Computer-Controlled Machining
Week 7
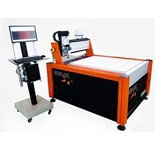
Computer-Controlled Machining
Tasks
make something big
CLIMBING PEGBOARD
For this week assignment I decided to buid a climbing pegboard for a friend of mine that asked for my help. These kind of pieces are usually buit in CNC routers with a manual finish process.
Scheme of the climbing pegboard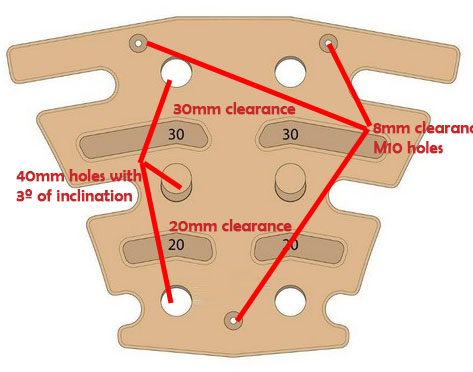
I searched wood types to machine this board and I found near a local supplier medium density overlay (MDO) boards of 22mm and 18mm each to glue after and achieve the 4cm thickness.
I cutted this boards separately and the glue them with liquid nail glue, a very strong glue for this kind of operations.
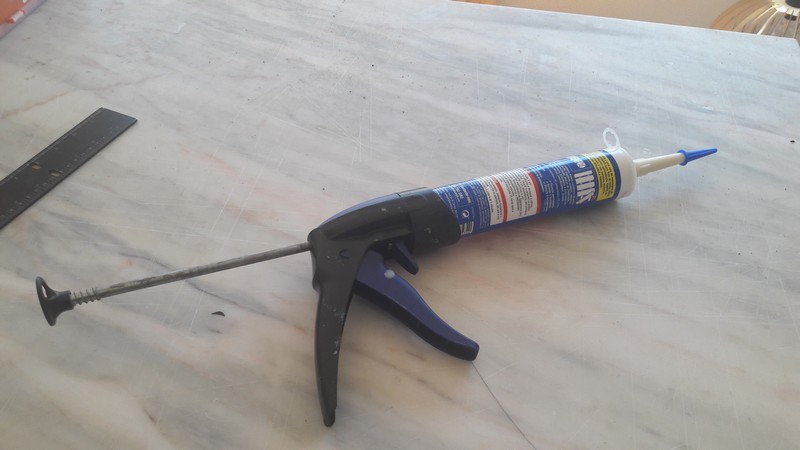
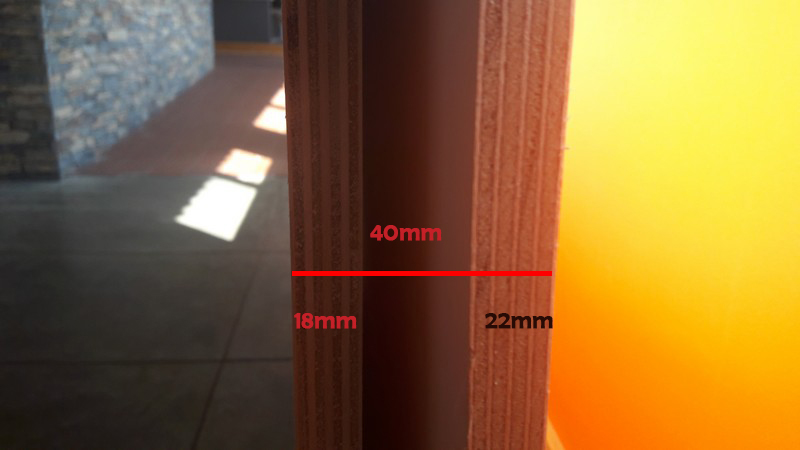
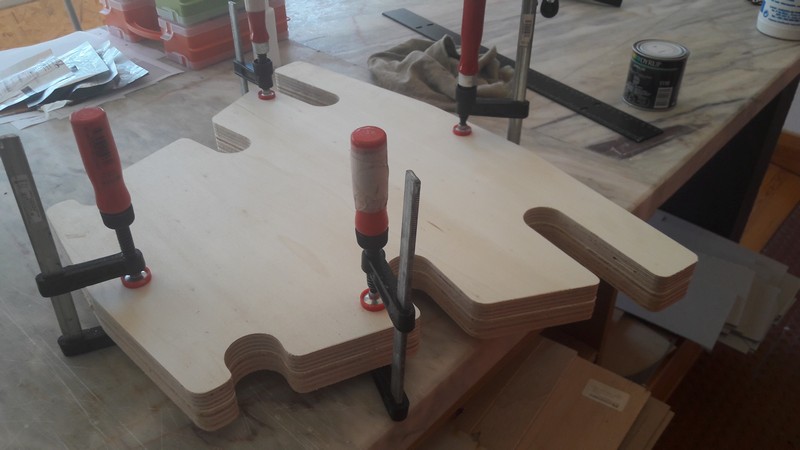
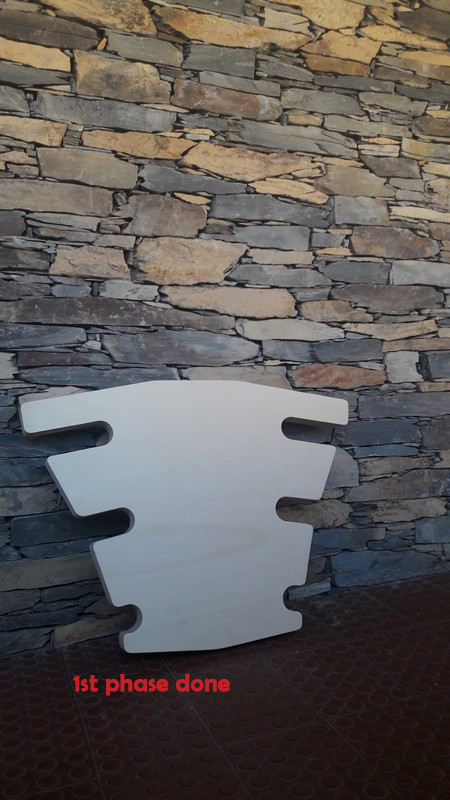
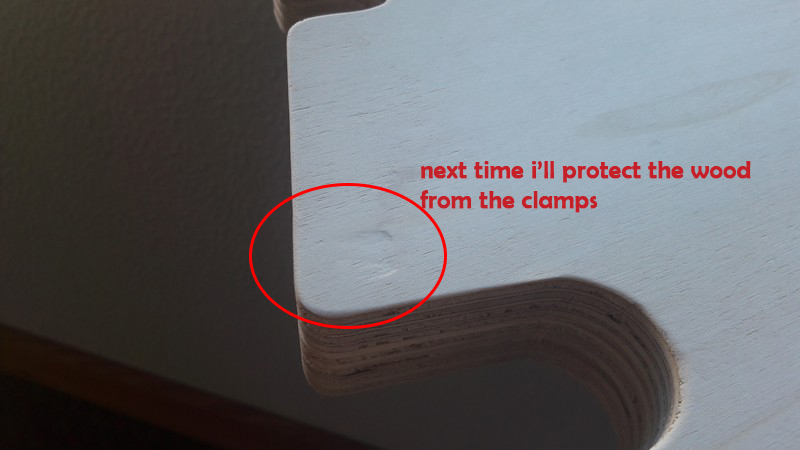
I started drawing in illustrator with the photo locked in background and used the pen tool to start drawing half of the pegboard shape. The other half I used reflect tool.
