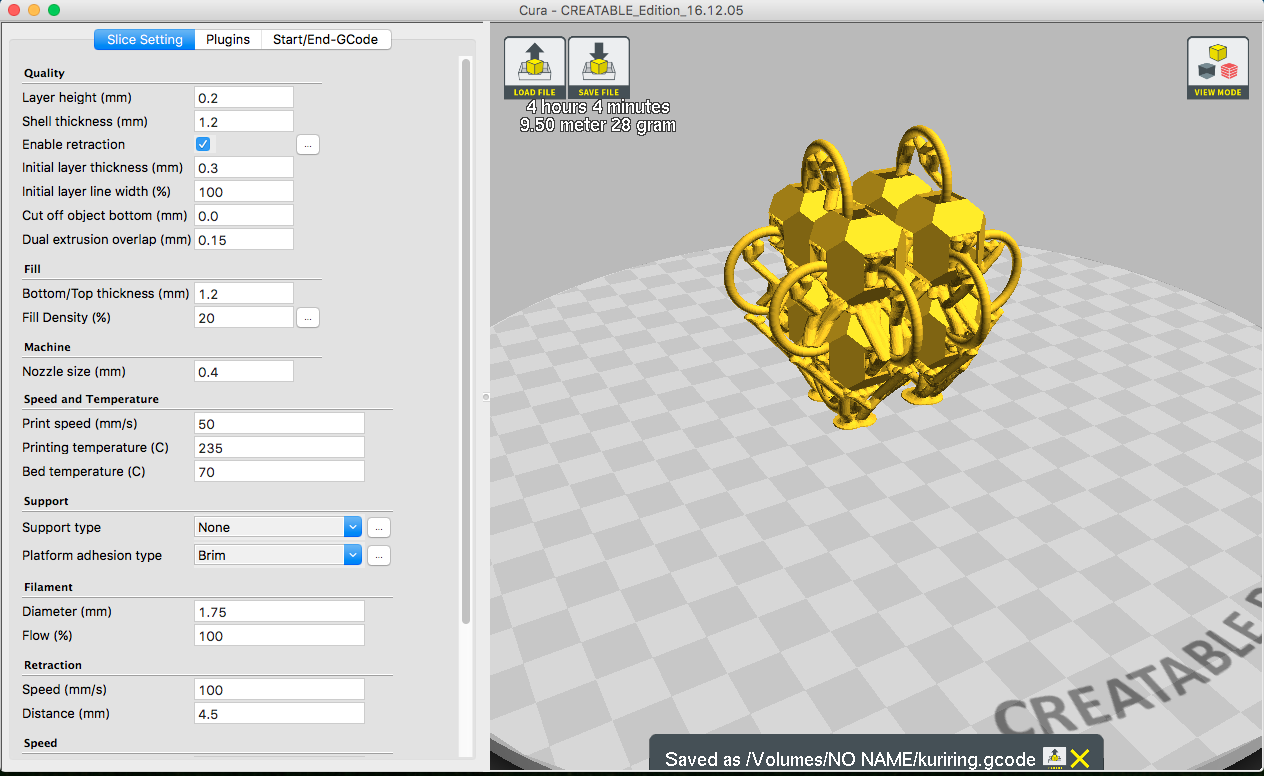
In process
Support structure was different among two program. Cura was more vertical and Meshmixer seemed more organic.
