Week 5 : 3D printing and Scanning
Assignments:
It's quite interesting week with a good amount of assignments to do!!
3D Printing
Machine at our Lab:
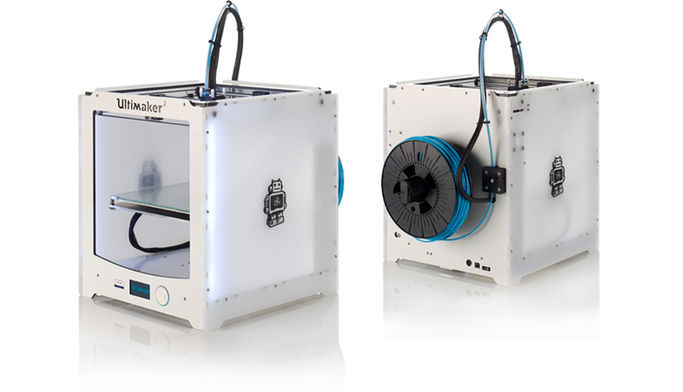
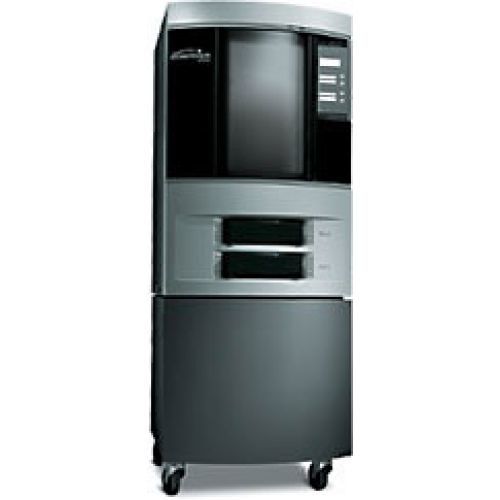
Testing the limits of your printer (Group Work):
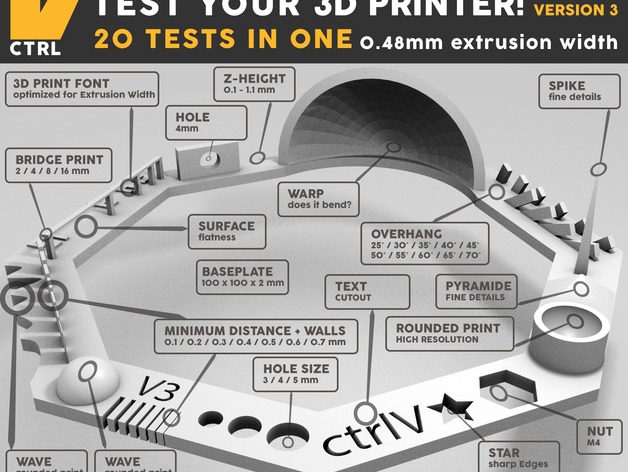
Then we print it on Ultimaker with the following settings:
The print we got is shown below. (Yogi printed it...we all inspected the test print!)

Few insights:
- 01 Nut, Size M4 Nut should fit perfectly
- 02 Wave, rounded print
- 03 Star, Sharp Edges
- 04 Name, Complex Shapes
- 05 Holes, Size 3, 4, 5 mm
- 06 minimal Distance: 0.1, 0.2, 0.3, 0.4, 0.5, 0.6, 0.7 mm
- 07 Bridge Print: 2, 4, 8, 16 mm
- 08 Sphere, Rounded Print 4.8mm height
- 09 Sphere Mix, 7 mm height
- 10 Pyramid, 7 mm height
- 11 Overhang: 25, 30, 35, 40, 45, 50, 55, 60, 65, 70°
- 12 Warp, does it bend?
- 13 Surface, Flatness
- 14 Hole in Wall, 4 mm diameter, check for proper print
- Instant export to Shapeways 3D printing services
- Instant export to Sketchfab online sharing platform
- Export OBJ, PLY, STL and VRML
- Geometry Simplification
- Precise model editing tools
Individual Assignments:
To 3D print an object that can't be by substractive manufacturing.