Use round corners effect to the shape I draw (Effect > Stylize > Round Corners)
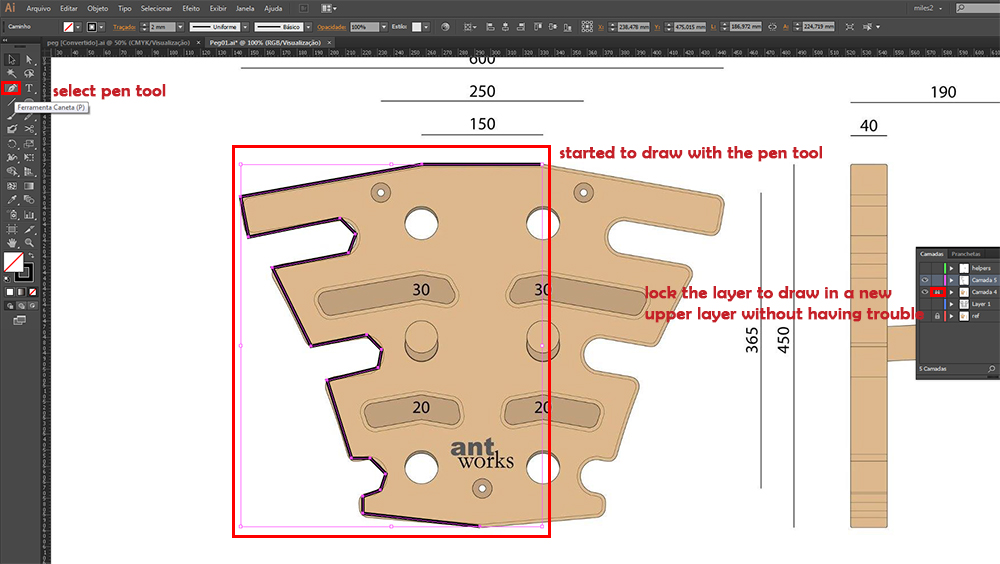
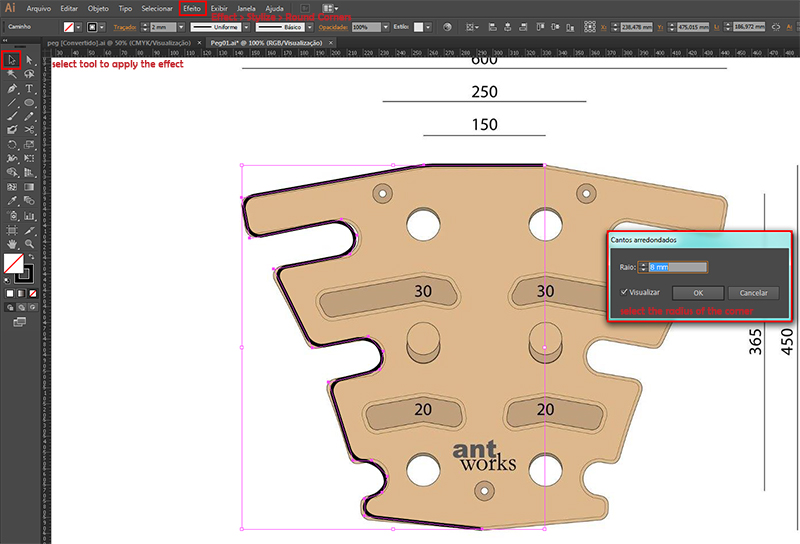
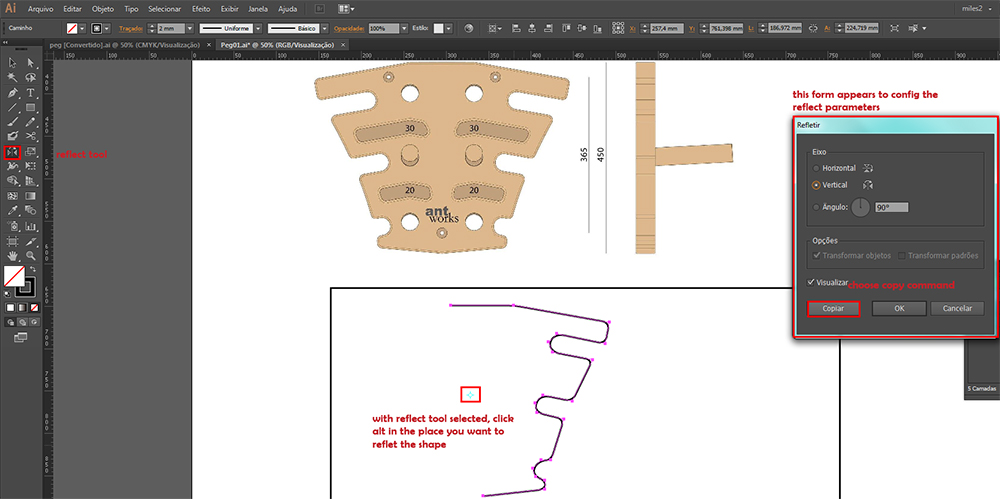
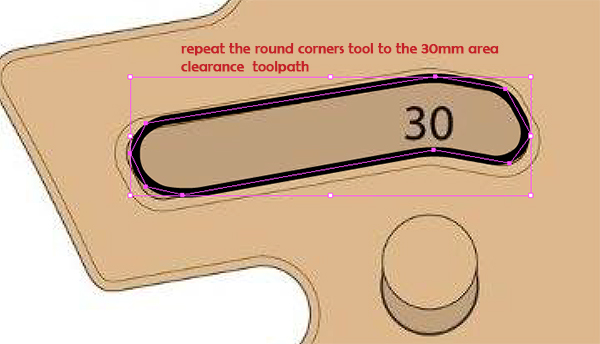
Calculating the angle for the pin holes
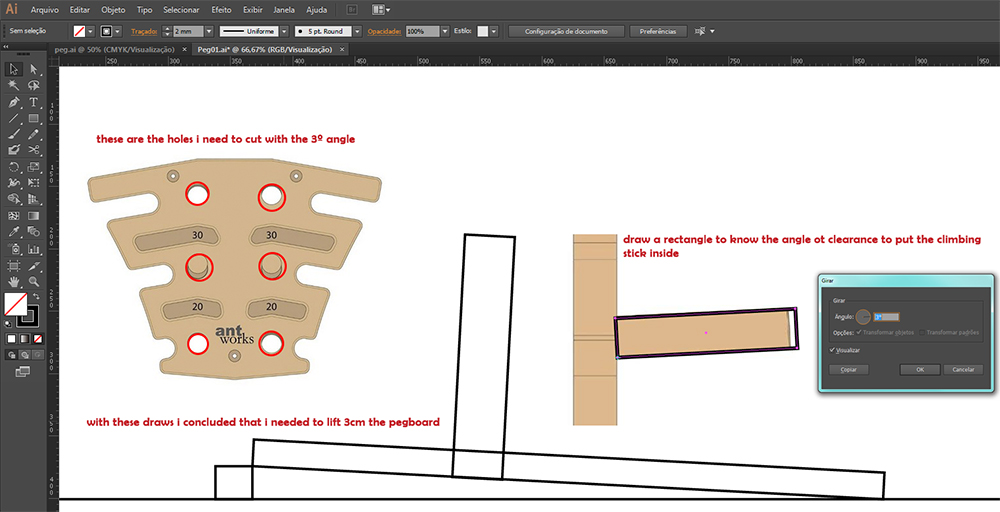
After completing the draw I checked all the alignments and saved my file. I was ready to go to CAM software. I’m learning to use new Autodesk Artcam 2017 that I downloaded with my Autodesk education license but for this board I used Artcam 9, which I’m more familiarized with. I started by creating a new model and importing the vector drawn in illustrator (saved in Japanese format).
