Fabacademy 2017
Third Week
Third lesson
Computer-Controlled Cutting
Following last week format we went through a wide range of software tools and techniques. First fabrication tools were introduced, the vinyl cutter –which we don't have yet at our fab lab and based on Neil high praises about it, it's now first in our priority list– and the laser cutter, we have some experience with this tool as we build a lasersaur ourselves four years ago.
Lasersaur (open source laser cutter) assembly time-lapse. Fab Lab Limerick.
Fablight was a great finding as I thought that similar technologies were much more expensive. Automated metal-cutting (and welding) is something we have been really interested about since we started our Fab Lab as digitally fabricated architecture is one of our main areas of research.
Third assigment
Parametric press-fit construction kit
Last week I started using Freecad for the second exercise. To be honest, I am still finding Freecad's UI a bit buggy and not very intuitive so this week I planned to try out some other parametric tools such as Solidworks and Inventor.
Fusion360
I primarily work on a Mac so I installed both of them on a virtual machine but after doing some research it felt to me that Fusion360 –a freemium, cloud based, multi platform and fabrication oriented parametric software from Autodesk– may be a great way to get started in parametric modeling.
Inventor | Fusion 360 | |
---|---|---|
General | Large feature set that requires some training, more expensive | Easy to learn, less expensive |
Industry Focus | Aimed at large assemblies | Aimed at smaller assemblies (less than 1000-2000 parts, for example) |
Modeling | Robust parametric tools | Freeform models |
Add-ins | Numerous add-ins, including sheet metal, injection molds, chains, frame design | Not available |
Work Environment | Local or network-based files | Cloud-based files |
Usage Example | Designing complex assemblies such as conveyor lines or plant layouts | Designing less complex products that require both mechanical and freeform shapes, such as a vacuum cleaner or a leaf blower |
Computer | Runs natively on Windows | Runs natively on both Windows and Mac |
For More Information | Inventor product page | Fusion 360 features page |
I started with a simple tutorial in Hackaday for building a parametric box.
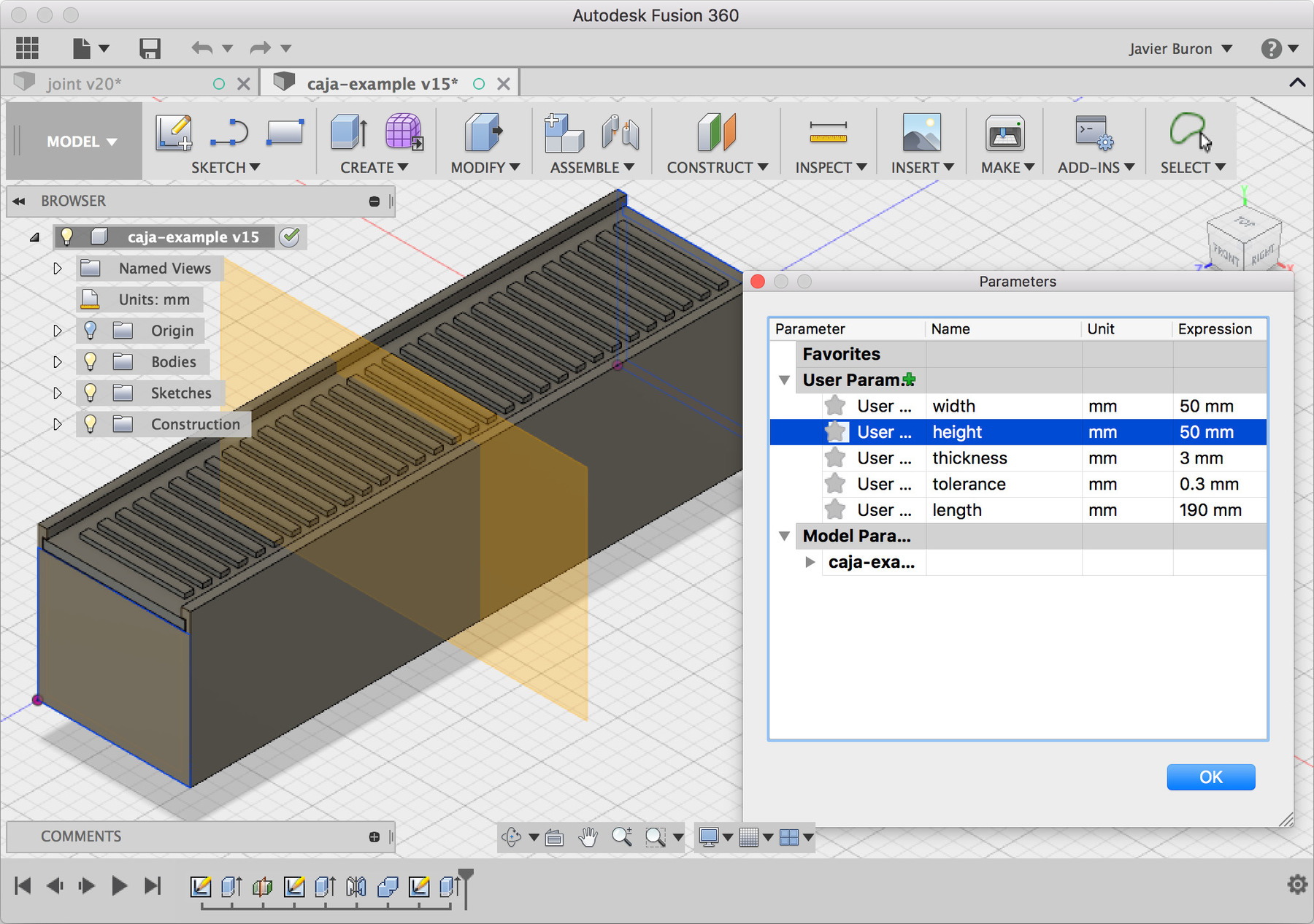
Sketches, constraints and variables are concepts used in most parametric design tools. As it was explained in the second class, using some sort of parametric design tool is a real necessity when working with digital fabrication tools. A parametric model allows the almost inevitable adjustments when fabrication happens, tolerance, kerf and real material thickness should be parameters in every design.