During the Pre-Fab's, I've made strap for my watch by 3D printing. Links of the strap are something which cannot be made by substractive methods.
Strap: The strap was a series of chains linked together. My Goal was to print it as a piece inorder to avoid assembling the pieces individually. I was pretty successful in designing the chain as such printed using ultimaker instead of dimensions. I gave enough clearance space between links and the casing so that the printing doesn't make them stick together. The whole designing was done using Rhino software. I found it pretty good to toggle between different viewpoints. The case had a dimension of 3.5cm by 3.5cm.
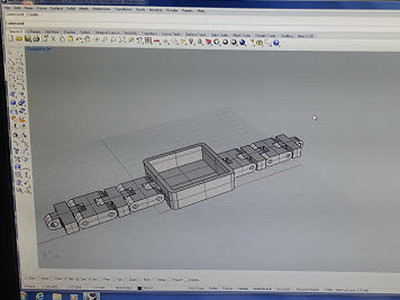
Initially to check out whether the links are coming up pretty good and movable, I did a test print of a small section of the strap. I found out that the links were stiff and needed more clearance space between the links.
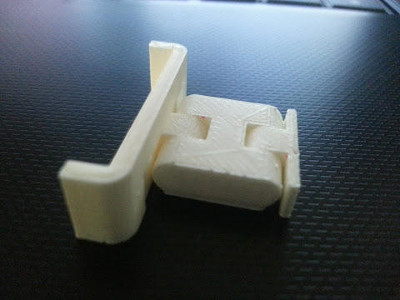
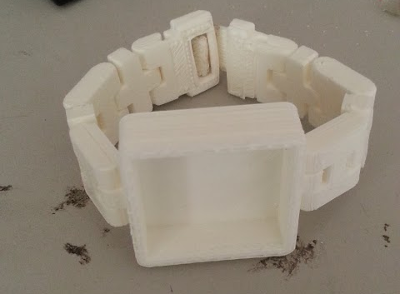
So, I was planning to try out nesting of objects and 3D print them. Sphere within a sphere was the model I choose to design. I faced a lot of issues while designing the file in rhino, especially with aligning all the spheres to the base plane. After designing, I saved the file in .stl format and used Cura software to create gcode format for ultimaker. I scaled the figure by 2.5 times in Cura before printing. At first since I aligned the inner sphere in air, the print did not come as expected. Which is obvious, you can't print in air. There should be a support beneath.
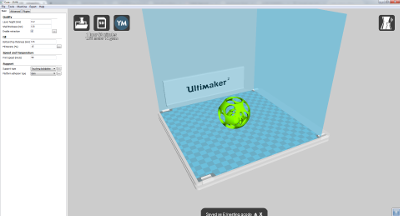
After aligning all the spheres to the base plane, when I took the print since I did not increase the brim width. The bottom support structure was not enough to hold the model as it was being build up.
This resulted in a lot of layer being misaligned from the bottom layer. By the end of printing the model just stripped off from the base plate. Still, I managed to print the whole figure.
Learnt a big lesson that check out all the settings are done before printing!