Creating model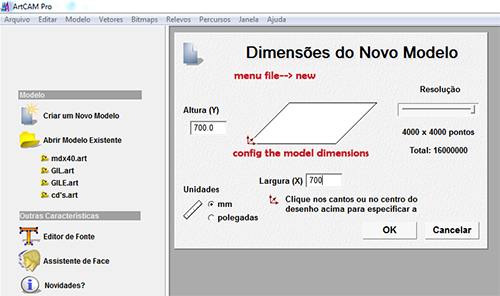
Common settings for our 4mm endmill (please test these with caution)
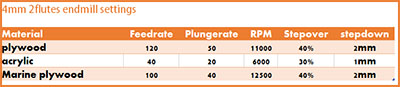
cuting parameters for the model
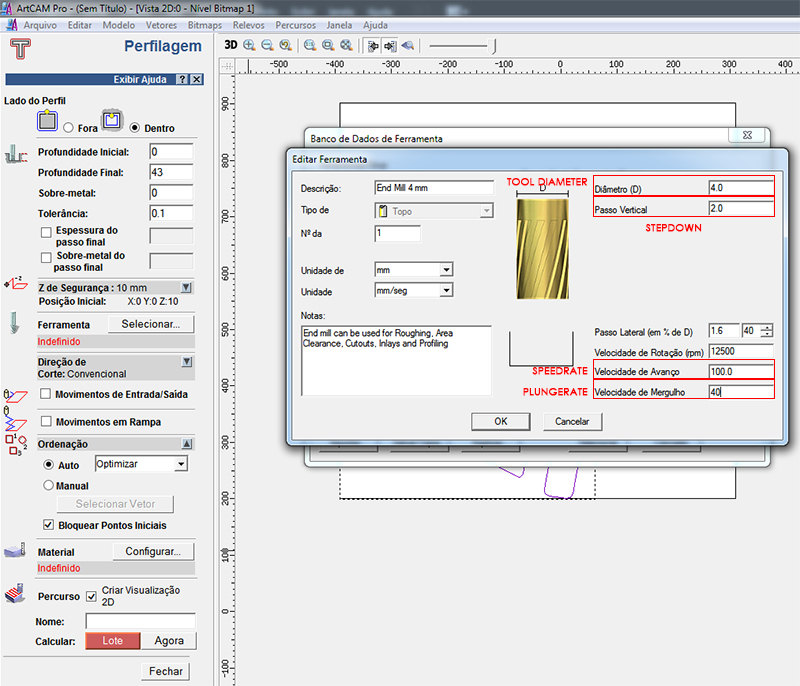
Toolpaths created for the model
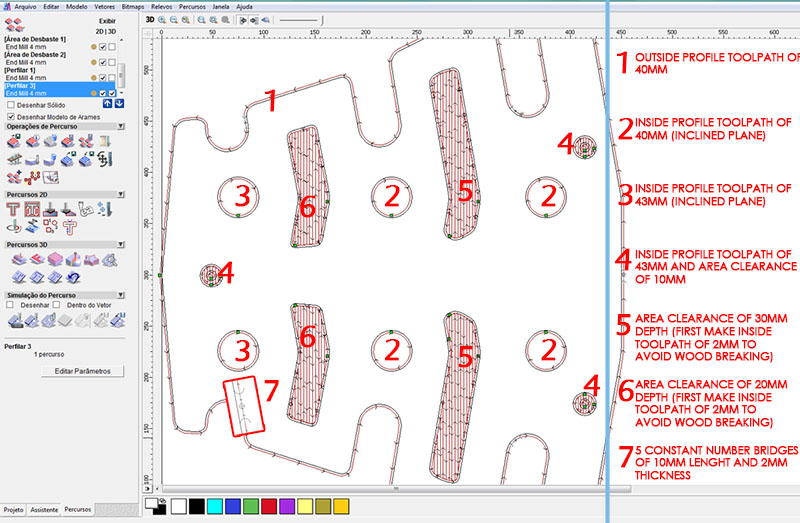
It was time to start the second cnc round. After calculating the angle for the wood pins I had to lift the upper side of the board 3cm. I used 25mm and 5mm wood to achieve it, then clamped well the board to the platform. This was the first time I did an angle machining, so almost everything was new to me. Even the depth of cut I had to increase, because one side was 3mm down from the other. I cut the holes in 3 times, with diferent zero Z for each one of them. After the cuts, it was time to put the board in place and start the clearance jobs and finish the board. Now things got easier !