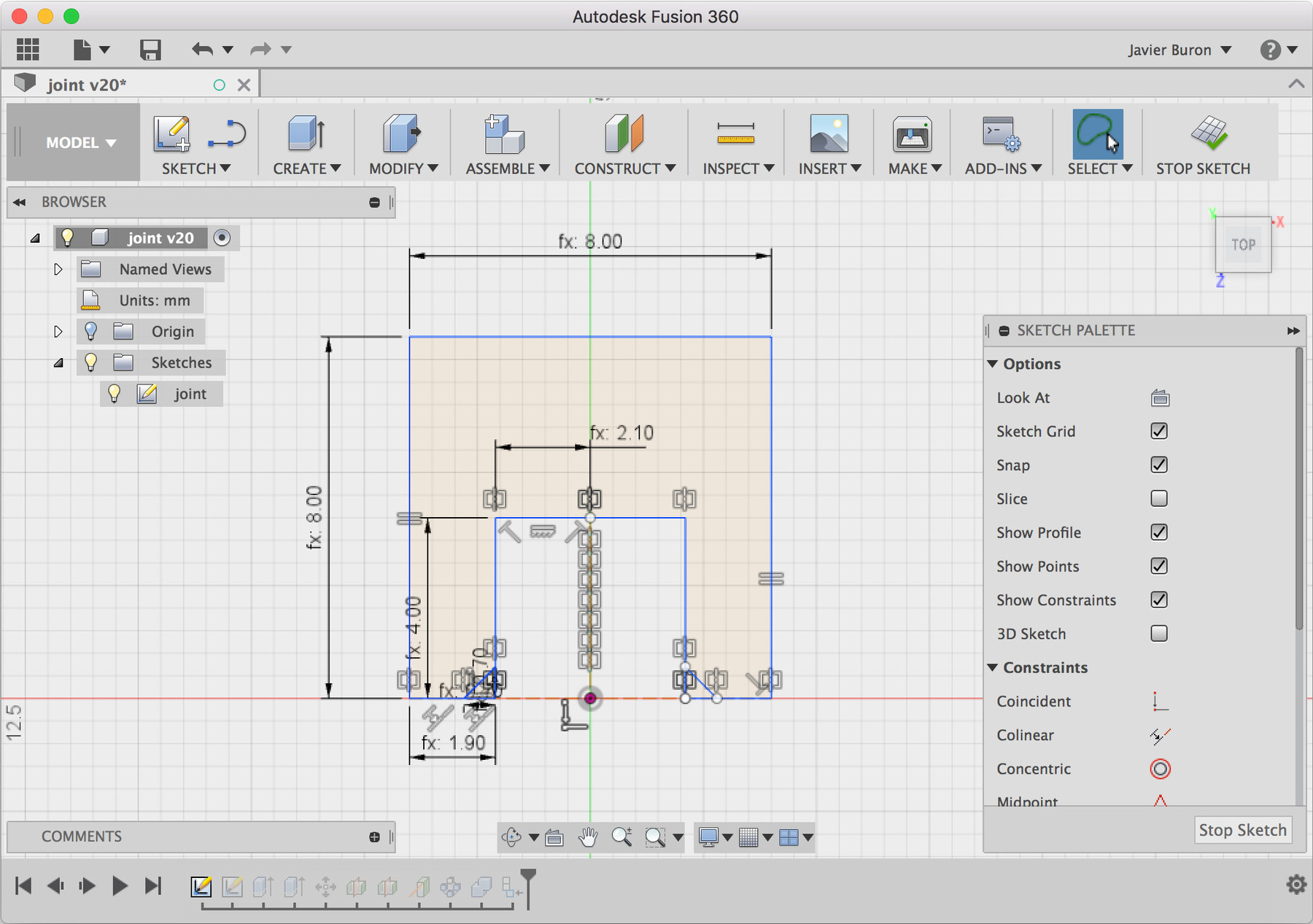
The press-fit design that I have been working on is quite simple and follows the same principles than GIK showed in class. Different angles are constructed by using pieces based on regular polygons with the same press fit joint so a triangle will allow 120º angles, a square 90º, a pentagon 72º and so on.