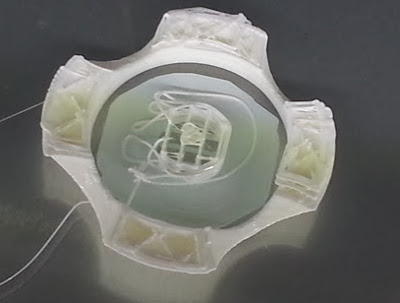
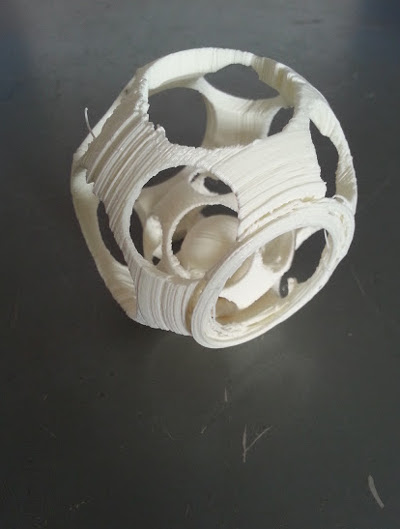
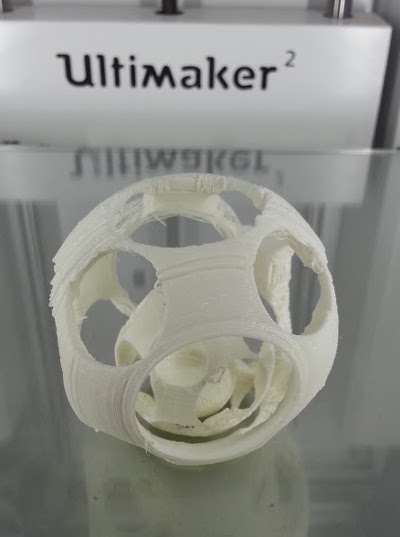
Design Files of sphere (in .3dm)
Design Files of sphere (in .stl)
3D Scanning
I tried out 3D scanning using 123D Catch mobile app and also using Kinect device.
Using 123D catch Mobile app
I scanned a couple of objects using the app including a mountain dew bottle, laptop mouse, a switch box.
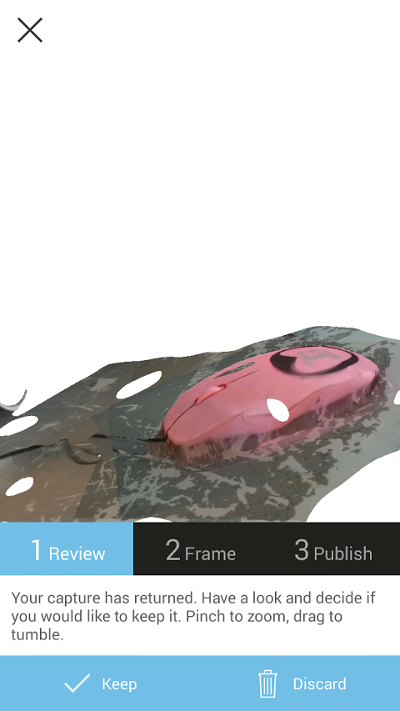
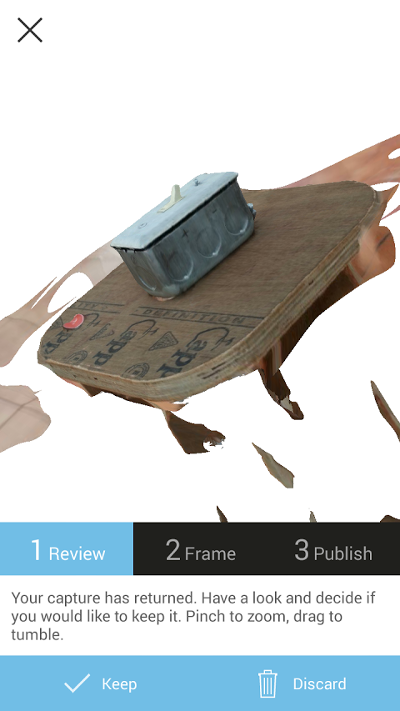
View and download Scanned Files from AutoDesk 123D Link
Using Kinect
I used Kinect with Skanect to do 3D Scanning. With Skanect, capturing a full color 3D model of an object, a person or a room is easy.
Some Features of Skanect:
Tutorials are available at the support page of skanect, which I found useful while learning how to 3D scan object.
I did 3D scanning of body for my assignment of 3D scanning. Below are the images and the files.
Since taking print out of the scanned object is not necessary, I did not take print out of the scan. "3D printing is not for making figures", Francisco's dialogue!