Some issues during the first clearance toolpath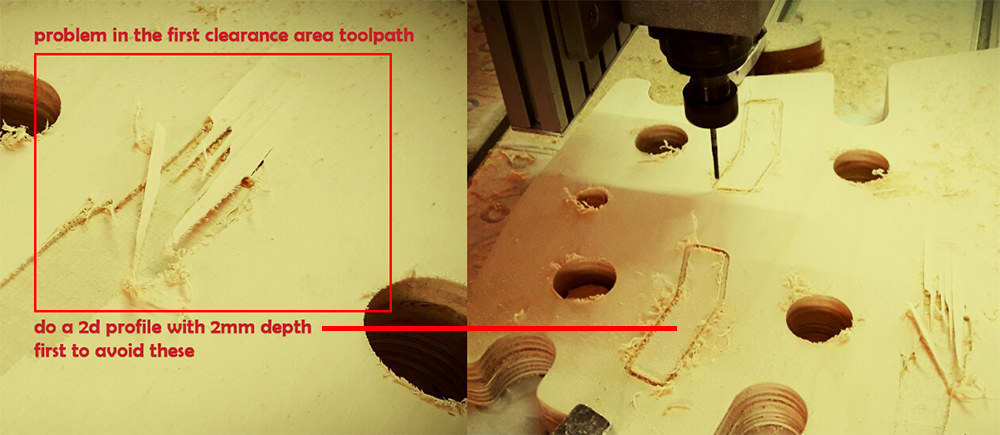
machining on a plane axis
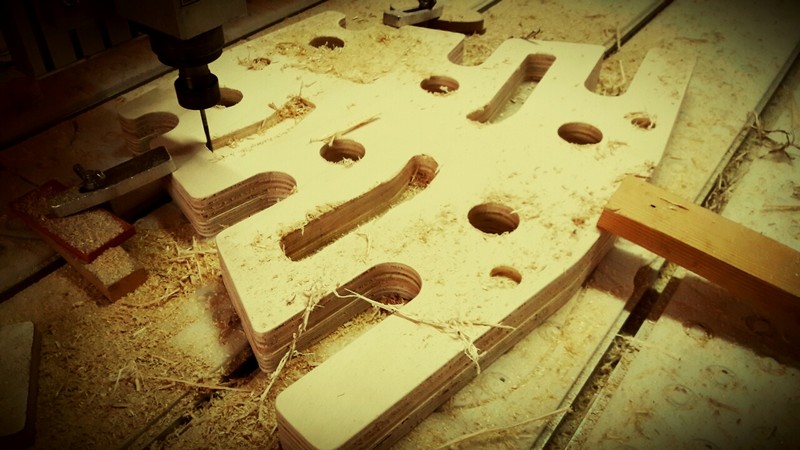
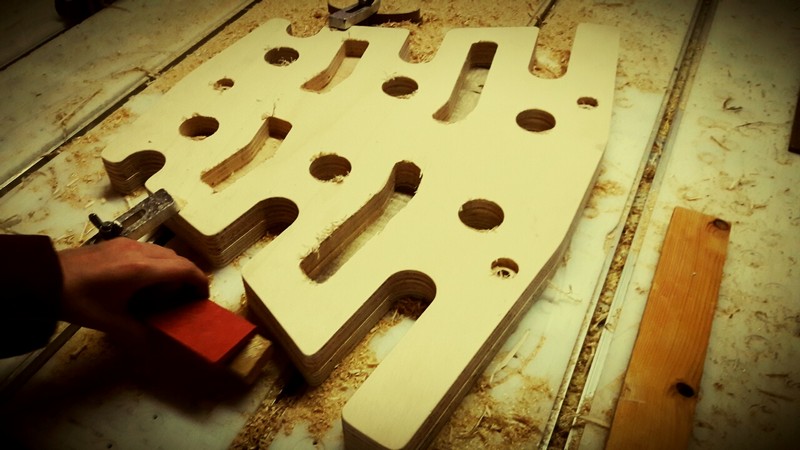
UPDATE 08-07-2017 - Feeds and Speeds
Besides knowing the feeds and speeds for our CNC at the lab for most of the endmills, i was advised to study a bit more and READ THIS ARTICLE. "Speeds" refers to your spindle speed in rpm (revolutions per minute), and "Feeds" refers to the feedrate, i use them in metrix system, mm per sec. If you're a newbie you should start with very secure rates for this parameters, to avoid broking endmills and damage the CNC axis. If your machine is ready for metal milling (mill lubrificant and cooling system), you must be even more carefull. To select your tools you must also be carefull, depending of the material you want to mill, and the finish look you desire. Selecting the materials of the endmills is up to you, there are HSS and carbide, wich have different price/quality ratios.