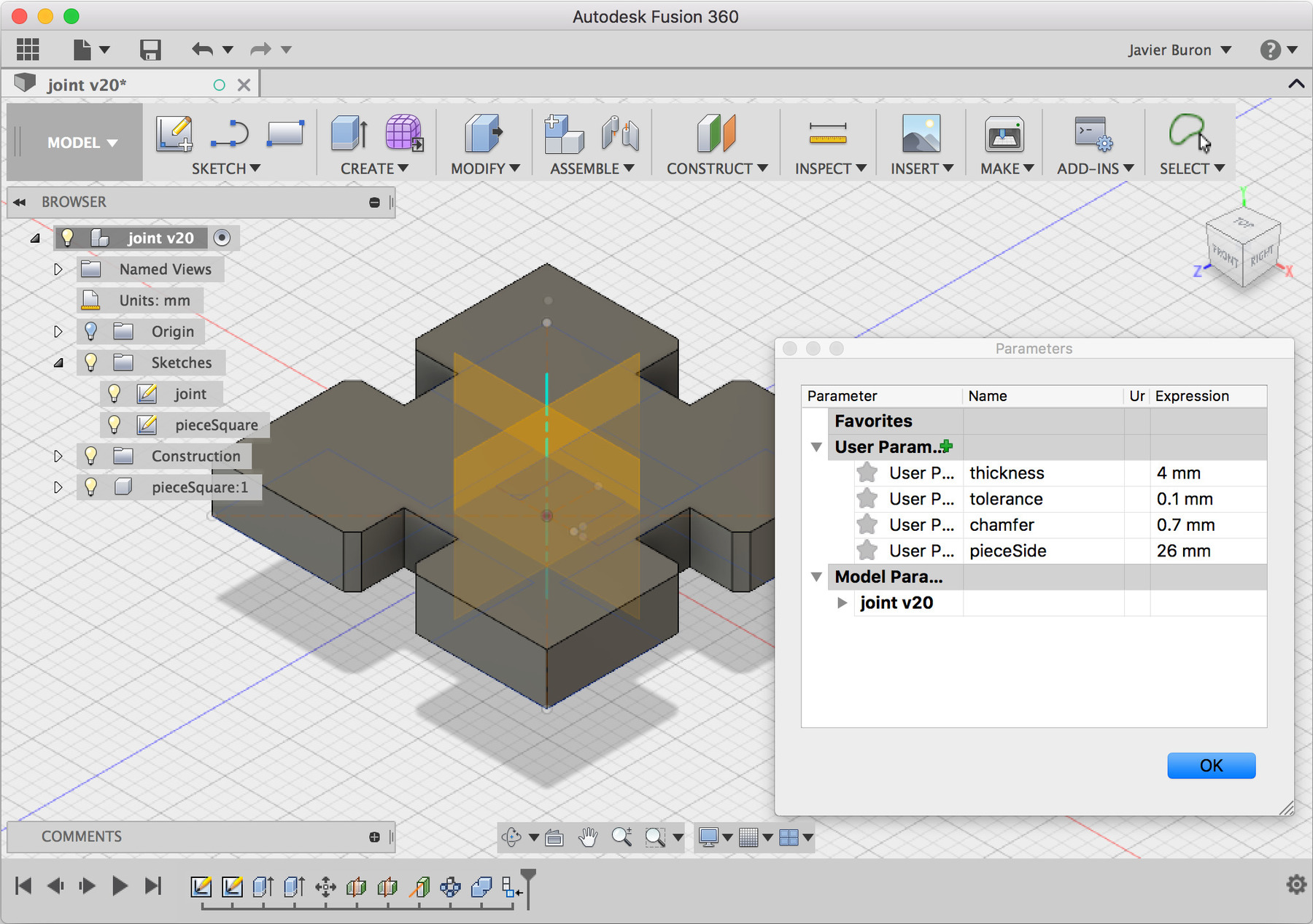
Instead of building each piece individually, I wanted to build a single parametric model that will produce all these variations. After a bit back and forth with the interface I managed to build a four side parametric piece that will constrain and resolve as planned.