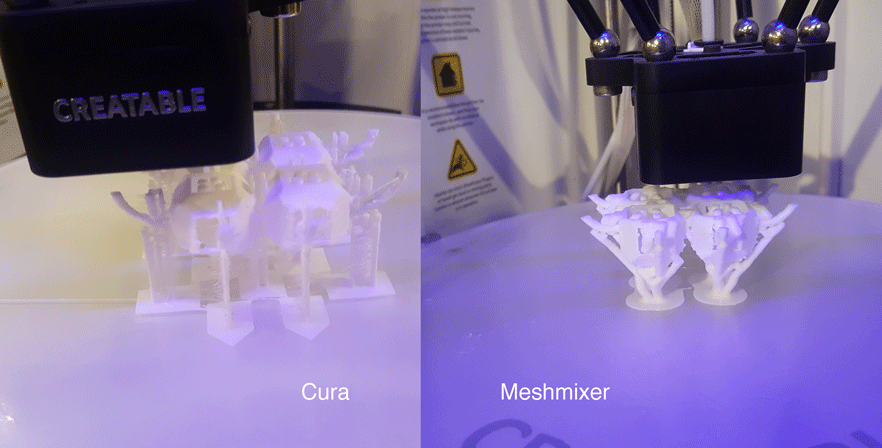
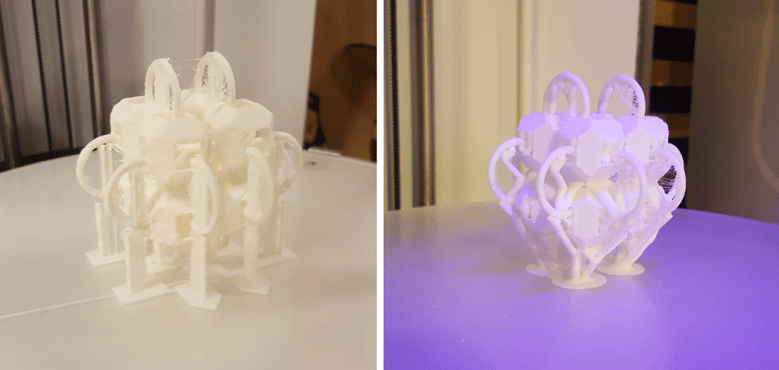
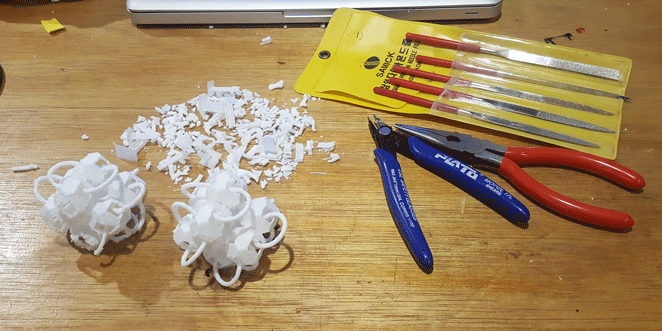
Finished!
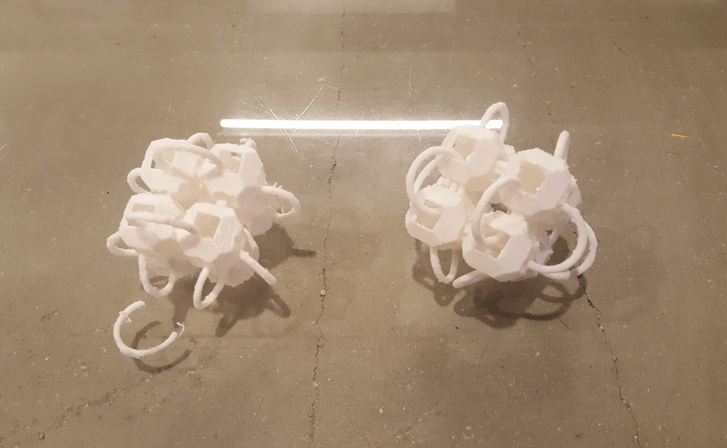
For this design purpose, Meshmixer was better. Cura didn't have the support for the bottom boxes, so the result was not even. However, Meshmixer had too much support, it was hard and time consuming to take support out.
3d Printer test from Kurina Sohn on Vimeo.
5th Meeting:
3D Scanning and Printing February 22, 2017 11pm~2am(Seoul)
Homework
o - Shown how you designed/made your object and explained why it could not be made subtractively
o - Scanned an object
o - Outlined problems and how you fixed them
o - Included your design files and ‘hero shot’ photos of the scan and the final object