Before stepping to speeds and feeds calculation, you should be able to understand better chipload concept, that's independent from the measurement of spindle rpm, feedrate, or
number of flutes and gives you information about how hard the tool is working. Remember that each tool have a certain chipload.
different tools working on chiploads
When selecting the number of flutes of your endmill or the type of end you need for your milling processs, you must be carefull. An endmill with 4 flutes lefts a better finish look in your work, but with 2 blades you have more power for each blade, wich means you can work with more speed and sometimes get the same look in your work. In industry, time and costs means everything. Stepover settings are also important in this cases, if you select a larger tool you can clear areas faster and save time.
different kinf of tools
Always ear the sound of your machine working! Just like us, if you feel it's screaming, reduce speeds or stepdowns. With some practice, you can get to know the sound of your machine better and see if it's in pain or not.
Let's pass to the numbers, how can you calculate them according to your tool and material? There are a few ways of doing it:
- They can go by seat of pants and experience or by asking other machinists.
- They can use rules of thumb.
- They can punch it up on a calculator.
- They can rely on manufacturer's recommendations.
- They can use a machinist's calculator.
- They can rely on their CAM program.
- They can use trial and error and repeat what works
Each of these, in my opinion are valid, and you must choose your own way of doing it. for me sometimes, trial/error is the best way, because some materials we use have its own properties and calculators probably will fail giving me answers.
According with WIKIPEDIA SPEEDS AND FEEDS ARTICLE, For my 4mm endmill, lets's calculate my project values:
I'm going to cut plywood, and according to plain high speed steel cutter values wich has 600 feet per minute. converted to metric system, it gave a scary number of 3048 mm/sec, values that my machine can't use! Machinability rating is important, you should know yours.
I installed Gwizard and started exploring the interface. It's a very complete software and has a good library of machines and tools. Folow these steps to grab your values and voila!
Setup with your machine setting
Setup with your tool and material
Security in the Lab is very important. For this work, I’ve used protections Glasses and a mask for the dust. Our CNC is closed in a secured and isolated room.
Security duties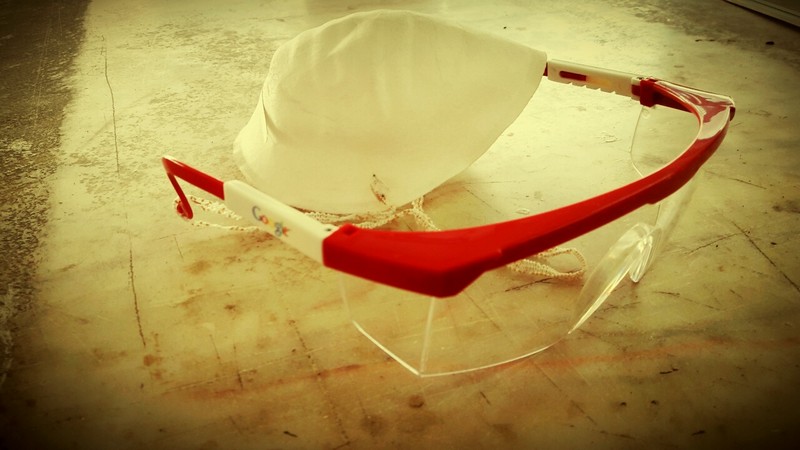
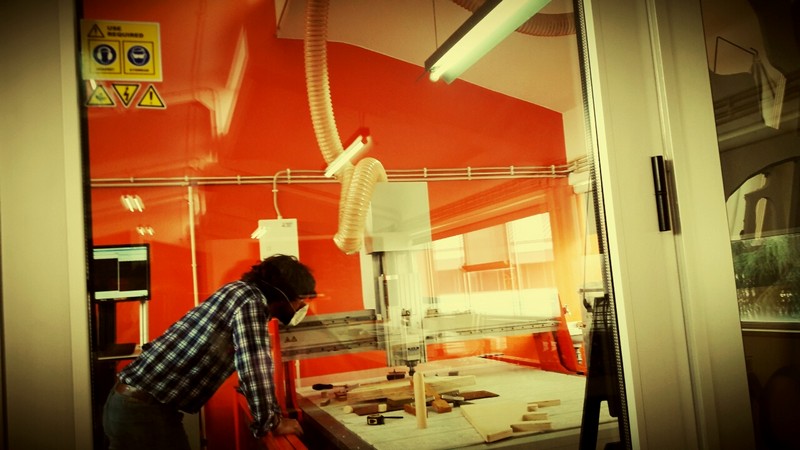
Cleaning duties
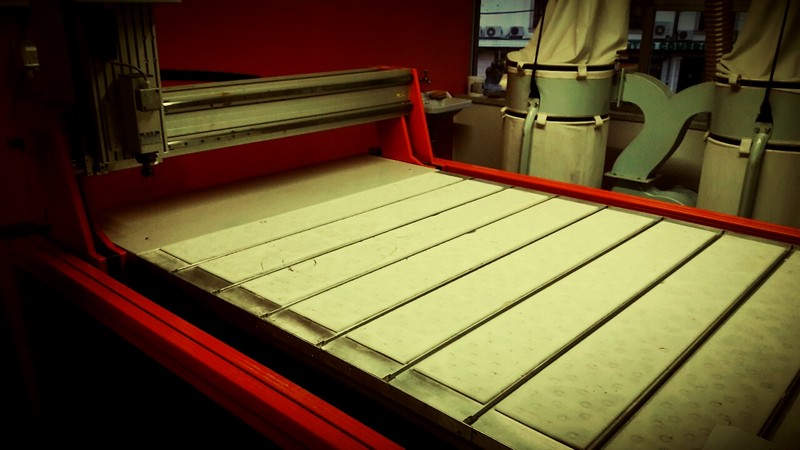
Final Job: scrub the board with Sandpaper to chamfer the corners a bit more and test!
Final climbing pegboard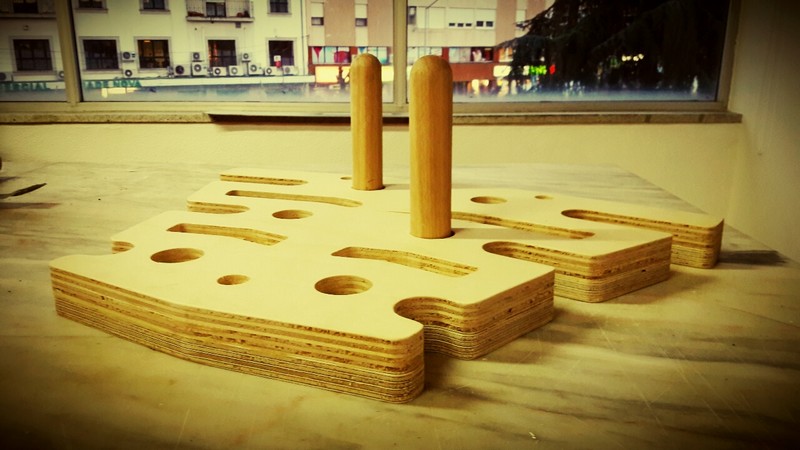
References - Autodesk Artcam Community,
Artcam file
Vector file for the pegboard