I have to say that I was somewhat disappointed with the constrains feature to date. Building an intuitive GUI for these type of operations seems a quite difficult challenge in any case. I have plenty of experience with non-parametric design tools so this may be working against my learning process too.
Antimony
I realized that the proposed design could be defined mathematically quite simply with some basic trigonometry so I decided to give a try to Antimony.
So far I found it quite enjoyable, GUI is minimal and syntax is quite similar to other programming languages so calling out variables and parameters feels very intuitive.
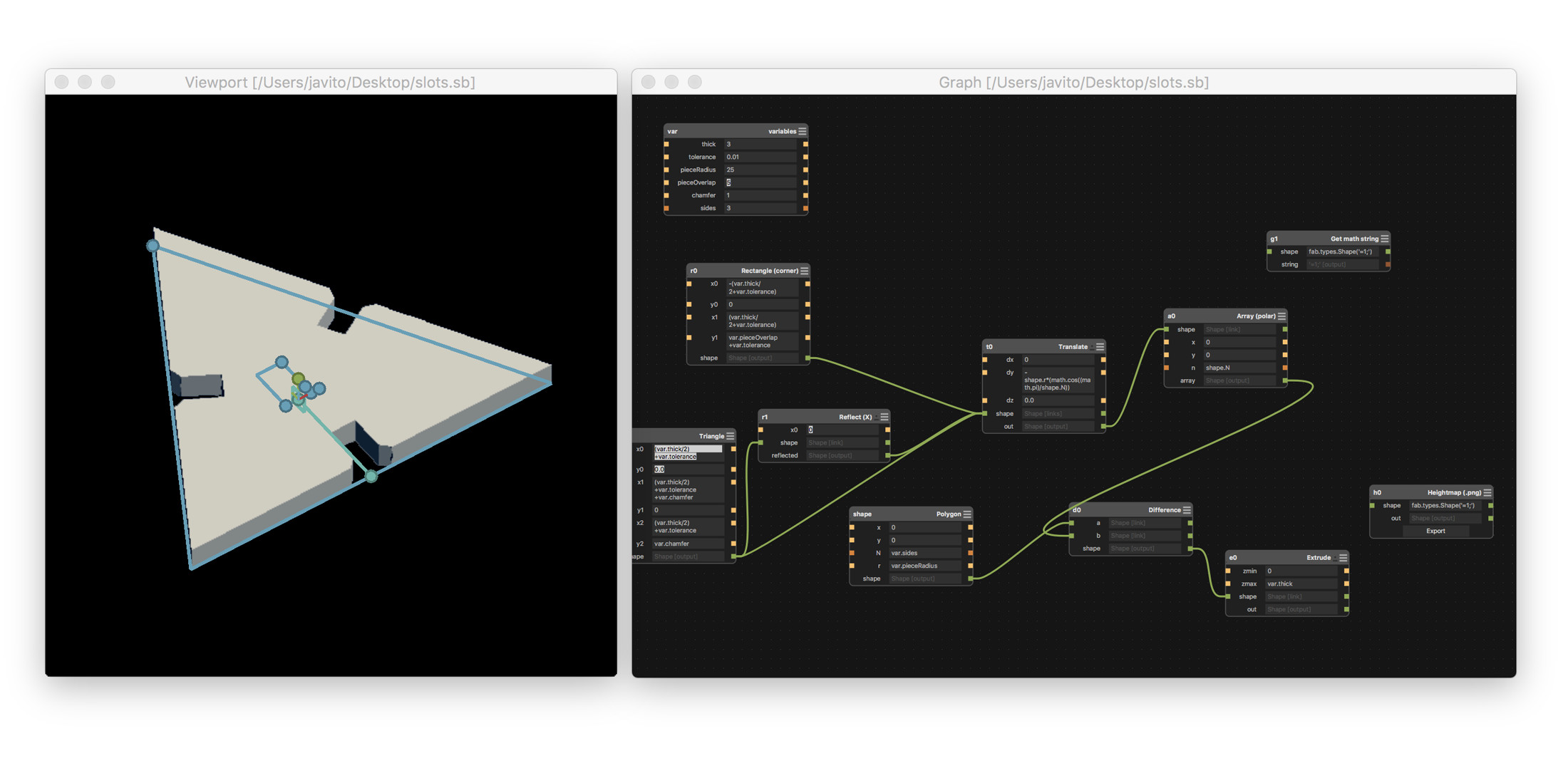
The current version uses the simplest joint that it was explained last week. I implemented a chamfer edge which can be adjusted easily in real units.
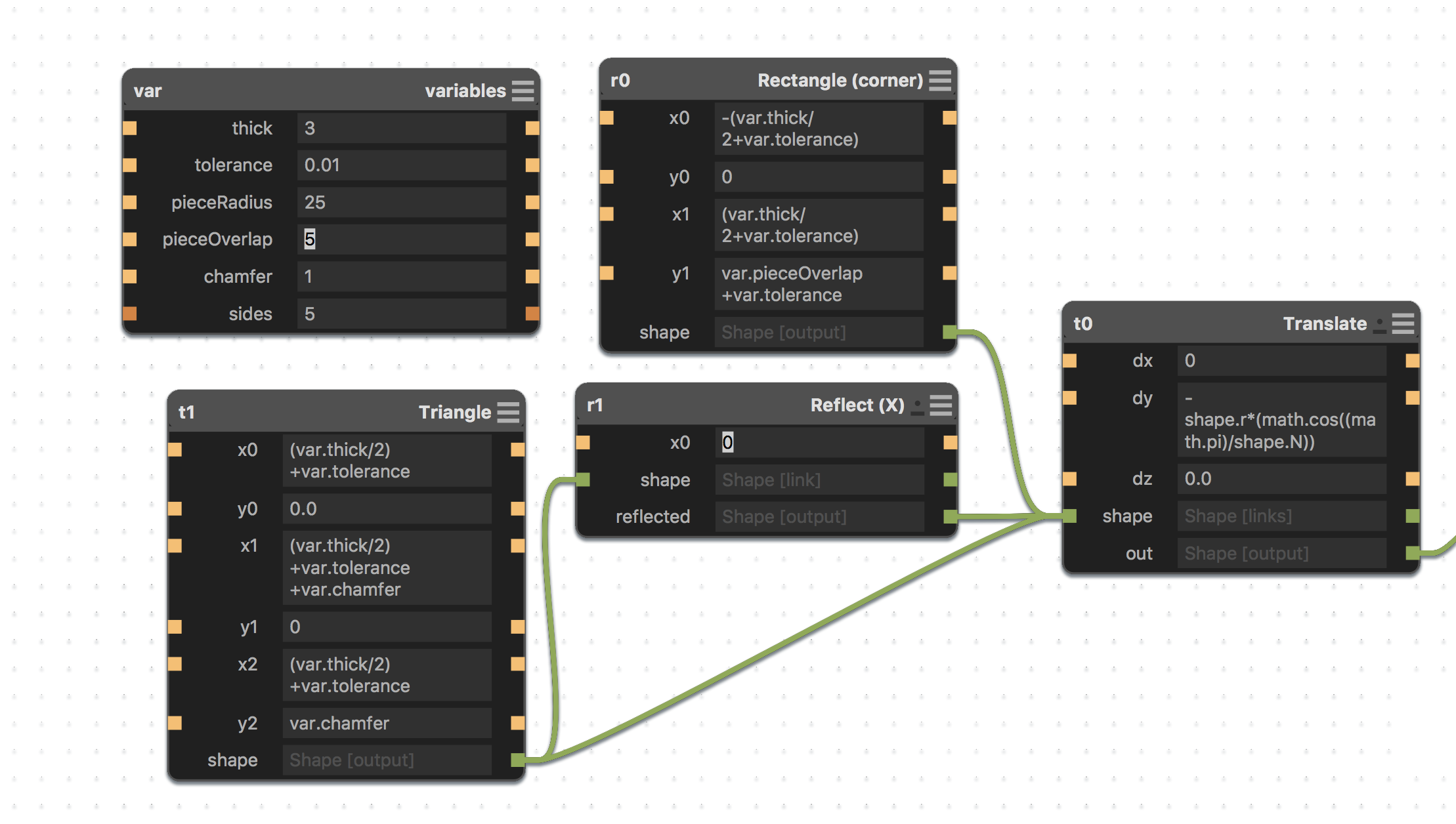
Sadly, I have a limited access to the laser and vinyl cutter this week as I have travelled from Córdoba to attend the Academy. I will be cutting the pieces this evening, hopefully it will work out!
Update: The press fit design developed into two different set of pieces which will allow more flexibility on what could be build with the kit. First, a circular joint piece with equally distributed slots and a second polygonal piece with 3, 4, 5 and 6 sides instances.
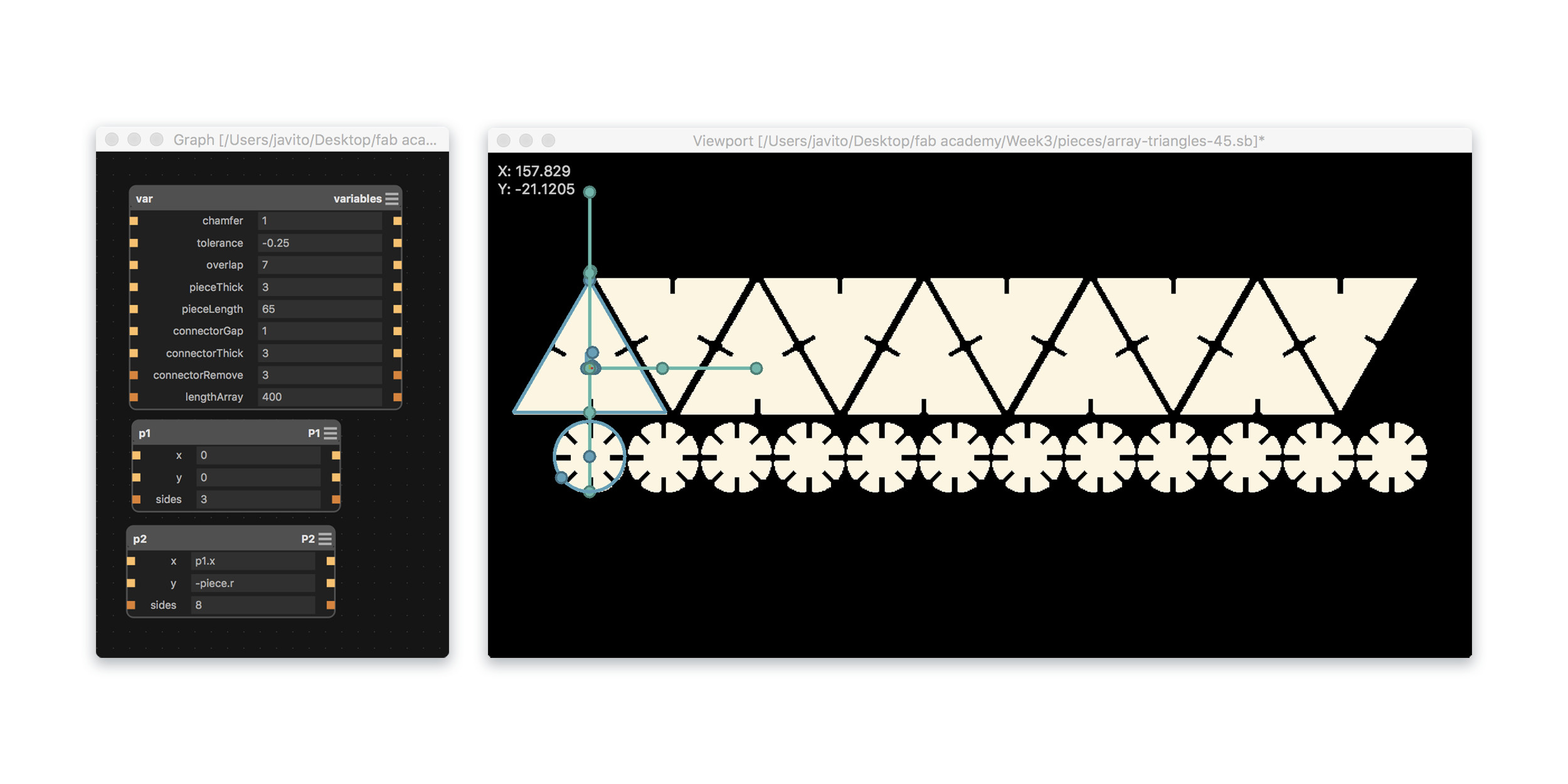
I added a number of extra parameters to optimize the design while laser cutting. Tolerance: an offset of the slot dimensions to compensate the laser kerf and adjust the how tight the connection is. PieceThick and ConnectorThick will help to adjust the design to the specific stock thickness. Overlap is the lenght of the connection between both pieces, which depending of the overall weight of the larger pieces might need to be increased. And finally, ConnectorGap which keeps pieces apart just enough to allow tight constructions specially for poliedric shapes.
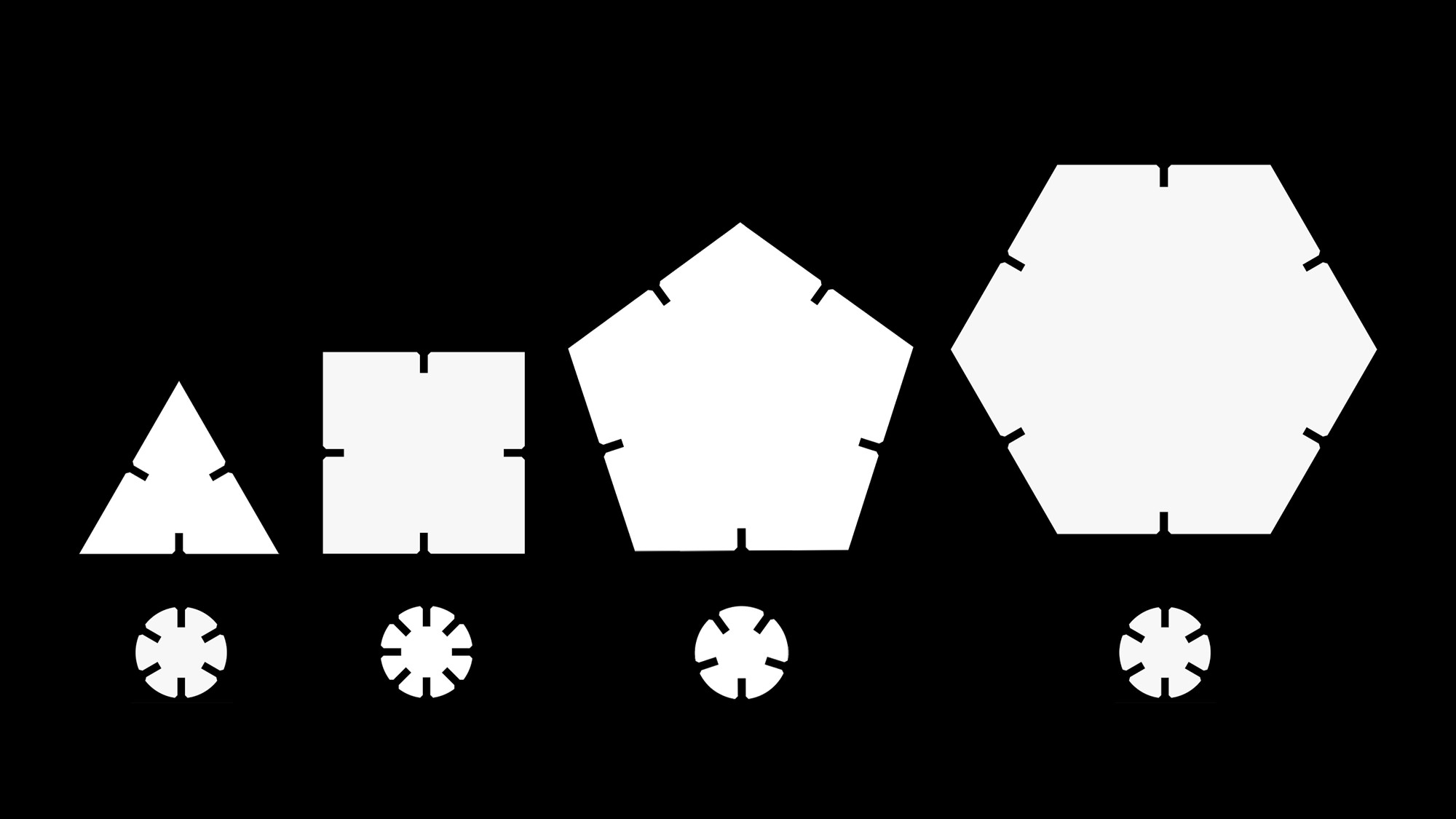
fabrication
The fabrication process was quite straight forward.
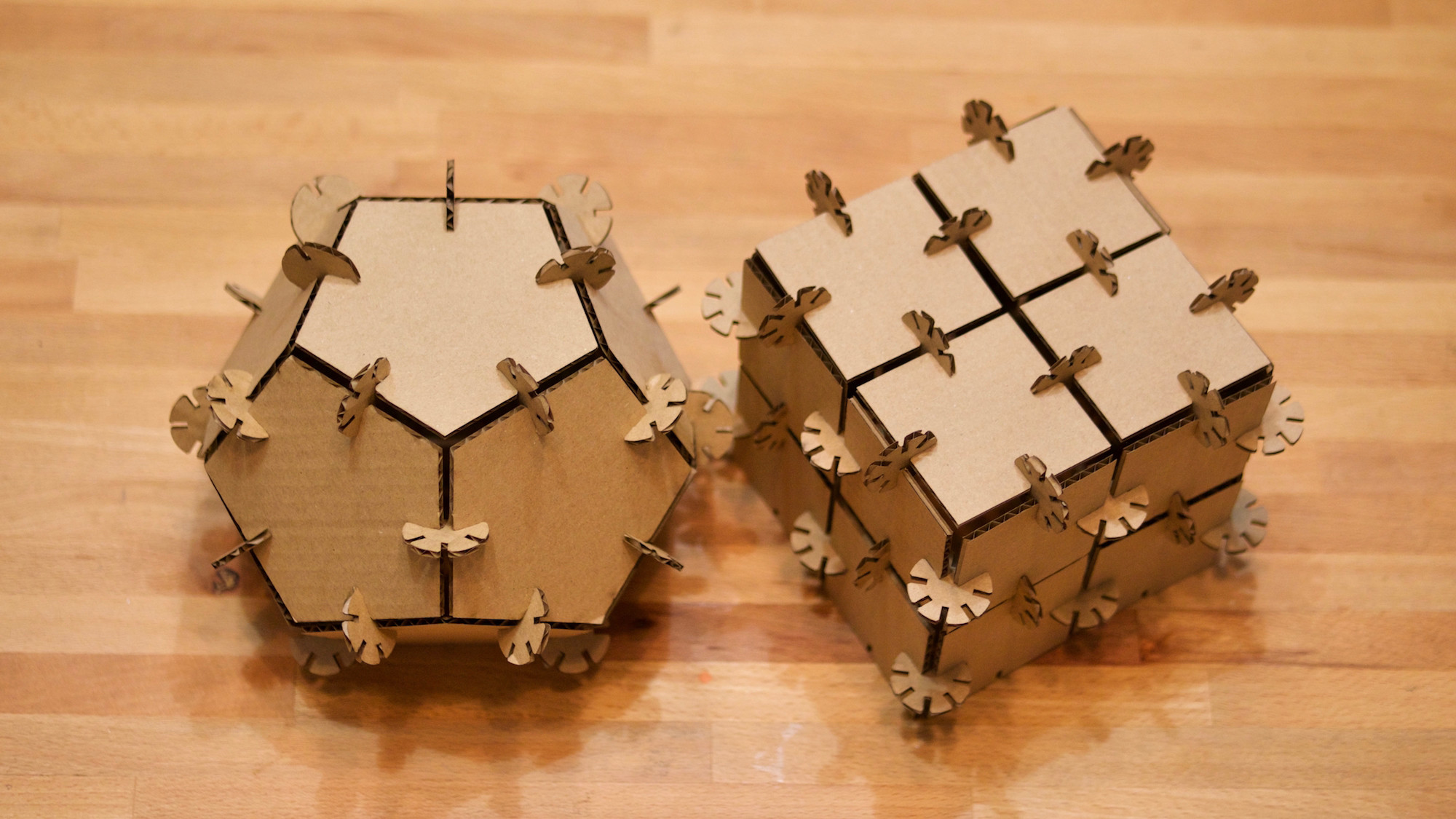
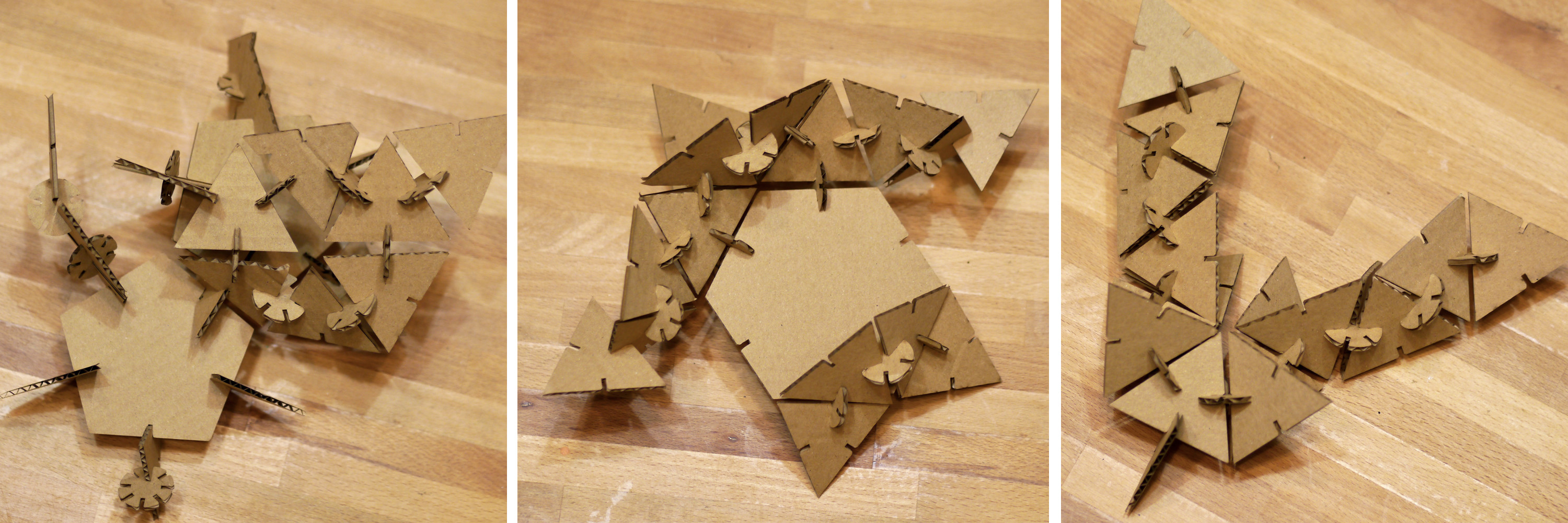